「生産性ロードマップ戦略」—儲かる工場経営を目指して—第189話 現場で共有しなければならない判断基準とは?
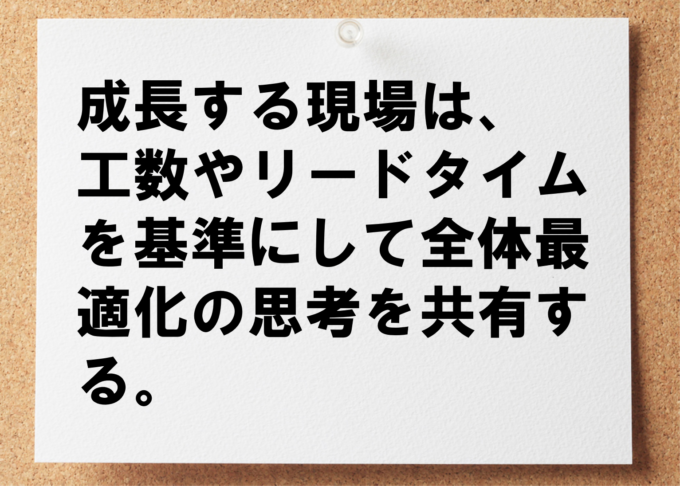
「見えないものが見えてきました。」
現場活動に着手した、機械加工企業、現場リーダーの言葉です。
受注生産の製品は、生産回数に基づくと大きく2つに分類できます。
1)生産が1回で終わる製品
2)生産が繰り返される製品
先のリーダーは前者を対象に見積もりの精度を高めようと考えました。
生産が1回きりの特注製品でも、製造現場で目標としなければならない数値があります。
見積もり価格です。
この見積もり価格には、固定費回収のために「現場へ投入される工数」が含まれています。
したがって、生産回数にかかわらず、この「現場へ投入される工数」がリーダーたちの判断基準になるのです。現場の勝手な都合や、個人の力量を基準に仕事をしているようでは儲かりません。
先のリーダーは従来の仕事のやり方に危惧を抱いていました。
半年以上の準備期間を経て、「現場活動に取り組まなければ生き残れない」という点で、先のリーダーを含め、数人のリーダーたちのベクトルが揃ってきたところです。
さっそく、作業日報の様式を見直して、実績工数を見積もりで設定された「現場へ投入される工数」と比べられるようにしました。
中でも取り組みに熱心な先のリーダーが、実績と見積もりを比べられるようになって、感じたことを報告してくれました。
比べることで、”考える”ことができようになったというわけです。判断基準を手にしたとも言えるでしょう。何か漠然としていたものが明らかになったのですから。
それが冒頭の言葉です。
製造現場で”考える”とは、”比べる、比較する”ことと言い換えられます。
・作業者の動作では、「作業標準」と比べて改善の余地がないかどうかを考える。
・検査では、「品質基準」と比べて不適合品がないかどうかを考える。
・経営判断では、「全社の付加価値額人時生産性」を月間、年間で比べて儲かる体質になったかどうかを考える。
・現場活動では、「製品別の付加価値額人時生産性」を活動前後で比べて成果があったかどうかを考える。
などなど。
製造現場でも、工場経営でも、私達は常に”実績”と”何か”を比べているのです。そして、差を認識して次の行動へ移行します。
実績と比べるものがなければ考えることができないわけです。考えられなければ、判断ができず、フィードバックもできません。フォローと評価が疎かになります。
皆さんの現場には実績と比べる対象、つまり標準や基準があるでしょうか?
現場の一体化、ベクトルを揃える上での重要な論点でもあります。
私達は常に”実績”と”何か”を比べています。
この”何か”が、「現場の勝手な都合」や「個人の力量」になっていませんか?また、「経験」だけを比べる対象にしてるベテランがいませんか?
