「生産性ロードマップ戦略」—儲かる工場経営を目指して—第457話 リードタイムを自動計算しているか?
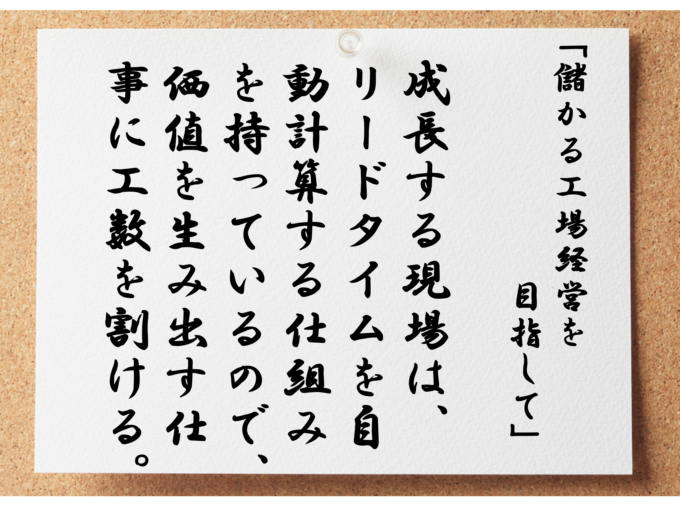
「営業に入力をやってもらっています。」
先日のプロジェクト会議で製造担当役員から上記の報告がありました。一見何気ない言葉ですが、この一言に革命的な変化が隠されています。
この企業では、わずか数ヶ月前まで工場長が孤軍奮闘する典型的な「属人化工場」でした。営業から届いた受注票に基づいて工場長が一人で日程計画を立て、全てを采配していたのです。その判断基準は「KKD」勘、経験、度胸。
これらが悪いわけではありません。それで儲かるなら問題ないのです。しかし、儲からならなくなったら話は変わります。売上が横ばいで伸び悩んでいた経営者はこう決断しました。
「このままでは会社の未来はない。改革が必要だ」と。
挑戦する経営者は行動が早いです。プロジェクトチームは新たな日程計画の仕組みを構築し、試行錯誤を経て、今や実践段階に至りました。
冒頭の製造担当役員の言葉に、その成果が表れています。単なる業務分担の変更ではなく、会社全体の構造改革の証なのです。どこに、その証が表れているのか?
●儲かる納期にはリードタイムの標準が不可欠
経営者である皆さんへ問いかけます。貴社はどちらの発想で動いていますか?
・「お客様から要望があったので、要望された納期に合わせて造る」
・「我が社の付加価値額を積み上げるために、儲かる納期に合わせて造る」
この違いは大きいです。前者と後者では、経営者の視線、思考回路、そして、実際の言動が全く異なってきます。目の色が変わるのです。
収益構造を真剣に考える経営者は、自然と後者になります。
「付加価値額を一層積み上げるには、毎月●●の受注が必要である、ついては現場も毎月●●だけ製造する能力を持つ必要がある」という逆算の思考からスタートするのです。
そして、現場では継続的な生産性向上が求められます。「詰めて、空けて、取り込む」という現場のブラッシュアップです。
そして、「詰める」には、まず、今のリードタイムを明確に把握する必要があります。今のリードタイムが分からなければ、何をどこまで詰めればいいのか、曖昧なままです。
「標準」抜きのカイゼンは存在しません。
多くの改善活動が失敗する理由は、この「標準」を明確にせずに始めるからです。儲かる納期で製造するためには、リードタイムの標準が絶対に不可欠なのです。
●工場長のKKDから脱却するには
リードタイムの標準は、日程計画で最大限に活かされます。これにより、工程管理の属人化から脱却できるのです。
工程管理の核心は「遅れを認識したら挽回する」ことにあります。遅れを認識する—この一点が極めて重要です。しかも、誰もが、この認識をできなければなりません。
仕組み化とは、誰でもできる仕事の手順を確立することです。リードタイムの標準があれば、製品リードタイムと工程リードタイムが客観的に計算できます。受注品の納期を即答でき、手順に従って日程計画を立てられるようになります。
先に紹介した企業の課題は、まさにここにありました。工場長のKKDに依存し過ぎていたのです。リードタイムの標準や計算方法を持っていなかったため、客観的な日程計画を立てられませんでした。
プロジェクトメンバーは、客観的な日程計画を立てる手順を構築し、受注品ごとのリードタイムデータを収集する流れを確立しました。これにより、日程計画から属人性を排除することに成功したのです。
経営者や製造担当役員、さらには工場長が不在でも工場が回る—この状態が、貴社にとっての理想形ではないでしょうか?
