「生産性ロードマップ戦略」—儲かる工場経営を目指して—第31話 停滞した現場活動を活性化させるには?
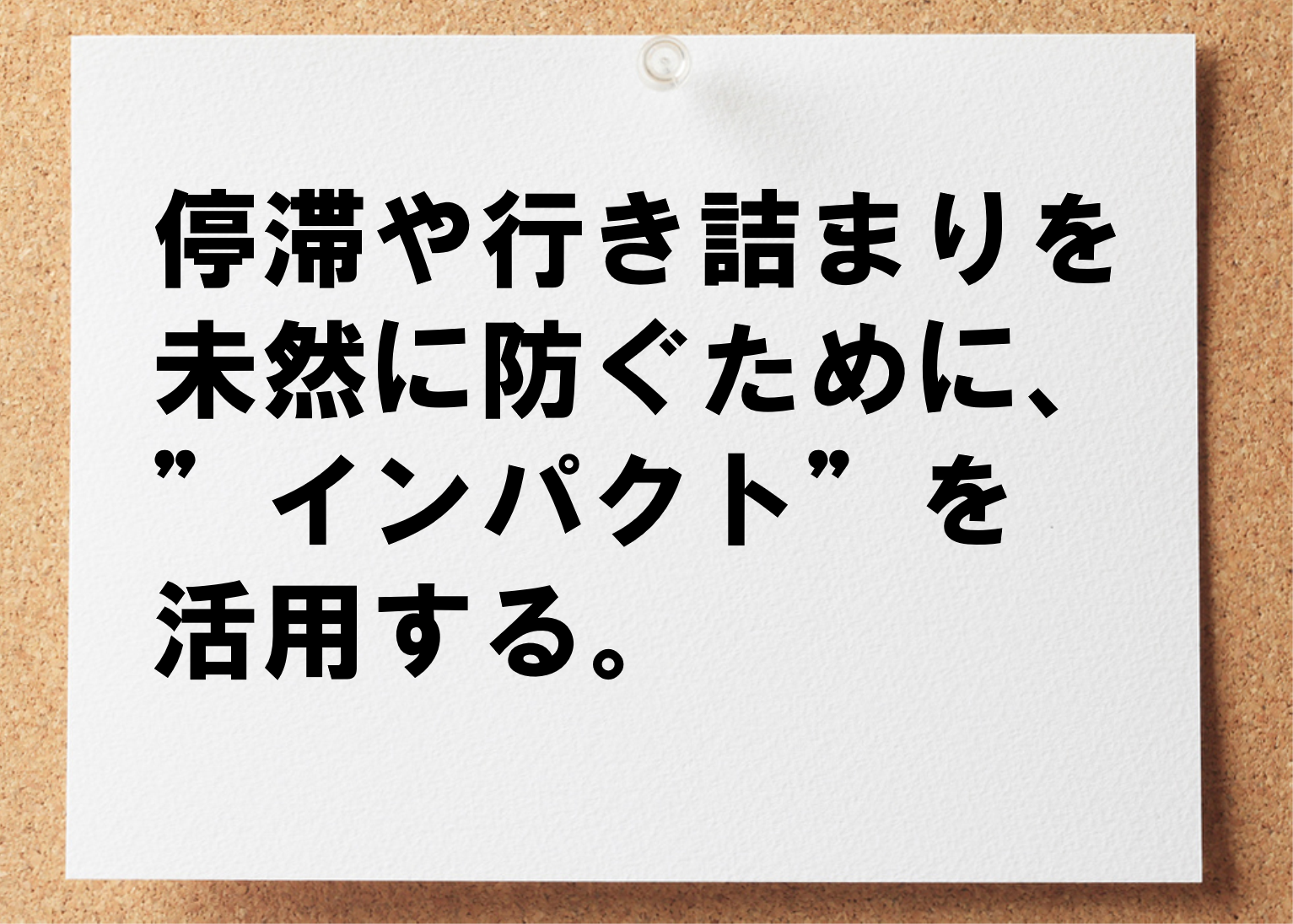
取り組みが停滞したり、行き詰まったりしたら、現場が、”今までとは違うぞ!”とか”今度は本気だ!”と感じる機会を経営者が仕掛ける、という話です。
改善や5Sの取り組みが停滞したらどうしますか?
