「生産性ロードマップ戦略」—儲かる工場経営を目指して—第355話 現場に考える力を持たせたかったらどうするのか?
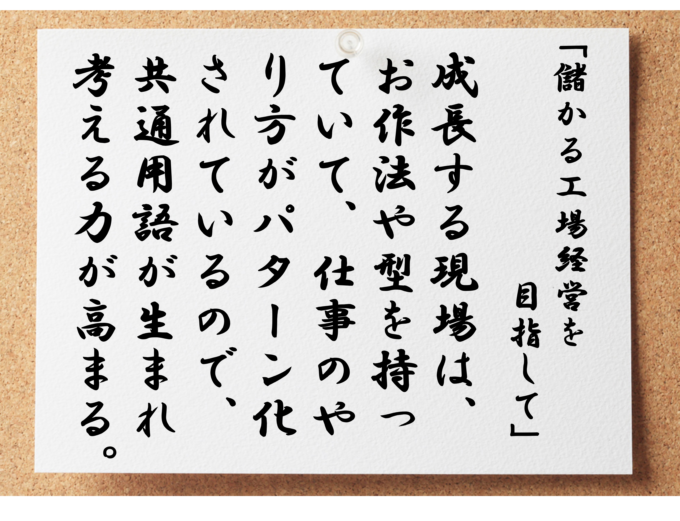
「先生、自分で考える現場に変えたいです。」
20人規模電子部品メーカー経営者の言葉です。
地元に根差した事業を展開しています。ただ、従来の事業モデルでは成長が望めなさそうです。経営者は地元の大手企業に依存しない事業モデルにしたいと考えています。
そうであるなら、新たなお客様を開拓しなければなりません。まだ見ぬ将来の主要なお客様とのご縁を引きよせる必要があります。トップ営業です。
HPで情報発信していますが、それだけでは「待ちの姿勢」のようで物足りません。もっともっと外へ直接に働きかけるつもりです。
そのために何が必要か?
その答えが冒頭の言葉です。工場のことを現場に任せられるようにしないと、経営者は外での仕事に専念できません。現場キーパーソンの考える力を高める環境整備が経営課題です。
人時生産性を高めるためにリードタイムを短縮します。工程管理の目的はこれです。
納期遵守は競合先でもやっています。競合先を出し抜くにはそれ以上のことをやらなければなりません。工程管理を生かす仕事のやり方も変わってきました。
今の工程管理に求められるのは、リードタイムを短くするタイムマネジメントです。
経営者は、繰り返し、繰り返し、そのことを現場キーパーソンへ説きます。
繰り返し説けば、現場キーパーソンの思考回路にリードタイム短縮タイムマネジメントが定着するのです。現場は自ら考えるようになります。
そうして、経営者は工場のことを現場に任せられるようになるのです。
右腕役の育成は、経営者が外の仕事に専念するための必要条件と言えます。考える力を持った右腕役が育つ環境が不可欠です。
人を育てようとしても、簡単に育てられるものではありません。貴社の現場キーパーソンの言動を眺めて下さい。
頼りになる現場キーパーソンは当事者意識が高く、使命感があると感じませんか?誰かに教わってそうなったのではなく、その人の生き様がそうさせています。
育つ人材は勝手に育つのです。勝手に育つので、環境の整備が大事な役割を果たします。経営者の言動以上の従業員が育たないのはそうした理由からです。
我が社のことを自分事のように感じながら仕事をしてくれる従業員は貴重な人財です。そうした人財は「自分がやらなければ。」という思考回路を持ってくれます。経営者の意志や意図に共感してくれているのです。
その心意気を成果につなげさせるのに必要なものがあります。考える力です。心意気だけで成果が出るほど製造業の現場は単純ではありません。
感性や感覚だけで現場を仕切ろうとしても行き詰ります。考える力を高める環境の有無が貴社の命運を左右するのです。
考えるには知識が必要です。お作法があるから画期的なアイデアが生まれます。ブレークスルーは型破り、守破離と言われるように、従来のお作法を超えて起きるものです。
製造現場でのお作法は生産管理3本柱と言われます。製造業で儲けるお作法です。
現場キーパーソンがお作法を身に着ける環境が整備されていますか?
