「生産性ロードマップ戦略」—儲かる工場経営を目指して—第15話 現場の見える化とICTは相性が良い
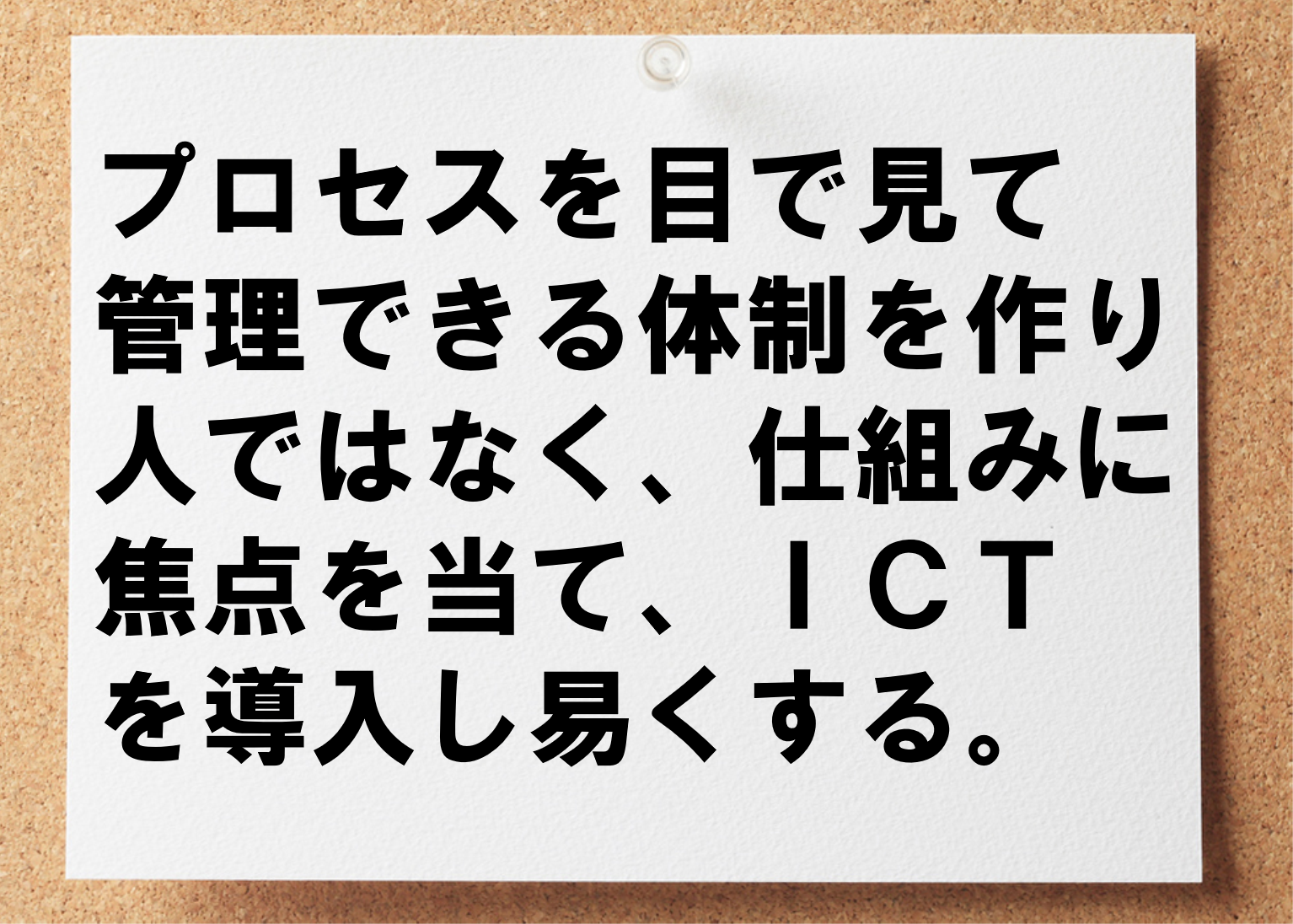
自社製品や自社サービスが生み出されるプロセスを、目で見て管理できる体制を作る。
”人”ではなく”仕組み”に焦点を当て、現場の高度化を図るのに欠かせない情報通信技術(ICT)を導入し易くする、という話です。
問題が発生した時、原因究明が、関連した現場の作業者や責任者を「特定」することに始終することはありませんか?