●リードタイム計算を自動計算できなければ儲からない
受注品のリードタイムデータを手にするための課題は2つあります。
・リードタイムの根拠となる工程フローと標準時間の体系を整備すること
・リードタイム計算の手段をもつこと
貴社が、やらなければならないことは、右腕役や現場キーパーソンに、この2つを明確に指示することです。そして、「手抜き」の重要性も教えなければなりません。
ある支援先での話です。数年前、別のコンサルタントの指導を受けていました。ストップウォッチで作業分析を行い、改善点を探す取り組みでした。しかし、細部の精度向上に時間を割きすぎた結果、プロジェクト全体が息切れして頓挫してしまったのです。
リードタイムの根拠となる工程フローと標準時間の体系を整備することは極めて重要です。これ抜きに工程管理は語れません。ただし、闇雲に工数をかけて整備すればいいというのではありません。
要点は全体像や体系を明らかにすることにあります。詳細はご支援の際に解説していますが、要するに、「不完全でもいいから、一本一本の木を植えて、まずは森をつくる」ということです。森を明らかにしてから、一本一本の木に手を入れます。
・ひとつひとつの精度は二の次、それよりも全体の準備を急ぎたい!
大手のように自動化、無人化、設備化、機械化で儲けるなら精度が命です。ただ、私たちは、そこで儲けるわけではありません。柔軟性、機動性、小回り性。私たちはここで戦うのです。実務で必要な日程計画の精度を思い浮かべてください。
・ひとつひとつの精度は二の次、それよりも全体の準備を急ぎたい!
これが少数精鋭の仕事の進め方です。成果を出している経営者はこのことを理解しています。儲かるタイムマネジメントはスピードが命です。
後者の「リードタイム計算の手段をもつこと」も、スピードが命を意味します。リードタイムデータは計算によって得られますが、その具体手段は3つです。
①KKD : 工場長の頭の中で計算される
②手計算 : 電卓やエクセルコピペで計算される
③自動計算 : 各種アプリケーション、マクロ機能やプログラムで計算される
弊社は③が必要であるとお伝えしています。なぜなら、計算それ自体に価値はないからですしたがって、この企業の工場長にも、計算作業に時間を割いてもらいたくないのです。
すでに生産管理システムや外販グループウェアを活用している現場なら、それへ反映させます。ただ、この企業では、そうした類のツールをまだ導入していません。
そこで、弊社より簡便ツールを提供し、自動計算をしてもらっています。
工程管理の仕組みづくりでじっくりやりたいのは、リードタイムデータを手にするところではなく、それ以降のところにあるのです。価値の少ない業務に時間を割きたくありません。
そこはスピードを上げて終わらせます。本質ではないところに時間を割いているようでは儲かりません。
●仕組みをつくる本質とは?
日程計画の仕組みが出来上がったら、次はその運用です。ここからは製販一体、全社一丸の取り組みになります。
日程計画運用の最初のステップは、受注品のリードタイム計算に必要なデータを揃えることです。受注票から品番を特定し、工番(製番)を設定し、対応する工程フローとリードタイム標準を選択します。
これは、難易度の高い作業に思えます。営業と工場の両方を理解している必要があるからです。しかし、先の企業はこの作業を営業担当者だけでできるレベルにまで標準化しました
「自動計算のツールがあるお陰でここまでできました」と製造担当役員は語っています。
計算作業自体や標準データを揃える作業それ自体に価値はありません。本当に重要なのは、その先にあるのです。
だからこそ、これらの作業は誰でもできるようにすべきです。型を作り、その通りに実行してもらう。仕組み化の本質は「誰でもできるようにすること」にあるのです。
中小製造企業は大手と同じ土俵では戦いません。大手が避ける領域、小回りを活かせる分野で付加価値を生み出します。
その中で、本当に価値を生む業務とそうでない業務を見極め、前者に人的リソースを集中させることが成功の鍵です。
一方で、価値を生み出していない業務の役割も忘れてはなりません。
つまり、価値を生み出す中核業務それだけでは、仕組みを回せないと言うことです。中核業務を支える様々な業務が必要です。先に挙げた計算作業や標準データ収集がその例です。
これらは直接的な価値は低くても、支援業務として役割を果たしています。
そこで、直接的な価値は低くても、支援の役割を果たしている業務を中心に仕組み化し、型どおりに、誰でもできるようにする——これが仕組み化の目的です。
仕組みそれ自体で儲けるのではなく、価値の低い業務の時間を最小化し、価値の高い業務に工数を集中させます。だからこそ、「リードタイム計算を自動計算できなければ儲からない」という結論に至るのです。
この支援先では、新たな日程計画の仕組みを構築し、試行錯誤を経て実践段階に入りました。「営業に入力をやってもらっています」という言葉が、その支援先企業での仕組み化レベルを物語っています。
営業担当者が工場関係者の助けなしに工程フローとリードタイム標準を選択できるまでになったのです。
「誰でもできる」——これが仕組み化の理想形です。
そして、この過程で製販一体のコミュニケーションが生まれ、チームの凝集性も高まりました。共通の目標に向かって協力することで、組織は強くなるのです。この支援先は構造改革水準の成果を手にしました。
プロジェクトを通じた人材育成の狙いがここにあります。
貴社では、リードタイムの自動計算ができていますか?
次は貴社が挑戦する番です!
成長する現場は、リードタイムを自動計算して、価値を生み出す仕事に工数を割いている
衰退する現場は、工場著のKKDでリードタイムを計算するので日々の業務で手一杯である