「生産性ロードマップ戦略」—儲かる工場経営を目指して—第98話 少数精鋭で展開する品質活動
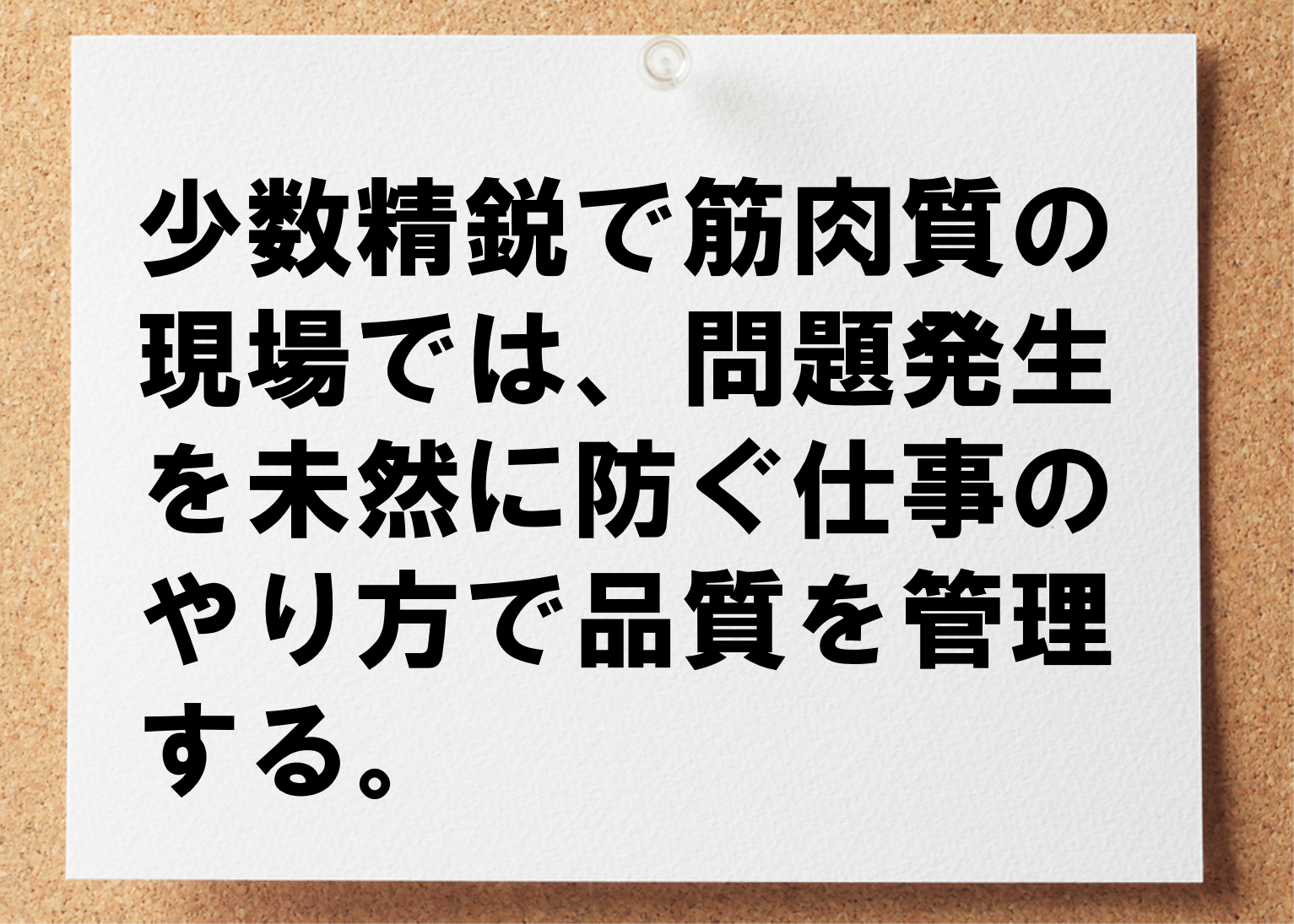
大手と同じような品質活動を展開しようとしていませんか?
品質原価という考え方があります。
「予防コスト+検査コスト」と「失敗コスト」はトレードオフです。
「失敗コスト」には内部失敗コストと外部失敗コストがあります。
製品をお釈迦にしてしまって発生するロスや手直で良品へ復活させた費用など、”良品ではない”モノが原因で発生したコストが内部失敗コストです。
対象は社内です。
余分なコストが発生しますが、まだ、直接的に顧客へ迷惑は掛けていません。
一方、外部失敗コストは、対象が社外です。
”良品ではない”モノが社外へ流出しています。
人を客先へ派遣して、選別作業をやらねければならないでしょう。
当然、代替品を急いで準備して、届けなければなりません。
原因究明と対策実施のために工数を割く必要もあります。
”良品ではない”モノの社外流出発生コストが外部失敗コストです。
これはマイナスから正常状態へ“戻す”ためだけの費用となりますから、これをどんな積み上げても、原則、価値を生み出しません。
コストを掛ける意義を感じることのない、いわゆる“モッタイナイ”費用です。
ですから、この失敗コストを最小化したいと考えていない経営者はいません。
したがって、生産管理3本柱のひとつ、品質を対象にした管理活動、品質管理も強化したくなり、品質を専門とするチームを設置できたら・・・・となるのは当然のことです。
昨今、大手メーカーの品質問題から感じるのは”主体性”と”客観性”のバランスの悪さです。
自ら製造し、自ら品質の可否を判断できるのが理想ですが、実際問題、納期に追われがちな現場に全てを任せるのは酷というモノではないでしょうか?
