「生産性ロードマップ戦略」—儲かる工場経営を目指して—第11話 中小製造業現場、機能別レイアウトを大いに生かす
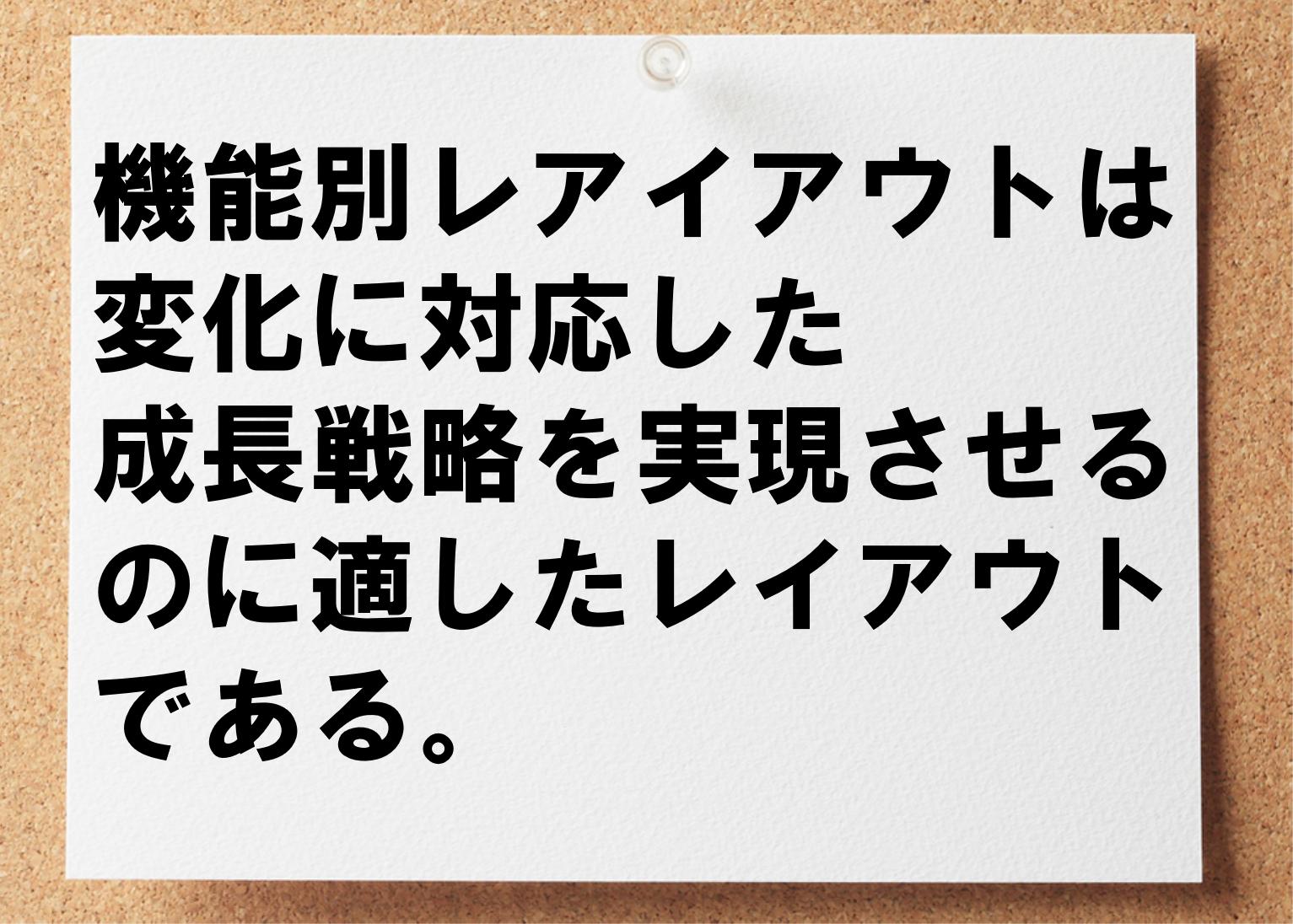
中小モノづくり現場の機能別レアイアウトは、レイアウト上の制約条件が少ない分だけ、製品仕様の幅を広げられ、変化に対応した成長戦略を実現させるのに適したレイアウトである、という話です。
自社工場のレイアウトの特徴、特色を把握していますか?
