「生産性ロードマップ戦略」—儲かる工場経営を目指して—第428話 段取り回数を増やして出来高を増やせるか?
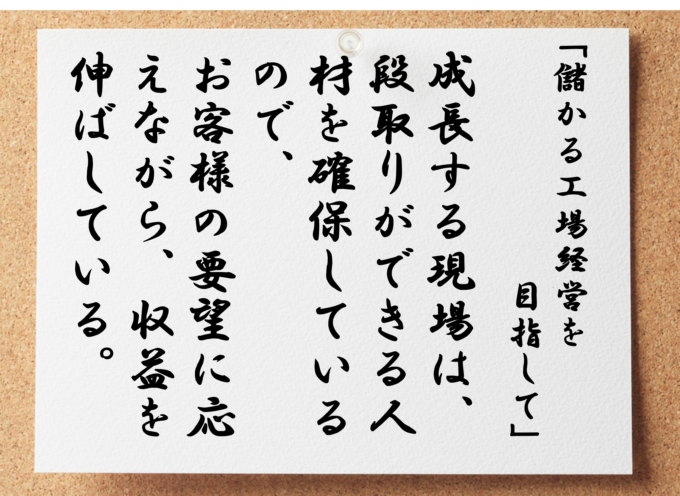
「段取り回数を増やせる体制にした方が出来高を伸ばせるかもしれません。」
40人規模の樹脂成形部品メーカー、ベテラン現場キーパーソンの言葉です。
実践会では人時生産性向上の対応策を議論しています。お客様から届く問合せを全て受注に繋げる体制づくりが課題です。
従業員数はコロナ以降、減少気味です。自己都合で退職する従業員がたびたび出ています。一方、採用活動もしていますが、なかなか応募がありません。従業員確保はそれ自体、重要な経営課題ですが、現場としては残った従業員に焦点を当てます。
従業員数は従来よりも減っていますが、今でも残業を厭わず、会社側の申し出に協力してくれる従業員はいるのです。そうした現場と生産性を高めていきます。
議論のなかで段取りが話題に上がりました。ベテラン現場キーパーソンが10年以上前、先代と一緒に仕事をしていたころの話から出された提案が冒頭の言葉です。
人時生産性向上を実現すると経営者は利益アップと給料アップを手にできます。経営者は事業と従業員の成長を後押しできるわけです。
「仲間と一緒に給料アップ!」を掲げてプロジェクトに汗を流している経営者がいらっしゃいますが、多くの経営者の方々も同じ想いのはずです。
成長の後押しのために4千円台、5千円台を6円千円台、7千円台へ高めます。経営者は我が社の人時生産性を高める論点について熟知していなければなりません。少数精鋭の現場です。改革の手順は的確でなければ現場が疲弊してしまいます。
人時生産性向上の論点のひとつは「詰めて、空けて、取り込む」です。現場は経営者が獲得した仕事を獲り込む体制をつります。
企業が倒産する一番の原因は販売不振です。固定費を回収する分の付加価値額を獲得できなければ市場から撤退せざるを得ません。
その付加価値額の源泉は全て外にあります。経営者の仕事場は外にあるとお伝えしている所以です。売上さえ確保できていれば、現場でどんなすったもんだがあってもなんとかなります。
お客様から届いた注文を取り込むために、詰めて空けるのは現場の仕事です。工数は増やさず出来高を積み上げます。
現場で出来高を増やしたい時、段取り回数を減らし、生産ロットを大きくするものです。この現場も同じでした。
「工数は増やさずにできるだけ生産量を増やしたかったどうしますか?」との問いに答えてくれたのは工程管理担当者です。
「段取りしないで、同じ製品を造り続けます。」
先の現場の段取りでは射出成形金型を入れ替えます。外段取りで予熱を済ませてから、30分ほどの時間を要してプレス機の金型を入れ替えるのです。
立ち上げや条件調整を含めれば、1時間以上の時間が掛かります。その間、生産は止まるのです。したがって、出来高を積み上げるなら段取りはやりたくありません。
製造ロットを大きくすれば、段取りが無い分、出来高は積み上がります。工数を増やさずに出来高を増やしたかったら、段取りをしない工程を組めば良いということになります。
理屈ではそうですが、多品種少量生産を標榜する中小現場で、製造ロットを大きい生産だけをやれるわけはありません。そもそも、それでは柔軟性と言う中小の強みを封印することになります。
負荷時間8時間、段取り時間1回当たり2時間とします。
・段取り0回では稼働時間8時間
・段取り1回では稼働時間6時間
・段取り2回では稼働時間4時間
段取りなしで同一製品を8時間製造できれば出来高を最大化できます。
