「生産性ロードマップ戦略」—儲かる工場経営を目指して—第185話 「作業が大変だ」という現場の声を生かすには?
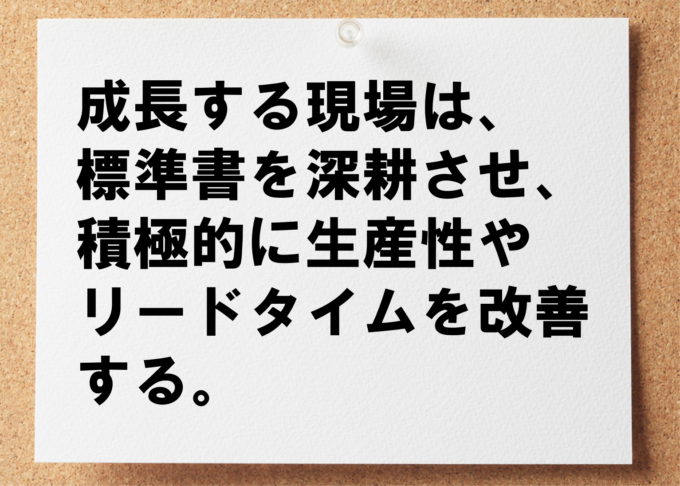
「作業するときに不安があると時間がかかります。」
現場活動のフィードバックミーティングで現場作業者から出てきた言葉です。
その現場では、現場リーダーを中心にして、PDCAを回す準備ができています。現場活動の手順は現場リーダーと作業者との間で共有されている状態です。
ある受注品に対して、生産指令書が発行されたら、そのロットでの取り組みがスタート。現場リーダーが生産活動をフォロー。最後に、生産実績を見える化したらゴール。
製品ごとに、こうしたPDCAを回すことになります。
現場活動の手順を明らかにすることは目標達成に欠かせないことです。目標を掲げれば、あとは現場が頑張って達成するものだという考えを持っていたら改める必要があります。
経営者や幹部は、現場へ目標達成の手順もセットで示さなければなりません。戦略と戦術はセットです。戦術とは戦略を達成するための手段ですから、戦術も伝えないと、現場は行動しようがありません。
その企業では経営者が掲げた戦略に対して、幹部が戦術、つまり社長の考えた戦略を実現させる現場活動の手順を検討しました。
活動自体の流れが明らかになり、今年の年明けより現場活動に着手したところです。手順の中に「フィードバックミーティング」があります。
そこで、製品ごとのチームで生産活動の振り返りをするのですが、現場活動を主導している現場リーダーが気が付いていなかったことを、ある作業者が語ってくれました。
それが冒頭の言葉です。
皆さんの現場には標準書があるでしょうか?
経営者や幹部は標準書の重要性を理解しています。ですから、経営者や幹部が現場に作らせることがしばしばであり、現場に標準書が”在る”ことは多いです。
しかし、”使われている”でしょうか?
あるいは、”使われている”かどうかを把握できているでしょうか?
在ることはあるのだけれども、使われず、後生大事に持っているだけという現場も少ないないです。なかには、ISO9001認証取得のために作っただけで、更新審査を乗り切ればそれでいいですと割り切っている現場もあったりします。
ISO9001の是非は別にして、せっかく手間暇かけて標準書、つまりマニュアルを整備するわけですから、使うことを前提としたいです。
先の現場にも標準書はありました。「工程指示書」が生産命令書と一緒に現場へ届きます。その「工程指示書」に、作業手順が説明されているのですが・・・・・。
現場では、標準書があまり機能していなかったのです。なぜなら、工程指示書の内容には、あいまいな表現が散見され、作業者自身が判断しなければならない作業がいくつもあったからです。
作業の途中で、作業者が度々、自分で判断をしなければならず・・・・・・その結果、どうなるか?冒頭のような状況に作業者は陥ります。
現場リーダーは、標準書の不明確さ故に、作業者が不安を感じて、立ち止まり、考え込むことになっていたとは気が付きませんでした。
作業者へ判断をさせること自体は問題ないです。ただ、判断基準を明らかにしないで、作業者に判断を強いてはダメです。
現場リーダーは現場の生え抜きのベテランでもありますから、作業内を熟知しており、標準書を見れば、自分がするように、作業者は作業ができるはずだと思い込んでいました。
しかし、その標準書を改めて読み込むと、「きちんと」やるとか、「気をつける」という表現にとどまり、結局、「何」を「どこまでどうする」という作業の判断基準が不明確な個所が散見されたのです。
ケーブルをきちんとそろえるのはいいのだけれども、そろえた端部をどこまで整えるのか?
