「生産性ロードマップ戦略」—儲かる工場経営を目指して—第41話 真の能率とみかけの能率
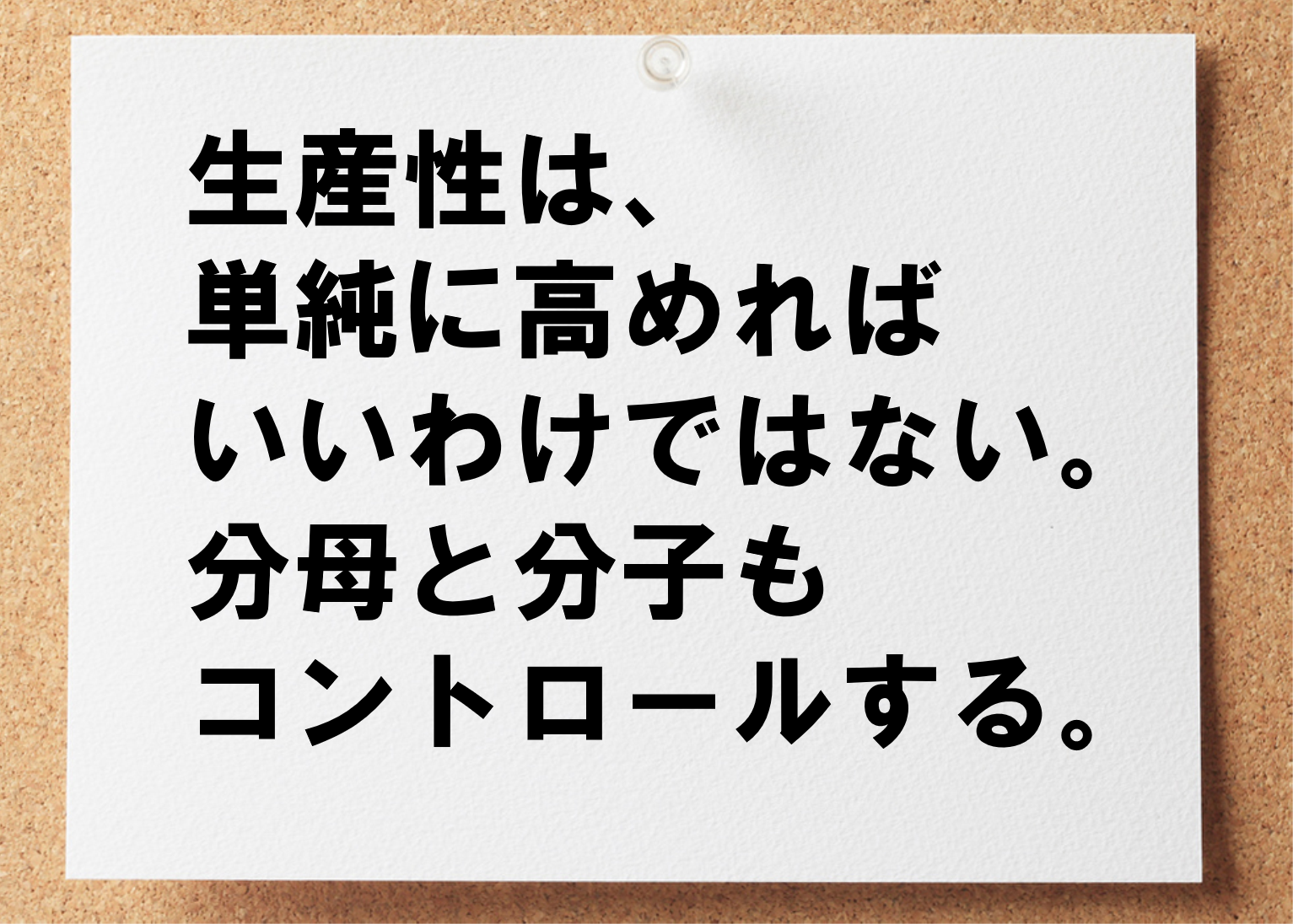
現場で生産性の指標を活用していますか?
