「生産性ロードマップ戦略」—儲かる工場経営を目指して—第40話 IOTでモノづくり連鎖の全体最適を図る
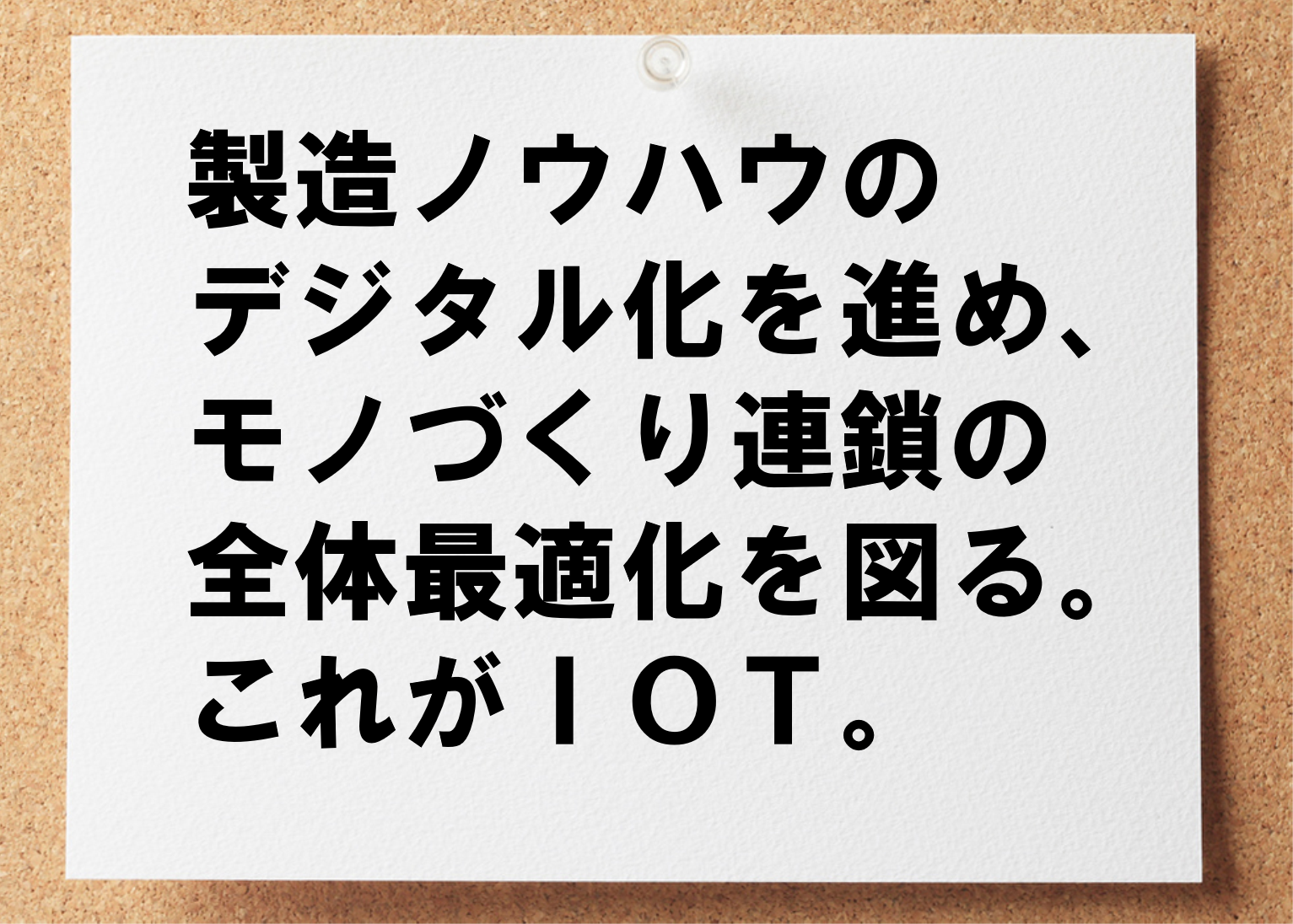
工学的な因果関係を明確して、製造ノウハウのデジタル化を進め、モノづくり連鎖の全体最適を図る、という話です。
新たな価値を生み出すために、製造活動のデジタルデータをどのように生かしますか?
生産性の向上、付加価値の創出。
モノづくりを事業とする企業の永遠の課題です。
これらの課題に対応するために、現場のモノづくり連鎖全体を最適化する必要があります。
個別工程内の最適化に留まる従来型の改善活動では、成果も限定的です。
ここで必要なのは、全体最適を実現させる工場。
未来の現場の姿です。
昨今、工場のスマート化が提唱されています。
デジタル化とも言い換えられます。
製造活動のデジタル化を生産性の向上や付加価値の創出へどうつなげるか?
