「生産性ロードマップ戦略」—儲かる工場経営を目指して—第42話 イノベーションで全体最適を目指す
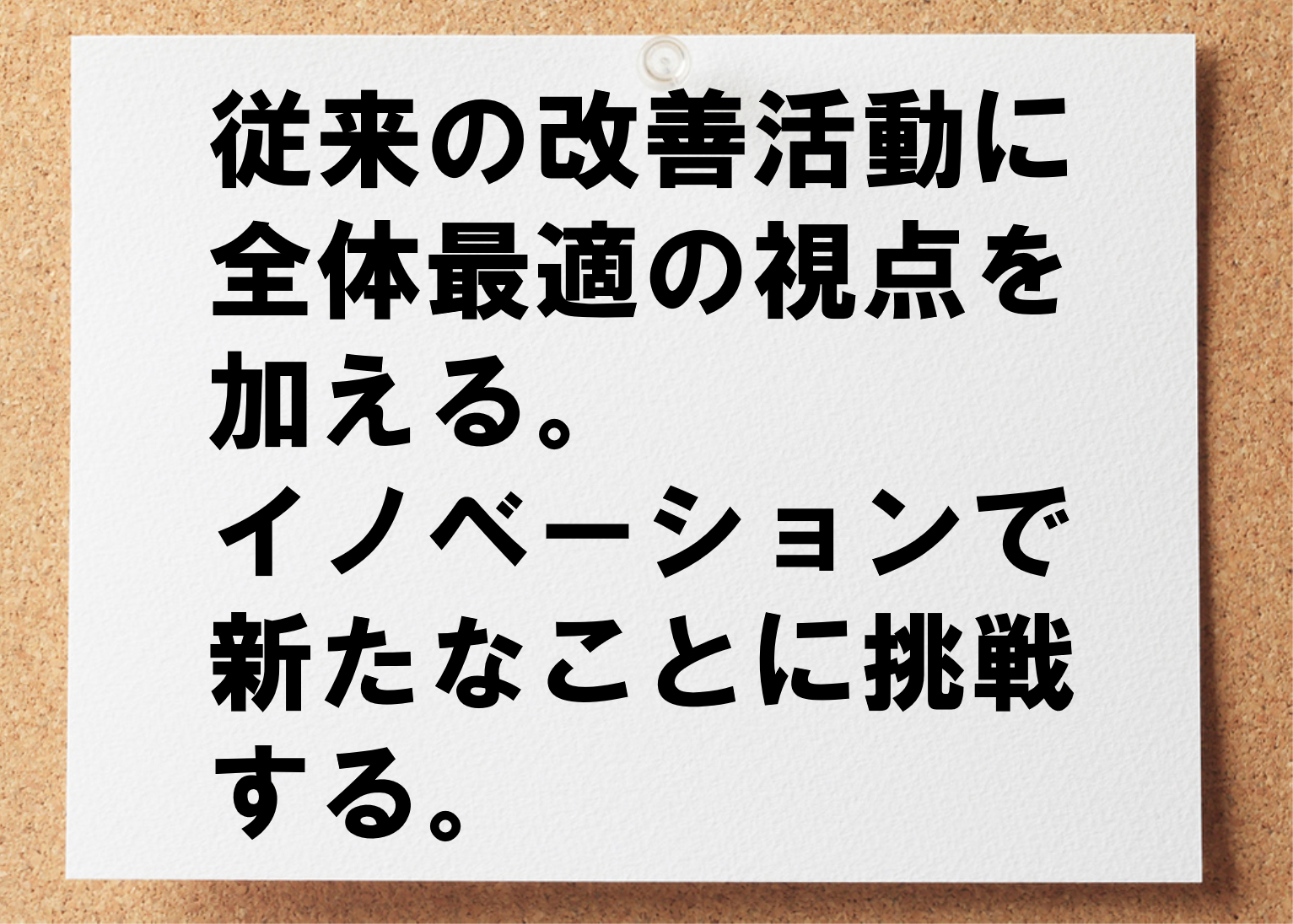
従来の改善活動を継続するだけでは何かが足りない。
このように感じる経営者の方も多いのではないでしょうか?
それは、改善活動の成果が部分最適化にとどまっているからです。
造れば売れる時代が過去のものとなりました。したがって、今、私たちは、顧客に「選ばれる」製品を「最小コスト」で造ることが求められています。
貴社の製品は、競合製品と比較されることなく真っ先に選ばれていますか?貴社の製品は、削減の余地がないと言い切れるほどの最小コストで生産されていますか?
