「生産性ロードマップ戦略」—儲かる工場経営を目指して—第112話 現場改革の初手
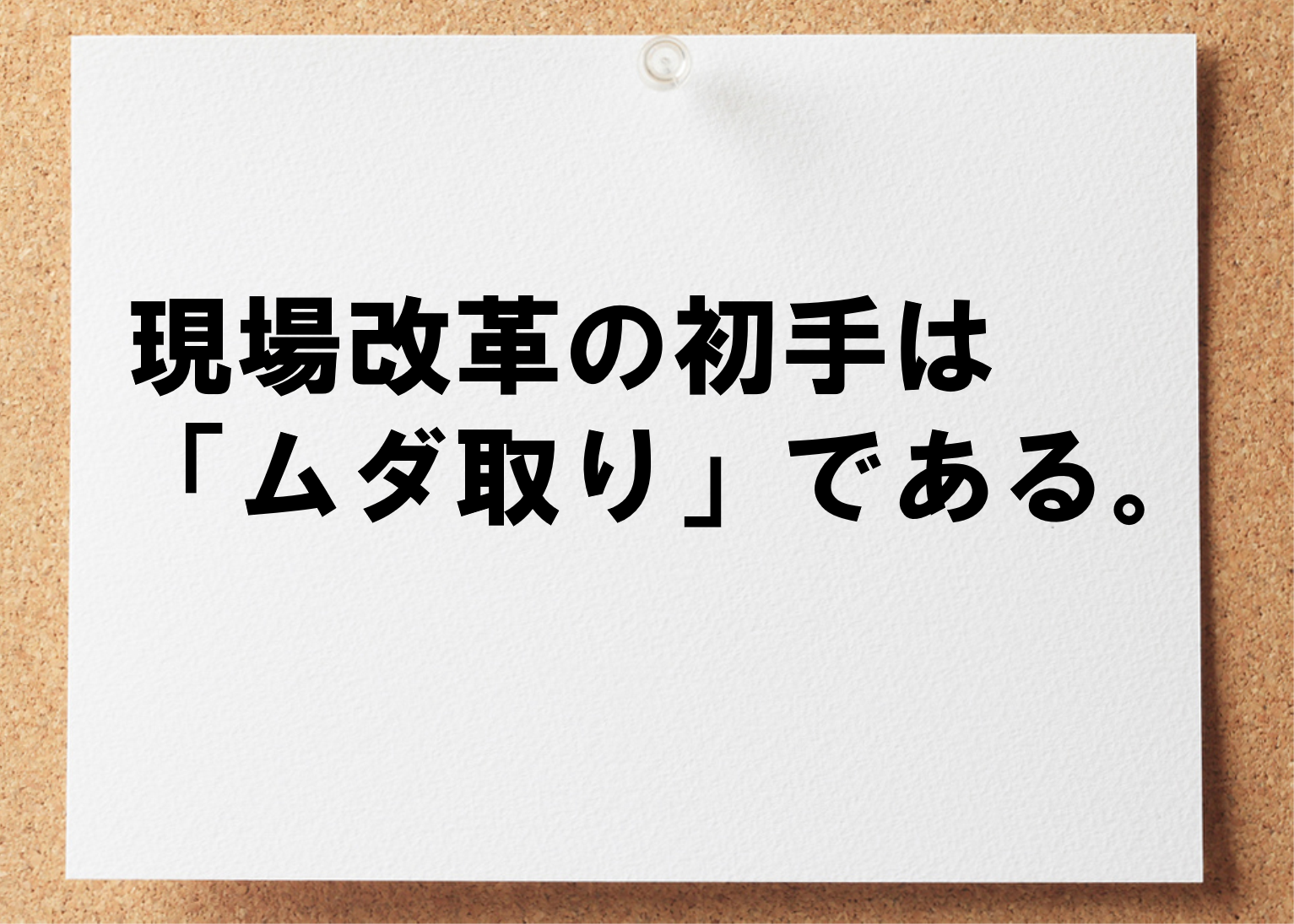
現場改革の初手を間違えていませんか?
「ウチの現場で新たな現場活動をやることができるでしょうか?」
小規模製造企業経営者の言葉です。
現場体制の再構築を目的に個別相談をいただきました。
その経営者は既存顧客の売上で確実に利益を確保しつつ、新規品の試作をドンドンこなせる現場へ変えたいと考えています。
既存顧客が要求する納期や品質が従来よりも厳しくなっている一方、価格は据え置きです。
既存顧客の売上高が伸び悩む中、まずは、利益をしっかり確保することが求められます。
さらに、新規顧客開拓を進めて、既存顧客への依存度を下げる必要があると考えました。
経営安定化のためです。
したがって、現場では、今後、既存顧客の仕事をさばきつつ、新規顧客への挑戦もしなければなりません。
従来の仕事のやり方のままでは利益を確保できなくなると経営者は考えました。
皆さんの現場では、改善活動が生産活動に組み込まれ、日常業務となっていますか?
それとも、事が起きた時、あるいは特命事項がある時、都度取り組むような非日常業務になっているでしょうか?
