「生産性ロードマップ戦略」—儲かる工場経営を目指して—第348話 プラントレイアウトの本質を理解できているか?
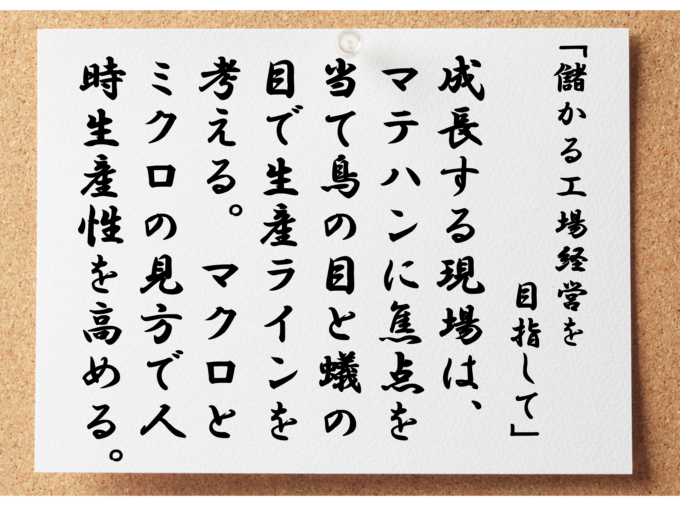
「先生、新しいラインの構想が見えてきました。」
Pjを進めている中堅部品メーカー経営者の言葉です。
この企業では1,2年先を目途に、新たな生産ラインの立ち上げを考えています。今の年商は4億円規模です。先代から事業を引き継いで以降、売上高は横ばいとなっています。
「停滞とは相対的な後退である。」との製造業の特性を理解した経営者です。付加価値額の人時生産を高めなければ生き残れないと考えています。
人時を高める手順を踏まえて、ロードマップを作成しているところです。「投資」で事業を成長させます。技術の世界で戦っている製造業の王道です。
現在の経営資源にしゃぶりつくす余地があると考えています。今の工場で詰めて空けて取り込むことが課題です。分母一定、分子最大化に挑戦しています。
主要なお客様は自動車業界です。手間暇がかかる製造プロセスに特徴があります。難易度の高い仕様をクリアするためです。効率ばかり追いかけると品質低下の懸念があります。
「効率を上げると品質が落ちる。」とは現場から上がってきた言葉です。
当然、手間暇かければ高品質になります。ただし、その考え方では競合と変わりません。競合と同じことをやっても儲からないのが商売です。特に大手と同じ発想では中小は負けます。
品質維持を言い訳にして、手間暇かけているようでは儲からないわけです。トップが現場と同じ発想では現状維持になってしまいます。
こうした外部からの指摘を自己変革の機会としようと考える誠実な経営者です。
先の経営者は、現在の経営資源をしゃぶりつくした先を見据えています。
「将来のために今、現在、何をしなければならないのか?」
これを考えられるのは経営者しかいません。新たな事業モデルを実現する生産ラインです。構想を考え始めて半年ほど経過しました。冒頭の言葉です。
人時生産性向上は2段階でやります。まずは現行の経営資源をじゃぶりつくすこと。次の段階が投資です。分母も増やします。分母を増やす前にやることが、しゃぶりつくすことです。
これ抜きに次の段階へ進むと、工場は「成長」ではなく、「肥大」します。「成長」を知らない現場が設備をたくさん持つことになるからです。
先の現場では、そうならないために、今の機能別レイアウトラインでLT短縮や人時生産性向上を実践しています。1000分台が求められる部位もあり、手間暇がかかる部品です。自動車業界に関連する部品なので基準は甘くありません。
「効率を上げると品質が落ちる。」とはベテラン従業員の言。経営者はその言葉に対して次のように指示をしました。
「技術的に難しいことであるのは分かっている。難しいからやるのだ。競合がやらないからウチはやるのだ。そうしないと生き残れない。」
自身の覚悟を現場へ示した経営者です。目先の話ではありません。1年、2年先のことです。できないことをできるようにならないと競合を出し抜けません。スケールメリットに依存しない中小製造企業の方針はそうなるのです。
1年、2年先の投資に向けて、先の企業でのしゃぶりつく論点は「効率を上げると品質が落ちるという常識を打ち破るやり方」の探索、となります。
これが、その企業独自の人時生産性向上の論点です。人時生産性向上の2段階目を実現させます。改善水準ではなく、イノベーション水準を狙いたいのです。更新投資ではありません。
人時生産性向上には手順と段階があることに留意してください。
先の経営者の「新しいラインの構想」とはプラントレイアウトのことです。
「プラントレイアウト」とお伝えすると、「いやいや、うちはそんな規模ではありません。」と考える経営者がいます。プラントレイアウトは規模に無関係で必要な概念です。ファブレスではなく、実体のある「モノ」を流すなら必要な論点になります。
プラントレイアウトは設備の置き方であると考えている経営者がいます。だから、規模が大きな工場ではスペース問題が出てくるので大事であると考えているるようです。先の経営者もそうでした。間違えではないのですが、的は射ていません。
プラントレイアウトの本質はマテハンだからです。
設備の置き方はマテハン検討の結果であり、目的と手段を取り違えています。プラントレイアウトの目的は収益最大化、そのためのマテハンです。製造活動=マテハンはプラントレイアウトのお作法です。現場のキーパーソンが管理します。
LT最短化を狙いたかったら、答えは製品別一貫ラインにあります。しかし、この形態では柔軟性や機動性が落ちるのです。