この問いにクリアに答えられる現場とそうでない現場の格差は広がります。
コンセプトが明確な現場はガンガン行動し、どんどんデジタル化を進めます。
情報通信技術が現場へ導入され、スマート化が進むのです。
中小製造企業もしっかりとこの課題に向き合います。
中小製造企業こそ、こうした技術動向を機会ととらえるべきです。
そもそも、中小製造企業の経営資源は大手と比べて制約があることが多い・・・・。
だからこそ、デジタル化を活用して、効率的に経営資源を使うのです。
こうした考え方が経営者に求められます。
勘と経験に優れたベテラン従業員が減ります。
さらに、少子化で若手人財の確保も難しくなるのです。
仕事の進め方、そのものを見直す必要があります。
その答えのひとつがデジタル化なのです。
モノづくり連鎖全体を眺めたとき、気が付くことがあります。
モノづくり連鎖全体で、デジタル化自体は、特別なことではないということです。
逆に言うと、連鎖を構成している他の活動と比べて、製造活動のデジタル化は遅れているとも言えます。
モノづくり連鎖の上流に位置する設計、開発ではPDM(Product Data Management)やPLM(Product Life cycle Management)の考え方があります。
短くなりつつある製品のライフサイクルでできるだけ多くの利益を獲得すること、一方で製品開発のコストはできるだけ下げることが狙いです。
CADデータ管理、図面管理、ドキュメント管理、部品表管理、設計変更管理、開発推進管理、等々、設計、開発に関連した情報を共有します。
また、資材購入ではMRP(Material Requirements Planning )や、それを発展させたERP(Enterprise Resources Planning )の考え方があります。
生産計画を起点として、生産に必要な材料の品種、所要量、所要時点を割り出し、生産や資材発注の指示を的確に出すことが狙いです。
少量多量生産から多品種少量生産、変種変量生産へ移行すると生産管理が煩雑になります。勘や経験では太刀打ちできなくなるほどに生産計画が細分化されるからです。
さらに、販売の現場においても、勘や経験から脱却し、デジタル化が進んでいます。
特に消費財の販売現場では顕著です。
顧客との関係性を強化するマーケティングでは、顧客に関する多様なデータが活用されています。
CRM(Customer Relationship Management)です。
顧客満足度と顧客ロイヤルティの向上のために顧客のデータベースを構築し情報の共有化を図ります。
モノづくり連鎖において、製造以外の活動ではデジタル化が進んでいるのです。
いよいよ、モノづくり連鎖の本命、製造活動でのデジタル化が、今後、進みます。
センシング技術をはじめとして、情報通信技術やその周辺技術が進化したおかげです。
ベテラン従業員の勘と経験に代わって、デジタルデータを活用します。
デジタルデータを活用して、工場のモノづくり連鎖全体を最適化するのです。
では、デジタルデータをどのように生かすのか・・・・・。
多くの現場では、ここで行き詰まっています。
モノづくりの現場で、価値の生み出し方の分析が進んでいないからです。
設計、開発や資材購入、販売の各活動と異なって、製造活動はキモの部分をデジタル化するのが難しい。
ベテランの勘と経験に依存したモノづくりをしているとそうなります。
また、工学的な因果関係が明確になっていない場合もそうです。
相変態を伴うモノづくりでは、現象自体がブラックボックスになっていることもあります。
溶融、凝固、気化、凝結、昇華・・・こうした現象を工学的にコントロールするには地道な分析が欠かせません。
ですから、製造現場のデジタル化を進めるときに考えるべきは、工学的な因果関係の明確化です。
製造現場で起きていることを全て把握します。
これを抜きにIOT(もののインターネット)は導入できません。
現場のスマート化、IOT(もののインターネット)の一歩目は現象を計測することだからです。
製造活動を通じて生み出される価値を裏付ける現象を計測します。
センシング技術は進化しています。
ですから、従来まで計測ができなかった項目も計測可能になっていることが多いです。
これまで知りたかったけれども、知り得なかったデータを手にすることも可能になりました。
しかし、工学的な因果関係が把握できていないと、計測すべき項目ははっきりしません。
そもそも、工学的な因果関係を知りたい!という思いがないとそうした発想に至りません。
したがって、現場のスマート化、IOT(もののインターネット)の一歩目は現象を計測することであることを踏まえ、製造現場で起きていることを全て把握するのです。
工学的因果関係を徹底的に洗い出します。
そうすることで、何を計測するべきかが見えてきます。
製造活動はモノづくり連鎖のキモです。
多くの価値はここで生み出されます。
モノづくり連鎖の他の活動と違って、製造のデジタル化が遅れているのは、製造活動が暗黙知のノウハウで構成されているからです。
ですから、暗黙知のデジタル化に挑むのことになります。
そこで工学的な因果関係を明確にします。
モノづくりを極めるということです。
そうしてモノづくり連鎖の全体最適を図ります。
製造活動の工学的因果関係を明確にする仕組みづくりをしませんか?
まとめ:工学的な因果関係を明確して、製造ノウハウのデジタル化を進め、モノづくり連鎖の全体最適を図る。