「生産性ロードマップ戦略」—儲かる工場経営を目指して—第54話 生産管理の仕組み化を通じて標準を設定する
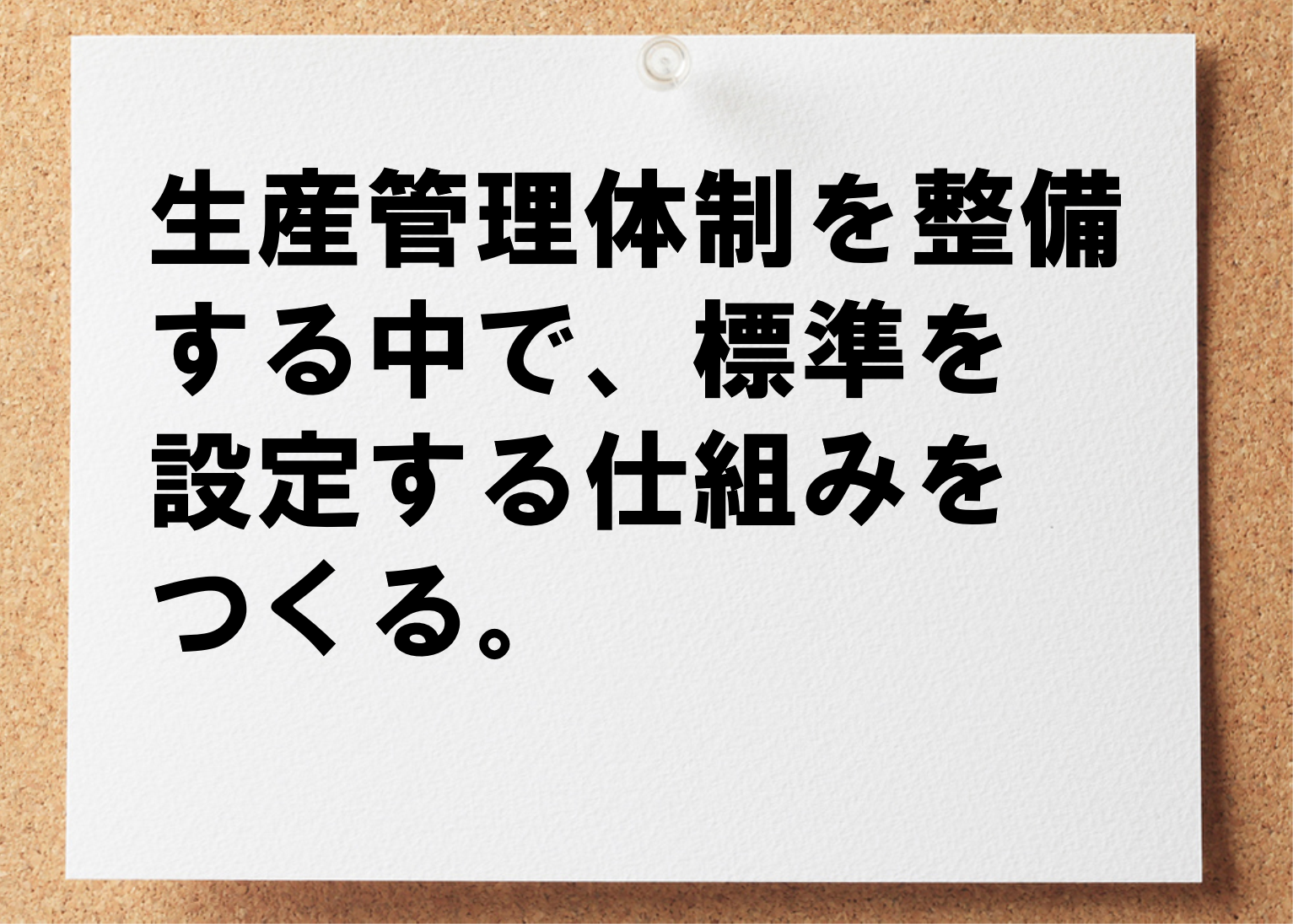
貴社では、生産管理の仕組み化を通じて、標準を設定していますか?
工場経営者の方々には、折に触れて、思い出していただきたいことがあります。
それは、”標準”です。
現場のあらゆる作業に、”標準”が整備されているか、ということです。
さて、改善活動の前にやるべきことがあります。
生産管理体制を整備することです。
部分最適に加えて、全体最適の視点も持つことになります。
そして、生産管理体制を整備する、もうひとつの目的が“標準”なのです。
標準のないところにカイゼンはない。いかなるカイゼンにおいても、その出発点は、現在の立脚点である。あらゆる作業者、あらゆる機械、あらゆる工程に適用される正確な測定基準が必要である。同様に、すべての管理者にとっても測定基準が必要である。
「カイゼン」の著者、今井正明氏の言葉です。
QCDが、モノづくりの3条件です。生産活動は、これら3つの視点から評価されます。
ですから、儲かる工場経営では、QCDの最適化を目指すのです。
大手の現場は、QCD3条件を、機能別に役割分担して管理する体制を敷いています。
規模が大きいですから、品質、原価、納期の管理を専門に担う部署があるのです。
例えば、品質保証部門、経理部門、生産管理部門などがあげられます。
一方、中小の現場では、QCD3条件を、現場で一括して管理するケースが多いのではないでしょうか?
