「生産性ロードマップ戦略」—儲かる工場経営を目指して—第121話 現場の数値化
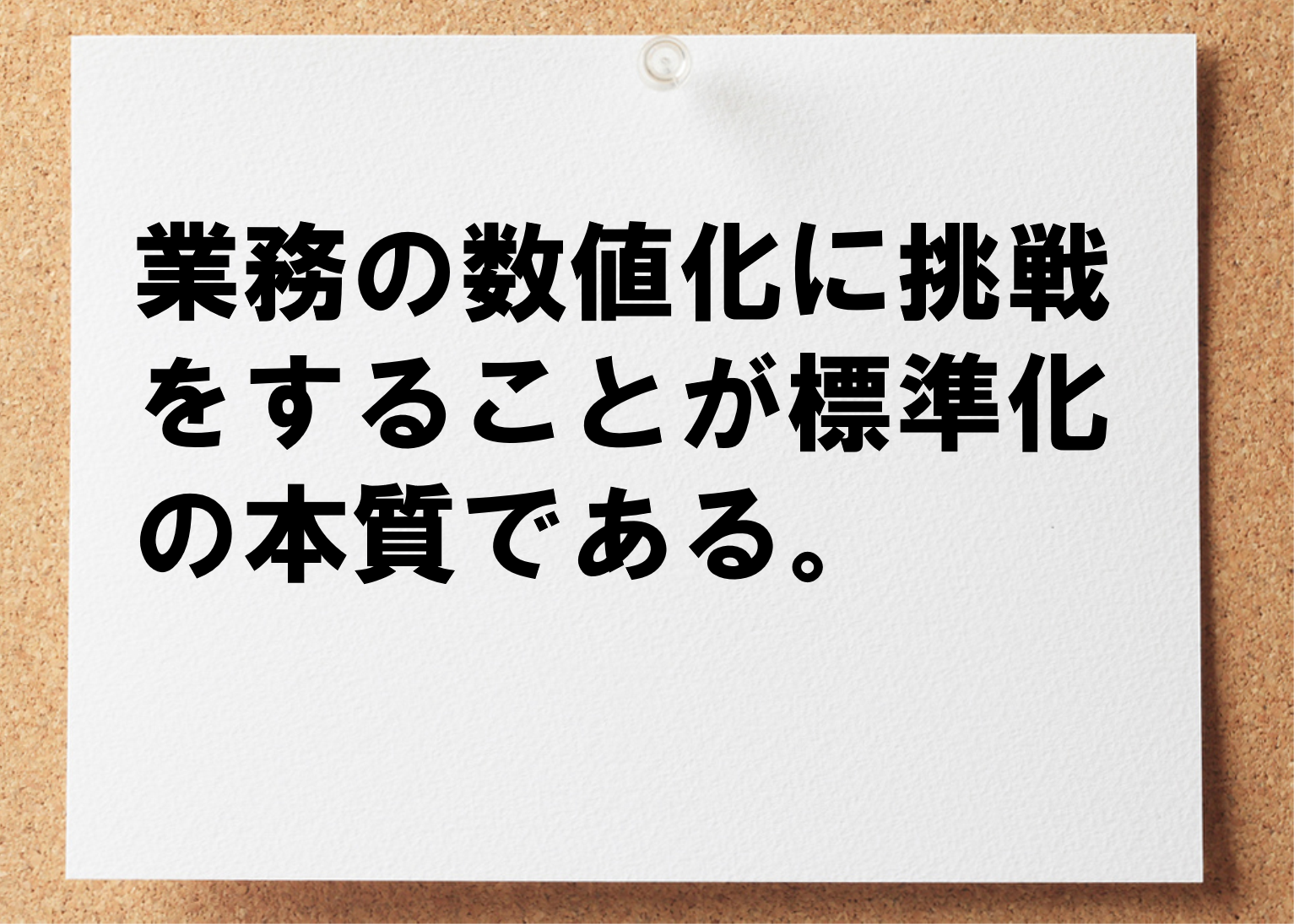
数値化できない業務があると考えていませんか?