主体性を重んじつつ、第三者が客観的に判断し、双方でその判定を尊重する土壌づくりが欠かせません。
品質活動では、主体性と客観性のバランスを重視したいと言う所以です。
多品種少量化で、求められる仕様もますます複雑化していくなか、品質を客観的に判断するチームが欲しくなります。
品質管理や品質保証の部門があればなぁと考える経営者も少なくはないでしょう。
しかし、人的資源に制限のある中小の現場で、そうした部門を抱える余力がないところも多いです。
モノづくり体制を優先させなければならない現場がほとんどであり、間接部門に人的資源を割けるところは稀です。
しかし、顧客は当然のように品質も期待しています。
少人数でどのように品質活動を展開すべきかお悩みの経営者も多いのではないでしょうか?
せっかく現場が稼いだ付加価値額を、みすみす失敗コストとして流出させるのは癪です。
そこで改めて、考えたいのが品質原価という考え方になります。
失敗コストの流出を減らしたかったら、「予防コスト+検査コスト」に注目して下さい。
さて、安全と品質の2つはモノづくりの前提条件であり、空気のようなものではないでしょうか?
あって当たり前、ですから普段はそれほど話題にはあがりません。
しかし、一端問題が発生したらどうでしょうか?
全てに優先して、現状復帰と対応策の検討をしなければならなくなります。
顧客に対して、公的機関に対して、やらねばならないことが出てきますね。
このときは、生産性もへったくれもありません。
四の五の言わずにやらなければならないのです。
安全と品質とはそのような類のものです。
弊社の事業の2本柱は「生産性向上」と「人材育成」ですが、どちらにおいても、”品質”の位置付けは小さくありません。
「人材育成」においては言わずもがな、「生産性向上」では主に生産の流れに着目し、リードタイムに焦点を当てていますが、品質も外せない論点です。
ですから、弊社の生産性ロードマップ戦略プログラムでは”品質”も扱います。
生産の流れをつくるなかで、品質への対応を無理なくできる仕組みを組み込みたいと考えているからです。
セミナーやコンサルティングの中でお話することですが、こうした考え方に至った出来事があります。
10人規模の自動車部品を製造する職場でクレームを発生させてしまったことです。
小さな部品でしたが、数万という多くの製品を選別しなければならな状況になってしまいました。
今、思い出しても、胃のあたりがきゅ~っとします。
その現場には、品質管理の仕組み、体制が皆無でした。
したがって、クレーム発生後の対応も、後手後手となってしまったのです。
2度とこんな辛い状況にはなりたくないと、現場も考えたこともあって、品質管理の仕組みを新たに導入しました。
雨降って地固まる、品質に全員で取り組もうという雰囲気が生まれたのです。
ただし、このときに配慮しなければならなかったことがあります。
その職場の規模です。
その職場は10人規模の職場でした。いわゆる、教科書に書いてあるような大掛かりな品質管理体制を敷くことは望むべくもありません。
少人数で継続できる仕組みとしなければなりません。
そこで、導入したのが品質原価の考え方でした。
失敗コストを最小化するために、「検査コスト+予防コスト」に着目します。
さらに、少人数ということだったので、検査コストよりも予防コストに焦点を当てました。
・不良を流出させない
・不良を造らない
この2つのうち、後者に重点を置いたのです。
不良を造らない観点、予防コストの対象は複数ありますが、その現場で定着して効果があったのは、工程能力管理と工程変更管理の2点でした。
弊社のコンサルティングでも現場にあった手段を現場の皆さんと考えながら選択します。
中小の製造現場を専門としている弊社としても、経営者に品質への不安をとり除いていただくことは重要な仕事と考えています。
生産性向上は安全と品質の上に成り立っているとも言えます。
地味ですが、しっかり取り組まなければならないテーマです。
「現場が小規模で品質管理の体制を構築することに苦労しています。」
このように相談される経営者がいらっしゃいます。
そこで、弊社では「小規模でもしっかりやれる方法があります。」とお答えしています。
品質原価の考え方は少数精鋭で筋肉質の現場にはぴったりの方法です。
少数精鋭で筋肉質の現場では、ひとりひとりのやる気がカギとなります。
問題が発生してから対応する仕事のやり方
問題は未然に防ぐものとする仕事のやり方
どちらが現場のやる気が引き出しやすいでしょうか?
前者ではマイナスからのスタートとなり、現状に引き戻すためのエネルギーが膨大です。
後者は先手です。
有能性を感じるのは明らかに後者ではないでしょうか?
事を起こさない体制はどんどん強化できます。
未然に防ぐ仕組みづくりでは強化されていく”型”を成果と感じ、有能性につながるのです。
”型”があれば、問題が起きても、直すべきものがはっきりしています。
問題を発生させた原因究明で個人攻撃をする暇があったら、前向きに、皆で”型”を壊して、作り変えればいいのです。
先手を打つ仕事のやり方で、スマートに仕事を進める環境整備が進みます。
現場の一体化を重視する弊社としては後者の考え方によっています。
そもそも不良を作らないことに知恵を絞るのです。
少数精鋭で筋肉質の現場ではひとり一人のやる気を引き出すことに焦点を当てます。
そうするとやるべきことも見えてくるのです。
品質原価の考え方を現場へ導入しませんか?