「生産性ロードマップ戦略」—儲かる工場経営を目指して—第16話 IOTを現場へ導入するときに考えるべきこと
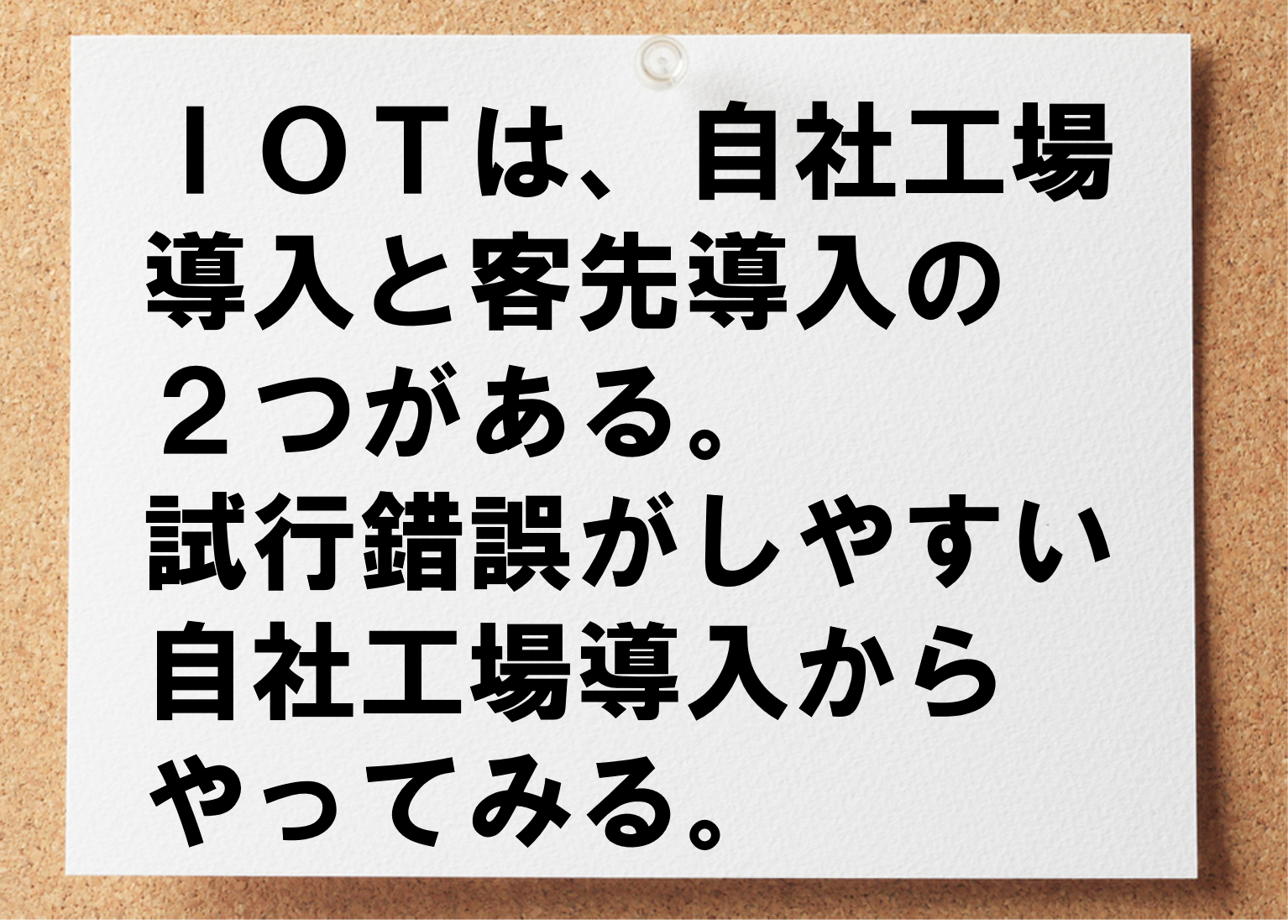
IOTを導入するとき、
1)生産のコストに焦点を当てて自社工場内へ導入するケース。
2)客先での「コト」「価値」の機能の維持に焦点を当てて客先へ導入するケース。
2つがあり、試行錯誤がしやすい1)からやってみる、という話です。
IOTを現場へ導入することを考えていますか?