「現場のあらゆる業務を数値化すればノウハウとして残せます。」
売上高10数億円規模の金属加工メーカー経営者の言葉です。その経営者は現場を仕切れる右腕役の育成が必要であると考えています。将来、実現させたい事業のためです。
現場力を強化して、現場自ら生産活動をコントロールすることは事業のステージアップに欠かせないことです。経営者が日常的に現場の生産活動を気にしなければならないと、本来やらなければならない仕事に集中できません。
外部環境の変化に対応して先を読み、先手を打つことが経営者の仕事ですから、経営者の意識が”今”にとらわれていると、その分、将来へ向けた作戦を仕掛ける時期が遅くなります。
”今”を現場へ任せることは、事業のステージアップを図りたい経営者の喫緊の課題です。外部環境の変化は待ってはくれません。
最初の言葉を発したのは、そうした危機感を持った経営者です。そこで、”今”を現場へ任せられる右腕役の人材育成に取り掛かりました。
現場を仕切るのに必要なのは部下の仕事をフォローし評価することであり、仕事ぶりの良し悪しを客観的に観る基準が欠かせません。
叱られるにせよ、褒められるにせよ、判断基準が現場と共有化されていないと、かえって現場の不満を助長します。
フォローや評価は現場との信頼関係を築くのに重要な役割を果たします。しかし、一方で、納得感に欠けた場合、かえって面倒なことを引き起こすのです。
ですから、現場の仕切り役を育成するときに忘れてはならない仕事があります。業務の客観化であり、標準化、言い換えると数値化です。仕切り役のための判断基準となります。
先の企業では業務を分析し、標準化していきました。そうした改善活動の成果物を評価して、経営者の発したコメントが最初の言葉です。
儲かる工場経営の仕組みづくりは3つの改革と3つの羅針盤で表現できます。そして、伸び行く”儲かる工場経営”に欠かせないのが生産性向上と人材育成の仕組みです。
3つの改革と3つの羅針盤のフレームワークを使い、取り組むべき具体策を考えます。フレームワークのひとつを構成するひとつが”見える化”であり、活用するのは生産管理です。
生産管理3本柱のひとつ、工程管理は生産の流れをつくる着眼点を体系的に示してくれます。工程管理の着眼点に沿って現場の仕事を分析し、あるべき状態を描いて明文化するのが標準化のやり方です。それは同時にあるべき状態の基準を決めていることになります。
生産性向上にしても、人材育成にしても、標準化に焦点を当てています。仕事の良し悪しを判断する基準抜きにして現場を仕切れるわけがありません。標準抜きのカイゼンがあり得ないのと全く同じです。
そして、標準化で必要となる観点が仕事の客観化、言い換えると数値化なのです。あらゆる業務の数値化に挑戦をすることが標準化の本質でもあります。
数値以外に公平性や客観性を引き出せる道具はあるでしょうか?現場から納得感を引き出すためにも、”数値化”の観点が必要です。
儲かる工場経営のキモのひとつに改善活動とロードマップの連動があります。現場活動が現在および将来のお金を生み出すこととどのように結びついているのかを見える化します。現場関係者なら誰でも知りたいことです。
この原単位を向上させると、○○のお金を生み出すのに結びつく。
多能工化で技能を向上させると、○○の生産性向上と結びつく。
若手を指導すれば、チームワークの醸成に結びつく。
いわゆる成果の因果関係を事前にはっきりさせると仕事の意味付けがなされ、それは、やる気を引き出すことにつながります。
弊社では基本的に下記の連動を考えます。
(1)ロードマップ(中長期経営計画)
↓
(2)年間経営計画
↓
(3)各工程フォロー表
↓
(4)改善活動計画表
↓
(5)生産進捗フォロー表
それぞれ、鳥の目、魚の目、虫の目で現場関係者がベクトルを合わせるのに必要な羅針盤となる道具です。そしてこれらを、数値で連動させます。
ある企業が5年後に売上高現状対比で20%UP、利益を50%UPの目標を掲げたとします。10年後に次世代の経営者へ引き継ぐ構想もあり、若手の採用、次世代の経営者を支える体制づくりが課題です。
それを受けて、毎年の達成目標を設定するのが年間経営計画です。中長期目標を達成するために5年後から逆算して、売上高現状対比で20%UP、利益を50%UPさせるのに、今、何をどうしなければならないのか、数値化します。
売上高〇〇円、利益〇〇円。
工場全体の人員数は〇〇人、総工数〇〇人時、付加価値額総計〇〇円、付加価値額生産性〇〇円/人時、固定費額○○円、損益分岐点比率。
工程別の付加価値額生産性〇〇円/人時、製品別の付加価値額生産性〇〇円/人時。
工程別のスキルアップ度、改善提案件数、作業要領書作成件数、小集団活動実施回数、主体作業率、段取り効率、設備余力率、納期遵守率、納期前倒し率・・・・。
このように数値化された年間経営計画を工程別にフォローするのが工程フォロー表です。そして、中には改善活動も必要な項目も出てくることでしょう。
例えばリードタイム短縮は全体最適化の視点が欠かせないですから、連携して目標達成を目指します。連携力の発揮には共通の目標が欠かせません。ビフォア、アフターが必要です。
製品Aのリードタイム 改善前5.0日 → 改善後3.5日と目標設定をして、目指すところを明らかにします。現在の立ち位置を把握していないと連携のしようもありません。カイゼンに標準が欠かせないと言われる所以です。
さらに、日々の生産活動を対象にした見える化、つまり生産進捗フォロー表も大切な道具です。日々生産実績、累積生産実績、昨日納期案件の実績、昨日指摘された問題の解決状況、本日納期案件の確認、本日懸念される事項への事前対応・・・。
数値化・客観化すれば、それまであいまいだった仕事の中身がはっきりします。役割分担ができる状況に至るので属人的な状況から抜け出せると考えらえられませんか?
