「生産性ロードマップ戦略」—儲かる工場経営を目指して—第127話 数値を使う
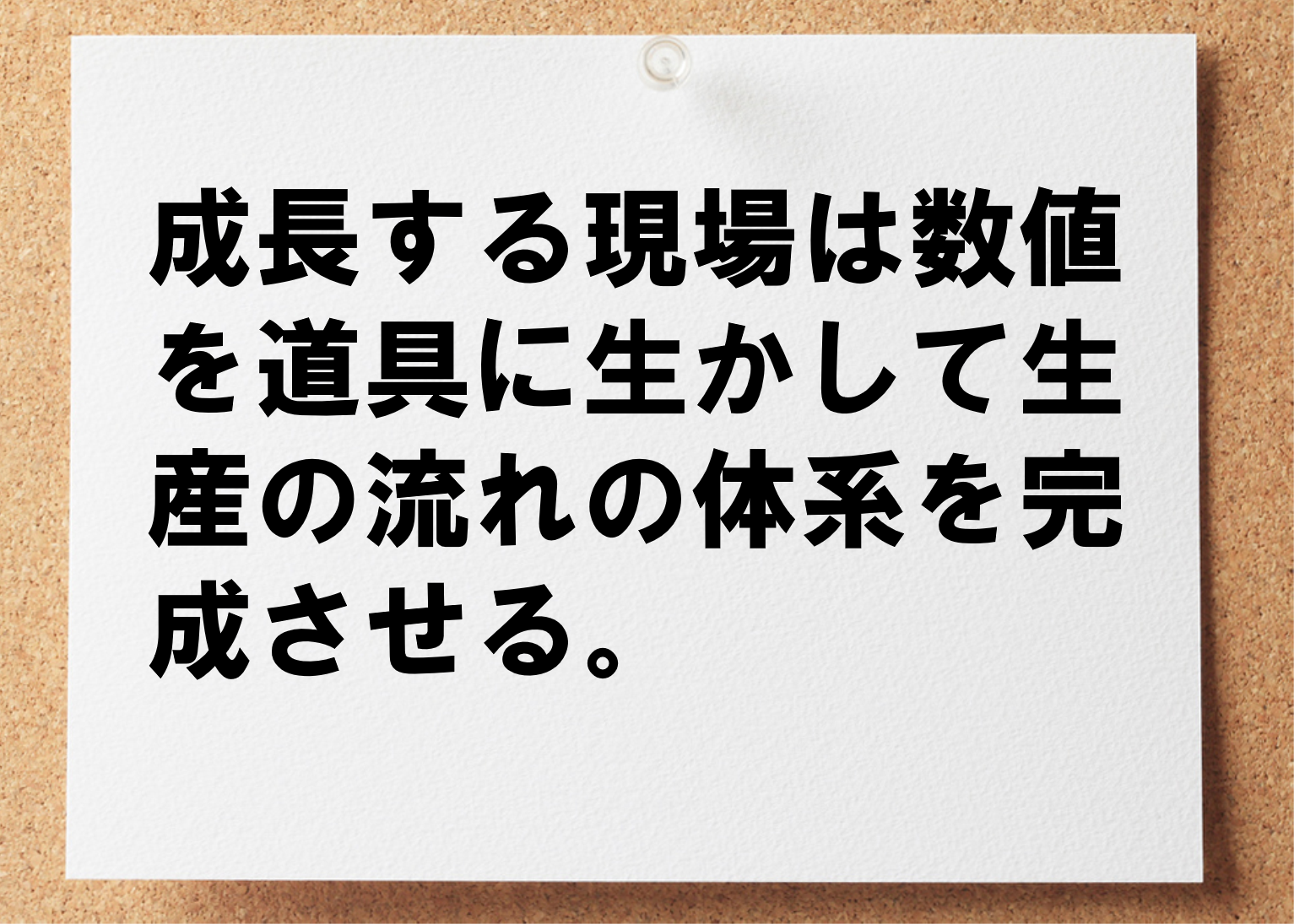
貴社の現場では「数値」を使っていますか?
