「生産性ロードマップ戦略」—儲かる工場経営を目指して—第149話 鎧を身に着けた現場
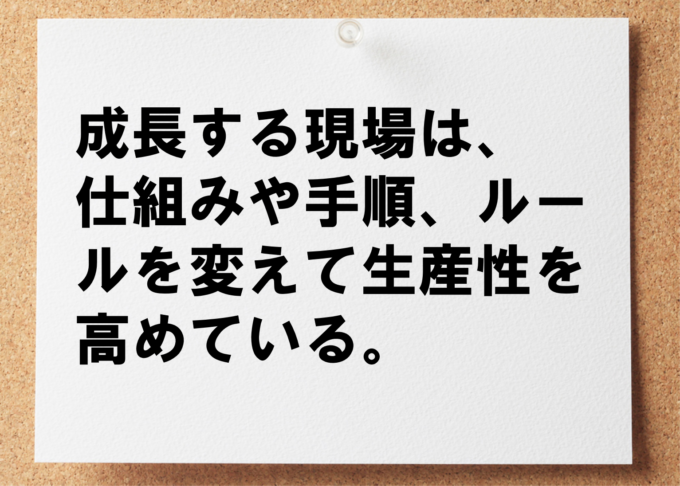
各現場リーダーの役割分担を明らかにしていますか?
「仕事のやり方が人によって違うからではないでしょうか?ルールがないからですね。」
生産性向上活動に着手した現場リーダーの言葉です。その現場リーダーは、経営者の右腕として、現場を引っ張っています。
経営者の意向を踏まえて、新たな現場活動を展開中です。その現場リーダーへ労働生産性を説明したことがあります。大手と中小の格差についてです。
製造業の労働生産性(付加価値額人時生産性)は大企業で6,500円/人時、中小企業で3,600/人時(概数)。中小は大手の55%にとどまっていると説明しました。
そして、「どうして中小は、大手の半分程度の儲けしか稼げないと思いますか?」その現場リーダーへ尋ねたところ・・・。
ちょっとの間、考えた後、冒頭の言葉が返ってきました。
中小の労働生産性が大手と比べて低いのは、そもそも・・・という論点がいくつかあります。まずは、「規模の経済」のメリットを享受しにくいことです。
ある部材を10個購入するのと、10,000個購入するのとでは、当然、後者の方が安価になります。中小には難しいスケールメリットです。
また、中小のほとんどが下請け型のビジネスモデルです。これは儲けにくいことを意味します。中小にとっての価格は大手の原価だからです。
特に競合と比べられる状況下では、価格競争に陥って、付加価値額を確保しにくくなることは多くの経営者が痛感していることでしょう。
そもそも、多くの中小製造企業は、縁の下の力持ちで存在感を示してきました。
こうした状況を考慮すると、収益力で差が出てしまうのはどうしようもないことのように感じます。ただ、こうした現状を認めながらも、中小は大手並みの労働生産性を目指す余地はあると考えたいのです。
現場で共有されている仕事の進め方、手順、ルールの有無が、付加価値額生産性に及ぼす影響は小さくないと考えています。
先の現場リーダーの表現を借りれば、人に依存した仕事のやり方をしていると、ムダが発生するからです。現場のあちらこちらに、澱のようたまっている見えないストレスが、ムダを生みます。
現場の仕事が、手順化、ルール化されていないとどうなるでしょうか?各人の役割が明らかにされません。その結果、判断基準が担当者個人となります。
こうした現場では、往々にしてベテランが幅を利かせることになるのです。経験で全てが語られます。するとどのような思考回路が定着するでしょうか?
