「生産性ロードマップ戦略」—儲かる工場経営を目指して—第376話 右腕役に繰り返し語ってもらっているか?
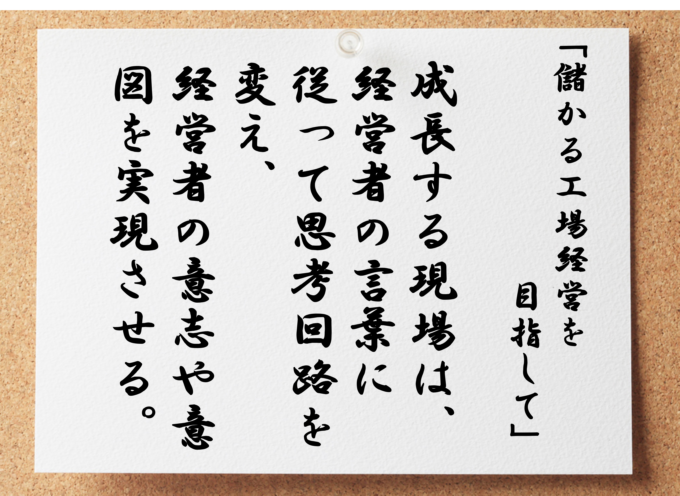
「在庫スペースが半分になりました。」
製造設備メーカー工場長の言葉です。
1年半のPJが仕上げ段階に至りました。PJ着手時、経営者から出された指示事項のひとつが完成品在庫の圧縮です。運転資金に関連しています。
将来構想は事業成長による人時生産性向上です。我が社を豊かに成長させます。課題のひとつが在庫圧縮です。物流増へ先手を打ちます。
ただし、PJリーダーの工場長にとって、完成品在庫圧縮は初めての挑戦でした。熱意はありますが、やり方がわかりません。わからなければ習得すればいいだけのことです。
半年間の現場とのすったもんだの末に在庫管理の仕組みを定着させました。そして、その後、実務の継続です。成果は目で見て分ります。
完成品在庫置き場で先の工場長がニコニコしながら説明してくれました。
冒頭の言葉です。
在庫管理は2つで考えます。
・ただいま現在の在庫を見えるようにする。
・製造物量と着手時期を決めるルールをつくる。
まずは、管理する以上、ただいま現在の在庫を見えるようなっていなければなりません。管理とはビフォーアフターです。
原材料、仕掛品、完成品、3つの棚卸資産は下記BOX構造で分ります。
月初在庫+原材料購入=原材料消費+月末在庫
月初在庫+製造着手=製造完了+月末在庫
月初在庫+製品完成=製品出荷+月末在庫
月初の数値とBOXへの入と出を押さえれば、月末の数値が明らかになる構造です。システム上の数値はこれで出されます。リアルな棚卸しと比べて数値の精度を高めます。
このBOX構造を活かせば、「ただいま現在の在庫を見えるようにする。」は可能です。
ただ、理屈はそうであっても、現場で実践しようとすると、意外と難しいものです。
・必要なデータを確実に整理する
・毎日、毎週、毎月、定期的にリアルな棚卸しを実施する
こうした実務を地道に継続する体制が必要です。
リアルな棚卸しでは、細かいけども実務的には決めておかなければならないことが、いろいろとあります。棚卸しの間、生産活動はどうするのか?棚卸の最中に、理由があって移動させた在庫はどう処理するのか?
