「生産性ロードマップ戦略」—儲かる工場経営を目指して—第108話 継続性に焦点を当てた品質管理
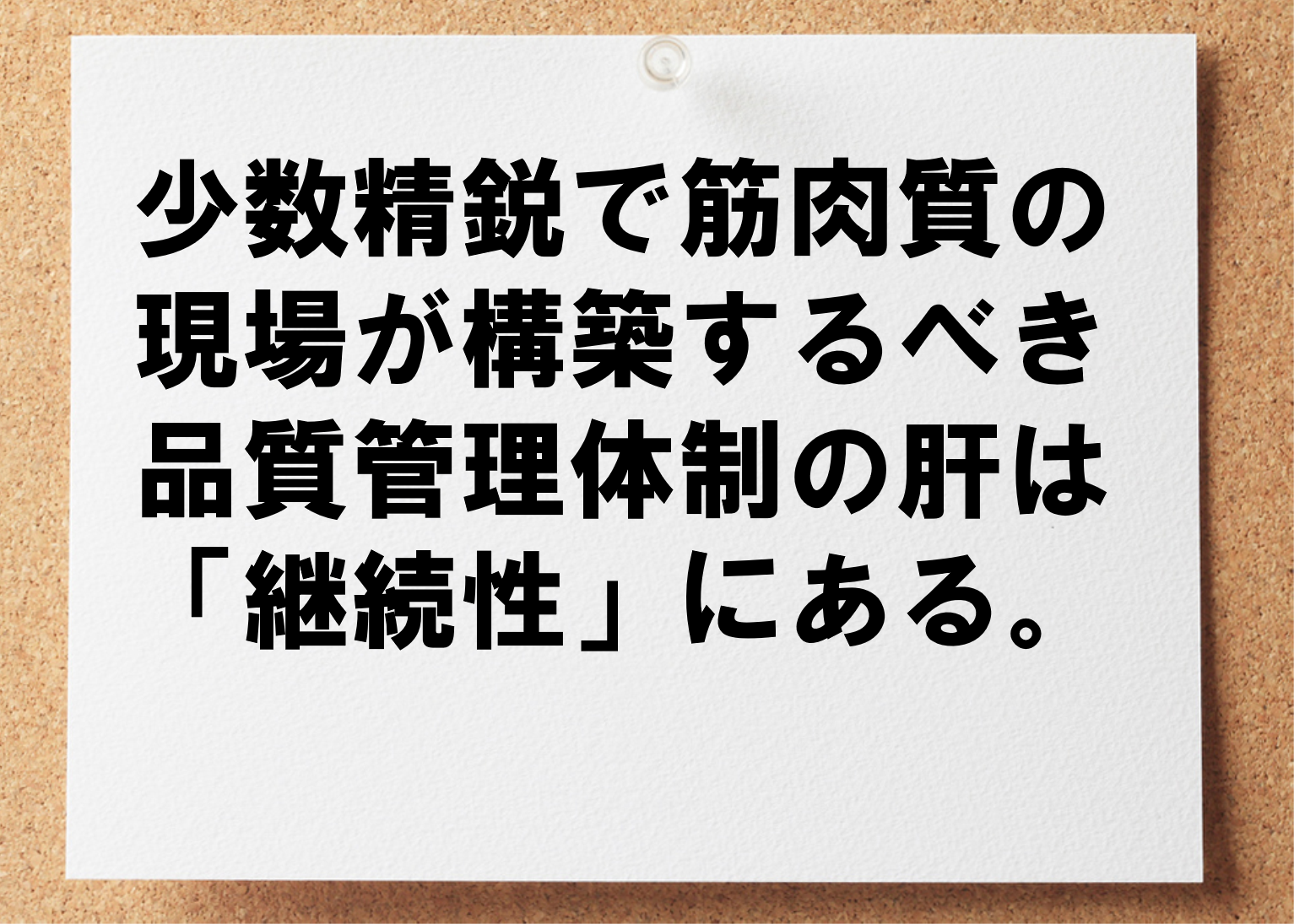
仕事の流れの中で、無理なく品質管理ができていますか?
「繰り返し品にもかかわらず、今も断続的に品質クレームを出してしまいます。」
個別相談でご相談を受けた、ある中規模メーカー経営幹部の言葉です。
そのメーカーではいわゆる下請け型の事業を展開しており、特注品と規格品の両者を生産しています。
売上規模で6:4と、特注品が多いですが、安定した収入源として重要な役割を果たしているのが4割を占めている規格品です。
ただし、こうした繰り返し品でしばしば顧客から要求されることがあります。
毎年求められる一定割合での値下げです。
一定期間毎、一定量の発注を出しているわけだから、造るのにも慣れ、徐々に効率が高まるだろうと顧客は期待します。
効率向上で実現できたコスト削減分を、双方で折半しようというのが顧客の意図です。
生産活動は学習の場でもあるわけで、現場は、継続的な生産活動を通じて、知識・技能を獲得し、作業の熟練度が高めます
そのよりどころは、学習曲線や経験曲線の考え方です。
学習曲線は「累積生産量」と「製品1個当たり直接労働時間」の関係を示しています。
経験曲線は「累積生産量」と「単位当たり実質総費用」の関係を示しています。
両者とも似ていて非なるものですが、累積生産量とともに時間、費用が右肩下がりになる点は同じです。
これが、顧客が「双方で折半しよう」と主張する根拠となっています。
しかし、先の中堅メーカーでは、そうなるどころか、品質クレームを出している始末。
こうした結果、顧客からも「同じ製品を造り続けているのに、どうして品質クレームが?」と問われているとのこと。
これまで、現場に任せきりだった品質管理を、組織で取り組まねばならないと考えてのご相談でした。
弊社事業の2本柱である「生産性向上」と「人材育成」のうち、品質管理体制の構築は「生産性向上」活動の一環として考えています。
品質活動の指標もいわゆる「生産性」で表現できるからです。
分母の「累積生産数量」に対して、「不良数」「手直し数」「クレーム数」を分子として当てはめれば、品質の生産性を評価できます。
これらを指標として、品質管理を展開するのです。
品質活動の良し悪しを評価できる指標を設定したうえで、品質管理の体制を作り上げていきます。
ただし、ここで注意すべきことがあります。
いわゆるISOで規定された品質マネジメントシステム(QMS)をはじめ、一般的な品質管理の手法をそのまま現場へ導入しようと考えないということです。
大手には人材や工数など、中小に比べて、間接業務に割ける多くの経営資源があります。
品質管理、品質保証の”専門部隊”を置けるほどです。
一方、中小の現場で同様な対応は難しいでしょう。
そして、品質活動で最も重要なのは「継続性」です。
ですから少数精鋭で筋肉質の現場ならでは品質管理体制を目指します。
最初から大手のやり方を目指しても、頓挫するのは火を見るより明らかだからです。
新規顧客開拓の際、顧客から「おたくでは品質管理、どうやっていますか?」と問われることがありませんか?