「何が正しいか」ではなく、「誰が正しいか」に焦点が当たるのは明らかです。いきおい、ベテランやその職場が長い人材が現場の判断基準となります。(経営者ではなく。)
すると、仕事上のトラブルが起きると仕組みではなく(もともとそうしたものがないので)、人を問題にせざるを得ません。
こうした職場では、間違いをやらかしたら、人はどうふるまうでしょう?対策を講じる代わりに、隠そうとしませんか?大手製造企業で起きた品質不正問題を踏まえれば明らかです。事業活動にとってこれほど大きなムダはありません。
仕事を丸投げされた上に、共有された仕事の手順やルールがなければ、人は自分の身を守ろうとします。
伊藤がかって勤務した中小現場で、次のようなことがありました。
工程管理上の問題を解決しようと、設計担当者へ相談した時のことです。その設計担当者から、下記の言葉が返ってきました。
「私が、そのようなことをしなければならないのでしょうか?」
その言葉を耳にしたとき、一瞬、「?」となったことを、今でも覚えています。その企業の前職時代、とにかく日々、横との連携、縦との連携を図りながら、仕事のやり方を「変える」ことに汗をかいていたからです。
製造業は日進月歩で進化する技術で戦っているわけですから、当然のことでした。
仲間と一緒に、つまり組織的に、付加価値額を積み上げるのが現場での仕事・・・。
学校を卒業し、社会人の生活を始めたその職場で、そうすることが”技術屋”の仕事だと上司や、先輩にたたき込まれていたのので、当たり前であると考えていたのです。
「氏より、育ち」と言えます。環境がそうした思考回路を植え付けてくれていました。
ですから同じように、先の設計担当者と一緒に「変える」ことをやろとしたのですが、異なった反応に戸惑ったわけです。
ただ、今なら理解ができます。その現場には共有された仕事の手順やルールがなかったのです。ですから、積極的に他部門と連携して挑戦するという思考回路を持っていませんでした。
したがって、組織的に仕事を進める感覚が乏しく、問題が起これは、原因究明で個人を問題としていたのです。
付加価値額を積み上げて、固定費を回収するために製販一体となって・・・という共通の目標もありませんでした。保身に走っても、いたしかたのないことです。
そして、保身に走れば、現場にストレスもたまります。ストレスで硬直した現場の生産性が高いわけはありません。
現場へ、目標実現の難易度が高い業務に挑戦してみようと投げかけて下さい。
「やってみましょう。こうすればできます。」
「忙しくてできません。難しくてできません。」
どちらの言葉が現場から返ってきますか?
後者であるなら、手順化、ルール化すべき業務があるかもしれません。仕事が属人的である恐れがあります。
金属製の鎧を身に着けた西洋騎士を思い浮かべてください。金属製の鎧でほぼ全身が覆われており、まさに自身の守りは鉄壁と言って良いでしょう。
その西洋騎士のチームがバスに乗って移動しようとしています(仮の話なので悪しからず)。バスの中は西洋騎士で満員です。
共有された仕事の手順やルールがない中小現場は、金属製の鎧を身に着けた西洋騎士で満員となったバスと同じではないでしょうか?
まず、鎧が邪魔で身動きがとりにくいです。そして、無理に動こうとすると、「ガチャガチャ」隣の鎧にぶつかります。
「動くな。じっとしていろ」と言われることでしょう。従来の仕事を、従来のやり方でし続けるのが無難です。
これでは中小現場の強みであるべき柔軟性、機動性、小回り性が生かされません。それどころか、見えないストレスが澱のように、現場のあちらこちらにたまることになります。
これらが積み重さなって、ムダを生み、ボディーブローのようにジワジワと生産性を貶めるのは火を見るよりも明らか・・・。
ですから金属製の鎧を脱ぎたくなる環境を整備するのです。仕事の進め方、手順、ルールを決めることです。組織的に仕事をする思考回路を共有することです。
中小の労働生産性を向上させる具体策のひとつは「手順化、ルール化」であると考えています。冒頭の現場リーダーはそのことに気づきました。
今、その現場リーダーは「連携」という言葉を現場へ投げかけながら、各種業務の手順を標準化しようとしています。
その結果、従来とは異なった反応も現場に出てきました。
各種業務の手順を明らかにして、各人の役割を決めると、工程間で自主的に相談する姿が見られるようになってきたのです。ストレスから解放されれば、挑戦する気持ちも生まれます。
付加価値額人時生産性(労働生産性)の向上は中小製造現場の永遠のテーマです。
付加価値額を効率よく積み上げる術を知っている中小現場が生き残ります。固定費を健全に成長させられるからです。
生産性向上に特別な技はいりません。まずは日常業務の仕組みや手順、ルールのチェックです。現場のストレスを放置してムダを発生させていないでしょうか?
弊社のご指導では、「価格力」と「現場力」を連動させ、付加価値額生産性を高める仕事のやり方を明らかにします。自主的な現場活動を定着させることが目標のひとつです。
共有された仕事のやり方がいわゆる「〇〇ウェイ」となります。それが皆さんの現場独自の思考回路を形成するのです。
こうなれば、問題が起きた時に、もはや人間に焦点を当てません。対象は仕組みや手順、ルールです。自ら金属製の鎧を脱ぎたくなります。
自律性が育まれ、生産性が高まりやすくなるのです。
・成長する現場は、仕組みや手順、ルールを変えて生産性を高めている。
・停滞する現場は、ストレスを放置してムダを発生させている。
現場の仕事を、手順化、ルール化する仕組みをつくりませんか?