「生産性ロードマップ戦略」—儲かる工場経営を目指して—第51話 本来の正味作業時間を把握し超短納期へ踏み出す
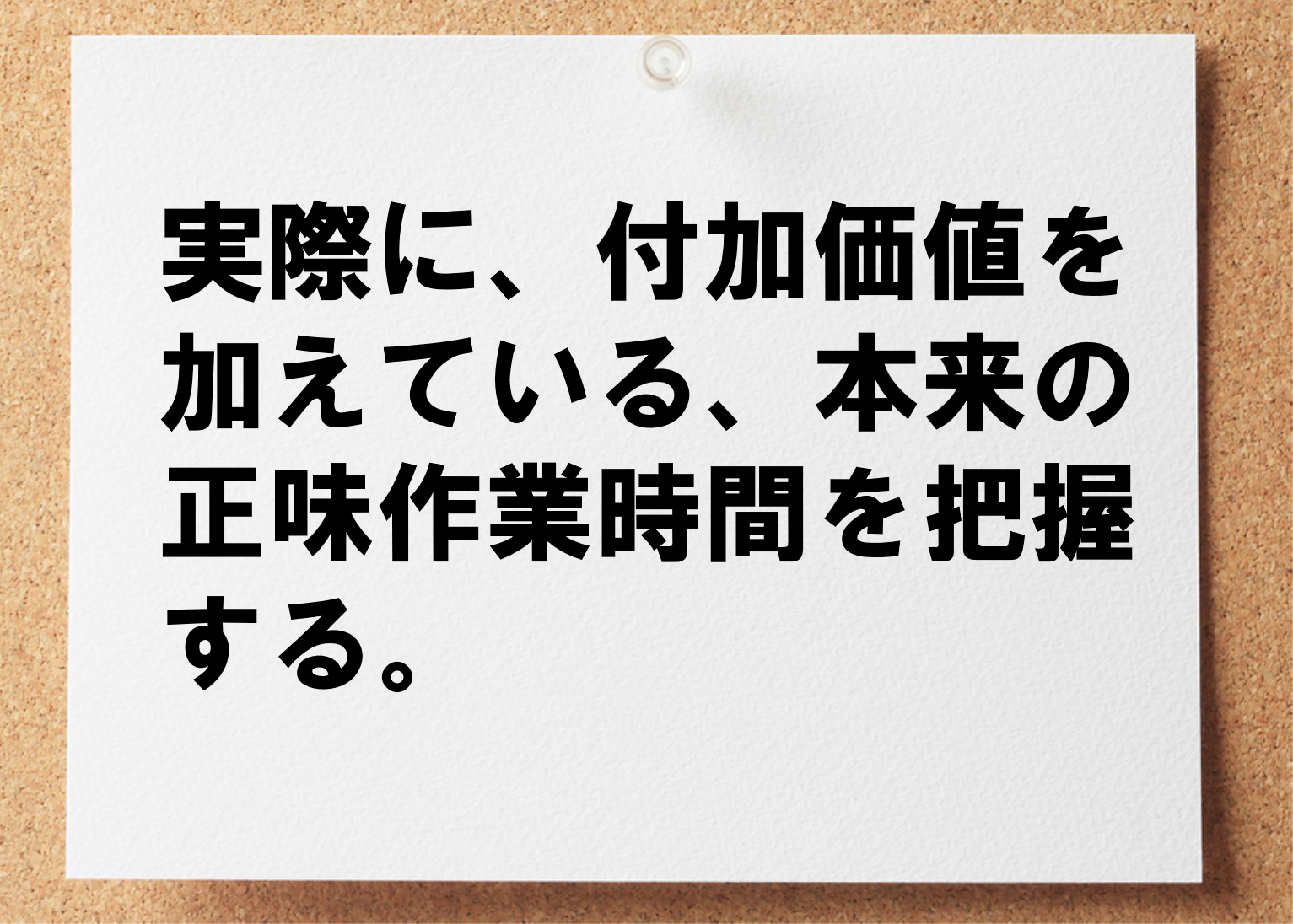
現場は「本来の」正味作業時間を把握しているでしょうか?