「せっかく実績値を現場へ掲示しているのに、見てくれる作業者が減ってきました。」
60人規模の中小製造企業、現場スタッフの言葉です。今、継続的な改善活動を目指して現場活動に取り組んでいます。
まずは、見える化で現場を活性化させようと、数か月前から日々の生産実績を現場へ提示し始めました。やってみようと考えたら、即、行動へ移す、フットワークが軽くて一生懸命なスタッフです。
現場にホワイトボードを設置して、そこへ前日の生産実績や品質実績を表示するようにしました。その現場には生産活動での目標値があり、実績が示されれば目標対比で〇か×の判定ができます。
それまでは口頭でやりとりしていた情報が”文字”として明示された効果もあり、そのホワイトボード前で各工程のリーダーたちが話し合う姿を目にするようになってきました。
自分たちの立ち位置や目標を数値で示されると現場は頑張りたくなるものです。その現場も同様でした。特に各工程リーダーの自発性を促すことになり、工程間連携が生まれつつあるのを感じます。
ただ、今、その現場で目指しているのはそのようなレベルの現場活動ではありません。作業者も自ら動いてリーダーをサポートし、チームとして仕事をする水準を目指しています。
ですから、作業者ひとりひとりが生産実績を気にするような雰囲気にしたいとそのスタッフは考えていました。
ホワイトボードを設置した当初はリーダーだけでなく、作業者も表示された実績を気にしていたようです。そのスタッフが、現場巡視の際、作業者へ前日実績を訪ねると、達成したとか達成できなかったとか、少なからず反応がありました。
しかし、その後、作業者からの反応は薄くなり、ホワイトボードの数値を気にしているのだろうか?という疑問がスタッフにわいてきたのです。
先の言葉はそうしたスタッフの気持ちを代弁しています。
経営者が手にしたいのは儲かる体質の事業や現場です。そのためには現場を”変える”こと、変え続けることです。
製造業は技術の世界で戦っています。その技術は日進月歩です。現状維持は相対的な後退を意味します。そうした現場は生き残れません。
ですから、生き残る中小製造企業は、いわゆる”改革”の連続を実践しており、その改革を成功させる土台として現場活動があります。生産活動と現場活動、両者がバランスよく機能していないと”改革”はやり切れません。
中小の現場が生産活動で忙しいの当たり前です。そもそも、生産活動が忙しくない現場は、”今”生き残っていません。”将来”も生き残るには生産活動に加えて、現場活動が欠かせないのです。。。。”変える”ために。
継続的な現場活動の先に改革があります。経営者はそのことに気づく必要があるのです。日々の生産活動の延長線上には改革はありません。
ですから、現場活動を促す仕掛けが重要であり、生産活動で忙しい現場に”生き残り”をかけたプラスアルファの活動(=現場活動)への動機付けが必要となるのです。
日々すったもんだしながら、なんとか納期を順守している現場は青色吐息ですから、”引力”がはたらき、励みとなる「何か」が欠かせません。
そうした動機付けへの手段のひとつが見える化です。そして、弊社では見える化=数値化と考えています。くらべる基準を現場へ示したいからです。
数字で客観化された評価基準を現場へ示すことで、生産活動に加えて、現場活動へ向かう動機づけをします。
誰でも自分の仕事ぶりを評価されたいと感じるものです。自職場を良くしたいと考えない作業者はいません。
ただ、どうしても日々の生産活動にのみに引っ張られることはしかたのないところです。納期は絶対であり、納期遅延は力づくでも回避するような仕事のやり方が普通になっています。
日々の”力づく”が常態化している現場も少なくありません。当然のことですが、そこでは生産性向上やリードタイム短縮に組織をあげて取り組もうという雰囲気が希薄です。
何せ、日々、それどころではないわけで、生産活動に加えて新たなことをやるなんてとんでもない!という思考回路が定着しています。
もともと、その”それどころではない”状況を改善して、楽に仕事ができる仕組みを作ろというのが現場活動ですから、そのことに気付かせることが先です。気付きを与える、きかっけとして見える化があります。
今は問題に直面しているものの、先の現場のやり方は間違っていません。ただし、数値を現場へ表示した後、引き続きやらなければならないことがあるのです。
「ホワイトボードに表示された数字を使っていますか?」
伊藤はそのスタッフへ尋ねました。
弊社のご指導では「生産の流れ」をつくることに焦点を当てています。付加価値額を積み上げるためです。
効率の良い「生産の流れ」をつくれば、目論んだ付加価値額がドンドン積み上がり、それは利益の最大化へつながります。
「生産の流れ」をつくるための継続的な現場活動が、付加価値額を積み上げるのに重要な役割を果たすのです。現場活動を中心にしてあらゆる取り組みを連携させます。
品質や生産性などが低下したら、原因を究明し、改善活動のPDCAを回します。そして、成果を評価して、収益性への貢献度を明らかにし、経営者としての意思を表すのが業務評価制度です。
さらに、歯止めのために標準化や勉強会などにも取り組むでしょう。現場活動は連動させることが必要なのです。弊社では「生産の流れをつくる体系」と称しています。
先の現場のホワイトボードに表示した数値はこの体系の一部を過ぎません。ですから、数値を表示しただけでは、現場の関心も薄れるのです。この数値を「使って」、次の取り組みへ歩みを進めます。
・目標値に未達の日が1か月あたり5日以上の場合、緊急リーダー会議を開催して対応策を協議する。
・目標値に未達だった翌日は毎朝の工程会議で原因を明らかにして課題事項を共有する。
・目標値にすべて達した月は月末に金一封で慰労し、次の目標を新たに掲げる。
などなど。
数値を使って、次のアクションへ繋げます。数値を道具に使うのです。数値は具体的な活動と「連動」させると、「くらべる」判断基準になります。
見える化はそれ自体にとても意味があります。なんの情報も示されていない現場にくらべれば、日々実績が現場へ表示されているだけでも、それは現場を動かすためのりっぱな”仕掛け”です。
ただ、ここまでやられるのならもっと踏み込みこんでいただきたい。貴社の生産の流れをつくる体系の一部として欲しいのです。そうすることで現場は表示された数値を生きた道具として使うようになるでしょう。
日々の生産実績、生産性、リードタイム、品質情報などなど、生産活動を評価する数値は数多あります。
先の現場では、日々実績→累計実績→日々付加価値額→累計付加価値額というように段階的に進め、付加価値額積み上げ状況の見える化が最終目標です。
中小製造企業の経営者には現場へ数値を示す効果を知っていただきたいのです。経営者の代わりに経営者の意思や意図を語ってくれるのが数値でもあります。
・成長する現場は、数値を道具に生かして生産の流れの体系を完成させる。
・現状維持にとどまり、今の仕事のやり方でいいと思い込んでいる現場は、納期以外の数値を知らない。
見える化を生産の流れをつくる体系に組み込みませんか?