将来的な成長戦略を描く時、工場レイアウトで目指すべき状態を設定していますか?
インダストリー4.0という言葉を新聞や雑誌、インターネットの各種サイトで頻繁に目にするようになりました。そして、その主役はIOT(もののインターネット)です。
製造業で何か大きな変化が起き始め、新たな流れができる予感に満ち溢れている昨今、自社工場を長期的な視野でどう成長させ、発展させるか、将来に向けての戦略立案に腐心している経営者の方々も多いと思います。
今後、5年、10年で製造現場が大きく変化することは間違いないです。なぜなら、外部環境が大きく変化しているからです。
少子化は今後の採用活動に影響します。国内の人口減少は、将来、市場自体が大きく成長する見込みが無いことを示唆しています。さらに、国内市場の成熟化は単品の大量生産で収益を拡大させ続けることは困難であることを警告しています。
市場と直接に向き合った事業形態のモノづくり企業も、下請け型のモノづくり企業も、事業形態のいかんを問わず、変化に対応するための新たな戦略が、今、求められています。
そこで、「ウチの工場ではIOTを導入したら、どのような効果があるのだろうか?」という疑問を持っている方も多いかもしれません。
ただ、ここで忘れてならないのは・・・・・、IOTは”道具”に過ぎないということ。自社工場を成長・発展させる将来構想をIOTで加速させる、というのが正しい認識です。IOTを導入することで、魔法のように現場が変わるわけではないことに留意します。
あくまでモノづくりの本質に立脚した戦略に従って、目指すべき状態を設定する”構想力”が自社の継続的な成長のカギです。
IOTを考える前にやるべきことがあり、将来を見据えた構想力で豊かな成長を実現させる戦略を描くことが最優先事項です。
さて、中小製造業では価格競争回避の戦略によって持続的な競争優位を確立させます。成長戦略を描くときに、先々、価格競争に陥らない目途はつけておきたいです。
ですから戦略立案に当たっては、まず、高付加価値化をどのような方針をもって実現させるのかはっきりさせる。
そして、ここでのキーワードはマスカスタマイゼーションと超短納期の2つであると考えています。
マスカスタマイゼーションは次のように説明されています。
・大量生産に近い生産性を保ちつつ、個々の顧客のニーズに合う商品やサービスを生み出すこと。
・企業と顧客の何らかのやり取りから、製造または組み立て工程でカスタマイズされた製品を大量生産品と同程度のコストと価格で製造し、価値を生み出す戦略。
(出典:ウィキペディア)
「モノ」のみではなく「コト」まで対象範囲を広げ、モノづくり+サービスもマスカスタマイゼーションの対象と考えます。
顧客の顕在的、潜在的なニーズへ”ピンポイント”へ対応させる多品種少量、多品種変量、モノづくり+サービス等、多様なモノづくりの事業形態を大量生産並みの最低コストで実現させる。そして、それを短納期で実現させる。
マスカスタマイゼーションと超短納期の2つキーワードは牛丼の吉野家のキャッチフレーズを連想させます。
「うまい」・・・・顧客の顕在的、潜在的なニーズへ”ピンポイント”へ対応
「はやい」・・・・超短納期
「やすい」・・・・最低コスト
(ちなみに、この吉野家のキャッチフレーズは時代と共にその順番が変化しているそうです。今はこの順番らしいです。モノづくりの成長戦略にも沿っている感じがします。)
吉野家のキャッチフレーズを実現させる現場のイメージをもって、モノづくり戦略の方向性を探るのはいかがでしょうか?