道具の中では、(3)が現場を仕切るうえで有益なツールになるのですが、そのことに理解を示す経営者は必ずしも多くないと感じます。上記の構成をお話ししたとき、「?」という表情をされる経営者が少なからずいらっしゃるからです。
納期や生産数、売上高や利益といったマクロ的な数値には慣れているようですが、一方で現場活動を構成する個々の作業、業務の定量化は進んでいないのではないでしょうか?
各工程責任での原単位、稼働率、生産性、リードタイム、業務効率・能率、小集団活動、人材育成・・・、あらゆる業務を数値化してフォローと評価の判断基準を整備したいのです。
例えば作業者がどれだけ付加価値額の積み上げに貢献しているかを示す主体作業率などは現場に気付きを与える指標となります。
かって伊藤が勤務した自動車部品工場の部門長は徹底して仕事の数値化を求めました。あらゆる業務を数値化して業務の客観化を図り、業務の良し悪しを判断する基準を決めたのです。
生産活動の定量化は当然のこと、間接業務に携わるスタッフ部門も自分の業務の定量化をしなければなりませんでした。開発業務、試作業務など、能率や効率とは一見かけ離れた業務も数値化するために知恵を絞ったことを思い出します。
現場からスタッフ、管理職まで工場関係者すべてがそうした仕事のやり方に変えていった結果、月当たり億単位の営業利益を稼げる現場になったのです。それは、その工場で長年、夢として掲げていたことでもありました。
こうした経験を通じて、数値化できない業務はないという考えに至るとともに、チームのベクトル合わせでは数字に働いてもらうのが効果的だと確信を持ちました。業務の判断基準が数値化されると、それを達成しなければならないという気持ちが自然と生まれてくるものです。
あらゆる活動の数値化は標準化に通じます。作業の標準化では、作業を要素に分解するところから始めます。いくつの要素に分解するかを考えるのは、いわゆる数値化、デジタル化の観点です。
カンやコツを整理するため、作業を分割するのは分析の常道です。分割された要素にカンやコツを盛り込み、標準化していきます。その分割が細かくなればなるほどノウハウの密度は濃くなります。
先の経営者が「数値化すればノウハウになる」と言っていたのはまさにこの事です。
生産指標としての数値化は当然ですが、あらゆる業務を数値化するのはノウハウを残すことにつながります。これは事業を成長拡大するときには欠かせない論点です。
なぜなら拠点を増やすときに必要なのは、マザー工場の仕事のやり方をコピーすることだからです。ベクトルを合わせるのに必要なマザー工場の仕事のやり方を可能な限りデジタル化すれば、最小労力で付加価値額の積み上げに貢献する拠点を増やせます。
先の経営者にはこうした目論見もあるのです。拠点を増やしたために混乱が助長されるのでは、何のために拠点を増やしたのかわかりません。
成長する現場は業務を数値化し、ノウハウを見える化しているので、パートや外国人労働者も即戦力にできる現場力を持っています。
現状維持にとどまり、今の仕事のやり方でいいと思い込んでいる現場は人に仕事を付け、業務を暗黙知化のまま放置しているので、人員不足に直面したら衰退の道へまっしぐらです。
数値化する仕組みをつくりませんか?