製造プロセスを、目で見て管理できる体制が整備されていますか?
付加価値を高めたかったら、自社製品や自社サービスが生み出されるプロセスを、目で見て管理できる体制を作ります。
目で見て管理しているので、客観的な戦略的意思決定ができます。そして、自社工場の強みの延長線上に戦略を描けば、研究開発の不確実性を最小化しつつ、戦略をやりきる確率が上がります。
さらに、自社工場のプロセスを、目で見る管理ができていれば、情報通信技術(ICT)を現場へ導入する時、取り組みの論点が絞りやすくなります。
プロセスをデジタル化するには、プロセスを工学的な用語へ変換し、それを具体的な現場の管理項目、調整項目にまで落とし込む必要があります。
こうした業務は、モノづくりの流れを的確に把握していること、工場全体での最適化を理解していること等、言い換えれば、現場を客観的に知っていないとできないことです。プロセスの見える化を図るためには、現場を熟知している必要があります。
目で見る管理ができていれば、情報通信技術(ICT)を現場へ導入しやすくなり、問題が発生した時の原因の特定が迅速にできます。
・・・・・と言うよりは、問題の原因の特定を迅速にできるような体制が整備されていて、初めて、情報通信技術(ICT)が現場へ導入しやすくなり、IT活用力がますます高まる。つまり、プロセスの客観化ができていてこそ、現場でのIT活用力が生きる、と考えます。
ITはあくまでも”道具”であり、その道具を生かすには事前準備がいるのです。
プロセスの客観化が図られていないと、問題の原因を”人”に求めがちになり、付加価値を高めるどころの話にはなりません。
従業員規模100名前後の金属製品製造業の経営幹部の方と一席、ご一緒した時の話です。
その方の現場で製品外観上のクレームが発生し、その原因究明をした時のことが話題になりました。
「ウチの現場は、まだまだ考え方が甘くて、決められたことが守られないくてダメなんですよね。」
問題の原因として、”工学的”な話よりは、”属人的”な話の方を多くされていました。
そして、会話の最後の方では、人財育成も上手くすすまなくてねぇ、という話になりました。
問題発生の原因として、”人”に焦点を当てがちな現場では、往々にして製造プロセスが目で見えるようになっていない、言い換えると、品質管理や納期管理が現場の各工程に丸投げ状態になっていることが少なくないです。
さらに、そうした現場では、ノウハウはあくまで個人的にしか蓄積されていないことが多いです。その結果、現場のOJT、技能伝承も担当者任せになり勝ちで、組織的に進めることができていないことがしばしば見られます。
生産管理者の仕事は、生産指示書の発行と最終納期のフォローだけという体制の工場では、そうなります。(そもそも、これだけでは”生産管理”とは言わない。)
生産管理の本業は、生産計画立案、それに伴って発生する現品を管理し、各工程の生産能力の余裕度をチェック、そうして工程全体の進み具合をフォローすることですが、各工程に管理を丸投げしている状況では、管理の一元化ができず、”生産管理”が機能しません。
こうした業務は、製造プロセスを完全に把握していないとできない仕事です。
一方、製造プロセスが見える化されている現場では、本来の生産管理が機能しています。
”丸投げ状態の現場”と比べて、生産管理が機能している現場では原因究明で、焦点を当てる箇所が違います。問題を発生させた”人”ではなく、”仕組み”や”ルール”に焦点を当てます。
製造プロセスが見えているので、問題が発生したのは、望ましい姿とはズレがあったから、という発想になります。
当然、関与した”人”も関係しますが、それはあくまで従属的な要因。主因は、望ましい姿からズレていた”仕組み”や”ルール”となります。
ですから、問題が発生したら、従来の仕組みやルールに工学的な視点、組織的な視点で改善を加えていけばいいわけです。
製造プロセスが目で見えるということは、”属人的”な要因を排し、客観的に”仕組み”や”ルール”に改善を加え、ノウハウを蓄積しやすい環境になっているということに他なりません。
人に原因を求めている限り、現場への組織的なノウハウの累積は期待できません。
なぜなら、対象になった人が去ったらそのノウハウはなくなるからです。
人にではなく、現場自体にノウハウを蓄積する方が、経営者にとってもお得なはずです。