そもそも、なぜ在庫管理をしなければならないのか?のベクトル揃えも欠かせません。
製販一体でこれらを理解していないと、現場の自主性を引き出せないです。
先の工場長は、運転資金という工場経営の観点を「省スペース」に翻訳して現場へ伝えています。完成品在庫圧縮の目的を「省スペース」にあると現場へ説明し協力を求めました。
その方が、現場は成果を実感できます。分かりやすい説明は現場に受け入れられます。
成果を出す右腕役は、作業者に協力をお願いするのが上手です。
目的をはっきり伝えるからベクトルが揃います。目標を日々に小さく区切り、作業者を日々の小さな目標達成に没入させるので揃ったベクトルがブレません。
小さな目標達成に日々没入させる環境があれば、すったもんだしている暇などないのです。
・必要なデータを確実に整理する
・毎日、毎週、毎月、定期的にリアルな棚卸しを実施する
記述すればたった2行のことですが、先の現場にこれが定着するまで半年を要しました。
工程管理にはお作法があり、それをやれば上手くいくことが明示されています。ただ、決められたことを守る、ルールを守る、仕組みを回すのは5Sの5番目次第です。
現場力が問われます。
先の企業では、現場へ目標必達を必死に訴えてきた経営者とその右腕役の工場長が現場を主導しました。現場力の不足を補うためです。
意志改革と現場改革はトップダウンしかありません。仕組みづくりは2つです。ルールをつくること。ルールを守らせること。後者に必要なのはトップダウンです。
そして、ただいま現在、在庫がどれだけあるか見えるようにできても、完成品在庫は減りません。減らす具体策が必要です。
入るを量りて出ずるを制す
お金を扱う世界では、収入を正確に計算してから、それに応じた支出の計画を立てるべしと言われます。出は入で決めるものです。
そうであるなら現場でも入を制すればいいのです。具体的には、製造物量と着手時期を決めるルールです。
・原材料の購入量と発注日のルール
・段取り日時指示ルール
小ロット生産を標榜している先の現場は前者です。原材料は製造ロット毎での使い切りが原則となります。
先の現場にも工程管理担当者はいますが、これまで原材料の購入量と発注日のルールがはっきりしていませんでした。
・原材料発注者が製造部の各製品担当者になっていたのでやり方がばらばらだった。
・欠品や納期遅れが心配で常に前倒し、多めに、早めに、原材料を購入する傾向があった。
そこで、PJを機会として、経営者が方針を出したのです。工場長と工程管理担当者は方針に従い、原材料1ロット当たり購入量計算のやり方、発注日決定のルールを決めました。
判断基準が曖昧だった作業に明確な基準ができました。「欠品や納期遅れが心配で常に前倒し、多めに現場材料を購入する」必要はなくなります。
そして、原材料発注者は一元化したいのですが、それは次のステップで目指すことにしました。今は柔軟性、機動性、小回り性を重視したいので、製造部の各製品担当者が発注するやり方を継続です。全員がルールを守れば問題ありません。
先の現場では、安全在庫を睨みながら、原材料在庫をどこまで圧縮できるか試行錯誤中です。PJ仕上げ段階です。
完成在庫圧縮は原材料在庫から考えるのが一つの手となります。入りと出は繋がっているからです。
PJリーダーを担った工場長は「原材料在庫圧縮」を繰り返し、現場に訴えました。
経営課題は完成在庫の圧縮でしたが、「入るを量りて出ずるを制す」です。原材料購入コントロールがキモになると考えました。
繰り返し耳にすれば、その言葉が自然と頭に浮かぶようになります。それが、全社一体で重視したい要点です。現場での共通言語化が進み、思考回路も一緒になります。
先の現場では、在庫量を気にしながら原材料を発注する意識が高まりました。工場長による繰り返しの言葉が現場の思考回路を変え、経営者が望む判断基準が浸透していったのです。
繰り返し、繰り返し、訴えれば、現場も繰り返し、繰り返し、耳にすることになります。
「これまでも同じようなことを言われたことがあったけれども、今回はこれまでとは違うぞ。」と現場は考えるのです。
現場は経営者と工場長の本気度合いを感じ取ります。言葉に力があるのです。
日本古来の考え方に言霊があります。言葉に思いが乗っかるのです。
経営者の思いが乗っかった言葉が現場の共通用語になればベクトルは揃いやすくなります。指示導線が機能しやすい現場です。
経営者や工場長、経営陣の姿勢を見せることが、意識改革と現場改革の初手と言えます。
「主要製品のリードタイムを短縮したい。」と経営者が現場へ宣言したとたんに実績が出た支援先事例があります。言葉だけで、現場は改善モードに変わったのです。
その事例では、言葉に経営者の必死な思いが乗っかっていました。
経営者は意志や意図を言葉で伝えます。さらには、その言葉を実現させるやり方の提示も大切です。
「売上高30%アップ」「生産性10%アップ」だけでは絵にかいたモチに終わります。
目的をはっきり伝え、目標を日々に小さく区切り、現場を日々の小さな目標達成に没入させるのです。経営者は言動で導きます。
意識改革と現場改革は経営者の思いの乗っかった言葉で始まるのです。
目標を日々に小さく区切って伝えたか?
言いっぱなしになっていないか?
目標を実現させるやり方も教えたか?
軸はブレていないか?
そして、最後はフォローと評価です。これ抜きでは工場経営の本質を満たせません。
・工場経営の本質は他人の力を借りて経営者の想いを実現することにある。
「先生、こちらもスペースが半分ほど空きました。」
先の工場長は、完成品の在庫置き場に続いて、原材料の在庫置き場でも同じように、成果をニコニコしながら説明してくれました。経営者の意志と意図を理解して、工場長が繰り返し語り、現場キーパーソンたちの思考回路を変えた成果に他なりません。
右腕役にも繰り返し、繰り返し、要点を語ってもらうのです。共通言語化が進んで、指示導線が機能しやすくなります。
次は貴社が挑戦する番です!
成長する現場は、経営者の言葉に従って思考回路を変え、経営者の意志や意図を実現させる
衰退する現場は、経営者の言葉が記憶に残らないので従来の思考回路のまま仕事を続ける