「生産性ロードマップ戦略」—儲かる工場経営を目指して—第427話 ストレス解消のために手待ちを撲滅しているか?
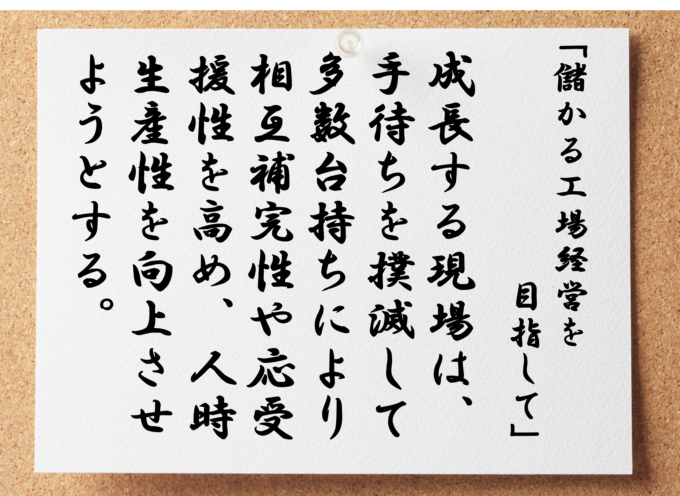
「安全のためにはどうしようもないのでは・・・」
支援先の部品メーカー現場で、人時生産性を高める方法をメンバーと議論していました。塑性加工、プレス工程です。作業手順を確認します。論点は「手待ち」の有無です。
作業者は材料をプレス機にセットしてから、起動ボタンを押します。挟まれ防止のための「両手押し」です。安全面で欠かせない対応となります。
さて、今の論点は「手待ち」の有無です。
起動ボタンを両手で押したら、プレス型が下降し始めるわけですが、プレス型がある位置に下降するまで、両手押しのままです。手の挟まれ防止のためです。
その時間5秒。作業者はその間、動作を拘束されます。
「これも手待ちですね。」と問いかけました。動作の拘束は価値を生み出さないからです。メンバーの1人から冒頭の言葉が返ってきました。
中小製造現場は少数精鋭です。その中小現場の目指す姿があります。
マスカスタマイゼーションです。
多品種少量の製品群を大量生産のコストで生産します。お客様の要望に応えながら、一方で安く造る工夫もするのです。
大手に勝つには価格競争を回避しなければなりません。「大手と同じこと」をやっても儲かりません。大手が嫌がることをやります。
それがお客様の要望に応える多品種少量生産体制です。
現場には柔軟性、機動性、小回り性が求められます。大手は嫌がり、真似し難いです。そして、その原動力は「人」です。
「人」が柔軟性、機動性、小回り性の原動力です。
手順書で仕事のやり方は決められています。ただし、多品種対応では、臨機応変さも必要です。お客様の要望に応える多品種製品の全手順を決めることは実際のところ、できません。作業者に最適手順化を補ってもらうこともしばしばです。「人」だから柔軟性があります。
中小の現場での機械化、設備化、自動化、無人化は大事です。ただ、大手と同じような設備投資をやっても、大手に勝てるわけがないことに注意を要します。中小での設備投資は「人」を活かすことに要点を置きたいのです。
「人」が柔軟性、機動性、小回り性の原動力です。
だから、経営者は作業者には仕事のやり易い環境を整備します。それが「手待ち」の撲滅です。作業者の能力(レイバーアワー)を最大限に活かせば、人時生産性を高められます。
生産現場の能力はマシンアワーあるいはレイバーアワーで表せます。「人」の能力はレイバーアワーです。その能力を楽に、早く、正しく発揮できるようにします。
「手待ち」の撲滅は論点のひとつです。手待ちの具体例には下記があります。
・組立工程で部品が供給されないので作業を止めて待っている
・前工程のプレス工程から材料が届かないのでベンダー作業を止めて待っている
・機械が自動で加工している間、そばで機械を監視している
「人」は付加価値を生み出せていません。
上記の「手待ち状態は楽だ」と考える現場がありますが、誤りです。
4階層の指示導線が機能している現場では、逆に、こうした状況はストレスになります。リズムよく仕事をこなせないからです。
トップダウンの職場では、作業者は、経営者が日頃から作業者に何を期待しているのかを知っています。それにも関わらず、作業者は積み上げの機会を奪われているのです。達成感もありません。モヤモヤします。
「手待ち」は人時性生産性向上の阻害要因です。
