「生産性ロードマップ戦略」—儲かる工場経営を目指して—第435話 現場へ在庫の上手な使い方を教えているか?
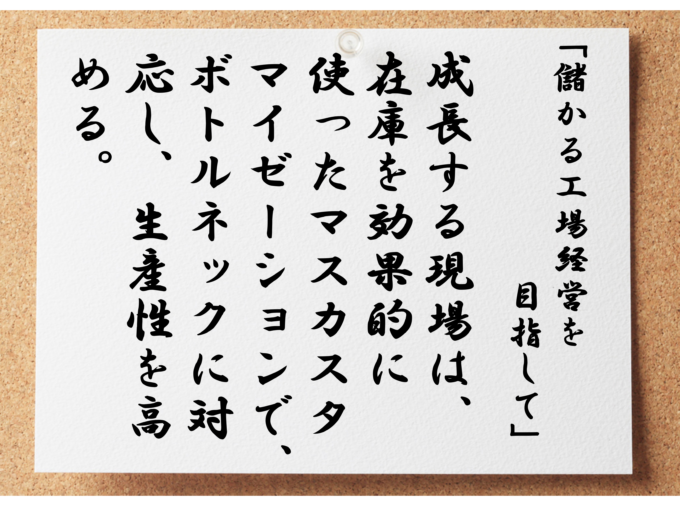
「原材料を早めに切断すればいいです。」
50人規模板金加工企業、工場長の言葉です。
実践会を始めて3か月が経ちました。工程フロー図をもとに現場の流れ分析を終えたところです。ボトルネックを認識したいからです。工場の生産能力はボトルネックで決まります。
この現場の工程フローは、主に、材料取り→板金加工→曲げ→塗装→梱包です。このうち板金加工工程がボトルネックになっています。
生産能力最大化の要点は板金加工工程の稼働率です。この工程を止めないようにします。前工程で処理された切断品を滞りなく送り込む必要があるのです。
しかし、板金加工工程の段取が終わっても、届いていないことがたびたびあります。作業指示が出てから材料取りをしていますが、板金加工に間に合わないことが起こっているのです。
工場長が冒頭の解決策をあげてくれました。
棚卸資産は重要な管理項目です。棚卸資産は運転資金と関連します。在庫を小さくできれば身軽な工場経営ができるので、「在庫の存在自体がよろしくない」と考える向きもあります。
ただし、必要以上に在庫を圧縮してしまうと、機会損失を招いてしまうのも事実です。いざ加工を始めようと原材料置き場へ材料をとりにいったら、該当する材料がなかった・・・。こうした時に限って、関係ない材料の在庫はたくさんあったりします。
必要なモノを必要な時に準備するのが原則です。
一方、その場合、現場の組織能力も問われます。在庫圧縮を実現するには、ルールをつくり、それを遵守するチームの総合力が必要です。したがって、チーム力が発展途上にある現場では、無理をせず、一定水準の在庫を持って対応します。
機会損失を回避する現実的なやり方です。在庫圧縮は機会損失とのもろ刃の剣ですから、ここは注意を要します。
在庫はその存在自体が悪なのではなく、計画性のない、意図しない在庫が悪です。儲けるために経営者が意志や意図を持って計画的に溜める在庫は別です。
先の現場では、作業指示が出てから、上流工程の材料取りをやっています。現場にモノが滞らないようにとの経営者方針があるからです。経営者の意志や意図が現場に浸透しています。素晴らしいことです。
ただ、板金加工への切断品供給に遅れがあることへは、何らかの手を打たなければなりません。受注生産の生産形態に、一部、見込み生産の機能を持たせます。
この企業で扱っている製品は一定水準、規格化、標準化されています。商品群が3つです。
お客様の要望に応じて、多様な寸法、多様な材料、多様な組み合わせの商品を提供しています。規格品ではありますが、多品種が行き過ぎて、特注品を扱っているような感じです。
「ウチは品種が多すぎて・・・・」が工場長の口癖になっています。
ただ、本質的には規格品です。ここに儲けのカギがあります。
そもそも、規格化、標準化するのはなぜか?
