「生産性ロードマップ戦略」—儲かる工場経営を目指して—第89話 悪い情報が現場から上がってくるために必要なもの
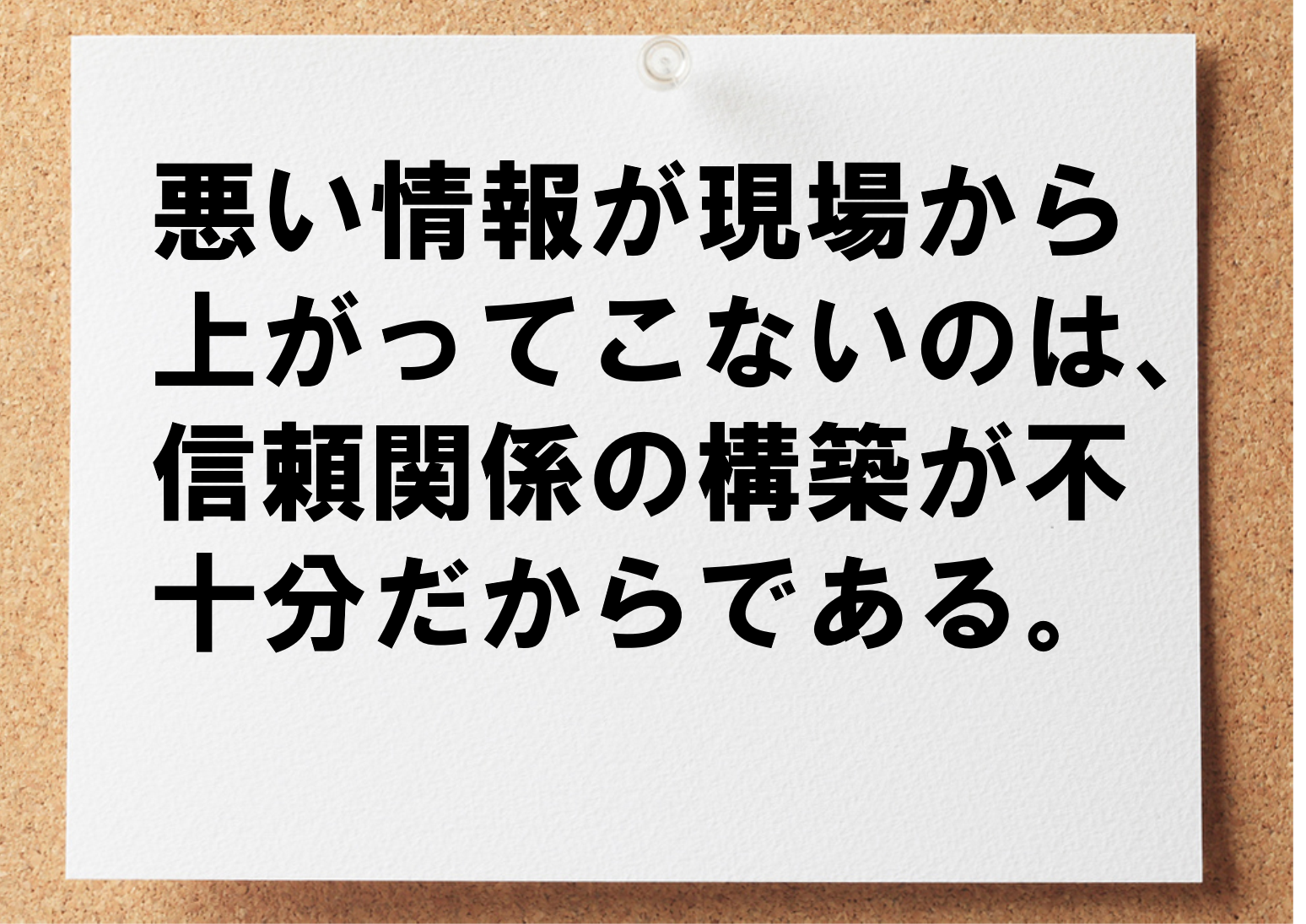
貴社では現場から悪い情報が上がってきますか?
「現場から報告が上がってくるようになりました。」
生産性向上活動を始めた企業の現場リーダーからこのような報告がありました。
この企業では顧客の要望に応じて、半製品に追加工を施し、製品の機能を高める仕事を事業の柱としています。
顧客の半製品が加工対象です。
顧客から、半製品がどんどん送られてきます。
一般的に、原材料の投入から始まるモノづくりでは、品質に関する不具合が発生したら、どのような対応をするでしょうか?