そうした問いかけがあったとき、どのような説明をしているでしょうか。
例えばISO9001を取得していれば、それが顧客の安心を獲得する手段になり得ます。
ただし、このISOを取得・維持する費用対効果を疑問視する経営者もいるようです。業界によって対応は多様ですが、顧客は、必ずしもISOを望んでいるわけではありません。顧客は、品質面で、安心して任せられる体制の有無を気にしていることが多いのです。
かって大手の製造現場の管理者を担っていたとき、金型製作の協力会社と一緒に仕事をしたことがあります。
協力会社の現場で製造してもらう金型の品質を高める活動を展開しました。
品質を高める方法、チェックの方法、いろいろアイデアが出ますが、依頼する側として最も気になったのが、その仕事のやり方には「継続性」が伴っているか否かです。
1回限りの対応でしたら、少々厳しめの管理でも力づくでやり切れます。
しかし、品質管理は1回限りではなく、今後、ず~っとですから、気が付いたら、やっていませんでしたでは、意味がありません。
その現場の持っている力、いわゆる現場力も反映されますが、「継続できる」品質管理でなければだめなのです。
そこで、先の経営幹部へお伝えしたことは、「継続性」の重要性です。
まずは、「継続できること」に絞って着手しましょうとお伝えをしました。
そこで、「継続性」に焦点を当てた体制作りの一例を下記に示します。
少数精鋭で筋肉質の現場ならでは品質管理体制では、焦点を「そもそも、不良を造らないこと」へ当てます。
当然、出荷検査、工程内検査で流出防止に力を入れている現場もあるでしょう。
ただ、この流出防止にのみ力点を置いていると、強化のために、ドンドン、工数を投入することになり、対応策にキリが無くなります。
ですから、現状の流出防止策を踏まえて、それらを補完し、あるいは代替する目的で、「そもそも、不良を造らないこと」に力を注ぎたいのです。
「そもそも、不良を造らないこと」の実践では、「①生産の流れ」と「②開発の流れ」に着目した定石がありますね。
そこで、①②の定石に着目して、「継続できる」品質管理の体制を構築するわけですが、ここからは現場の特徴を踏まえたいところです。
先の現場では、「設備ごとに生産活動が完結する」という特徴がありました。
そこで、先の企業では、①生産の流れに着目し、「そもそも、不良をつくらないこと」を実践する活動の一つ、「自主検査」に焦点を当てました。
「自主検査」とは、その設備で製造した製品について、その設備担当者が品質PDCAを回し、自分の担当工程内でPDCAを完結させる活動です。
では、どうやって、その設備担当者が品質PDCAを回すのか・・・・。
チェックシートを作って、云々という作業が思い浮かびますが、その現場では、多様な事情により、そうした手段には無理があると判断されました。
設備担当者は生産活動以外の指示を加えると混乱する懸念があり、現段階では、生産活動以外の「作業」を定着させられないと推測されたのです。
あくまで「継続性」のある活動にしなければなりません。
そこで、この現場では、連携力を生かした「自主検査」体制を試みることにしました。
つまり、「自主検査」の品質PDCAを回すために、隣接した設備担当者との相互チェック、リーダーとの相互チェック、昼夜勤務間での相互チェック、これら3つの相互チェックで体制の定着化を図ります。
さらに、本来、全数検査で対応したいところですが、最初からは無理なので、抜き取りからスタート、そして、「継続性」を実現するため、チェックに3つの連携力を生かすことにしたわけです。
チェックの内容もさることながら、まずは、「継続性」に焦点を当てた体制作りに着手しました。
品質管理も生産性向上の一環として取り組みます。
少数精鋭で筋肉質の現場ならでは品質管理とは、少ない工数で最大限の成果を上げる管理のやり方でもあり、それ自体が生産性向上活動です。
そして、その生産性を高めた品質管理で目指すべきことが「継続性」なのです。
これが中小現場での品質管理体制構築の進め方であると考えています。
現場の仕事の流れの中で、無理なくできてこそ、「継続性」が実現きるわけですから、品質管理の業務を仕事の流れへ組み込む視点が欠かせません。
「継続性」へ焦点を当てて、少数精鋭で筋肉質の現場ならでは品質管理体制を構築します。
継続性に焦点を当てて、少数精鋭で筋肉質の現場ならでは品質管理体制を構築しませんか?