「生産性ロードマップ戦略」—儲かる工場経営を目指して—第237話 プロジェクトが遅れたときに現場へ何を問いかけるのか?
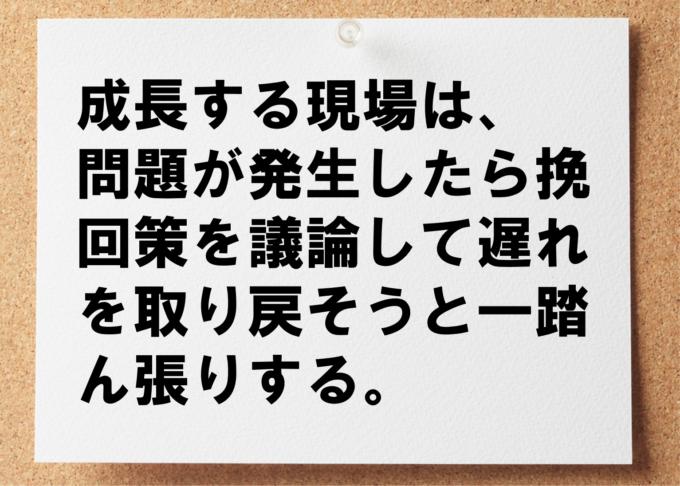
「できないと、直ぐに、できない理由ばかり言ってきます。」
半年前に人時生産性向上プロジェクトに着手した、産業機器企業経営幹部の言葉です。
プロジェクト体制の整備を終えて、進捗状況を定期チェックする段階に至りました。従来と同じことをやっていても儲かりません。プロジェクトの狙いは「変える」です。
「変える」思考回路を全員で共有するまで、試行錯誤が続きます。幹部は理解していても、主役となるプロジェクトメンバーひとりが同じ目線になっているとは限りません。
新たなことへの拒否反応もあります。冒頭の言葉です。そこで、次のように尋ねました。
「メンバーへはどう応えましたか?」
切削加工、表面処理、射出成形、鍛造、鋳造、プレス加工、熱処理、塗装等々は製造業の基盤技術です。技術で起きる各種現象には、因果関係があります。
貴社でも品質不具合品が発生したら、原因を究明していませんか?
前職の自動車部品工場も同じでした。
対象の基盤技術は鋳造、熱処理、切削加工、塗装。光学顕微鏡やSEM、発光分光分析、化学分析、および各種機械的性質試験で分析して、不具合品の発生原因を究明しました。
なぜ、原因を究明するのか?
科学的、工学的に的を射た対策を打つためです。
工学的ノウハウ蓄積という観点でも、分析に基づいた原因究明は欠かせません。
プロジェクトでは、計画が進まず、遅れることがたびたびあります。そうした際、貴社ではメンバーへ何を問いかけますか?遅れの原因を明らかにして・・・。原因が気になります。
しかし、ここで必要なのは・・・・・挽回策です。遅れ原因の解明ではありません。
プロジェクトに求められるのは成果です。遅れを取り戻し計画に追いつかなければなりません。原因究明も大切ですが、まずは成果を出せる状況に戻すことです。
プロジェクトのみならず、あらゆる仕事には納期があります。経営者の仕事は進捗をフォローして評価することです。遅れを認識した経営者は現場に問わなければなりません。
「遅れている状況にあるのは理解できた。で、次、どうする?」
挽回策に焦点を当てます。
現場や担当者に遅れの原因を説明させると、言い訳になっていませんか?
「設計からの図面が遅れたから。」
「外注先からの納入が予定通りでなかったらから。」
「予想外の不具合が発生したから。」
「作業者が指示した通りにやらなかったから。」
人は自分がかわいいものです。原因は自分の「外」にあると思いたくなります。これは人の本質のようなものですからしかたがありません。
問題が発生して原因を究明しようとすると(自分以外の)犯人捜しになってしまうことがしばしば。「個人」を責めることになります。本来なら、問題を未然に防げなかった「仕組み」を責めないとならないのに・・・。
いずれにせよ、プロジェクトでは、遅れの原因を究明しても、遅れは取り戻せません。
技術は科学、工学です。明確な因果関係があります。したがって品質不具合など、技術上の問題が発生したら原因究明がお作法です。
現象を分析して、軌跡を辿れば根本原因へ至ります。工学的に適切な対策のためです。明確な因果関係に基づきます。
一方、プロジェクトのような仕事で遅延などの問題が発生したときに必要なのは原因究明ではありません。挽回策です。
経営者が欲しいのは成果です。まずは遅れを取り戻さなければなりません。
遅れた原因、できなかった原因を言い合っている暇があったら、力尽くでも挽回することです。最優先事項はプロジェクトの推進です。
当然のことですが、問題発生の原因を分析して振り返ることは必要です。仕事のやり方を変える機会になります。
ただ、優先順位から考えると、明らかに挽回策なのです。成果を出すためのプロジェクトや仕事ですから。
技術とは違って、プロジェクトは人為的行為です。原因究明では、人的要因から逃れられません。感情的な要因も加わります。
責任の所在が「個人」ではなく、「仕組み」にあるという考え方が浸透している現場でない限り、プロジェクトの遅れを追求しても、スッキリした議論にはならないことは火を見るより明らかです。
技術上の問題が発生したら、3現主義に基づき原因究明をして適切な対策を考える。
プロジェクト上の問題が発生したら、計画通り成果を手にするための挽回策を考える。
技術上の問題とプロジェクト上の問題への対応は異なります。人為的行為に対しては「言い訳できない」環境づくりが必要なのです。成果を数値で示すことは環境づくりの具体項目になります。
製品別人時生産性を6,000円→7,000円へ高めることを計画したとします。そして具体項目を3つ計画しました。実行したけど、6,500円に留まったとしたら、それが答えです。
振り返って、原因を探っても7,000円にはなりません。500円分高める挽回策が必要です。
アフターコロナです。製造現場は新たなことに挑戦し続けなければ生き残れません。振り返る暇があったら、挽回策で前進あるのみです。問うのは「それで、次どうする?」です。
「できないと、直ぐに、できない理由ばかり言う」現場があるとしたら、そもそも、そうした言動を許してきた雰囲気や風土に問題があります。それを変えるのが課題の本質です。
経営者は、現場へ人時生産性を問います。生き残るためですから、内部の事情は関係ありません。プロジェクトはベクトルを揃えるところからです。
次は貴社の番です!
成長する現場は、問題が発生したら挽回策を議論して遅れを取り戻そうと一踏ん張りする。
停滞する現場は、問題が発生したらできない理由をあげてはモチベーションを下げる。