代表プロフィール
弊社代表 伊藤哉(いとうはじめ)について
PROFILE
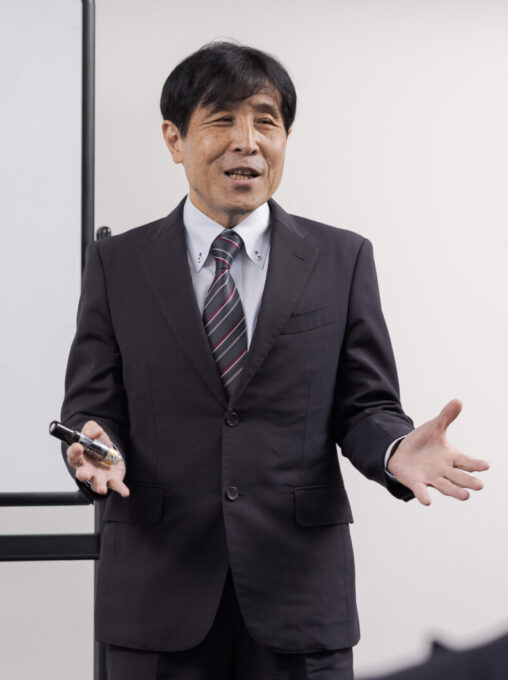
中小製造現場が専門の生産性向上コンサルタント。金属工学の専門家で製造/生産技術、生産管理、IEにも詳しい。独自の儲かるタイムマネジメントで、戦略的リードタイムを設定しながら、利益を拡大させる手法が多くの経営者から評価されている。
ロードマップとプロジェクトで経営者の右腕役を育成する人材再生産体制の仕組みづくり支援にも力を注ぐ。大手と中小の現場経験を踏まえた熱心な指導には定評があり、電子部品、金属製品、金属加工、表面処理、素材加工、樹脂成形、印刷、食品加工など業種業態にかかわらず、多くの製造企業の経営者の信頼を集めている。
大学を卒業後、大手特殊鋼メーカーに就職、20年間近く、工場一筋に現場実務と工場経営に携わる。エンジニアとして最初に任された業務は材料特性に注目した製品の軽量化を実現させる新生産プロセスの開発である。
2年間の取り組みの結果、軽量化に寄与する技術的成果を評価され、一般財団法人素形材センターの技術賞を受賞する。その後、生産性を向上させる技術開発プロジェクトを主導し、生産性を従来対比で10%向上させる。生産リードタイムの短縮に貢献する。
エンジニアとして現場で汗をかいた最初の5年間でモノづくりの基本を身に着ける。工学的な専門知識のほかに、生産管理、品質管理、原価管理など工場経営に必要な知識と実務を学ぶ。
加えて、現場を相手に仕事をする難しさも経験し、「人に動いてもらう」ことの重要性を肌で感じる。その後の管理者としての仕事のやり方に大きな影響を及ぼす。机上の空論ではなく、現場での実践を通じて身に着けた多様なノウハウは強みとなっている。
管理職となり、競争力を高めるため、新たな生産プロセスを開発するプロジェクトを立ち上げる。営業を含めて、現場、設計、設備など各部門の多様なメンバーと一緒に仕事をする中で「人に動いてもらう」ためのマネジメントの手法を鍛える。
開発後、当該生産プロセスを柱とした生産ラインをゼロから設計し立ち上げる。生産ライン立ち上げ当初は品質が安定せず、現場とともに汗をかき、対応策に知恵を絞り続ける。24時間連続操業現場であったため、昼夜、土日なく踏ん張る日々が1年ほど続く。
そうした活動の結果、70~90億円規模の事業が軌道にのる。プロジェクトをやりきる胆力を鍛えるとともにモノづくりにおける現場との連携の重要性を学ぶ。
引き続き、生産ラインの管理者として現場とスタッフをマネジメントしながら、IEの手法で生産性を従来対比で1.8倍に向上させる。こうした業務を通じて、品質改善、コスト削減、生産性向上などの改善活動や5Sを現場へ指導するノウハウを身に着ける。
その後、100人規模の中小製造企業で現場の管理者として業務に取り組むが、大手と中小の現場の違いに戸惑う。大手の現場とは違って、仕組みがない、組織で仕事をしていないなどの状況に直面し、思うように仕事が進まず、半年ほど悩む。
自分の考えを知ってもらうために、作業者との個別面談などコミュニケーションの工夫を図る。現場と管理者が腹を割って話をする大切さを実感する。品質クレームが発生しては自ら選別作業を指揮し、また、労災が発生しては自ら労基署とやり取りしながら現場の安全対策をするなど、プレッシャーの多い日々が続く。仕組みとチームワークの重要性を痛感する。
こうした中小現場での生々しい経験を通じて、「どんな中小現場にも強みがあり、やる気のある若手や頼りになるベテランがいる。」との想いを強くする。そして、中小製造現場が豊かに成長し続けるためには、リードタイム短縮による人時生産向上が絶対に必要であるとの確信に至る。
その具体策が生産性ロードマップ戦略プログラムだ。大手と中小の製造現場で工場経営に携わって出来上がった体系である。人時生産性を高め、ロードマップとプロジェクトで管理者を育成する。
技術立国日本と地域のために、前向きで活力ある中小製造企業を増やしたいとの一念で、中小製造業専門の指導機関・株式会社工場経営研究所を設立。現在、同社代表取締役社長。1964年生まれ、名古屋大学大学院工学研究科前期課程修了。技術士(金属部門 登録番号 第54246号)。
