「生産性ロードマップ戦略」—儲かる工場経営を目指して—第395話 現場に工程フローを深掘りさせているか?
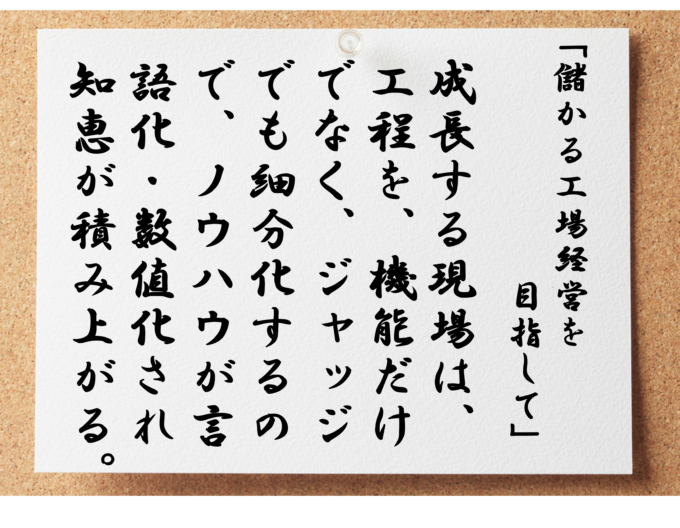
「なるほど自然とやっていますね。」
人時生産性活動に着手して1年になる現場キーパーソンの言葉です。
そのご支援先の経営者はこの現場キーパーソンに、将来の右腕役を期待して、PJリーダーの白羽の矢を立てました。意欲はありますが、管理技術は発展途上。
経営者からは、ベテランとの上手なやり取りの指導をお願いしますとの要望もありました。1年間の取り組みで現場活動の土台ができたところです。
次はベテランが持つノウハウを我が社のノウハウとすることに挑戦です。
既存の工程フロー見直しからやります。優れた技能者の仕事ぶりを観察し、既存の工程フローを強化するのです。
その現場キーパーソンもまだ30代ですが、優れた技能を持っています。自分自身の仕事ぶりを、特定の観点で振り返ってもらいました。
あることに気付いたようです。冒頭の言葉です。
「工程」は下記のように定義されます。出典は生産管理用語辞典です。
・入力を出力に変換する、相互に関連する経営資源および活動のまとまり
・製品又はサービスを作り出す源泉
原材料を加工して価値を生み出します。お客様への価値提供が、商売の基本です。
加工は製造業に限ったものではありません。飲食業も原材料を加工して美味しさを提供しています。また小売業でありながら自社商品製造に携わる事業モデルSPA(製造小売業)も有名です。ユニクロが当てはまります。
原材料を投入して、価値の高い製品やサービスを生み出すプロセスが加工です。そして、このプロセス全体、あるいは全体を構成している個々のプロセスを工程と言います。
製品やサービスを生み出すプロセス全体のスタートは「お客様からの問い合わせ」です。ゴールは「出荷」になります。
特に製造着手から製造完了までが、モノの流れを決めるプロセスです。このプロセスの核となるのが要素技術です。コア技術2本柱のひとつを構成しています。
技術の進化を踏まえ、この要素技術で競合先の追い上げに対抗するのです。貴社の要素技術は何ですか?