工場全体を俯瞰して、上記の2つの問い答える必要があります。モノづくり連鎖の最適化、全体最適の視点が欠かせません。
3つの流れに着目してモノづくり連鎖の全体最適を図ります。
物、お金、情報です。滞りのない流れを入口から出口まで一気通貫につくるのです。
「選ばれる」製品を「最小コスト」で造らねばなりません。各工程の部分最適を擦り合わせれが、モノづくり連鎖の全体最適に至るほど、昨今の製造業は単純ではありません。
3つの流れの部分最適化と全体最適化を並行して行う必要があるのです。従来よりも広い視野、高い視点が求められます。
したがって、すでに行っていることをさらに上手に行うだけではだめです。新たなことに挑戦する必要があります。これからは、現場でもイノベーションの観点が必要なのです。
高度化複雑化している製造業おいて、従来の延長線上に3つの流れの全体最適化の答えはありません。新たな視点や発想が必要です。現状を創造的に破壊するところから始めます。
そこで、カイゼンとイノベーションを連携させた仕組みで全体最適を目指すのです。ただし、イノベーションだからと言って、難しく考える必要はありません。発明発見、特に工学上の新しい知識だけがイノベーションの機会ではないのです。
全体最適化を目指すとき、2段階で取り組みを設計します。
1)まずは、貴社全体最適の状態を設定します。
2)そして、貴社の持つコア技術(固有技術と管理技術)の目指すべき状態を設定します。
これが貴社のイノベーションです。
従来の貴社にはなかった「新たな」貴社の姿があるからです。従来の延長線上にはない新たなことに挑戦するのがイノベーションです。
ドラッカーは新しいことを生み出す機会は「変化」にあると言っています。イノベーションとは意識的かつ組織的に変化を探すことでもあります。
今、貴社は、顧客に「選ばれる」製品を「最小コスト」で造ろうとしているのです。これは従来の延長線上にはない新たなことです。貴社は明らかに変化しようとしているのです。
科学技術的には何ら特筆すべきことがないイノベーションでも、高収益事業に発展した事例があるのをドラッカーは指摘しています。貴社も従来の改善活動にイノベーションの視点を加え、高収益のモノづくり連鎖を目指すのです。
中小の現場で生産性を1.5倍に高めたことがあります。
売上規模が1~2億円規模で毎月数十万個の自動車部品を生産する生産ラインです。その生産ラインは3台の加工設備が設置されていました。
品種は4つです。昼夜勤務体制で生産していました。
あるとき、顧客から納入ロットを小さくしたい旨の相談がありました。
品種の切り替え頻度が多くなります。品種数は変わりませんが、切り替え頻度が多くなれば、生産数量が減ります。多品種少量化による生産性の低下です。
すでに昼夜体制でもあったので、残業時間を増やすのにも限界がありました。そこで、多品種少量生産への挑戦が始まりました。
その現場は10名以下の小さな職場です。それまで、改善活動のような現場活動を展開していませんでした。
段取り作業の短縮を柱とした現場活動に挑戦したのです。現場にとっては従来の延長線上にはない新たな挑戦です。3台の加工設備のうち、1台の加工設備を対象にしました。
まず、顧客要望を満たすために必要なことを洗い出しました。現場リーダーを中心に現場で複数回、集まって、ワイガヤをやったのです。
すると意外にも、他の設備での作業へ、少量多品種化の影響が及ぶことがわかりました。それは、作業改善で克服しました。
柱となる段取り短縮は、新たな設備を導入して技術的に対応しました。
現場リーダーが中心になって、現場の意見を集約し、自職場に最適な仕様を検討したのです。自家設計の設備です。
こうした取り組みの結果、生産性を従来対比で1.5倍にできました。
科学技術的には何ら特筆すべきことはありません。しかし、現場リーダーと現場メンバーにとって、この取り組みはイノベーションです。従来の延長線上で考えませんでした。
新しいことに挑戦したのです。
小規模ながらも全体最適の視点で考えたので、やるべきことを事前に全て洗い出すことができました。こうした経験を経て、その現場では、改善活動を継続するようになったのです。
従来の改善活動に全体最適の視点を加えます。新たなことに挑戦するイノベーションの姿勢で臨めば、従来の延長線上にはない成果を獲得できるのです。
私たち中小製造業は、今、顧客に「選ばれる」製品を「最小コスト」で造ることが求められています。そして、高度化・複雑化している製造業おいて、従来の延長線上に3つの流れの全体最適化の答えはありません。
そこで、カイゼンとイノベーションを連携させて、モノづくり連鎖の全体最適化を図り、儲ける力をアップさせます。
そして、イノベーションを日常化する強力な仕組みをつくります。
それが儲かる工場経営です。
カイゼンとイノベーションを連携させて儲ける力をアップする仕組みをつくりませんか?