そして、そこでは、モノづくり戦略を実現させる自社工場の設計が課題です。自社工場の現状に合わせて、こうしたコンセプトを実現させる工場を新たに構築していきます。
さて、工場レイアウトには大きく、2つのパターンがあります。製品別レイアウトと機能別レイアウト。中小モノづくり現場では後者である場合が多いのではないでしょうか。
そして、今後、モノづくり戦略のキーワードになると考えられるマスカスタマイゼーションと超短納期に対応しやすい工場レイアウトは後者の機能別レイアウトです。つまり中小モノづくり現場に多く見られるレイアトであり、中小現場の小回り性や機動力を生かす戦略を目指します。
若手エンジニアとして腕を磨いていた自動車部品工場での話です。
毎月の売上高は十数億規模で、国内大手自動車メーカーのOEMを柱とした事業展開をしていました。
標準部品が大部分であり、生産量も多くなると数万個オーダーでした。典型的な大量生産による規模の経済で利益を上げていた製品です。
一方でアフター市場を対象にした部品のOEMも並行していました。こちらは典型的な少量多品種の製品です。
そして工場には、これらに対応した2タイプの生産ラインがありました。一つは国内大手自動車メーカーOEM向けの一貫ライン。そしてもうひとつは少量多品種OEM向けのラインでした。
私が働き始めた1990年代前半、大量生産向けの一貫生産ラインが大いに活躍しました。生産ロットも大きく、1ケ月のうちで数日間、生産ライン全体が特定の製品全てで埋め尽くされるような時もありました。
そうした中でも並行してアフター市場を対象にした部品のOEMも生産していました。こちらの生産ラインは機能別レイアウトです。
それぞれの生産ラインの実地で体感し、勘所を知ることができたのはイイ経験でした。
大量生産向けの一貫生産ラインと少品種向けの機能別ラインの狙いは当然に異なります。
大量生産向け一貫生産ラインで利益を上げる原動力は効率のイイ生産です。受注量は十分にあった時代です。多くの受注量をこなすために止めずに動かし続けることで利益を生み出していました。
生産ラインで求められる機能は生産性であり、可能な限り自動化、無人化を進め、現場でオペレーションしやすく、製品が滞りなく流れるような工夫がなされます。
ただし、そのかわり犠牲にするものがあります。それは、対応できる製品仕様の幅です。マーケティング的な表現で言うならば「商品の深さ」です。
生産ラインに流動させる製品の大きさや長さ、形や色に制限を設けることで生産活動の”標準化”を図り、自動化を適用しやすくし、現場でのオペレーションもやり易くする。
製品の複雑性を排除することで効率を高めるのが一貫生産ラインです。
ですから、一貫生産ラインの現場には多くの”新人”が配属されていました。現場の作業者はベテランが構築した標準にしたがって作業をすればイイからです。
一方、少品種向けの機能別ラインで求められるのは、製品仕様の幅の広さ、多様性です。
アフター市場向け製品は、大きさや長さ、形や色が多様です。その上、数も少ない。中には数個という製品もありました。大量生産向け一貫生産ラインでは1製品当たりで数万個の生産
をしている一方、機能別ラインでは数個~数十個です。製品の異品混入を防ぎつつ、正常に流動させるには、属人的な配慮も欠かせません。さらに、設備の汎用性も問われます。
仕様の幅が広いだけに、それを1つの設備でまともに対応していたら、規模も”巨大”になり、費用も”巨額”になる。ですから、汎用性を持った設備の組み合わせを考え、必要に応じて機能を加えておく。
製品の複雑性に対応するのが機能別ラインです。
ですから、こうしたラインではベテランの持つノウハウが頼りとなります。実際、当時、そのラインでは前工程から後工程まで3名程度のベテランが実務を切り盛りしていました。
特に切削加工工程のベテラン作業者は、生産ロット毎に知恵と工夫を発揮していました。このベテランの方には加工工程上のノウハウをいろいろと教えてもらったことを思い出します。
現場には必ず、こうした自発的に自らの能力を発揮して、現場に貢献しようと自律的に頑張るベテランがいるものです。(余談ですが、その後も、複数の現場でそうしたベテラン作業者に出会いました。)
中小モノづくり現場では、後者の機能別レイアウトが多いと推測されます。この機能別レイアウトをベースに現場の機能を高めればイイわけです。
カイゼン事例として、機能別レイアウト→製品別レイアウトあるいは一人生産ライン、U字ラインへの変更によって生産性を向上させた実績を多数目にします。
数kmに相当するコンベアーを撤去し工程と工程の間を詰め、多能工化を図ってU字ラインで効率を上げたというような事例です。
こうした考え方は今でも通用しますし、該当する現場では挑戦する価値は大いにあります。
ただし、こうした事例で実績を上げるには前提条件があります。それは、製品の仕様の幅に制約があって、ある程度の生産量が確保されていること。
ですから、受注量が増えない問題に直面している現場では、もう少し違った見方をする必要があります。
少ない量で負付加価値を高めるには?