10年ロードマップ戦略では、カイゼンとイノベーションを連携させます。
イノベーションを目指しつつ、並行してカイゼンに取り組みます。
カイゼンの位置付けをはっきりさせることが狙いです。
カイゼンにも、イノベーションにも、いろいろな役割があります。
繰り返し申し上げていることですが、狙いや目的が不明確な業務は絶対に定着しません。
カイゼン、5Sでは、社長が先頭に立ち、全社一丸となって取り組むことが必要なのです。
大きな目標を掲げているからこそ、現場は取り組みの必然性を感じることができます。
社長が先頭に立っているのですからなおさらです。
ですから、カイゼンは困ったから取り組み始めるものではないことに気付きます。
カイゼンは大きな取り組み(10年ロードマップ戦略)の一部を構成しているのです。
したがって、カイゼンでも、イノベーションと同じく継続性が問われます。
イノベーションの取り組みと同じく、経営者は停滞やマンネリに留意しなければなりません。
イノベーションの取り組みは、課題の技術水準が高いので、長期にわたることが多いです。
”なかだるみ”も生じやすいです。
ですから、マイルストンを設定し、停滞や行き詰まりを未然に防ぎます。
一方、カイゼンの取り組み期間は、比較的短期です。
テーマ選定が短期間で繰り返し為されます。
多くの場合、毎年毎年、現場はテーマ選定という課題を抱えるのです。
テーマ選定作業が毎年繰り返される・・・。
したがって、テーマ選定のやり方を誤ると、カイゼンの活動自体がマンネリに陥る懸念があります。
特に、現場の”自主性”に重きを置いてテーマ選定をさせている経営者は要注意です。
現場にとって、テーマ選定の作業がノルマになっている事例も少なくありません。
これでは、取り組みが停滞し行き詰まります。
現場はもともと、日々の生産活動で手が一杯であることがほとんどです。
納期を遵守することで精一杯。
ご相談を受ける現場で、「日々、余裕がありすぎて困っています」というところは1ケ所もありません。
そもそも人員配置を設計する時に、経営者は生産活動以外の活動も行うことを前提にはしないでしょう。
当然のことです。
プラスαを事前に設置できるほど余裕をもった工場経営が可能な経営者は、ごく少数です。
ですから、どこの現場も、カスカスの人員で日々の生産活動に汗を流しています。
そうした現場にやらせるプラスαの取り組みが、カイゼンなのです。
停滞や行き詰まりを起こさせないためには、経営者の意図を持った工夫が必要になります。
カイゼンの停滞や行き詰まりを打開するきっかけを作るのは、経営者の重要な仕事です。
では、何でカイゼンの停滞や行き詰まりを打破できるでしょうか?
それは・・・・・・・、
”インパクト”です。
現場が、”今までとは違うぞ!”とか”今度は本気だ!”と思う機会を、経営者が仕掛けることです。
従来に無い刺激を受ければ、現場は覚醒します。
現場にはやる気に満ちた若手人財やベテランが必ずいます。
しかし、その一方で、そうした人的資源のポテンシャルを100%、120%引き出し、最大限に生かしているかいうと、そうでない現場も多いです。
とてもモッタイナイ現場をいくつも体験してきました。
経営者が自覚していなくても、まだまだ現場には眠れる資源があるということです。
20%や30%程度のパワーアップは現状の人財のままで十分に可能です。
ですから、そうした眠れる資源に火をつけて、停滞や行き詰まりを打破するのです。
”インパクト”を引き金にして、現場力を呼び起こします。
自社工場にとっての”インパクト”とは何でしょうか?
中小製造企業の現場で新たな管理者として仕事を始めた時のことです。
それまで働いてした大手企業とはなんら繋がりのない新天地としての現場でした。
社長から「現場の黒字化を目指して欲しい」と指示され、新参者でしたが、現場といっしょに汗を流し始めました。
右も左もわからない状況で頼りになるのは、それまでの経験と知識です。
しかし・・・・、
良かれと考えて打った手が、現場に理解されなかったことも数知れず。
知ってもらい、理解してもらい、共感してもらうためにマンツーマンのヒアリングをしたことも数知れず。
できる限りのことを実施しました。
どんな現場にも熱意のある若手人財と頼りになるベテランがいます。
そうした仲間の協力を得ながら、少しづつではありましたが結果を出しました。
その後も、複数の中小製造現場の管理者を経験しましたが、興味深いことに、どこでも状況は同じでした。
あるとき、現場リーダーの役割を果たしてくれていた若手が、こう話してくれました。
「こうしたやり方があることを知りませんでした。自分たちの現場へ来てくれたので刺激を受けました。」
自分がやっていたことに理解を示してくれたことがうれしかったとともに、大きな気付きがありました。
それは、その現場にとっては、伊藤自身が”インパクト”であったということです。
自分としては、現場の立て直しという目的で、これまでやってきたやり方を、駆使したに過ぎません。
現場、現場によっての特徴は当然ありますから、一部アレンジしながら仕事を進めます。
ただし、柱となる考え方は一緒です。
ですから、管理者の立場で仕事をする上で、取り立てて特別なことを展開している感覚はなかったのです。
しかし、一方で、それまで、こうした経験のない現場にとっては、新鮮であったということです。
だから、生産活動で手が一杯でも、プラスαの取り組みに賛同し、実行してくれたのでしょう。
その現場にとっては、新たな管理者がやってきたこと自体が”インパクト”であったということです。
プラスαの取り組みを継続させるのに取り入れたい視点です。
カイゼンは、現場にとって、プラスαの取り組みです。
それに加え、毎年、毎年、テーマを選定して、活動を継続させねばなりません。
ですから、停滞や行き詰まりに陥りやすい点にも留意しなければならないのです。
こうした状況を打開するために、現場が”インパクト”を感じる手を打つのです。
”インパクト”を引き金にして、現場力を呼び起こします。
”インパクト”は、現場に経営者の本気度を伝えます。
停滞や行き詰まりを未然に防ぐために、”インパクト”を活用します。
こうした状況を事前に予測し、打つ手を考えておくことは、あらゆる”仕組みづくり”で欠かせない論点でもあります。
自社工場や現場にとっての”インパクト”は何ですか?
どんな現場にもあるはずです。
改善や5Sの取り組みが停滞したらどうしますか?
まとめ:取り組みが停滞したり、行き詰まったりしたら、現場が、”今までとは違うぞ!”とか”今度は本気だ!”と感じる機会を、経営者が仕掛ける。