「生産性ロードマップ戦略」—儲かる工場経営を目指して—第440話 進捗を前から追いかけ、知恵を蓄積しているか?
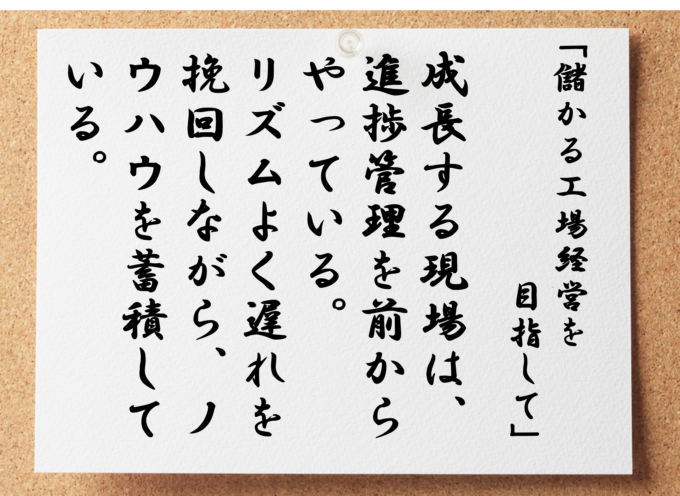
「ベテランの経験に任せています。」
プロジェクトに着手した経営者の言葉です。
リードタイムで納期を管理できていると、人時生産性を高める取り組みが進みます。
しかし、今の我が社でやられている日程計画と進捗管理には、リードタイムという考え方がありません。納期、出荷日にのみ焦点が当たっているのです。
お客様の納期に間に合わせるのが仕事になっています。現場には、リードタイムを短縮するという発想もありません。そもそも日程計画自体が無いのです。
では、今、どうやって、日程計画と進捗管理をやっているのか?冒頭の言葉です。
現場は、ベテランが経験から導き出した製造納期にしたがって動いています。
日程計画は生産活動の進捗確認に欠かせないものです。日程計画を立てず、納期だけで進捗を確認するやり方では、現場は辛くなります。進捗を確認するきっかけが納期だけです。
例えば、各工番の納期3日前になった時点で進捗を確認するとします。
現場は、提示された納期を遵守しようと、経験的に判断した順番で工番をさばいていきます。その中で、日々、納期3日前の工番をピックアップするのです。
残り3日で製造が完了するか?これを判断します。もし、完了しそうにない工番を認識したら、追い込みをかけるのです。
このやり方では、遅れを認識するのは、いつも納期直前になってしまいます。遅れを挽回するにも時間が足りません。
遅れ挽回では、残業、休出が常態化します。現場には大きな負荷がかかるのです。後ろから追いかける進捗管理は現場が疲弊します。
日程計画は、製品別日程計画がスタートです。そこから工程別日程計画へ変換して使用します。作業指示は工程毎に出すからです。
多くの現場は工程単位のチームになっています。
小日程計画の目的は日々の作業指示です。
機能する小日程計画の多くは、工程別日程計画になっています。工程別の日程が計画されていれば、進捗確認は簡単です。日々、やることは自然と決まります。
昨日どうだった?今日の予定は・・・、これだけです。
各工番が、予定された工程に至っているかどうかを確認します。その日に通過する工程をミクロの目で確認するのです。
予定通りの工程を、予定の日時で通過中ということは、そのまま行けば、納期は自然と守られます。納期自体を特別に意識しなくてもイイのです。
そして、遅れを認識したとしても、挽回の負荷は大きくありません。昨日、遅れた分だけの挽回となります。
ミクロの目で、昨日どうだった?今日の予定は・・・、これだけです。
工程別日程計画を上手に使っている現場は、この辺りのやり方を、独自に工夫しているようです。前から順に追いかける進捗管理は現場にリズムを生み出します。
日程計画の基本はガントチャートです。時間軸に沿って予定が立てられます。個別生産や小規模なロット生産はこれで進捗管理をやります。進捗確認の観点が「過程」です。
一方、大規模なロット生産や連続生産の進捗管理の観点は「数量」です。予定通りの数量生産できたかどうかを確認します。多くの現場で使われているのは流動数曲線です。累計数値の遅れを見える化しています。
進捗管理の観点が「過程」なのか?「数量」なのか?あるいは両者なのか?全ては生産形態次第です。
ただし、全ての生産形態に共通していることがあります。
・リードタイムを計算しなければならない。
つまり、生産形態によらず、工程毎の標準時間は必要です。
・リードタイム=標準時間×数量
工程管理はこの式で始まり、この式で終わります。
