「生産性ロードマップ戦略」—儲かる工場経営を目指して—第236話 現場が腹落ちするパフォーマンス評価のやり方は?
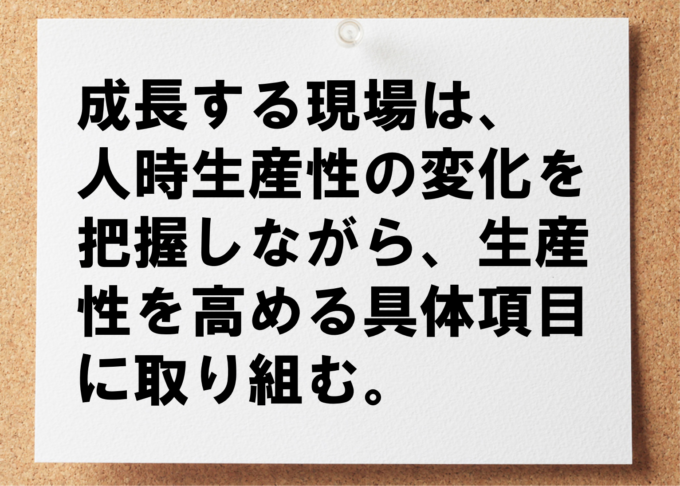
「各工程の損益を見えるようにしました。」
昨年年末からプロジェクトに着手した中堅部品製造企業経営者の言葉です。
工程間連携を促して、工場全体の生産性を高めたいと考えています。工程の収益状況を知れば、現場も自発的に動きたくなるはずです。
隣の工程は黒字なのに、自分の工程は赤字だ!なんとかしなければ・・・。比べられれば頑張りたくなるのが現場です。
そこで、せっかく工程別損益を評価したのですから、工程別で人時生産性の変化も評価してはどうですか?と提案しました。収益と現場活動をつなげる数値が人時生産性だからです。
それと、もうひとつ別の理由もあります。
複数の工場、複数の工程、これらのパフォーマンスを損益で比べるやり方があります。必要な数値は各工場、各工程の固定費と付加価値額。赤字なのか?黒字なのか?赤字ならどの程度の水準なのか?各工場、各工程で比較します。
ただし、評価される工場、工程の立場で考えると、このやり方には、ちょっと引っかかることもあるのです。
1.生産活動と直接には関係ない費用を固定費に配賦される
2.製品の付加価値額を貢献度で配分される
1.「生産活動と直接には関係ない費用を固定費に配賦される」の検証
仕事の「型」が整備され、会社が成長段階に至ると、「本社」機能を担うチームが必要になってきます。全体最適化のためです。そして、そのコストは各工場、各工程へ配賦されます。
配賦基準はいろいろです。人員数規模、売上高規模、付加価値額規模・・・。理屈は理解できますが、各工場、各工程の責任者は複雑な気持ちになります。
「ウチのコストでないのに、なぜ、ウチが負担しなければならないのだ。」
前職の工場でも同様のことがありました。工場外の管理費用が売上高の7~8%程度です。当時、営業利益ベースの利益率は5%前後でした。二桁をめざしていたときです。
「この費用さえなければ達成するのに」という状況がしばしばありました。理屈では分かっていても、どうしても納得感が得られません。
配賦基準の是非を議論しても、結論は出ないと感じたことを憶えています。
2.「製品の付加価値額を貢献度で配分される」の検証
製品1個当たり付加価値額は簡単に求められます。「単価-@外注費-@材料費」。現場もこの評価に異論はありません。
そして、その付加価値額を各工程の貢献度によって配分したかったら何を基準にしますか?
頭に浮かぶのは、各工程で投入された工数です。実際このようにやっている現場もあります。客観的です。見積もりの構造から考えると自然かもしれません。
レートと工数を乗じて固定費回収分が算出されます。つまり、概ね工数に比例した規模で固定費を回収できるのです。この辺りの考え方は貴社も同じでしょう。
ただし「工数の多い方が儲かるの?」という誤解に注意です。
機械化、自動化、無人化が進む製造現場は高度化、複雑化しています。各工程が生み出す付加価値額を工数のみで評価するのは難しくなってきました。投入工数が多いから儲かる訳ではありません。
複数の工場、複数の工程の損益を精度良く比較しようとすると、上記の論点を解決する必要があります。
やり方自体に根拠はありますが、評価される側としては、今ひとつ腹落ちしないません。現場がコントロールできない要素を含んでいるからです。ここが論点になります。
1.生産活動と直接には関係ない費用を固定費へ配賦するやり方では、「製造活動と直接には関係がないのに割り振られるコストの存在」が問題になります。
2.製品の付加価値額を配分するやり方では、「工数だけでは貢献度は評価できないこと」が問題となります。
この2つを議論しても埒はあきません。特に前者はそうです。したがって、各工場、各工程のパフォーマンスを収益の絶対値で比較するのは、そもそも難しいです。
各工場、各工程でコントロールできない要因が含まれています。腹落ちできない気持ちを引きずります。ではどうするか?
各工場、各工程のパフォーマンスは「人時生産性の変化」で評価したいです。
・固定費は無関係です。
・経営者が定義した付加価値額と工数で評価します。
製品毎に、経営者が下記の2つを設定します。
・工程別@付加価値額
儲かる見積もりの構造は@変動費+@固定費+@技術料です。したがって、見積もりで設定される@付加価値額は@固定費+@技術料。そして@固定費=Σ(レート×工数)になります。工数と@技術料で評価したいです。
・工程別工数
段取り+実作業の定義を明確にしたいです。
これらの数値は、概ね、自工場、自工程でコントロールできます。コントロールできる範疇で比べられれば、現場も腹落ちします。
そして、時系列で人時性生産性を追うのです。「変化」が見えてきます。「絶対値」ではなく「変化」に注目です。比較の対象は自らの過去実績です。
現場には、実績対比で人時生産性を高める思考回路を持ってもらいます。人時生産性を高めるには、リードタイムを短縮する、品質を高める、内製率を高める・・・。取り組むべき具体項目を思い浮かべるためです。収益だけを問われても見えてきません。
したがって、もし各工場、各工程を比較したかったら、絶対値の多寡ではなく、変化の多寡を比べます。先の企業でも工程別の損益に加えて、人時生産性の変化を追うことにしました。
ただ、今のまま数値だけを設定しても効果はありません。その前にやらなければならないことがあります。ベクトル揃えです。こちらの方が重要であることを経営者は知っています。
闇雲に数値を振り回しても失敗するだけです。手順があります。
次は貴社の番です!
成長する現場は、人時生産性の変化を把握しながら、生産性を高める具体項目に取り組む。
停滞する現場は、損益だけを問われ、収益向上の具体項目が浮かばないので変わらない。