ですから、自社製品や自社サービスが生み出されるプロセスを、目で見て管理できる体制を整備します。
結局は、こうした状態がIOT(もののインターネット)の導入で成功するための前提条件でもあることに留意します。
付加価値を生み出すプロセスでは、職人芸的な側面は当然にあってもいいですし、そうした”超”属人的な要因が中小現場の強みになる可能性はあります。しかし、それでもやはり、製造プロセスを全体最適の視点で見ると、プロセスの客観化は欠かせません。
製造プロセスの付加価値への寄与度は多様です。寄与度の低いプロセスや高いプロセスが、現場で混在しています。
寄与度の低いプロセスで、可能な限り”人”の要因を排除することは、コストの上でも欠かせないこと。それに加え、付加価値への寄与度の高いプロセスでも見える化することは、高付加価値化を加速させることに繋がるからです。
工場を対象にした全体最適による高付加価値化では、製造プロセスの客観化、見える化は重要課題です。人の要因を極力排除します。
属人的な要因を排除する、という考え方は、進歩著しい”自動運転車”でも見られます。
政府は自動運転車の技術進歩を示すロードマップを作成しました。レベル0からレベル4の5段階で将来を描いています。
レベル0 アクセル、ハンドル、ブレーキ、すべてドライバーが操作
レベル1 アクセル、ハンドル、ブレーキのどれか1つを車側が操作
レベル2 アクセル、ハンドル、ブレーキのうち複数を車側が操作
レベル3 アクセル、ハンドル、ブレーキの全てを車側が操作。
ただし緊急時はドライバーが操作。
レベル4 アクセル、ハンドル、ブレーキの全てを車側が操作。
もはやドライバーの関与ゼロ。
現在、レベル2の新車が発売され始めているようです。政府としては2020年東京オリンピック開催に合わせてレベル3の実現を目指したいとしています。そうして、レベル4は2025年を目処に実現させる。
こうした自動運転技術の開発で話題になるのが、”事故”を起こした時の責任の所在。
運転手なのか、車なのか?責任の所在は、ロードマップによると、・・・・・、
レベル0からレベル2までは運転手側の責任。
レベル3では原則運転手側の責任、ただし自動運転時は車側に責任がある。
そして、レベル4では車側にのみ責任がある。
ここ10年のうちにレベル4まで進めることを目指すのですから、技術の進歩が想像を超えて早くなることは確実なようです。運転という作業から人を完全に解放すること。こうした状態を目指しているのは明らかです。
これを実現させるには、当然のこと設計者自身は、車を動かす”管理項目”に関して全て理解していなければなりません。
人任せのところを、ゼロにすることを目指しているわけですから。
それを可能にするプログラムの行数は、原子力発電所を稼働させるそれに匹敵するとか、それ以上であるとか、そんな水準の仕事です。人工知能(AI)も駆使して、あらゆる場面、事態を学習させることも行われているようです。
モノづくり現場にICTが導入され、IOTを生かして付加価値を高めようとするならば、あらゆる生産活動を目で見る管理、客観的にしておく必要があります。
人の要因を排除し、客観的に判断できる状況を作ります。
そうなるために、自動運転では”プログラム”が、モノづくり現場では”仕組み”や”ルール”が主役になる必要があります。
自社製品や自社サービスが生み出されるプロセスを、目で見て管理できる体制を目指します。現場で問題が発生した時、”人”が原因でトラブルが発生した、という体制をいつまでも続けていると、技術の進歩から取り残されてしまいます。
自社工場の”今”を知って、自社の強みの延長線上に戦略を描き、研究開発の不確実性を最小限にしつつ、成功させる確率を高めます。
付加価値を高めるための視点として、製造プロセスの客観化・見える化に注目です。
自動運転技術のように、属人的な要因を排除するという論点でプロセスの客観化を図ってみませんか?
結果としてIOTを導入しやすい環境整備を行うことにもなります。
将来を目指した取り組みです。
まとめ:自社製品や自社サービスが生み出されるプロセスを、目で見て管理できる体制を作る。”人”ではなく”仕組み”に焦点を当て、現場の高度化を図るのに欠かせない情報通信技術(ICT)を導入し易くする。