「生産性ロードマップ戦略」—儲かる工場経営を目指して—第445話 原価管理の使い方を間違えていないか?
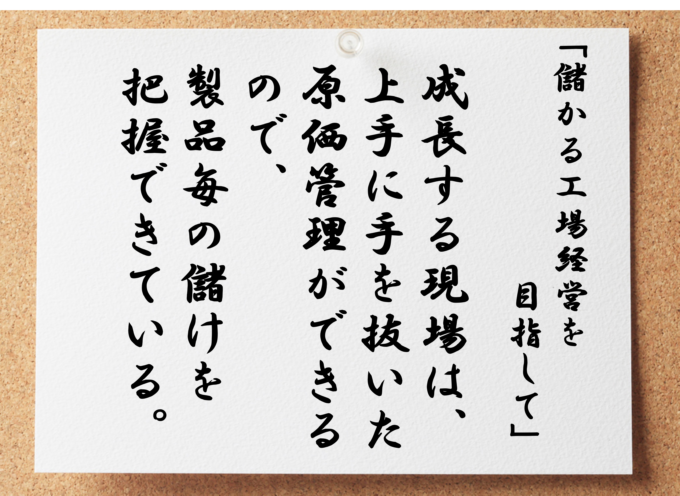
先日、金属製品メーカーの経営者からこんな相談をいただきました。
「原材料や運賃が高騰し、収益が厳しい状況です。これまで経験や売上規模を頼りに利益を判断してきましたが、それではもう対応できません。原価管理が必要だと感じています。」
この経営者は、収益が圧迫される中で、従来のやり方が限界にきていることを痛感していました。経営者の口から原価管理の必要性が語られました。
そこで、「原価管理をやって何を知りたいですか?」と尋ねました。
返ってきたのが、「製品1個1個が、儲かっているのかどうかを知りたい」でした。
「製品1個1個が本当に儲かっているのか?」という問いは、実は多くの中小製造業経営者が直面する共通の課題です。
特に、多品種少量生産やカスタマイズ対応が必要な企業では、どの製品が利益を生んでいるのかを把握するにはやり方があります。
こうした状況では、単に全体の売上や利益を見るだけでは不十分です。製品単位での分析が求められます。
原価管理は、収益性の可視化と改善に直結する強力なツールです。
しかし、複雑な使い方をすると、現場に定着しません。中小製造業には、現場に馴染むシンプルで効果的な方法が必要です。
中小製造業の収益構造を踏まえた、現場に定着する正しい使い方をします。
●経営者の勘や経験も大きな役割を果たす
中小製造業では、経営者の勘や経験に基づく判断がしばしば大きな成果をもたらします。特に、人時生産性を高める大きな施策や、製品・技術開発の決断は、過去の経験が重要な指針となることが多いです。
例えば、新しい技術に投資するタイミングや製品ラインナップの拡充について、数値データだけでは測れない「直感」が必要になる場面があります。経験豊富な経営者は、市場の動きや顧客の反応を敏感に察知し、的確な判断を下すことができます。
ただし、将来を見据えた判断が必要な場合、現在の延長線上だけで物事を考えるのは危険です。市場が成熟し競争が激化する中、事業モデルを構築する際には、ミクロ的な視点も欠かせません。
特に、外部環境が急激に変化する場合、経験だけに頼らない数値的な裏付けが重要になります。経営者の勘や経験を補完する数値に基づいたミクロ的な判断基準が必要です。
●収益を獲りに行くときはミクロの視点が大事
市場が右肩上がりで成長している時代であれば、「とにかく製造し、販売する」ことで利益を確保できます。収益は結果として把握できていれば十分です。黙っていても会社に電話が掛かってきます。
しかし、経営環境が厳しくなると、収益を獲りに行かないとなりません。黙っていても玄和はかかってきません。
収益が出にくい状況では、製品ごとの収益性を詳細に分析する必要があります。製品1個1個が儲けを生み出しているかを把握する必要があるのです。
収益を獲りに行くときは、マクロ的な視点に加えて、ミクロ的な数値判断も重要になります。積み上げるなら、儲かりやすい製品を対象にした方が成果が出やすいです。製品毎の儲けの多寡を知らないと、的確な積み上げができません。
例えば、ある中小製造企業での話です。頻繁に受注がくるので「親孝行製品」と思われていた製品がありました。しかし、調べると、低い儲けしか生み出していなかったのです。
顧客の要求に応じて多くのカスタマイズ対応を行い、その手間暇が、見積もりよりも知らないうちに多くなっていました。
このような場合、製品単位で儲かっているか、儲かっていないかの判断を行わなければ、どの製品が収益確保に貢献しているかの見定めで見誤ってしまいます。
新製品を上市する際、収益が予測通り獲得できるかどうかの確認も重要です。この判断を誤ると、売上が伸びても、付加価値額が想定程積み上がらないことがあります。