目で見る管理では多種多様な指標を活用します。
全体最適化と部分最適化を測る指標を使い分けることが肝要です。
加えて、全体最適化と部分最適化の指標を関連付けることも欠かせません。
カイゼンには大きな目的が重要だからです。
カイゼンに取り組む必然性を現場に感じさせます。
そして全体最適化、部分最適化の指標として頻繁に取り上げられる指標があります。
生産性です。
国内では労働生産性の向上が叫ばれています。
とりわけサービス業の生産性は欧米諸国と比べて低いことが指摘されています。
生産性は投入量(インプット)と産出量(アウトプット)の比です。
インプットは労働量、原材料、投入資本・設備で表現されます。
またアウトプットは物量、金額で表現されます。
したがって、生産性の指標は基本的には6種類です。
製造現場で使われる頻度が高い指標は、インプットが労働量、アウトプットが物量の組み合わせです。
10人で100個生産した。
4時間で20個生産した。
現場では日常的に使われています。
少ないインプットで、多くのアウトプットを得ることを目指しています。
投入する経営資源の効率は高い状態が望ましいです
ですから、基本的に、生産性はひたすら高めるものです。
市場の需要が右肩上がりで増えているとき、つまり造れば必ず売れる時代ならばそうです。
なにせ、造れば必ず売れるのです。
欠品による機会損失のほうがもったいないと判断されます。
こうした経営環境では生産性をどんどん高めるように経営者は現場に発破をかけます。
10人で100個できた現場が、110個できるようになり、120個できるようになれば、生産量の上乗せ分だけ利益も上乗せされます。
10人という経営資源の投入量は変わりません。
したがって、利益を獲得する効率が高まったことになります。
需要が拡大しているときは、生産性を高めれば、結果として利益がついてくるのです。
生産性の数値それ自体に注目します。
さて、今、消費財を中心に国内市場は成熟化という状況です。
少子化による人口減少という背景もあり、今後、特定の製品の需要がどんどん伸びることは考えにくいです。
多品種少量、変種変量の時代です。
つまり特定の製品を大量に造れば売れる時代、ではないということです。
売れないものをどんどん造っても儲かりません。
工程指標である生産性の解釈の仕方も環境変化に合わせて変える必要があります。
需要が伸びている時なら、10人で100個できた現場で、120個できるようになるとうれしいです。
インプットを一定にしてアウトプットを増やすのです。
生産性が10個/人から12個/人に高まっています。
しかし、成熟化に直面した現場に求められる生産性向上は逆です。
アウトプットを一定にしてインプットを減らすのです。
つまり10人で100個できた現場で、8人で100個できるとうれしいのです。
需要が減少するリスクが高まっている昨今、生産性の向上はインプットを減らすことがポイントです。
100個うれているうちはいいです。
もし需要が10%、20%減少して、90個、80個しか売れなくなる事態になったらどうでしょうか。
10人で120個できるようになっていても、もはや儲けにつながりません。
さらに、そのラインは80個しか製造する必要がなくても、10人の作業者を投入しなければ機能しない構成になっているかもしれません。
8人で100個できるようにしておけば、需要が減った時に2人減らして80個生産体制を敷けます。
人件費を変動費化することができるのです。
また、100個生産体制で、高付加価値化を目指す業務へ、2人投入することもできます。
付加価値を創出することが今後の経営課題である中小現場では、固定費を効率的に活用しなければなりません。
トヨタ生産方式の著者である大野耐一氏は、同著で、みかけの能率と真の能率について語っています。
上記の例でいえば、10人で120個できるようにするのはみかけの能率。
8人で100個できるようにするのが真の能率。
大野氏は1970年代で、すでに「低成長時代」を生き抜くことの大切さに触れています。
アメリカ式の量産思想では、量の経済が頓挫すると行き詰まる。
したがって現場は真の能率を目指さなければならいと説いています。
今から40年も前です。
平成バブルがはじける何年も前から、低成長時代をにらんで手を打ってきたのがトヨタ自動車なのです。
その成果が今日のトヨタ自動車の決算に見事に結実しています。
モノづくりに対する経営者の思想がその企業の将来を決めるのです。
生産性の指標ひとつ取り上げても、トヨタの思想は明確です。
生産性の分母と分子に経営者のこだわりが表現された仕組みづくりをしませんか?