「生産性ロードマップ戦略」—儲かる工場経営を目指して—第441話 標準化、規格化で管理コストを下げているか?
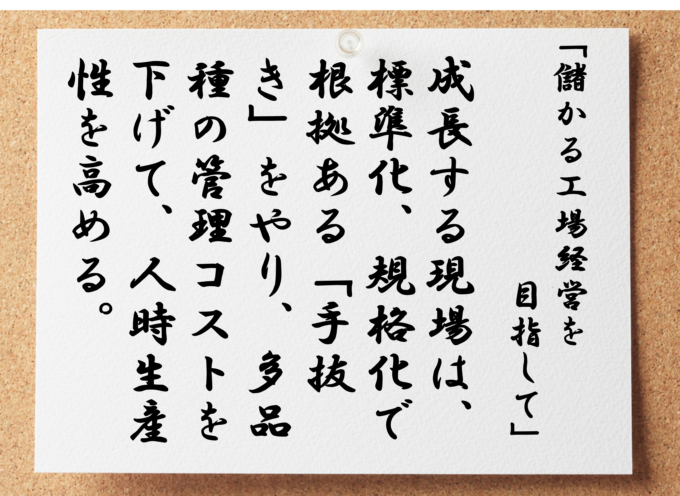
「ウチの製品はいろいろあって分類は難しいです。」
工程フロー図作成に着手した工場長の言葉です。
この企業では、建物に設定される板金製品を扱っています。現物合わせなので、サイズは多様です。基本的な構造は同じですが、同一寸法の製品はありません。現合の状況によっては、特注対応もあります。
このような現場で、工場長は、工程フロー図の検討を始めました。
工程フロー図は現場の思考を揃える役割を担います。製造手順の認識で、ベクトルが揃っていないと、議論が無駄に長くなるものです。工程を定義し、主要製品のフローを整理します。
「工程の流れを整理する」という言葉を耳にした工場長の頭には、扱っている多種多様な製品が浮かんできました。品種がいっぱいあります。ごちゃごちゃした特注対応もあります。
製品を分類、整理できるだろうか?
冒頭の言葉です。
工程管理や品質管理、原価管理の各種管理で欠かせない考え方があります。
・標準化、規格化
グルーピングです。共通要因に従って製品や作業、モノの流れを分類します。管理効率を高めるためです。
自社商品が100品種あったとします。これら100品種を個別に管理すると100通りの管理項目が必要です。一方、商品の共通要因を探して、自社商品を10通りに分類できたら、管理項目は10分の1に減らせます。
どちらの管理コストが有利なのかは明らかです。管理を強化しても儲かりません。管理は最低限にしたいのです。そのために標準化、規格化をやります。
多品種職場の工場長や現場キーパーソンから、しばしば聞こえてくる言葉があります。
「ウチの製品はいろいろあって分類は難しい。」
多種多様な製品を前にして分類できないと感じるのです。
品種で整理しようとすると、そうなります。そもそも品種が多いので「多品種」です。製品の品種で分類すると項目に際限がありません。
そこで、工程管理ではプロセスで分類するのです。中小製造現場では、多くの場合、プロセスは「設備」と「人」となります。その品種を製造するプロセスで分類すればグルーピングは可能です。
製品の色が黒、赤、青・・・といろいろあっても、プロセスは「塗装」で分類できます。
多品種でグルーピングする要点はプロセスです。グルーピングできれば、管理項目数を減らせます。これが、標準化・規格化です。根拠のある「手抜き」とも言えます。
少数精鋭の中小現場では、根拠のある手抜きをやりたいのです。標準化、規格化すれば、管理項目数を減らせるので、仕事が楽になります。
マスターファイルに記述される標準時間の計測でも、標準化・規格化の考え方は大事です。
「ストップウォッチで計測しようとしましたが、途中で息切れしてしまいました。」
外部の支援を受けて、マスターファイルを作成しようとした現場があります。作業時間をストップウォッチで計測するよう指導がありました。
ただし、少数精鋭の現場です。計測だけに専念できる余力はありません。計測に要する工数に制限がありました。そうしたなかで、全てを計測しようとして、行き詰まったのです。
根拠のある「手抜き」をやる必要がありました。
マスターファイルを作成するなら、まずは、工程と作業の標準化、規格化です。
標準時間の最小単位は0.5分、場合によっては1分でも問題ないかもしれません。標準時間の最小単位は1秒である必要はありません。
マスターデータの目的はLTと生産能力の算出です。日程計画を立てられれば、それでイイわけです。数値精度は高いことに越したことはありませんが、最初からそうする必要はありません。要は目的次第です。
根拠ある「手抜き」で、実務上必要な精度を確保できていれば、その標準時間はマスターファイルとして使えます。場合によっては、標準時間を推測で設定しても構わないのです。必要に応じて、精度を高めていきます。
多品種小ロット生産は規模を追いかける大手が嫌がる生産形態です。
中小製造企業の強みを発揮できる生産形態です。中小で、事業モデルの全てが、この多品種小ロット生産では、儲かりませんが、生き残りのためには、必要な生産形態です。
こうした生産形態への対応力があれば、お客様に選ばれます。人時生産性を高めることもできるのです。したがって、中小製造企業は、効率を追いかけるだけでなく、多品種生産にも対応できるようにしておかなければなりません。
経営者は、右腕役や現場キーパ-ソンへ多品種生産のやり方も指導する必要があるのです。根拠のある「手抜き」のやり方を教えます。マスターファイル作成では、特にそうです。
必要以上に精度を高くする必要はありません。推測を用いても良いのです。
多品種は面倒くさいです。ただ、だからこそ、大手は嫌がります。中小の商機はここにあることを現場へ知らせるのは経営者の仕事です。
工程や作業の標準化、規格化では、手順を分類して整理する作業が必要です。具体的なことを抽象化する力、さらには抽象化したことを具体化する力。
標準化と規格化による根拠のある「手抜き」では、具体→抽象→具体の力が、求められます。その結果、管理項目を減らせるのです。
経営者が右腕役と現場キーパーソンを指導します。
次は貴社の番です!!
成長する現場は、標準化、規格化で根拠ある「手抜き」をやり多品種の管理コストを下げる
衰退する現場は、いろいろあって分類は難しいと考えるので多品種を強みにできない