ねじをしっかり締めるのはいいのだけれども、具体的にはどこまで締め付けるのか?
作業者からの声によると、不必要にこだわってしまい、時間がかかっている人もいるようです。現場には良い仕事をしようという意識が溢れているのですが、こうなると、標準書が”使われている”とは言えません。
現場リーダーは、これまで、現場に基準のない判断を強いていたことに気が付きました。
そこで、フィードバックミーティングの場で、記述内容を具体的にどう改訂していくべきかを議論するとともに、標準書の内容を計画的に見直すことにしたのです。
現在使われている標準書の多くは、前任の現場リーダーによって10年前に作成されており、現行の作業内容と一致していない記述がいくつかありました。
その現場では、これから、製品ごとのリードタイムを短縮することに挑戦していくわけですが、作業の手順が不明確のままであると、リードタイム短縮どころではありません。
作業者に判断をさせるにしても、その基準がなければ、不安な気持ちを抱えながらの仕事となるわけです。立ち止まり、考え込み、その分、時間がかかります。
現場活動では生産性向上やリードタイム短縮に挑戦するわけですが、その前提条件として、標準書が使われていることを忘れてはなりません。
目隠ししたままの100m走では全力ダッシュとはいかないからです。
全力ダッシュができるのも、20m、50m先を見通しているからであり、足元で、あれこれやっているようでは、100m走でいい記録が出るわけはないのです。
目標を達成する手順を共有しないままでは、生産性やリーダータイムを対象にした現場活動を一体感を持って進めることはできません。
生産性向上やリードタイム短縮を目的とした現場活動において、標準書は”在る”だけではダメで、作業に関して不安を抱かせない、不必要に立ち止まらせない、考え込ませない、こうした状態で仕事ができるよう”使われている”ことが絶対です。
標準書で作業内容が明らかになっていると、作業者は先を思い浮かべながら、今の作業に全力投入できます。
作業者の声に耳を傾けてください。作業者が「作業が大変だ」と発言していたら、その趣旨を汲み取る必要があります。
いろいろな現場でのフィードバックミーティングに参加して気が付くことですが、作業者から出される「作業が大変だ」という発言の裏には下記があります。
1)作業が複雑で時間がかかり、間違えやすい。
2)作業が職人的で難易度が高く、時間がかかる。
作業の単純化、簡素化のほか、スキルアップ、多能工化が解決策です。
3)肉体的、精神的に辛い。
重量物を扱うことや時間がかかることによるストレスが原因であり、抜本的に作業を変える必要があります。
4)治工具類や設備が足りない。
設備投資にも関連することですが、現場の要望を実現させると、工数削減やリードタイム短縮へつながることが多いです。
「作業が大変だ」と作業者が語る背景には上記のようなものがありますが、さらに、次のことがあるなら、あらゆることに優先して標準化を進めなければなりません。
5)そもそも、仕事の手順が明らかにされていない。
現場丸投げはダメです。現場の作業は標準化されていないといけません。仕事を進める判断基準を現場へ明らかにするためです。
さらに”在る”だけでもダメです。”使われている”かどうかを把握する必要があります。標準書は作るだけでなく、深耕させることも欠かせないということです。
今回のやり取りは、現場と上司とのコミュニケーションを深めるきっかけとなりました。定期的なフィードバックミーティングで現場の問題点を明らかにしようと全員で確認したところです。現場一体化へ寄与しそうです。
次は貴社の番です!
・成長する現場は、標準書を深耕させ、積極的に生産性やリードタイムを改善する。
・停滞する現場は、作業は現場へ丸投げなので、改善活動の意義を見出せない。