「生産性ロードマップ戦略」—儲かる工場経営を目指して—第310話 非常時に立ち向かう思考回路が共有されているか?
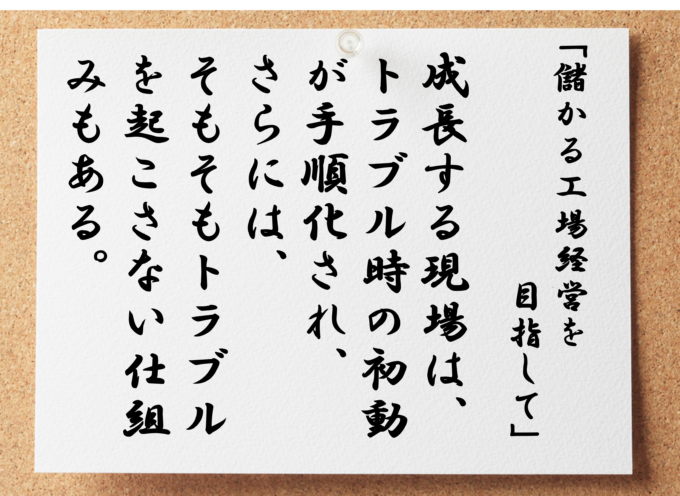
「納期調整に追われています。」
50人規模中小製造企業、経営者の言葉です。
人時生産性向上プロジェクトも折り返しです。取り組みを加速させようとしていた矢先、現場の要となる設備が故障してしまいました。
初めての故障です。「想定外でした。」とは先の経営者の言。
起きてしまったことはしかたがありません。設備を復活させることに全精力を傾けます。さらには、足元の納期対応もしなければなりません。冒頭の言葉です。
緊急度の高い業務に専念します。重要度が高くても、緊急度の低いプロジェクトは一時、停止です。
家が火事になったら、必死に火を消します。当然の対応です。理屈はありません。目の前で大切な家が燃えています。全てに優先して消火活動に専念です。
一生懸命な消火活動が功を奏し、なんとか全焼は免れました。
やれやれです・・・と、ここで思考回路を止めてはいけません。喉元過ぎれば熱さを忘れる。やれやれで思考を止めてしまったら、また同じ失敗をやらかすかもしれないのです。
・万が一火事がまた起きても、被害をもっと最小化できるようにする。
・そもそも火事を起こさないようにする。
前者も大切ですが、抜本的な対策は後者です。
日本の平均賃金は21世紀になってから横ばいです。伸びていません。日本の低労働生産性が指摘されていますが、このあたり、低生産性なので賃金が低いのか、賃金が低いから低生産性なのか、鶏と卵のような議論があるようです。
儲かる工場経営の要諦は、お客様に選ばれる商品や製品を効率良く造ることであるとお伝えしています。したがって、低賃金問題解決の本質は「お客様に選ばれる」です。
選ばれてさえいれば価格競争に巻き込まれません。稼げるビジネスモデルで解決です。経営者は従業員の平均給与を上げられます。上げられないのには理由があるのです。
例えばキーエンス、東京エレクトロン、レーザーテック各社の平均年収は下記です。
キーエンス 1,751万円
レーザーテック 1,379万円
東京エレクトロン 1,285万円
(2021年度有価証券報告書から)
各社共に、事業モデルや製品に特徴があって、お客様に選ばれています。国内の平均賃金が横ばいの中、こうした企業もあるのです。
(ちなみにパーソルキャリアが運営する転職サービス「doda」によると2021年の平均年収は403万円。昨年から6万円の減少とのことです。)
人時生産性10,000円以上、大手のやり方も参考にします。イイどこ取りで、貴社独自の儲かる工場経営を実践し人時生産性を高めるのです。
3,000円、4,000円台に甘んじません。経営者は従業員の物心両面での幸福を願うからです。常時の戦略は、お客様に選ばれる商品や製品を効率良く造ることにあります。
ただし、現場ではいろいろなことが起きます。労災や品質クレーム、設備故障などの突発的なトラブルは避けられないものです。
これらが起きると「非常時」です。「常時」活動を止めなければなりません。そうして、直接的、間接的なロスが発生するのです。現場には常時活動を阻害する非常時が起きます。
昨今は自然災害への備えも求められます。BCPをお持ちの経営者もいらっしゃるかもしれません。BCPを決めておけば、初動は上手くいきそうです。
「非常時」は2つあります。避けられないトラブルと避けられるトラブル。
避けられないトラブルとは新型コロナウィルス感染拡大、原材料高騰、原油高、物価高、ウクライナ侵攻、自然災害などのことです。これらは避けようがありません。
一方で労災や品質クレーム、設備トラブルは全て我が社の事情で起きます。避けようと思えば避けられるのです。