●製造業の収益構造を踏まえた原価管理
製品毎の収益性判断では、原価管理の体系を活用します。中小製造業では、「固定費」と「付加価値額」の関係に基づいて考えるのが有効です。
製造業の収益構造 固定費VS付加価値額
儲かっているかどうかは、何かと比べて判断します。「比較対象」が重要です。製造業の収益構造を踏まえると、以下の2点が「比較対象」になります。
・固定費の観点からは、トントンになるための工数
・付加価値額の観点からは、@付加価値額を決定する原単位
この2つが要点です。儲かる見積もりのベースでもあります。
こうした構造になっていることを理解していると、的確な原価管理ができるのです。目標値と実績値を比べます。そして、これらは、人時生産性向上の考え方に繋がるのです。
ご支援先の現場では、人時生産性の考え方を使って、現場のフォローと評価をやっています。改善活動の指標が、製造業の収益構造を踏まえた原価管理からも導かれるのです。
自主性がなければ継続できない改善活動には、明確な数値目標が必要です。経営者の代わりに数値に語ってもらいます。数値はやる気を引き出すのです。
原価管理の考え方を改善活動に活かせます。
●原価管理の使い方を間違えない
原価管理は効果的なツールですが、使い方を間違えないことが重要です。例えば「費用の配賦」は、中小製造業には、必ずしも適していません。
中小製造企業は、少数精鋭の体制で、直接員・間接員が多能工化しています。そのため、費用の配賦計算は煩雑になりがちです。
計算しているうちに何をやっているのか分からなくなります。中小製造現場での原価管理は簡単でなければ活用されないのです。複雑な計算では中小製造現場の実態に合わず、本質から離れてしまうことが多いと感じます。
中小製造業における原価管理は、固定費VS付加価値額の、シンプルな構造を用いた判断基準が適しているのです。儲かっているか、儲かっていないかの判断基準をシンプルに決めてしまいます。
先の経営者も原価管理の使い方で迷っていました。
シンプル イズ ベストです。
製造業の収益構造を踏まえて、原価管理を正しく使うことが肝要です。
●経営者は現場に手を抜くことも教える
原価管理で求められる数値精度は、「儲かっているか、儲かっていないか、判断ができればいい程度」です。
必ずしも詳細な数値精度は求められません。決算書のように公の役所へ届け出る必要もないのです。そうであるなら、少々手を抜いて、計算定義や数値定義を簡単にしても構いません。
それよりも大事なことは、「儲かっているか、儲かっていないか、判断をする原価管理の考え方」を現場に定着させることです。考え方が複雑だと多品種現場は敬遠します。
精度を見極めたうえで、手を抜くことを右腕役や現場キーパーソンに指導することも大事です。経営者は、「絶対に手を抜いたらダメなこと」と「手を抜いてもイイこと」、メリハリをつけて教える必要があります。
少数精鋭の現場では、従業員1人当たりの業務負荷が高いです。全て手を抜かずにやれ!では従業員が疲弊します。マスタファイル作成のための標準時間計測なども手を抜く対象です。
人時生産性向上では分子の積み上げが要点となります。
そうであるなら限られた工数を、効果的に現場へ投入しなければなりません。儲けを積み上げる業務に時間を割きたいのです。経営者に代わって現場を導く右腕役には、手を抜く要点も知ってもらいます。
「手を抜いてもイイと言う考え方は現場に伝わりそうです。」
原価管理の使い方を理解した先の経営者は、製品1個1個が儲かっているかどうかを知る判断基準のイメージが湧いてきたようです。原価管理に対するイメージも変えてもらいます。
次は貴社が挑戦する番です!
成長する現場は、上手に手を抜いた原価管理ができるので製品毎の儲けを把握できている
衰退する現場は、数値精度のこだわった原価管理をやろうとして疲弊し長続きしない