生産リードタイム短縮は、高付加価値化のカギとなります。
超短納期は、中小製造企業が取り組みたいモノづくり戦略のひとつです。
現場の実働時間は、直接作業時間と間接作業時間からなります。
さらに、直接作業時間は主体作業時間と準備段取り時間から構成されています。
主体作業こそが、素材へ付加価値を加えている作業です。
正味作業時間と余裕時間からなっています。
そして、生産リードタイムを短縮したかったら、やるべきことは2つです。
1)付加価値を加える作業を高速にする。
2)付加価値を加えない作業を除去する。
ここで、マシニングでの切削加工を想定します。
直接作業は2つから構成されています。
・マシニングをオペレートして、素材を加工する一連の作業(主体作業)
・品種切り替えの段取り替え作業(準備段取り)
したがって、間接作業を短くすることは当然として、段取り替え作業の短縮化が課題です
付加価値を加えない作業は除去します。
多品種化へ対応するためにも、外せない論点です。
そして、正味の作業を対象にした、作業の効率化を図ります。
付加価値を加える作業の高効率化です。
今後、超短納期を目指す経営者は、常に、この視点を持つ必要があります。
限りある経営資源の投資効率を上げるには、実働時間に占める正味作業時間の割合を増やす必要があるからです。
現場では、品種切替えの段取り作業を終えたら、正味の作業へ移行します。
正味の作業となる加工作業の時系列は、以下です。
1.素材をマシンへセットする。
2.自動ボタンを押す。
3.ツールが選択され、バイトが素材の位置へ移動する。
4.切削加工
5.バイトが所定の位置に戻る。
6.自動運転が終了する。
7.加工品を外す。
作業全体で、付加価値を加える工程であることには、違いはありません。
したがって、これらの一連の作業の累計時間が正味作業時間です。
しかし、ここで、「本来の」正味時間は、もっと短いとも考えられます。
加工工程を、情報の「転写」の視点から見るのです。
顧客へ届けたい情報を素材に「転写」している時間こそが「本来の」正味作業時間。
すると、上記の時系列では、4項のみが、「本来の」正味作業時間と言えます。
チップが素材に触れ、素材が削られている時間帯です。
機械加工の管理者をやっていたとき、現場リーダーに、この「本来の」正味作業時間を調査してもらったことがあります。
主に特注品対応の現場だったので、複数の受注品に着目して調査しました。
結果の数値を見て、現場リーダーが一言。
「実際に加工している加工時間が、こんなに少ないとは思いもしていませんでした!」
実働時間1日7時間で、情報の転写時間に相当する「本来の」正味作業時間は30分程度でした。
のべで、1時間もありませんでした。
420分の持ち時間のうち、素材に付加価値を加えていたのほ30分程度だということです。
決して現場が、怠けていたわけではありません。
長年、やってきた仕事の仕方が、普通だと考えていただけです。
「本来の」正味作業時間は、意外と少ないことに気付きます。
現場の、この気付きが大切なのです。
超短納期を目指すなら、とにかく、この本来の正味作業時間以外を除くことです。
転写の速度を上げる、つまり切削速度を上げるのは、技術的な壁もあります。
切削加工時間を短くするのは、難しいです。
しかし、「本来の」正味作業時間以外を除くことは、まだまだ、できるはずです。
黄現場でも、改善の余地は、大きいのでは、ないでしょうか?
生産リードタイムの短縮は、これから積極的に進めたいテーマです。
実働時間のうちの、直接作業時間に注目し、まずは、付加価値を加えない作業を除去し、付加価値を加える正味の作業の効率を高めます。
そして、これから、さらに一歩踏み込みます。
情報の転写の視点で、「本来の」正味作業時間を把握するのです。
そして、現場には、まだまだ、改善の余地があることに気付いてもらいます。
数値で実感すれば、現場も、改善活動の必然性を感じるのです。
数値に語らせます。
超短納期への第一歩目です。
実際に付加価値を加えている、本来の正味作業時間を把握する仕組みを作りませんか?