「弊社代表伊藤の大手と中小製造現場での改善実績」
1)品質向上
・自動車部品で品質管理の観点からデザインレビュー、初期流動管理、工程変更管理のしくみを定着させた。新規製品の量産立ち上がり品質を安定させるためである。立ち上げ時の不良品を30~50%低減できた。
・自動車部品(ギアの中間材)の生産現場で品質クレームがあり、数十万個の製品を選別する事態に陥ったことをきっかけに品質管理体制を強化した。品質指標を新たに設定して継続的な品質改善活動を開始した。さらに標準偏差と工程能力により生産設備のばらつきを管理した。月1回のお客様との連絡会議によって信頼回復のきっかけをつかむことができた。
・自動車部品の不良品を継続的に分析する体制を整備した。毎日、現場で関係者が集まって不良品の現物を確認し、、3現主義に基づいて迅速に動いた。継続的な不良品対策の結果、不良率が5~10%改善された。
・機械加工職場(20名程度)で過去クレーム事例の月1回勉強会を定着させた。毎年数件発生していたクレームを年間ゼロ件に抑えることができた。
2)コスト削減
・2年連続赤字だった機械加工職場(10名程度 売上高10~12百万円/月)を1年で黒字化できた。コスト減策と売上高アップ策の両輪を回した。コスト削減策では改善活動の進捗を見える化した。ひとりひとりと個別面談をして動機づけを図った。
・新たに立ち上がった自動車部品の生産ラインで5~10%のコストを削減した。生産技術改善、作業改善、物流改善などで現場のムダ取りを実施した。成果が現場へ定着するように作業標準化を進めた。
・住宅関連板金製品の生産ラインで現場と一緒にムダをピックアップした。梱包材に改善すべき点が見つかり、梱包形態、梱包材の仕様を見直した。輸送テストを経て現場への採用が決定、年間数十万円のコスト削減となった。
3)生産性向上(リードタイム短縮)
・新たに立ち上がった自動車部品の生産ラインの生産性を1.8倍に拡大できた。継続的な品質改善、IEを活用した作業改善、5S、作業標準化を進めた。
・自動車部品生産ラインの生産性を従来対比10%向上させた。技術開発プロジェクトを主導した。現場と連携して安全性を確認しながら、新技術を現場へ定着させた。
・自動車部品(ギアの中間材)の生産現場で多品種化に伴う小ロット生産への対応策を検討した。物流改善と加工機改良で対応できることが判明し、現場と連携して、3ヶ月で対応策が完了した。現場で同時に流動させられる品種を従来の2種類から4種類に増やすことができた。
「弊社代表伊藤の工場経営関連の業務実績」
1)新規事業計画策定と実行
自動車部品の新生産プロセスを開発し、5~7万個/月の生産ラインを立ち上げるプロジェクトの事業計画を策定し実行した。営業部隊とも連携して、3年間の取り組みで、70~90億円規模の事業を軌道に乗せた。
2)生産管理体制構築
・自動車部品(ギアの中間材 40~50万個/月)の生産ラインで進捗管理の体制を強化した。目で見る管理ができる体制を整備し、管理工数を半減させた。
・住宅関連板金製品の生産ラインで一部の製品の生産計画を標準化した。受注実績と生産能力のデータをもとに現場と検討し、誰でも迅速に精度の良い生産指示を現場へ出せる仕組みを構築した。それまで計画確定に半日要していたのが1時間に短縮された。
3)人事管理
・機械加工の職場(20名程度)で生産性を上げるために多能工化を推進する必要が生じた。現場のモチベーションを高めるためスキルマップ管理体制を構築した。さらに、それに基づく人事考課制度を半年間で整備して多能工化を加速させ、1年で成果が得られた。
・ベテラン作業者が直近の1年間で数名退職する職場(20名程度)で人材確保の問題に直面した。以降1年間の人材採用及び人材教育の計画を立案してやるべきことを明確にした。現場リーダーと連携して仕事を進め、人材確保が達成された。人材採用計画の手法が現場に定着した。
4)現場改善指導
・5名程度~30名規模の複数の現場で改善活動を指導し推進した。改善の着眼点と5Sを柱に指導した。現場リーダーを中心にしたチームづくりを重視し、半年~1年間で活動を定着させた。