先のプレス機の両手押しも、いわゆる「手待ち」です。
作業者は、ぼーっとしているわけではありません。ただ、次の動作ができず「拘束」されています。両手押しをしている5秒間、作業者は価値を生み出す仕事ができません。
ぼーっとしているわけではないのですが、「手待ち」と考えます。
安全面は安全面で違う観点で考えればいいのです。
例えば、材料をプレス機にセットした後、プレス機の前を離れ、離れた場所にある稼働スイッチをワンタッチで押す構成にすれば、挟まれ防止という安全面への対応もできます。
光電管でのエリアセンシングやセットされた材料の位置ずれ防止など、そのための付帯的な技術課題はあります。できない理由はいくらでもあるわけで、要は人時生産性向上を貪欲に追いかける経営者の姿勢次第ということです。
30秒/回のプレス作業を想定します。そのうち起動ボタン両手押しのため作業者は5秒間拘束されるとします。1分間で2回プレスできるので、拘束されるのは1分間で10秒です。
設備を8時間稼働させる場合、8時間=480分なので、作業者は両手押しのために4,800秒=80分の時間、「手待ち」しています。8時間稼働のうち、1時間半近くも「手待ち」していることを知った経営者は、何か手を打つはずです。
「手待ち」を撲滅してレイバーアワーを最大限、活かします。作業者はリズムよく作業ができるのでストレスを感じることなく、積み上げ達成感を味わうこともできるのです。
弊社ご支援先の現場にはこのあたりの達成感を数値化で感じさせているところがいくつかあります。そうした現場では「手待ち」はストレスです。「手待ち」は、人時生産性向上の阻害要因と解釈しています。
工場管理がこの水準に至れば、経営者は内の仕事を右腕役や現場キーパーソンへ任せられるのです。現場はそうしたことを全て分かっています。
上記の事例で確認した80分の「手待ち」は、それを解消した後も大事です。
生み出された時間をどう生かすのか?
例えばワンタッチで押す構成を導入したとしても、それだけでは80分の「手待ち」は文字通り、「手待ち」になるだけです。そこで、多台持ちや多工程持ちへ移行します。チームで実践する多台持ちや多工程持ちが効果的です。
現場の応受援性や相互補完性も高まります。応受援性や相互補完性は現場力強化の要点です。その結果、人時生産性が向上します。
多台持ちや多工程持ちもレイバーアワーを最大限に活かす手段です。「手待ち」なく、リズムよく作業ができるようにします。
この時、レイバーアワーは活かされますが、機械の稼働率が落ちるかもしれません。ただ、人時生産性を計算すると高まっていることがほとんどです。
・作業者1人が1台持ちで1台の設備に張り付き、設備をオペレーションする場合
・作業者1人が2台の多台持ちで、一定のリズムで「手待ち」なくオペレーションする場合
後者では、設備の稼働率は落ちますが、人時生産性は高くなるはずです。設備が少々、止まっても気にしません。設備稼働率よりも、レイバーアワー最大限活用ということです。
これはコスト面からも理にかなっています。収益の固変分解をすれば明らかです。
・1時間当たりの人件費および労務費
・1時間当たりの設備費
貴社での両者を比べてください。経営者の方針がはっきりします。
次は貴社が挑戦する番です!
成長する現場は、手待ちを撲滅して多数台持ちにより応受援性を高め、生産性を向上させる
衰退する現場は、手待ちを現場の余裕と考えるのでそれが放置され生産性は横ばいである