したがって、多くの中小現場は機能別ラインになっています。貴社もそうなっているはずです。従来の経験を踏まえて、この辺りに設備を置けばうまくいくと多くの中小製造経営者は経験則から判断します。
ただし、自由度が高い現場は無駄の放置と表裏一体です。これは、当事者には分かりません。それでずっとやってきているので、そのやり方自体に無駄を感じないのです。
効率最大化、LT最短化を実現させるプラントレイアウトの理想形は製品別一貫ラインにあります。したがって、製品別一貫ラインでのマテハンがひとつのひな形です。
運搬活性指数をみても明らかなことです。そこで、製品別一貫ラインをひな形として、自社の機能別レイアウトに取り込める要因を見つけ出し、自社の技術にするのです。
プラントレイアウトはマテハンから考えます。
「新しいラインの構想」を検討するとき、経営者は衆知を集めます。右腕役や現場キーパーソンの持っている知恵やノウハウを生かすのは大事です。
しかし、工場を仕切る右腕役、あるいは現場キーパーソンが直面する壁があります。効率最大化、LT最短化を実現させる製品別一貫ラインでのマテハンを知らない場合が多いということです。
ひな形を知らなければ、ひな形は描けません。アラスカ、エスキモーの人達にサバンナを駆け巡るライオンを描けと言っても見たことがなければ無理です。
いきおい自社で経験してきたことが最良と思い込むことになります。これでは成長できません。異質なことに触れていないとそうなります。
したがって、経営者は工場を仕切る右腕役や現場キーパーソンに、プラントレイアウトは設備の置き方ではなく、マテハン検討に本質があり、効率最大化、LT最短化のひな形は製品別一貫ラインにあることを教えなければなりません。
知らなければ考えられないからです。
ただ、これはたいした問題ではありません。右腕役や現場キーパーソンが知らないというなら、外部に見に行かせて学ばせる、知っている人に教わって学ばせる、学べばいいだけです。
ここは経営者が悩むところではありません。時間がもったいないです。
我流でやっても間違えます。経営者は一日でも早く右腕役に工場を任せ、市場へ向き合って社長業に専念しなければなりません。
新しいラインや工場を造る目的は何か?
これは設備投資で不可欠の論点です。売上高を増やしたい、生産数量を増やしたいなどの表層的な考えだけでは成り行き経営になってしまいます。投資効果が見えてきません。
新しいラインや工場を造るときの論点として欠かせないのがマクロとミクロの判断基準です。鳥の目と蟻の目の判断基準です。
なぜ、巨視的と微視的が必要なのか?
新たなラインや工場では、これまで我が社でできなかったことをできるようにする技術を取り込むからです。その評価をしなければ新技術開発の評価をできません。
コア技術をミクロでチェックし、生み出される儲けをマクロで評価します。
小さくチェック、大きくチェックです。
具体的には付加価値額の人年と人時の生産性を組み合わせます。ざっくり一人頭で評価しながら、小さく時間単位でチェックするのです。
まずは人年で事業モデルの確認です。ラインに配置する従業員数の目途を付けます。そうして、工程別の人時生産性、時間単位の検証です。
プラントレイアウトは事業モデルの根幹をなします。現場活動はプラントレイアウトの上で成り立っているので、改善活動の80%は概ね、プラントレイアウトで決まるものです。
大手のやり方も踏まえて、最良のマテハンを決断するがプランとレイアウトにおける経営者の仕事になります。
先の経営者は決定した構想に基づいて、1年先、2年先のために今やらなければならないことを検討中です。
新しいことに挑戦する場合、試行錯誤は避けられません。ただ、避けられる試行錯誤なら避けた方がイイに決まっています。時間を買っている経営者です。
弊社も大手の事例や中小の事例を経営者の方々と学びながら、ご支援を進めています。経営者に必要なのは、正しい判断と、さらには正しい判断をするための適切な助言です。
我流と独自は違います。我流は思い込みからなるものです。独自は体系の上で構築されるものです。弊社が多くの中小製造経営者の方々に人時生産性を高める考え方を知っていただきたいのは、我流に陥って時間を無駄にしてもらいたくないからです。
気が付いたらもう今年も3か月(4半期)過ぎていたとなっていませんか?
光陰矢の如しです。
次は貴社の番です!
成長する現場は、マテハンに焦点を当て鳥の目と蟻の目で生産ラインを考える
衰退する現場は、我流と独自を勘違いして、勝手な思い込みでラインを考える