一方、製品A、製品B、製品C、3種類の製品を製造する場合、段取りは2回です。稼働時間は4時間。段取りにより、多品種対応はできますが、出来高は段取り0回の場合と比べると大幅に減ります。稼働時間が半分です。
多品種少量生産を標榜する中小現場では、段取り0回の製造ロットを設定できる大ロット製品だけでなく、段取り2回程度の製造ロットで設定せざるを得ない小ロット製品が混在しています。
多品種少量生産が中小製造企業の生き残り戦略です。しかし、受注品が全て少量品では辛くなります。規格品で一定期間、一定数量を約束された製品があると収益上、助かるものです。
多品種少量を標榜する経営者も、付加価値額率が小さくても安定した付加価値額積み上げができる規格品が欲しくなります。その結果、多品種少量生産であっても、実際は大ロット製品の合間を縫うように小ロット製品が生産されることが多いのです。
大ロットと小ロットが混在する工程管理で出来高を増やすカギは「段取り」です。品種切り替えをサクサクできれば出来高を増やせます。
先のベテラン現場キーパーソンが先代と一緒に仕事をしていた時、段取り作業ができる作業者は3人いました。当時の現場は15人規模です。作業者5人に1人は段取りができます。
昼でも夜でも(この職場は昼夜2交代)段取り作業をこなせる従業員がいたので、工程管理者からの指示にしたがって、いつでも、直ぐに、短時間で品種切り替えができました。
・いつでもできる
・直ぐにできる
・短時間でできる
この3つが出来高を増やすのに貢献します。
段取りをいつでも、直ぐに、短時間でできる体制があれば、工程管理担当者はお客様の多様な要求に応える日程計画を組めるのです。
・小ロットの要求
・突発、特急の割り込み要求
今の現場で段取りができるのは、先のベテラン現場キーパーソン、1人です。それも昼の時間帯のみです。お客様から小ロットの問い合わせがあっても、品種切り替え作業回数に制約があります。
それが原因で失注することが度々あるようです。ちりも積もれば山となる。1件あたりの収益は小さくても、こうした状況が常態化すれば目に見えて、収益は伸び悩みます。一度離れたお客様は戻ってきません。
さらに、お客様の突発、特急の割り込みに応えたくても、品種切り替え作業回数に制約があると、そうできません。柔軟性を発揮できないのです。
また、品質切り替え作業回数に制約がある中で、お客様からのムリな要望に応えるため、ロットの大きい製品の生産を一旦止めて、そこへ割り込ませることもあります。
せっかくロットを大きくして効率を高めた生産をできるようにしたのにその効果が薄れるのです。現場も混乱します。混乱する現場は儲かりません。
先のベテラン現場キーパーソンは、「段取り回数を増やせる体制にした方が出来高を伸ばせるかもしれません。」と言いました。
そのコメントの趣旨は、下記です。
・お客様の多様な要望に応えるには段取り回数を増やす必要がある。
・段取回数を増やせる体制に変えれば、お客様の要望に全て対応できる。
・お客様の要望に対応できれば、その結果、出来高を増やせる。
品種切り替え作業回数に制約があるので、受注案件数を伸ばせなかったという事実を関係者で理解できました。
この現場では、段取り作業ができる従業員を増やすことが課題となります。従業員が減る中、骨の折れる仕事になりそうです。
作業者の協力を仰ぎながら全社一丸で、そうした人材を育成します。計画表、フォローと評価が成功のカギです。
さらに段取り時間短縮も加えれば、効果は倍増します。トヨタ生産方式におけるシングル段取りの考え方です。
次は貴社が挑戦する番です!
成長する現場は、段取りができる人材を確保しているのでお客様の要望に応え収益を伸ばす
成長する現場は、段取りができる人材が減ってもそのままなので失注が増え収益が伸びない