少ない量でも「うまい」「はやい」「やすい」の吉野家キャッチフレーズを実現して収益を確保するには?
顧客の顕在的、潜在的なニーズへ”ピンポイント”へ対応させることを目指しても、そもそも、最初から製品の仕様を絞り込んで設定することは困難です。生産量にしても、顧客のニーズにしても、予測することはまず不可能だからです。
どのようなサービスが”ストライク”になるかは、やってみないとわからない、トライアンドエラーの要因が多分にあります。
ですから、こうした将来的な不確実性に対応するなら、機能別からスタートするのが都合がイイです。
自社工場の現場をじっくり見渡します。
そして、考えるべきことは、各工程が持つ機能をどこまで高められるかです。
機能別ラインの各工程で高めるべき付加価値の内容と水準を検討します。これは対応できる製品仕様の幅に直結します。
さらに、機能別レイアウト上での流れを考えます。モノづくりのみならず、モノづくり+サービスの事業を展開すると、どのような流れが求められるかです。
機能別レイアウトであるからこそ、設備上の制約条件なく、流れを考えることが可能です。
市場の不確実性が高まり、変化の頻度も幅も大きくなる先々を見据えた時、機能別レイアウトから将来構想を考えるのは好都合です。中小小モノづくりの機動力、柔軟性を生かせます。
先に説明した大手自動車メーカーOEM対応の大量生産向け一貫ラインでは、その後、製品のコモディティー化に直面する事態となりました。2000年台後半からアジア新興国から安価な製品が大量に輸入され始めたからです。
それなら、対応できる製品仕様を変更するように生産ラインを構築し直せばイイわけですが、設備を一気に変更する必要があり、生産ラインの柔軟性の低さが、その後の苦労の種となりました。
さらに、大手ならば潤滑な資金力でこうした状況を新たな設備投資で乗り切ることは可能ですが、中小では簡単なことではありません。
変化に対応するのが企業の仕事の本質です。
自社の持つ機能別ラインの特性を整理して、現状を把握し、
「うまい」・・・・顧客の顕在的、潜在的なニーズへ”ピンポイント”へ対応
「はやい」・・・・超短納期
「やすい」・・・・最低コスト
によって中小製造業ならでは強みを発揮できる事業形態を考えます。
モノづくりのみではなく、モノづくり+サービスもターゲットです。
そして、中小モノづくり現場の機能別レアイアウトは、レイアウト上の制約条件が少ない分だけ、製品仕様の幅を広げられ、変化に対応した成長戦略を実現させるのに適したレイアウトです。
自社工場のレイアウトに基づいて将来の事業形態を考えるのか?あるいは、将来の事業形態に合わせて自社工場レイアウトを構築するのか?
対応は様々ですが、現場のレイアウトは事業形態と密接な関係にあることに留意します。
機能別レイアウトをスタートにして、将来構想を考えてみませんか?
現場からの知恵も引き出しやすいです。
まとめ:中小モノづくり現場の機能別レアイアウトは、レイアウト上の制約条件が少ない分だけ、製品仕様の幅を広げられ、変化に対応した成長戦略を実現させるのに適したレイアウトである。