「生産性ロードマップ戦略」—儲かる工場経営を目指して—第191話 仕掛品を減らすには?
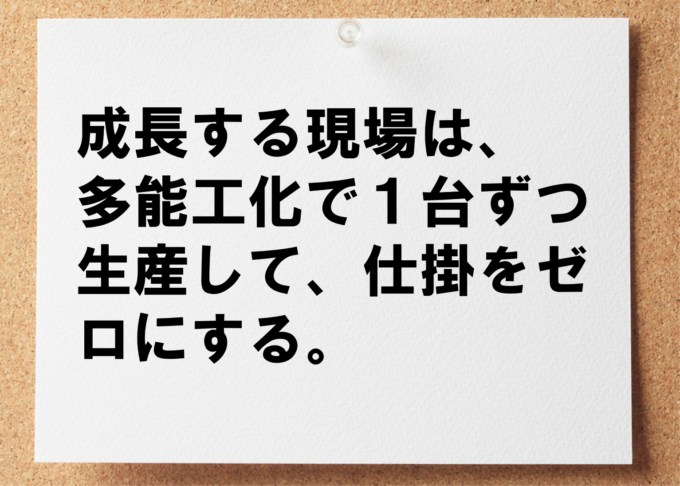
「先生、机1つ分を目指してみます。」
100人規模の電子機器組み立て企業、製造管理者の言葉です。
その企業では今月から「生産革新」プロジェクトを本格化させています。
経営者からご相談をいただき、現場へ足を運んだときのことです。その経営者は現場を見ながら経営問題を説明してくださいました。
「机の上を見てください。とにかく仕掛品が多すぎます。もっと、どんどん製品を回すようにしたいのです。」
プロジェクトのきっかけは経営者のこの言葉です。
机の上に停滞している仕掛品を減らすにはどうしたらいいのか?
具体的な取り組みを検討しているなかで、作業スペースのことが話題に上りました。その時、製造管理者が口にしたのが冒頭の言葉です。仕掛品を減らす本質をついています。
その職場には、横長のテーブルを横に5つ並べている「島」が10列程あります。これまで、その「島」を作業台として、ロット単位で製品を組み立てていました。
受注数量が20台なら20台分の製品を並べます。
受注数量が30台なら30台分の製品を並べます。
納入に必要な数量を並べながら組み立てるロット単位の作業です。ですから組み立て作業が全て完了するまで、中間製品が現場に停滞します。
終業時に、仕掛品が机の上に置かれたままになっていることがしばしば、常態化しているのです。経営者はこれを気にしていました。
多くの仕掛品を抱えながら生産している現場では、手順上のミス、品質上のミスのリスクが高くなります。キャッシュフローの観点からも望ましいことではありません。
では仕掛品を減らすにはどうすればいいのか?
先週のコラムで「リードタイム短縮を目指して手離れの良い製造現場をデザインする」ことを考えました。「工程分析4つの記号」を紹介しましたが、仕掛品を減らすときも全く同じ考え方を適用します。
・「運搬」と「停滞」抜きのラインを設計する。
「停滞」を必要とするラインなので、仕掛品が生まれるのです。横長のテーブル5つ分のスペースがあるからそうしたつくり方になっているとも言えます。「停滞」する暇がなければ仕掛品は生まれません。
ではどのように「停滞」する暇をなくするか?
ここで、製品Zを5台、組み立てる事例を考えます。基板に部品A、部品B、部品C、3つの部品が取り付けられている製品です。
従来のようにロット単位で組み立てるとします。部品の取り付け手順は次です。
A、A、A、A、A、B、B、B、B、B、C、C、C、C、C。
完成品はどの時点でできるでしょう?
手順の11番目以降です。中間製品は、手順の10番目まで、停滞することになります。つまり、5台分の仕掛品を置くスペースが必要です。
一方、次の取付手順ではどうでしょうか?
A、B、C、A、B、C、A、B、C、A、B、C、A、B、C。
この場合、完成品はどの時点でできるでしょう?
手順の3番目、6番目、9番目、12番目、15番目です。1台分の組み立てスペースがあれば十分です。仕掛品は発生しません。作業が終わったら「1台ずつ造っている」からです。
工程統合を重ねていくと、「停滞」をゼロにする生産方式に行きつきます。1人屋台方式、セル生産方式といわれる方式がそれです。
それまで、部品をロット単位で組み立てるやり方から1台ずつ組み立てるやり方に変わります。したがって、作業者は自分が担当する製品全体を理解していないとなりません。
工作機械職場で言うなら、旋盤もフライス盤も研削盤も・・・・多種の技能が求められます。「自分はこれだけやっていればいい」と勝手に考える職場では成立しないのです。
従業員の多能工化も経営課題となります。結局、現場ひとりひとりのモチベーションがプロジェクト成否のカギを握っています。
・作業スペースは1台分だけで十分である。
・仕掛品は原則、発生しない。
仕掛品を減らすことと生産に必要なスペースを減らすこととは同義です。
小ロット生産や需要増への対応が容易で、作業スペースも少なく済みます。
したがって、現場で同時に組み立てる品種数も増やせます。
部品ごとの繰り返し作業なので従来の方が優れているように感じるかもしれません。しかし、ロットで生産していると、知らないところで「運搬」と「停滞」が生み出されるのです。
1台ずつ造るという新たな生産方式に変えるには、従来の仕事のやり方を変える必要があります。多品種小ロット化への対応力を高めるためです。
付加価値額人時生産性を向上させる具体策であることを理解してもらい、新たな仕事のやり方に挑戦してもらう環境づくりも経営者や幹部の重要な仕事となります。
先の現場には、新たなことに挑戦しようという雰囲気があります。「これまで1台ずつ組み立てたことがなかったのでちょっとたいへんでした。」とは作業者Aさんのコメントです。
従来の工具や部品の置き方の前提はロット単位での組み立てでした。Aさんは、1台ずつ組み立てるには、別のやり方があることに気付きました。
さっそく、Aさんは、次回のトライアルに向けて工具と部品の配置のやり方をあれこれ考え始めています。
先の現場では、生産革新プロジェクトの対象となった製品での成功をプロジェクトのひな型にしようと考えています。新たな付加価値額を積み上げる手法とするのです。
試行錯誤は続きますが、ワクワク感が加わった試行錯誤です。多能工化にもじっくり腰を据えて取り組もうとしています。競合には見えない強みです。
次は貴社の番です!
・成長する現場は、多能工化で1台ずつ生産しで仕掛をゼロにする。
・停滞する現場は、1台ずつ生産していては効率が低下する思い込んでいる。