「生産性ロードマップ戦略」—儲かる工場経営を目指して—第190話 手離れの良い生産現場をデザインするには?
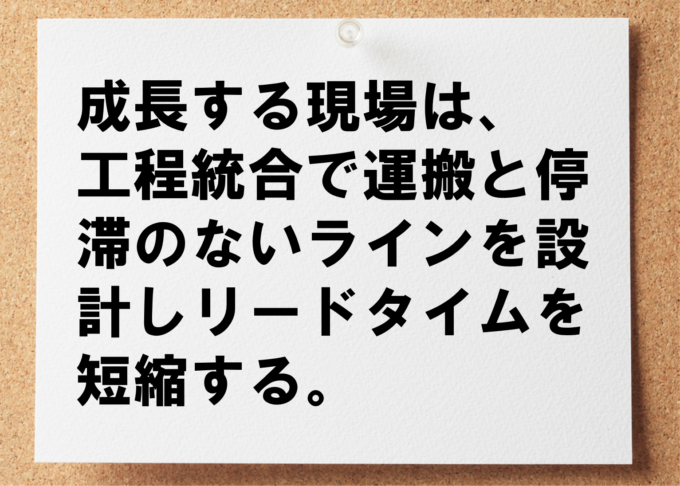
「先生、製造と検査を一緒にするのもありですね。」
30人規模の生産ライン、製造課長の言葉です。
儲けの見える化で現場のベクトルを揃えました。製品別のフィードバックミーティングも軌道に乗り始め、現場活動の小さなPDCAが回り始めたところです。
そこで、プロジェクトを次のステップへ進めるため、メンバーと具体策を議論しました。
製販一体で付加価値額を積み上げる全体像を理解した後、課題をメンバーで検討していたときのことです。リードタイムを決定する2つの設計に言及しながら、製造課長がひとつの具体策を口にしました。
それが冒頭の言葉です。
貴社の付加価値額人時生産性はどれくらいですか?
付加価値額の定義によって若干変動しますが、大手製造企業では6,500円/人時、中小製造企業では3,600円です。中小企業白書で公表されています。
自らの意思で事業を展開している経営者であるなら、豊かな成長を実現させ、従業員へ少しでも多くの給料を払ってあげたいと考えているのではないでしょうか?
ただし、無い袖は振れません。
さらに、小売りやサービス業と異なり、技術の進化に合わせた設備投資も持続的な競争力に欠かせません。
これらを踏まえると、固定費を健全に成長させられるかどうかが儲かる工場経営の要諦であることに気付きます。
したがって、中小製造企業の儲ける力とは固定費を効率良く回収する力であり、それが付加価値額生産性です。それも単位は「人時」です。
「人日」で評価するのは時代遅れであることは論を俟たないでしょう。
したがって、付加価値額人時生産性を判断基準に、製販一体となった現場活動を展開することになります。
先の企業でも3,000円台前半の数値を4,000円、5,000円へ引き上げようと、取り組みに着手しました。
人口減少、少子化という避けられない外部環境変化にあって、21世紀は積み上げの時代です。コスト削減の重要性に変わりはありませんが、豊かな成長を目指すなら、生産計画で「詰めて、空けて、取り込む」です。
取り込むために詰めます。経営者の意思を「取り込む」に示すのです。「取り込む」ことまでを考えないと儲かりません。製販一体の活動が欠かせない所以はここにあります。
そのために、まず何をどうするのか?
リードタイム短縮です。リードタイムを短縮して、「詰めて、空ける」を実現させます。言い換えると「手離れの良い生産現場をデザインする」です。
「手離れの良い生産現場をデザインする」定石がいくつかあります。定石中の定石は「工程分析4つの記号」から導かれます。
先の現場でも手離れの良い生産現場をデザインするために考えたことは、この「工程分析4つの記号」です。
「工程分析4つの記号」とは下記です。
・加工
・検査
・運搬
・停滞
一見複雑な製造現場は4種類の工程に分類されます。現場で実際に製品の流れを見ていると実感できるはずです。そして、重要なことは・・・・・。
4つの工程のうち、価値を生み出す工程はどれか?ということです。
一般的に、価値を生み出す工程は「加工」だけと言われています。
昨今、「検査」も価値を生み出していると考えられるかもしれません。検査料を見積もりに上乗せできることが少なくないからです。
このように「検査」が価値を生み出すか否かは議論の余地がありそうですが、ただひとつ明らかなことがあります。
それは、「運搬」と「停滞」は、絶対に価値を生まないと言うことです。
パレットに積んだ仕掛品をフォークリフトでどんなに運ぼうが、また、作業者が製品を手にしてどんなに走り回ろうが、原則、顧客にとっての価値を生み出すことはありません。
停滞に至っては説明は不要でしょう。長期停滞をしている仕掛品や完成品は眠っているお金に他なりません。
したがって、リードタイム短縮を目指して手離れの良い製造現場をデザインしようとするなら「工程分析4つの記号」の考え方から次のことが導かれます。
・「運搬」と「停滞」抜きのラインを設計する。
リードタイムを決定する工程設計の勘所はこれです。
工程設計を考える時のキーワード、「工程統合」を考えます。
従来工程が工程A1と工程A2の2工程構成であり、それを工程Aの1工程に「工程統合」するとどうなるでしょうか?
工程A1と工程A2の間に存在している「運搬」と「停滞」が消えます。この分だけリードタイムが短縮される訳です。
先の現場では、製造と検査を別工程と考えており、場所も離れています。したがって、製造と検査の間に「運搬」と「停滞」があるわけです。
製造課長はそれをなくそうとしています。
ただし、こうした工程設計では留意点があります。全体最適化の思考回路を全員で共有していることが、前提条件にあるということです。
自分たちの仕事だけをやっていれば問題ないだろうという考え方しか持てない現場を対象に「工程統合」はできません。
全体最適化のためには、従来の仕事のやり方を変える必要があるからです。
自分たちの仕事のやり方を優先させる現場に、こうしたことが無理であることは火を見るより明らか、全体最適化は絵に描いた餅に終わります。定石や手法で成果を出せるのも、現場のベクトルが揃っていて、目的を共有できているからです。
先の現場では、製造課長が目的をしっかり説明しています。新分野へ進出して付加価値額を積み上げる新たなチャンネルを獲得することが狙いです。
経営者は既存顧客にだけ依存していてはジリ貧になると危惧しています。経営者の健全な危機感を理解できている現場です。新分野へ進出するために基礎体力を高めようとしています。
リードタイム短縮を目指して手離れの良い製造現場をデザインしようとするなら、定石や手法だけでなく、全体最適化の考え方を理解させる必要があります。
成果を出す現場の行動は早いです。そして、あらゆる行動に一体感を感じます。
次は貴社の番です!
・成長する現場は、工程統合で運搬と停滞のないラインを設計しリードタイムを短縮する。
・停滞する現場は、自分たちの仕事のやり方を優先させるので工程統合ができない。