これでは、「自分はベストと思うやり方でやっているのだからそれで問題ない」という思考回路を放置することになります。判断基準が自分なのです。
自工程の最適化を目指した部分最適化にすらなっていません。いわんや会社の最適化を目指した全体最適化においておやです。
これではベクトルが揃いません。
また、「納期さえ守っていれば問題ない」という思考回路も、今となっては、同じようなものと言わざるを得ません。
安定した受注が約束される時代なら、顧客の納期に合わせて工場を回していれば大丈夫です。しかし、時代は変わりました。
いつ何時、安定した受注が電話一本でなくなるやもしれないのです。
現状の生産計画を基準にして、詰めて、空けることに挑戦し続けなければなりません。新たな受注を取り込み、積極的に付加価値額を積み上げられるようにします。
削減の時代から積み上げの時代へ変わりました。
比べる対象を明らかにして、積み上げる思考回路を共有したいのです。経営者は判断基準を統一しなければなりません。
製造現場にとって、納期は身近な判断基準です。ただし、繰り返し申し上げますが、これだけでは儲からなくなりました。
儲かる価格に基づいて判断基準を設定したいのです。製品の生産回数を踏まえて、判断基準を設定します。
1)生産が1回で終わる製品:見積工数や見積リードタイムを判断基準にする。
2)生産が繰り返される製品:目標工数や目標リードタイムを判断基準にする。
実施が難しいのは前者です。1回しか生産の機会がありません。この場合、実績と見積もりに乖離があったらどのように考えるのか?
・現場の実績が劣っている。
・見積もり精度が劣っている。
両者を両天秤にかけながら知見を得るのです。
今や多品種少量生産は当たり前と言われますが、多品種であってもグルーピング、分類は可能ではないでしょうか?グループピングができれば、知見を新規製品へ生かせます。
ただし、生産が1回で終わる製品の場合、生産形態が現場独自であることが多く、定石がない分、生産が繰り返される製品よりも取り組みは難しいです。
しかし、難しいからこそやりたいのです。独自のノウハウは外からは見えません。見えない限り競合はマネできないわけで、圧倒的な強みになります。
中小製造企業の生き残りのカギは付加価値額人時生産性を高めることです。
固定費を豊かに成長させられる中小現場こそが、変化に対応し、日進月歩の技術革新を生かせると考えるからです。削減の発想だけでは行き詰ります。
付加価値額を積み上げるには?という発想も加えて儲かる工場経営を考えたいです。
会社全体の付加価値額を高めるときに分母と分子のそれぞれをどうするか考えるわけですが、現場としては、まず分母に注目。
密度の濃い工数を現場へ投入することが目標となります。
したがって、儲かる現場活動の初手は工数削減やリードタイム短縮であり、付加価値額積み上げ作戦の橋頭堡です。
経営者は現場を導く役割を担っているリーダーに、こうした思考回路を共有させる必要があります。
自分勝手な判断基準が放置されていると、プロジェクトは絶対に行き詰まるからです。大きな成果を手にするためにも、確実な足場を現場に構築しておきます。
考えるとは比べることです。
ブレない判断基準の共有がブレないプロジェクトに欠かせません。キーパーソンたちのベクトルが揃っていなければ、焦ってプロジェクトを進めても必ず頓挫します。
考える判断基準の有無が現場の風土や文化も決めるからです。
・見積工数や見積リードタイム、目標工数や目標リードタイム
→ 全体最適化に従った判断基準
・現場の勝手な都合や個人の力量や経験
→ 個人の勝手な判断基準
どちらが豊かな成長に貢献するかは言うまでもありません。まずは、考えるための判断基準の共有化に力を注いで下さい。製造現場では、製品別の工数とリードタイムです。
日本の製造業の労働生産性は2017年時点で98,157ドルです。現在、世界第14位です。
2000年頃まではトップクラスに位置していましたが、2005年は9位、2010年は11位、2015年は16位と年を追うごとに順位を下げていきました。
現在の生産性は米国の概ね7割の水準です。
生き残りをかけて、仕事のやり方を変えなければならないことだけはっきりしています。会社の規模に関係なく付加価値額人時生産性を高めるのは製造業にかかわる私たちの使命です。
従業員や地域のためだけではなく、国益にもかないます。
志を高くして最初の1歩目を踏み出しませんか?
プロジェクトを成功させるカギはキーパーソンたちに当事者意識を持たせることです。やるのか、やらないのかとごちゃごちゃ言っている時間はないのです。ただひたすらに、「どうやったらできるのか」に焦点を当てなければなりません。
先の現場でもキーパーソンたちのベクトルが揃ってきました。比べる仕組みの構築に着手したところです。
ブレない判断基準が共有され、考える拠り所を同じにできます。これからの取り組みは加速されるはずです。
次は貴社の番です!
・成長する現場は、工数やリードタイムを基準にして全体最適化の思考を共有する。
・停滞する現場は、個人の勝手な判断基準で工程毎の部分最適化すら実現できない。