改善活動は日常業務として、日々の生産活動に組み込むことを考えてください。
改善活動はモノづくり欠かせない論理的思考を鍛える場になるからです。
改善活動は問題の認識から始まります。
そして、問題を問題として認識するには基準が必要です。
現状が基準よりも劣っていることを客観的に知って初めて問題を問題として認められます。
それには、生産活動が定量化、数値化され、見える化されていないとできません。
さらに、”なぜなぜ分析”で問題の原因を探ります。
なぜなぜ分析の目的は因果関係を明らかにすることです。
人や仕組み、固有技術の切り口で原因を複線でドンドンさかのぼり、解決の手がかりを見つけます。
そして、明らかにされた因果関係をもとに、複数の原因へ手を打つわけです。
さらに、ここで欠かせないの対策前後、いわゆるビフォアー、アフターで比べる体制を整備しておくことです。
フォローと評価も欠かせません。
それからPDCAを・・・・・というように、改善活動の活動領域は広く、現場の総合力が試されます。
改善活動は、あらゆる手法が駆使され、ものの見方、計画の進め方、工程間で連携のやり方など、科学的・工学的思考ばかりでなく、実行力や人間力も必要とされる活動なのです。
ですから、改善活動は継続的、組織的でなければなりません。
単発的、属人的な仕事で、科学的・工学的思考力や実行力、人間力が強化されることはなく、やっつけ仕事で終わります。
つまり、こうした総合力は仕事のやり方を規定することとなり、それはとりもなおさず組織文化の形成へ繋がるのです。
弊社が、継続的、組織的な改善活動を重視する所以はここにあります。
生産性ロードマップ戦略の狙いのひとつが改善活動の現場定着であり、これによって経営者は、”今”のことを現場へ任せられる体制に近づくのです。
先の経営者にも、こうした継続的、組織的な改善活動の意義を説明し、その定着に挑戦してみましょうと提案した次第です。
そして、返ってきた言葉が最初に挙げた言葉です。
活動の重要性は理解できたものの、日々の生産で手一杯の現場に新たな活動をさせられだろうか?というのが経営者の懸念事項でした。
「だからこそ、生産性を高める活動に取り組むのです。」
多くの中小製造現場を見てきた伊藤は、中小現場に余力がないことを十分に理解しているので、まずは、生産性向上の初手をお話をしました。
現場改革の初手、それは・・・・・。
まずは、余剰工数を生み出すことからです。
生産性向上に取り組む工数を確保しなければ、現場は動けません。
改善活動を始めたとたん、日々の生産活動に支障が出るようでは本末転倒です。
経営者の右腕役、つまり現場リーダーに新たな業務を加える余力があるなら、早速、課題の本丸を攻めましょう。
しかし、多くの中小現場では、右腕役のリーダーが多様な業務で手が一杯、新たな業務をさばくだけの余力を持たないことが少なくありません。
「忙しくて手が出ない。」というリーダーの言葉に首肯せざるを得ないことが多いです。
ですから、こうしたとき、まずやるべきことは、全体最適化の視点で、余剰工数を生み出し、改善業務に取り組むための工数を獲得することからです。
リーダーを含めて、現場全体の持ち時間は一定ですから、その持ち時間内で新たな業務を加えられる状況にしないとなりません。
限られた持ち時間の中で最良の仕事をこなせる体制を構築するのです。
生産性向上には2つのタイプがありますが、弊社で定義しているところのタイプYの生産性向上で余剰の経営資源(人、時間)を生み出すところから始めます。
タイプYとはインプットが減ってもアウトプットを維持する生産性向上のことです。
まず、ここで、余剰の工数を生み出します。
そして、獲得できた工数で、さらにタイプYの生産性向上を推し進め、さらなる余剰工数を生み出すのです。
そうして、余剰工数をもとにしてさらなる・・・・・。
余剰工数からさらなる余剰工数を生み出して、活動に十分な人や時間が確保できたら、本来狙っていた改善活動に着手するのです。
いきなり本丸に乗り込もうとしないことです。
具体的には「ムダ取り」から取り掛かかります。
いきなり、改善活動に取り組みましょうと声を掛けても、今の仕事のやり方では、そもそもその工数がない現場が多いからです。
現場や業務を見渡して下さい。
ムダはないですか?
ムダとはいわゆる”価値(顧客にとって)”を生み出さない作業、業務、仕組み、ルール、あらゆることです。
長年の慣例で開催している会議、それ価値を生んでいますか?
活用されていない報告書、提出物を現場に書かせていませんか?
運搬作業を減らせませんか?
自動サイクルボタンを押した作業者が設備の前、自動加工終了を待っていませんか?
必要な情報を伝達するのに、現場を走り回っていませんか?
…などなど。
こうしたムダが全て省かれたと仮定してください。
どれほどの工数が生み出されるでしょうか?
手一杯と思い込んでいた現場から”工数”という貴重な資源を拾い出すことができます。
現場には”慣れ”があるため、ムダをムダと認識できないことが多いですから、客観的な目で指摘することも欠かせません。
中小現場の改善活動は「ムダ取り」から始めます。
これは、いわゆる、店舗における品揃え理論と同じですね。
限られたスペースで最良の品揃えを実現しようとしたら、現状の品揃えに対して、何を抜いて、売れ筋を加えることをしなければなりません。
あれもこれも店舗に商品を並べることは不可能です。
店舗の効率を高めることにつながります。
中小生産現場の生産性向上活動では、継続的、組織的に取り組むための経営資源を生む出すことから始めます。
いきなり、狙った生産性向上の本丸を攻めるのではなく、「ムダ取り」で本丸を攻める体制をつくるところからです。
そうして生産性向上、改善活動の原資を獲得します。
余剰を投入して、さらなる余剰を生み出す・・・、利子が利子を生むという複利のような考え方の先に本格的な生産性向上があると考えてください。
成果物は継続的、組織的な改善活動の現場定着です。
こうして現場の基礎体力が強化され、少数精鋭の筋肉質の現場へ変わっていきます。
中小の現場でも、大手に負けない、継続的、組織的な改善活動を定着させられるのです。
継続的、組織的な改善活動のしくみをつくりませんか?