可能な限り手直しをしますが、最後の最後、どうしようもなければ、”廃棄”をし、つくり直すでしょう。
やり直しができます。
しかし、この企業のように顧客の半製品が加工対象である場合、”廃棄”という選択肢はありません。
したがって、加工対象品のハンドリング、および加工作業の精度を高める必要があります。
ハンドリングでミスをして、顧客の半製品にキズを付けてしまった。
加工作業が不適切で、要望された仕様を実現できなかった。
こうした失敗をしたとき、現場ができるのは手直しだけです。
”廃棄”して、顧客が加工対象品を新たにつくって、やり直し・・・、とはいきません。
その企業では、ハンドリングの問題を抱えていました。
1)顧客から受け取った半製品を加工待ち置き場に保管
2)製作手配があったら、加工待ち置き場から加工現場へ移動
3)加工作業後、顧客へ納品
これらの過程で顧客から受け取った半製品を曲げる、キズを付ける、壊す、などの失敗があり、こうした不具合が手直しされないままに納品されることが散発していたのです。
サイズの大きな半製品もあります。
そうした場合は、フォークリフトで搬送をしなければなりません。
半製品を曲げる、キズ付ける、壊すというリスクが、一層高まります。
ハインリッヒの法則として、しばしば取り上げられますが、見えていないトラブルの増加は大きな問題に繋がる懸念があります。
一体どれだけハンドリングでの失敗が起きているのだろうか?
まずは現状を全て把握しなければ・・・。
受注量拡大方針の下、現場リーダーはそう考えるようになったのです。
ハンドリングで失敗しても、自ら、曲がりやキズなどを直す作業者もいます。
ただし、直したつもりでも、不十分でクレームにつながることがありました。
ハンドリングで失敗してキズを付けても、当事者は気が付かず、第三者がそのキズを見つける場合もあります。
ハンドリングの失敗を認識するきっかっけは様々ですが、まずは発生しているハンドリングでの失敗を全て見える化することが必要です。
問題解決では、まず森全体を知る必要があります。
特定の木に気をとられて、的を外した対応になってしまうことは避けなければなりません。
全体を把握して、問題を分類、優先順をつけて対応策を進めるのが定石です。
そこで、現場リーダーは、作業者を対象に、新たなルールを決めました。
加工前の半製品に曲がり、キズ、破損の異常を見つけたら、報告書を提出させるようにしたのです。
ハンドリングで失敗した場合も報告書の対象です。
そして、このルールを開始して、しばらくしてからですが、現場リーダーは、全ての失敗事例が上がってきていないと感じていました。
特に、自分で”やってしまった!”失敗が報告される割合が低いと感じたようです。
実際は、報告がある件数の3倍は発生しているはずだと考えていました。
現場巡視での肌感覚によります。
そこで、現場リーダーがやったことは、次の2つです。
・報告書の様式を簡略化した。
・失敗を罰することが目的ではないことを繰り返し伝えた。
前者では、記述を減らし、場所、モノ、日時の3つに絞ってチェックで状況を表現できるようにしました。
現場に手間を掛けさせない工夫です。
意外と見落とされる論点です。
情報を把握したいあまり、多すぎるほどの記述を現場へ求めることがありますが、提出への壁が高くなります。
また、後者では、自分がやった失敗に関連した報告の件数が少ないことを受けて、日々の現場ミーティングで狙いや想いを伝えました。
・失敗を罰するためではなく、失敗を減らすための対策を考えたいからやっている。
・失敗を報告してくれることは評価の対象である。
・失敗を報告しないことが罰せられる対象となる。
失敗事項、悪い情報を報告させるには、後者がポイントとなります。
その現場リーダーは、失敗を罰するのでないと明言しました。
報告が上がったら個人を責めるのではなく、問題解決のきっかけとしたいのです。
悪意を持って現場で意図的に失敗する作業者は論外ですが、そもそも、そうした作業者はモノづくり現場にはいません。
そうしたことを踏まえて、作業の感情に訴えることが肝です。
そうして、日々のミーティングで、今日はどうだった?昨日はどうだった?と声をかけ続ける訳です。
日々、繰り返し声を掛けてもらうことで、現場には”気軽さ”が醸成されます。
つまり、そこまで言うのなら、こちらも隠さずに報告しないければと現場は感じるのです。
繰り返し、繰り返し、繰り返しです。
信頼関係の構築とも言い換えられます。
悪い情報が上がってくる現場は経営者を信頼しているのです。
困ったことや、悩みごと、自分にとって”悪いこと”は誰に相談しますか?
家族や友人です。
つまり信頼している人たちです。
信頼関係が築けていない人に自分が不利になる話をしたくないのは人間の自然な気持ちであり、それは仕事であっても同じです。
ちなみに、先の現場リーダーの取り組みでは、上記の対応により、それ以前対比で2倍を超える情報が上がりつつあります。
3倍近くと見込んだその現場リーダーの見立てもかなりの精度でした。
現場巡視をしっかりやって現場を把握しているからこそです。
作業者もそうした現場リーダーを信頼しています。
悪い情報を現場から上がってくるしくみをつくりませんか?