そして、その後はスケジューラーであろうが、エクセルの表であろうが、手書きの表であろうが、プログラムや電卓でこの式を計算して、ガントチャートや流動数曲線に当てはめるリードタイムを計算しているだけです。これは生産形態に関わらず、共通した要点です。
右腕役はリードタイムを把握していますか?これを把握できていない右腕役に工場を任せることは二の足を踏むはずです。
リードタイムの計算抜きに工程管理はできません。
しばしば、支援先の経営者から「ベテランが勘、経験、度胸(いわゆるKKD)で日程計画を立てている」との説明を受けることがあります。ただ、結局、やっていることは同じです。
ベテランは、標準時間のマスターデータ表の代わりに、頭の中にある、「ふわっとした」数値の集まりから該当するもの引っ張り出して計算をしています。
したがって、ベテランのKKDによるリードタイムは次のようなものになりがちです。
・安全率の高すぎるリードタイム
・工程毎の内訳が不明のリードタイム
ベテランが恐れるのは約束した納期を守られないことです。したがって、KKDによるリードタイムは下駄を履かせた数値になります。安全率が高くなるのです。
「ウチの工場ではもっと生産数量を増やせるはずなのだが・・・」
経営者がしばしば感じる原因のひとつがここにあります。
また、KKDでは、ベテランはマクロ視点で評価しています。内訳までは分かりません。
ベテランからでてくる数とは、製造ロットの製造着手から製造完了までのおおよそのリードタイムです。出荷までに、ざっくりどれくらいかかるか?納期にのみ焦点が当たっています。
工程毎の内訳が不明です。これでは、前から順に追いかける進捗管理はできません。
経営者は右腕役に標準時間のマスターデータを整備する重要性を指導する必要があります。工程管理を属人的な業務にしない要点でもあるからです。
進捗管理を納期から追いかけるやり方をしている限り、現場は楽になりません。
もし、現場が、納期にだけ注視した進捗の確認をやっていたら、やり方を変えるよう指示する必要があります。このやり方のままでは、リードタイム短縮を考える機会がないまま時間が過ぎるのです。
前から追いかけるやり方変えます。標準時間のマスターデータ整備です。ここに我が社の知恵やノウハウが記述されることになります。
仕事のやり方をモグラ叩き式から蓄積式に変えられるのです。標準時間のマスターデータは貴社の工程管理を蓄積式にしてくれます。進捗管理は前からやるものです。
先の現場は、「前から追いかける」やり方に慣れていません。標準時間のマスターデータもつくったことはありません。ただ、やらなければならないのです。
だから、職制のリーダーシップ、4階層指示導線によるトップダウンが欠かせません。先の現場ではここからの改革です。PCのOSを更新するように、右腕役の思考回路を更新してもらう必要があります。
先の経営者は、内部の人間だけでは、改革はできないと判断しました。
そこで、プロジェクトを始めたのです。
まずは前から追いかけるやり方に変えます。お客様の納期をリズムよく遵守したいのです。そして、それができたら、いよいよ人時生産性向上に移ります。
お客様の納期ではなく、我が社が儲かる納期で製造する体制づくりです。ここに関して、先の現場はうれしい状況にあります。
場内に有休のスペースがたくさんあるからです。付加価値額をドンドン積み上げるのに役立つ「計画的な仕掛品」および「計画的な完成品」を処理できます。
「ムダなスペースと考えていましたが、将来活かせそうです。」とは経営者の言葉です。
経営者の視点はいつも将来に向いています。
次は貴社の番です!
成長する現場は、進捗管理を前からやるのでリズムよく遅れを挽回でき、蓄積式になる
衰退する現場は、進捗管理を後ろからやるので挽回の負荷が大きく、モグラ叩き式になる