技術開発で最初にやることは、既存技術の徹底的な調査と研究です。既存技術の限界を知った先に、独自性が生まれます。
型がなければ破りようがありません。守るものがあるから、それを壊せます。考える論点を提供してくれるのがお作法や型です。
お作法抜きの独自性は勝手気ままな我流に陥ります。
例えば、リードタイム計算のやり方にも手順があります。リードタイムを評価する目的は2つあり、目的に応じて計算のやり方も変わるのです。
●ひとつは日程計画基本データのためです。
この場合、製造ロット毎の製品1個当たりリードタイムを計算します。
工程リードタイムと製造リードタイムの実績値を蓄積すればスケジューラーのマスターができます。さらにこれらは現場の成績表に活かせます。作業者の仕事ぶりをフォローして評価するのは現場キーパーソンの大切な仕事です。
●もう一つは工場指標のためです。
この場合、お客様別平均、製品別平均、工場全体平均の製品1個当たりリードタイムを計算します。
ここで知りたいのは収益性の推移や変化です。将来の見通しを示してくれるのは指標の推移や変化です。我々が正しい方向へ進んでいるかどうかを教えてくれます。
指標がない工場経営は羅針盤のない航海と同じです。不安にさいなまれます。製販一体のベクトル揃えもできません。
さらに、平均を計算するにしても
「製品1個当たり」なのか?
「製造ロット1ロット当たり」なのか?
正しく考えられないと現場はこのあたりをなんとなくやるだけです。経営者は正しく考えるための知識を現場キーパーソンへ教えます。
パターン分けは正しく考える要点のひとつです。闇雲な思考は、我流なので共通用語も生れません。パターン分け、型、手順が考える力を高めてくれます。
1.リードタイムは、かくかくしかじかで構成されている。
2.構成要因を踏まえると、リードタイムを決める項目は○○と▽▽、□□・・・である。
3.○○でリードタイムが決まる場合、○○をいじればリードタイムは短くなる。
4.さらに▽▽でリードタイムが決まる場合、▽▽をいじればリードタイムは短くなる。
5.また、□□で・・・
6.そして、そうでない場合は・・・
考える手順。これが型です。生産管理3本柱の知識とはこうした型に他なりません。
華道にも流派があります。池坊、小原流、草月流。それぞれ独自の型があるのと同じです。考える力の源はここにあります。
型があるから、仲間との共通用語を持つことになり、型があるから、仲間とそれを破り、壊したくなるのです。お作法が我々を導いてくれます。考えるには知識が必要です。
儲けるために考える。
これを実践できる従業員が多い現場は儲かります。トヨタ生産方式でしばしば言及される7つのムダ。トヨタの現場では、このお作法が徹底されていると想像できます。
座学で、実務で、繰り返し、繰り返し教えているはずです。「なぜを5回繰り返す」も有名な思考回路と言えます。トヨタの型です。
型があるから考える力が高まります。壊すべきものが明らかだからです。共通用語も生まれやすいので独善、我流にも陥りません。
「自分のやり方が一番だから、自分は自分のやり方で仕事をする。」というベテランをご支援先の現場で見かけることがあります。共通用語になっていないので、独善、我流です。
成果が本人ひとりの範囲で限定的です。チームで仕事をしなければならないのに相乗効果がゼロ。本人はこれでイイと思っているので気の毒です。
経営者は知識を身に着け、考える力を磨くよう促します。我が社の型を伝えるのです。型がはっきりしていなければ、お作法や型をつくるように指示します。経営者の意志や意図を伝えることも要点です。我が社のお作法や型が考える力を高めてくれます
弊社がプロジェクト方式でご支援するのは、知識を座学と実践で伝えたいからです。生産管理3本柱は実学です。現場キーパーソンは実践を通じて知識を習得します。
ただし、闇雲に現場活動をやってもダメです。
型を教える、知識を身に着けさせるという経営者の意志と意図がないと、共通用語を生み出す知識が蓄積されません。
・利益は製品1個1個にぶら下がっていない。
・最終検査を強化しても儲かる品質管理にならない。
・納期遵守だけでは儲からない。
これらは全て知識です。生産管理3本柱のお作法、型とも言えます。考えるためには正しい知識が必要です。教えなければ知識は身に付きません。
「感覚で説明していてはいつまでたっても考える現場にならないということですね。」先の経営者は考える力を高める要点に気付きました。
次は自社の番です!
成長する現場は、仕事のやり方がパターン化されているので共通用語が生まれ考える力が高まる
衰退する現場は、独善、我流の仕事のやり方に陥るため共通用語ができず考える力が高まらない