「生産性ロードマップ戦略」—儲かる工場経営を目指して—第367話 管理された在庫は武器になることを現場は知っているか?
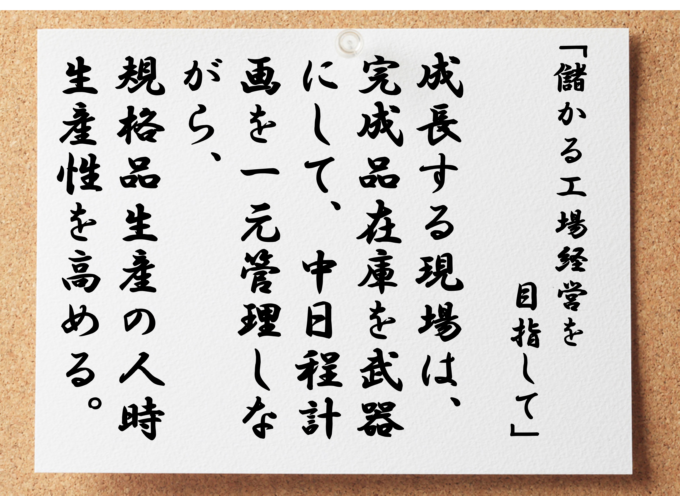
「造りすぎることがあります。」
30人規模自動車部品メーカー工場長の言葉です。
日程計画導入準備に着手しました。
規格品受注生産現場です。今、問題点を整理しています。
主要なお客様から毎週金曜日の夕方に届く向こう3か月間情報をもとに日程計画を立てるのですが、この時点ですでに問題があるようです。
現場は前工程と後工程で構成されており、前工程作業者は製品を割り当てられています。前工程作業者が製造するのは自分が担当している製品です。
そして、日程計画はこの前工程作業者が各自で決めています。
毎週届くお客様情報に基づいて、前工程作業者が、製造着手日、製造数を納期から逆算して決めているのです。そうしたやり方でやってきましたが、以前から問題として認識していることがあります。冒頭の言葉です。
一元管理されていないことが原因のひとつと思われます。
日程計画では、大日程計画、中日程計画、小日程計画の3つを使い分けます。付加価値額積み上げ最大化が目的です。
・目前の仕事をこなした結果、付加価値額が積み上がった。
・見通しを立て、不足分を認識して仕事を獲りに行った結果、付加価値額が積み上がった。
結果として、同じ規模の付加価値額が積み上がったとしても、両者の状況は、全く違っているのは明らかです。
後者には経営者の意志や意図が反映されています。一方、前者はそれがありません。たまたまです。市場が変化して行き詰ったときの対応に大きな差が現れます。
仕事が安定して届くようなGDP右肩上がり時代なら経営者はコスト削減だけを意識していれば、ある程度は儲かります。
しかし、今、GDP横ばい時代。生産性もグローバルで劣後しています。経営者が、市場に向き合わず、働きかけないと我が社はジリ貧です。
削減の時代から積み上げの時代へ。
大日程計画をロードマップで明らかにします。
お客様の要望に応えながら、効率よく製造する日程を考えるために整理したものが中日程計画と小日程計画です。
「お客様の要望に応えること」と「我が社が効率よく製造すること」とは相反します。お客様の要望に応えると現場は多くの場合、混乱するからです。
・お客様は小ロットで作って欲しいと考えるが現場はロットを大きくして造りたい。
・お客様は日程変更や突発にも柔軟に対応して欲しいと考えるが現場は自分たちのペースで造りたい。
相反する両者の落としどころを見つけるのが中日程計画であり、そこから小日程計画がつくられます。
中日程計画ではお客様から届く情報に基づいて、製造数と製造着手日、原材料数量と原材料発注日を決めるのです。要点は製造時間枠の確保です。
突発、特急、変更があれば、中日程で確保した時間枠を絶妙に変更調整します。
日程計画では一元管理を目指します。
製販一体に関わる情報をキーパーソンに集め、そこで製造数と製造着手日、原材料数量と原材料発注日の決定をします。全体最適化された中日程計画をつくるための一元管理です。
先の企業では前工程作業者が担当する製品の日程計画を立てていました。部分最適化はされています。しかし、全体最適化、つまり工場全体として生産性MAXか否かは不明です。
全体を見通している人がいません。
作業者は納期遵守の重要性を理解しています。欠品だけは避けなければならないと考えるのは普通です。
加えて、扱っているのは規格品です。少々造りすぎても近い将来出荷されます。ルールがなければ、少々、多めに製造した方が無難と考えるでしょう。
決められた判断基準がなければそうなります。
前工程作業者の思考回路から、生産性とか適正在庫量の観点が抜けていても責められないのです。これから、中日程計画一元管理の仕組みをつくることになります。
また工場長には我が社の生産形態を生産性向上に活かす視点も必要です。
規格品受注生産は上手にオペレーションすれば効率を高められます。繰り返し製造する商品、製品を扱っているからです。
一見さんのお客様による特注品生産は一回限りの製造です。
設定された生産数があります。お客様からの要求が5台なのに、我が社が効率よく製造するなら10台が好都合だからと言って10台製造するわけにはいきません。
ロスが発生しても5台製造で計画を立てます。6台以上製造してもそれらは売れません。
その点、規格品生産では完成品在庫を持てます。
サイクル在庫に加えて、安全在庫を設定すれば日程計画の自由度が高まるのです。
サイクル在庫のみでは、在庫が切れるころに合わせて製造着手日を設定しなければなりません。事前に設定した製造着手日の前後に突発や特急、変更があるとすったもんだします。
ここに一定水準の安全在庫を設定すれば、それがバッファとなり、設定した製造着手日の柔軟性を高められます。
さらに、安全在庫の水準を1か月分バッファ規模にすれば、今月分の製造着手日は原則、いつでもOKとなります。
「我が社が効率よく製造すること」を判断基準に日程計画を組めるのです。
棚卸資産は運転資金に影響します。肥大した在庫はロスです。しかし、製造活動の自由度や柔軟性を高める管理された在庫は武器になります。
・製造数=出荷数
・製造数≠出荷数
毎月の製造数で上記のような設定も自由です。規格品生産ならではの戦術となります。全ては「我が社が効率よく製造する」ためです。
お客様の要望に応えることが私たちの使命ですが、使命を果たすためには、我が社は儲かる必要があります。
「規格品生産の特徴をもっと知って仕事をしやすくしたいです。」とは先の工場長の言葉。
「造りすぎ」を「計画的な在庫の積み上げ」へ変えます。規格品生産を活かした現場に変えるのです。管理された在庫は武器になります。
先の工場長は、他社の事例を知って、新たな知識を我が社へ取り入れています。仕事のやり方を変えたいからです。
意欲的な幹部は聞く力を持っています。改革意欲も強いので仕事がドンドン進むのです。意欲的な幹部は学びを辞めません。
他社事例を紹介しても、「ウチの業界は他とは違って・・」と言っている幹部に率いられた現場は取り残されます。
多くの事例を知っている弊社がなぜその事例をその企業へ伝えるのか?やれば効果があると判断するからです。客観的判断です。
新たな知識を取り入れることに慣れていない幹部に鍛えて欲しい力があります。
客観的判断を咀嚼する力。
知識を現場の血や肉に変えるためです。日頃から感じることですが、訓練すれば高められる力でありスキルです。
貴社の幹部はどうですか?
次は貴社が挑戦する番です!
成長する現場は、在庫を武器に、中日程計画の一元管理化で規格品生産の人時を高める
衰退する現場は、規格生産でも属人的なやり方に留まり一元管理ができず人時は伸びない