人財などの経営資源に制約があるため、業務分担はできません。
しかし、それは、かえって中小の強みにつながります。
モノづくり3条件を現場で主導するからこそ、中小では、小回り性や柔軟性という強みを発揮できるのです。
3条件の管理方法は、一般的に、
・品質管理
・原価管理
・生産管理
と表現できます。
したがって、これら3つの管理方法のポイントを押さえれば、中小の強みである小回り性を強化できるのです。
そして、その中心にあるのが「生産管理」なのです。
大手は、モノづくり3条件の管理を、専門部署に任せています。
規模も守備範囲も広いので、3条件を管理するには、専門性が必要です。
ですから、3条件を管理するとき、機能別に組織立てられた大手において、”専門性”は欠かせません。
しかし、中小の現場は、大手と違います。
中小で3条件を管理するとき、大手と同じやり方をしても現場に定着しません。
同じやり方をしても、複雑になり、継続性に欠けます。
中小の現場で、モノづくり3条件の管理をうまく機能させるには、中小ならではのコツがあります。
それは、生産管理の体制を、何よりも優先して整備することです。
”流れ”に着目した生産管理の仕組みづくりを優先させます。
品質やコストを議論するまえに、生産管理の仕組みをつくるのです。
さて、貴社の現場では、仕組みがあろうがなかろうが、日々生産活動が展開されています。
モノづくりは、すでにやられているのです。
したがって、最適な生産活動を目指すことは、品質向上やコスト削減より、比較的やりやすい状況にあります。
少なくとも、現場の意識は、”納期”に向いているからです。
そして、モノづくりの”流れ”を改善し、水準を上げると、現場も効果を実感できます。
しかし、生産管理体制の構築抜きに、品質管理、原価管理をやろうとしても、現場活動は定着しません。
活動の目的が正しくても、生産活動が中心の現場にとって、品質やコストの取り組みは、新たな負担となり、長続きしないのです。
生産管理でモノづくりが仕組化されている環境でなければ、品質やコストの取り組みは、成功しません。
標準の有無がポイントとなります。
切削加工を中心とした加工現場の管理者をやっていたときの話です。
加工品の品質向上を目的に、不良要因分析をやろうとしたことがあります。
現場の作業者に不具合事項を記入してもらい、現場リーダーに集計するように、指示をしました。
しかし、期待に反して、正確な情報がなかなか上がってきませんでした。
不良項目、不良原因、数量を関連付け、データ収集したかったのですが、できません。
そこで、現場リーダーや作業者へヒアリングをしました。
分かったことがあります。
加工作業の手順が、作業者の判断に任されていたということです。
つまり、標準が存在せず、作業者は自らの作業の良し悪しを判断する手がかりがない状態でした。
したがって、加工不良の原因を、表現することができなかったのです。
生産現場ではモノの流し方、作業の手順、サイクルタイムなど、モノづくりに関連した一連の流れを明確にしておく必要があります。
標準です。
標準がなければ、現場は、”何が、どう悪いのか”を認識できません。
ですから、生産管理体制が確立された上で、品質管理や原価管理に取り組まねば、活動は現場に定着しないのです。
”良いものを安く”造ろうにも、そもそも、どのように造るかはっきりしていなければ、どうしようもありません。
取り組みが前後しましたが、先の加工現場では、主要部品の加工手順の標準を現場と作成しました。
生産指示から出荷までの生産管理の流れを、見える化したのです。
加工手順の標準によって、加工タクト、作業手順がはっきりします。
作業者と現場リーダーが、良いものつくる条件を共有できます。
そうすると、作業者は、動作チェックの判断基準を持つのです
生産管理体制を整備するとは、生産活動の「判断基準」を設定することに他なりません。
「標準」を設定するとも言い換えられます。
今井氏も著書の中で「測定基準」の大切さ語っています。
これらは、生産管理体制を整備する中で、「標準」という形で整理されていくのです。
「標準」が設定されて、初めて、品質やコストの話ができます。
ですから、生産管理の仕組みを構築してから、品質やコストの取り組みを活動に組み込むのです。
現場の問題は、一般的に、品質やコストという形で現れやすいです。
したがって、多くの経営者は、現れた問題に、焦点を当てやすくなります。
しかし、生産管理体制が整備されていない現場では、作業者は品質やコストの取り組みに負担を感じるものです。
そもそも、生産活動自体が見えていない上に、判断基準がないからです。
自分の立ち位置もわかりません。
生産管理体制があってこそ、改善活動に取り組む必然性を感じることができます。
そうして、現場は、改善活動の成果・効果を定着させていくのです。
立脚点を知らなければ、現場は、改善活動に取り組む必然性を感じることができません。
まずは、「生産管理」です。
そうして、現場のあらゆる活動の標準を設定します。
生産管理体制を整備する中で、標準を設定する仕組みをつくりませんか?