「生産性ロードマップ戦略」—儲かる工場経営を目指して—第430話 誰がマスターデータを整備しているか?
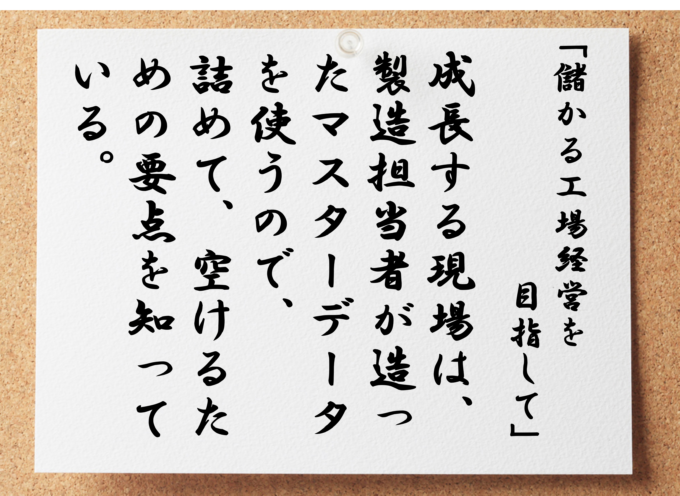
「作業者によってバラツキがでてしまいます。」
アルミ合金製部品を鋳造加工する製造現場、生産管理担当者の言葉です。
人時生産性を高めるために、詰めて、空ける日程計画の立て方を考えなければなりません。空けたところに、新たな仕事を取り込んで付加価値額を積み上げます。
この現場では多台持ちです。1人3台持ちをやっています。この体制自体、人時生産性向上に貢献しているのです。
ただし、留意点があります。
冒頭の言葉です。
バラツキがあると、日程計画通りの生産活動ができません。
日程計画は現場の製造条件に従います。そして、製造条件のベースは見積もりです。見積もりとは経営者が「こうやってつくれば儲かる」と考えた結果でもあります。
その通りできないと、儲かりません。そこから導かれた望ましい生産状況が、マスターデータに整理されます。
製造担当者が望ましい生産状況をマスターデータとして数値化するのです。生産管理担当者はこのマスターデータに基づいて日経計画を立てます。
マスターデータから「単位時間当たりに生産できる良品数」が明らかになるので、製造ロット数をこの数値で除すれば、生産に必要な所要時間(リードタイム)が出るのです。
ここまでの作業に属人的な要因はありません。
先の現場にもマスターデータはあります。しかし、使い方を改善しなければなりません。生産管理担当者が製造状況を数値化しているからです。
製造担当者がやるべきことを生産管理担当者がやっています。把握できていないことが多々あるので、そこは属人的に処理しすることになるのです。
「単位時間当たりに生産できる良品数」は標準時間(CT、LT)、稼働率、良品率の組み合わせで計算されます。そして、これらの数値は、製造担当者でなければ把握できないものです。
これらの数値を組み合わせた結果、「単位時間当たりに生産できる良品数」が計算されます。したがって、「単位時間当たりに生産できる良品数」を増やしたいとき、
・標準時間を短縮する
・稼働率を高める
・良品率を高める
などを、製造担当者が判断するのです。
もし、この業務を生産担当者がやるとどうなるか?
生産管理担当者は工番、製番毎の標準時間(CT、LT)、稼働率、良品率を扱う立場にありません。状況を把握するために、現場にヒアリングして、稼働率や良品率など必要な数値を調べることもあります。ただし、体系的に全ては分かりません。
したがって、原則、扱うのは「単位時間当たりに生産した良品数」の実績数そのものです。
・1時間当たりの実績生産数
・シフト当たりの実績生産数
・1日当たりの実績生産数。
生産管理担当者は、この数値そのものを、マスターデータで扱うことになります。
本来は、標準時間(CT、LT)、稼働率、良品率の組み合わせで計算しなければならないところを、実績数を平均するなど、なんとなくという感じで決めざるを得ないことになるのです。
この現場は多台持ちでオペレーションされている鋳造加工現場です。作業者の技量による出来高のバラツキが避けられません。変動要因があります。
そのため、生産管理担当者がマスターデータで設定した「単位時間当たりに生産した良品数」だけでは、詰めて、空ける日程計画は立てにくいのです。
生産管理担当者はアウトプットの出来高しか分かりません。変動要因が不明のままです。その結果、次のことが頻繁に起きています。
・所定の日時で計画生産数に達しなかった。
・所定の日時よりも早く、計画生産数に達してしまった。
前者が起きると、計画全体が後ろ倒しです。後者が起きると、段取り準備ができていないので手待ちです。どちらにしても、人時生産性を劣化させます。
アウトプットの出来高実績から、なんとなく決められた「単位時間当たりに生産した良品数」だけでは詰めて、空ける日程計画は立てられません。
生産に必要な所要時間は、マスターデータの構成要因を明らかにした上で、製造担当者が計算して決めるものです。作業者によるばらつきがあれば、それも反映させます。
生産管理担当者は、その構成要因から計算された「単位時間当たりに生産する良品数」に基づいて、日程計画を立てるのです。もし、詰めて、空けたければ、製造担当者にその旨を伝えます。
標準時間(CT、LT)、稼働率、良品率を改善して、詰めて、空けることを実現するのは製造担当者の仕事です。
経営者は日程計画に使われているマスターデータの構造を把握しておく必要はあります。そして、生産管理担当者と製造担当者の役割も要確認です。
細かいところは現場キーパーソンに任せておけばいいですが、誤りがあったら指摘しなければなりません。積み上げの実務計画は、全てここで決まるからです。
マスターデータの「単位時間当たりに生産する良品数」は標準時間(CT、LT)、稼働率、良品率の関数ということです。関数なので、詰めて、空ける日程計画を立てるときに、どの変数をいじればイイのか、現場は分かっています。そこは任せます。
多台持ちではどうしても作業者間での技量の差が出るものです。したがって、多台持ちの現場で「単位時間当たりに生産する良品数」を設定する時、関数の変数にあたる構成要因を作業者毎に設定する必要もあります。
そうした場合、必要になるのが、作業者毎の「単位時間当たりに生産する良品数」の設定です。多台持ちは、柔軟性が高く、かつ生産性を向上させられる体制ですが、その分、作業者間での技量に差があると、アウトプットが大きくばらつきます。ここは要注意です。
したがって、作業者毎の「単位時間当たりに生産する良品数」を設定できれば、多台持ち現場でも日程計画の精度が上がってくるのです。その数値を裏付ける構成要因も把握できます。
生産管理担当者は、詰めて、空ける具体策を、製造担当者と一緒に考えることができるようになるのです。「単位時間当たりに生産する良品数」の関数が明らかになれはそうできます。
「そうしたやり方をやってみたかったです。」とは生産管理を担当している女性の現場キーパーソンの言葉です。
業者によるバラツキのために、詰めて、空ける日程計画を立てられませんでした。その問題を解消するのは、その現場キーパーソンではなく、製造担当者です。
その現場キーパーソンは、このプロジェクトを機会として、やってみたいことを言語化できました。
多くの現場キーパーソンは解決策を知っています。ただ、言語化できないので、そのままになっていることが多いようです。
経営者の方々には、こうした事実にも気付いて欲しいと感じます。
次は貴社が挑戦する番です!
成長する現場は、製造担当者が造ったマスターデータを使うので、詰めて、空けられる。
衰退する現場は、生産管理担当者がなんとなく決めた数値なので空けて、詰められない。