まずは「火事が起きたらどうするか?」をルール化します。そうすれば、初動で迷いません。被害を最小化できます。これで経営者は少し枕を高くして寝られるのです。
そして、さらに考えれば、「そもそも火事を起こさないようにする。」に至ります。避けられるトラブルなら、避けるに越したことはありません。
「非常時」戦略
1.トラブルが起きたらどうするか?手順を決める。
2.そもそもトラブルを発生させない仕組みをつくる。
先の企業で起きた設備故障は全く想定をしていないものでした。ノーガードだったということです。したがって、トラブルが起きてから、具体行動を考えました。
常時に戻るまで2ヶ月余りを要したのはノーガードだったからです。収益上のダメージは小さくありません。
製造の要となる設備が故障したらどうするか?
設備トラブル復帰の手順を明らかにします。初動が肝要です。
まずは故障箇所を特定しなければなりません。それを特定できたら、復帰の具体策を考えます。部品を交換すればイイのか?外部のサポートが必要になるのか?
そして、整備が復帰するまでは、常時の製造活動ができません。非常時の製造活動です。他部門から人を送ってもらいながら人海戦術で乗り切ります。外注先の協力も欠かせません。特殊工程ならなおさらです。
そして、そもそも設備トラブルを起こさない仕組みをつくります。事後保全だけでなく、予防保全の実践です。
現場では、部品の在庫管理、設備保全の知見を深めます。そして、経営者も設備1台1台の状況を把握するよう努めるのです。老朽化の程度や故障の起きやすさ等、設備毎の癖を知らなければ的確に判断できないことがあります。
予防保全の重要性を現場に指導することも欠かせません。いわゆる緊急度が低い仕事だからです。こうした仕事の成果は日頃、見えません。それだけに、設備トラブルを起こさない仕組みの定着には思考回路の共有が鍵となるのです。チーム力が問われます。
1.設備故障が起きたらどうするか?手順を決める。
2.そもそも設備故障を発生させない仕組みをつくる。
現場の担当者だけでなく、全員にこの考え方を浸透させなければなりません。設備保全の深い知識と経験が必要となるので、人材育成も大事です。
さらには進化する技術に対応した設備投資の計画も対策になります。IOTを活かした予防保全の設備を設置することも具体策です。
手順を決めて、仕組みをつくる過程で人と設備へお金を掛けることになります。3年先、5年先を見据えた取り組みです。トップダウンでしかできません。時間を要するものです。
先が見通せず、いろいろなトラブルが起こる時こそ、時間軸を意識したロードマップが必要になります。トラブルへの対応力とは変化への対応力に他なりません。
羅針盤があれば、経営者は変化への対応がやり易くなります。判断基準があるからです。ズレがあれば、軌道修正をします。「3年先、5年先の構想」があるから修正ができるのです。
トラブルや変化があるので計画を立てても無駄だと考える経営者がいらっしゃいます。それは間違いです。逆です。トラブルや変化があるからこそ、経営者はロードマップでブレない軸を持つ必要があります。そうでないと、目的地を見失ってしまうのです。
こうして出来上がった手順や仕組みは、避けられないトラブルへの対応力も高めます。従業員の心構えや姿勢も変わるからです。
非常時は立ち向かって対応するものです。非常時に立ち向かう思考回路が現場で共有されれば自ずと当事者意識も生まれます。経営者は社長業に専念できるのです。
次は貴社の番で!
成長する現場は、トラブル時の初動が手順化された上にそもそも起こさない仕組みもある。
停滞する現場は、喉元過ぎれば熱さを忘れるのでトラブルを繰り返している。