そして、工程はこの要素技術単位で設定されることが多いです。
・設備に依存する工程
・作業者に依存する工程
NC旋盤やマシニング、研削機、プレス機、塗装設備等々は前者。組立、溶接(手動による)、仕上げ、手直し等々は後者。
前者、設備に依存する工程では、通常、NC旋盤工程、マシニング工程、研削工程、プレス工程、塗装工程のように設定されます。
多くの場合、工程は機能(要素技術)別で分類されます。入力を出力に変換する機能別です。その結果、設備単位で設定されます。これはこれで問題はありません。普通はこうです。
ただ、もう少し深掘りすることが必要な場合があります。目的は現場の環境整備です。
昨今、多くの現場では、ベテラン従業員から若手への技能伝承が課題となっています。なかなか進まないのです。ご支援先でも、その進捗状況はまだら模様です。
抜群のコミュニケーション力を発揮して上手にやっている現場がある一方、相変わらず属人的でできていない現場もあります。
特に後者の現場では、経営者が早く手を打たなければ、事業の命脈を保てません。ノウハウの言語化、数値化が必要です。
そこで、工程フローを深掘りします。工程を細分化するのです。
従来の機能別に加えて、「ベテラン作業にしかできない作業」と「新人でも手順さえ教えればできる作業」に分類します。言い換えればジャッジ(判断、判定)有無での分類です。
自動車部品工場時代のことです。
現場エンジニアの業務として、金型整備技術の勘所を整理したことがあります。手段は、ベテラン作業者との徹底的なコミュニケーションです。
金型に、セラミック製部品とのはめ合い部位がありました。
一定期間使用後、セラミック製部品を整備して、再度はめ込みます。金型の穴を構成している部位を溶接肉盛りした後、セラミック製部品と現合で最適な穴径を決めるのです。
金型の穴部図面やセラミック製部品図面はあります。ただし、それは金型製作時での寸法です。金型使用後の整備で必要な寸法はそれとは異なります。
現場では、各作業者自身のジャッジ(判断、判定)で対応していました。
整備にあたって、穴部分を溶接肉盛りした後、穴を一定寸法で切削加工するのです。
その後、ベテラン作業者は、空気式研磨機で、金型の穴の内面を軽く舐めるように研磨していきます。
「どこまで研磨するんですか?」
「セラミック製部品がコツコツやって入るまでだね。」
「コツコツって、具体的にはどんな風ですか?」
「セラミック製部品がカタカタと音をたてながらでも、穴の最後まで入ることだね。そして、逆さにしても抜けないことを確認しないとダメ。」
「それじゃ、穴を研磨しすぎると、セラミック製部品が抜け落ちますね。」
「だから、削りすぎないように、少しずつ削らないとダメだね。」
「少しずつって、どのくらいずつですか?」
・・・・・・・
こんな風でした。こうやって整備作業を通じて得られた整備時穴径や初期研磨量を数値化していったのです。暗黙知の形式知化です。現合の言語化、数値化と言い換えられます。
しつこい質問にも気軽に答えてくれるベテランが多かったのが幸いでした。最初は煙たがれましたが、「本物の」職人は心意気を感じてくれたら協力を惜しみません。
(ここで、似非職人には要注意です。似非職人は「本物の」職人とは違います。若手に協力してもらうベテランは見極めが肝要です。)
こうして、当時、金型整備作業を、「ベテラン作業者にしかできない作業」と「新人でも手順さえ教えればできる作業」に分類できました。
技能の優れた作業者は、作業の流れの中で自然とジャッジ(判断、判定)しています。先の現場キーパーソンが口にした冒頭の「なるほど自然とやっていますね。」とはこのことです。
●金型整備作業の既存工程
作業1→作業2→「セラミック製部品はめ合い部整備」→作業4→・・・・
●「セラミック製部品はめ合い部整備」工程の工程細分化
1.金型穴部肉盛り溶接工程
2.1st穴部研磨工程
3.2nd穴部研磨工程
4.セラミック製部品挿入工程
ベテラン作業者が自然とやっているジャッジを基準にして、作業を分類し、それを工程とします。工程も結局は各作業の繋がりで構成されているので、工程細分化をしなくても、作業毎で分類しても同じことです。
ただ、ここでは新たな細分化された工程定義を導入することで、若手の注意を喚起したかったのです。工程をベテランのジャッジ単位まで細分化すれば、新人に暗黙知を形式知として伝えやすくなります。
機能に加えて、ジャッジの有無で工程を分類する目的は、ご支援先現場での環境整備です。「困難は分割せよ。」しばしば言われることです。
工程フローの目的はモノの流れの見える化です。したがって、工程フローの本質から考えれば、加工は機能別で分類されていれば十分です。
ただし、暗黙知を形式知に変換したかったら、工程フローを深掘りしたいのです。工程フローはISOのためではなく、人時生産性を高めるためにあるのです。せっかく作成したのなら、使い倒さないとモッタイナイ。
一見複雑なことも、分解し、判断基準を明らかにすれば理解しやすくなります。さらにそれらを統一した形式の図表で見せればさらに分かりやすいのです。
これは標準化の論点でもあります。
弊社PJでは、現場キーパーソンに暗黙知を形式知に変換するやり方を知ってもらい、そのスキルを磨きます。多くの現場で直面している技能伝承を後押しする具体策のひとつです。
「言語化、数値化できるという言う意味が分かってきました。」とは先の現場キーパーソンの言葉です。
この1年間の試行錯誤でベテランとの言葉のキャッチボールも上手くなっています。上手くなるには訓練しかありません。
指導を受けながら、管理者に欠かせない「具体-中小-具体」の思考スキルを高めるのです。フォローと評価で動機付けします。将来の右腕役を期待されている現場キーパーソンです。
次は貴社が挑戦する番です!
成長する現場は、工程を機能だけでなく、ジャッジでも細分化するので知恵の言語化が進む
衰退する現場は、ノウハウが相変わらず個人の頭の中にあるので属人的なままである