製造の手間暇を軽くして、ドンドン積み上げるためです。
大手は価格戦略で攻めてきます。圧倒的な効率で規模の経済を最大化させるのです。設計と製造では徹底的な規格化、標準化をやります。物量で攻めるのが大手です。
したがって、少数精鋭の私達は、多品種少量生産でお客様に選んでもらいます。
ただ、多品種少量生産であっても、職人が木彫りの熊を丁寧に一品一品、仕上げるがごとく製造しているだけでは、数量を積み上げられず、儲かりません。
したがって、経営者は、特注品の個別生産に規格品のロット生産や連続生産のやり方を組み込んで効率化も考えるのです。
先の現場では、多品種が行き過ぎて、特注品を扱っているような感じを持っています。しかし、商品群が3つあるように、主要商品はあくまで規格品です。
規格品ですから、繰り返し使われる部品があります。多品種であっても、お客様からの要望が多い仕様があるものです。
これまでの実績を振り返れば、その部品の一定期間で必要な生産数量を見通せます。
そうすれば、その一定期間で必要な生産数量の部品を見込生産できるのです。見込生産はお客様の納期ではなく、我が社の納期でつくれます。現場のストレスも減るのです。
見込生産する部品は中間製品として管理されます。在庫として管理されるので、必要な時に、必要なだけ供給できるのです。棚卸資産が増えますが、計画的にやれます。
機会損失と比べれば、損得勘定の上で、どちらが積み上げに貢献するかは明らかです。
先の現場では材料取り工程で、特定の部品を見込生産することにしました。
このやり方にすれば、工程管理の負荷を減らせます。該当の部品の物流は押出式ではなく、引出式になるからです。現場に任せられます。これは、現場の意識改革にも貢献するのです。
少数精鋭の中小製造現場の多くは多品種対応です。差別化戦略だからです。@付加価値額を少しでも多く稼ぎます。ただし、一方で効率化も考える必要があるのです。
手間暇ばかりがかかると、稼ぐのに必要な物量の積み上げができません。
・製造する商品や製品の@付加価値額を高める一方で製造コストは最小化する。
この考え方が大事になります。
マスカスタマイゼーションです。
自動車の組み立て工場が代表的な具体事例となります。部品を見込生産する一方、お客様の多様な要望には受注生産で応えるのです。要点は規格化、標準化にあります。
・複雑に見える商品や製品、作業を分析、整理し、「共通点」を見つける
儲ける中小製造現場に求められる能力です。
先の現場では板金加工工程がボトルネックです。ボトルネックへの対応は「絶対に止めない」です。製造頻度が高い製品の部品を中間製品として先行してつくり、在庫管理するのはボトルネック対応にもなっています。
ムダな在庫は悪ですが、生産性向上に貢献する在庫は大いに生かしたいのです。現場へ在庫の上手な使い方を教えていますか?生産性向上の具体策です。
製造業の本質は、「できないことをできるようにすること」にあります。
商品開発でも、技術開発でもそうです。競合と同じことをやっても勝てません。競合に先駆けてやることが要点です。
経営者はドラえもんのポケットのように多くの引き出しを持つ必要があります。できないことをできるようにするネタは多いほどいいのです。
そして、そのネタは全て外(市場)にあります。内(工場)にはありません。だから、経営者の仕事場は外にあると申し上げています。
そして、分からなければ、知っている人に教えてもらえればいいのです。意欲的な経営者は決断と行動が早いです。タイム イズ マネー。
このプロジェクトのメンバーは、そんな経営者に導かれている右腕役や現場キーパーソンです。感度が高いメンバーなので実践会がドンドン進んでいます。
次は貴社が挑戦する番です!
成長する現場は、マスカスタマイゼーションを使ってボトルネックに対応し生産性を高める
衰退する現場は、品種が多くて手間暇がかかるから何もできないと考え新たな挑戦をしない