IOTを導入する時の考え方が整理されていますか?
モノづくりの本質を強化するには、2つの変換の質を高めます。
1)現場のモノづくり(コア技術、カイゼン) → 製品やサービス
・コア技術やカイゼンを通じて、当初設定した「コト」「価値」を含む製品、サービスを製造すること。
2)製品やサービス → 顧客の利便性(付加価値)向上
・顧客の手元にある製品やサービスを通じて、当初設定した「コト」「価値」を顧客へ届けること。
2つの「変換」の質を高めるのが重要な論点です。
もののインターネット(IOT)は、その取り組みを加速させる道具です。
IOTを導入したからと言って、”自動的”に「変換」の質が高まるわけではないと申し上げました。
極めて重要な認識であると考えています。
引き続き、IOTを現場へ導入する具体的な考え方を整理します。
さて、ここで、顧客へ”快適”さを届ける製品を想定します。この製品を持てば、顧客は”快適”になる。その製品の従来仕様は、形状が直方体、重さが100です。
研究開発の結果、形状を板状、重さを10に仕様変更すると、より水準の高い”快適”さを提供できることがわかりました。重さ100から重さ10への仕様変更です。
必要材料が10分の1と激減しています。
したがって、従来対比で大きな原価低減も同時に見込める”おいしい”新製品となるのかと思いきや・・。
技術課題が2つがありました。
a.従来の直方体を板状へ変更するには、新たな「金型技術」や新たな「製造条件」を確立する必要がある。
想定される歩留まりや不良率を考慮すると、従来技術のままではコスト高になる。
b.板状製品では構造強度が求められ、強度を維持する必要がある。
時間を重ねるにつれて、経年劣化で強度低下する懸念がある。
新製品を開発した時に、しばしば直面する類の技術課題です。
1)では、設定された顧客へ届ける「コト」「価値」が正しく、狙った原価で転写されること。
2)では、設定された顧客へ届ける「コト」「価値」が客先でも維機能低下することなく、維持されること。
軽量化、薄肉化、小型化、高機能化、高意匠化・・・・・・・、こうした高付加価値化は作りにくさを伴います。ですから設定された「コト」「価値」が狙った原価通りに生産できるかが一つ目の論点です。
もうひとつの論点は、自社製品がお客様の手元に届いた以降の話。自社製品が、お客様に「コト」「価値」を提供し続けているかどうかです。
このように考えると、2つの変換で議論される焦点が絞られます。
1)現場のモノづくり(コア技術、カイゼン) → 製品やサービス ではコスト。
2)製品やサービス → 顧客の利便性(付加価値)向上 では機能の維持。
コストと機能維持。
この2点に焦点を当てます。
1)の変換は、付加価値を、自社工場内で高める変換です
コストが議論の対象になります。
製造品質です。
設定された「コト」「価値」を生み出す製品やサービスを造るのに、手間ひまばかりかかっては儲からない。出来たはいいが、原材料の歩留まりは低いうえに、不良率も高く、人手もかかって生産リードタイムも長いでは利益を獲得できません。
儲かるためには、当然に、コストを意識した生産活動が必要です。
一方、2)の変換は、顧客にとっての利便性(付加価値)を、顧客の手元で高める変換です。
設計品質です。
そして、この設計品質が新たな付加価値を創出します。ですから、ここで生み出される「コト」や「価値」が、そもそも顧客の心に響くかどうかポイント。
そして、その「コト」や「価値」が顧客のところで継続的に機能しているかどうかです。
お客様が使い始めて、最初はヨカッタけれども徐々に機能が低下してきた、これでは信頼を失います。
2つの変換は、これまで暗黙知やノウハウの形で現場に蓄積されてきました。
それがモノづくり力であり製品設計開発力です。
こうして蓄積されてきた暗黙知やノウハウを”組織”として活用できる企業が強いメーカーです。トヨタなどはその代表的な企業でしょう。
トヨタにおける1)現場のモノづくり(コア技術、カイゼン) → 製品やサービスの変換はトヨタ生産方式です。知らない人がいないほどに有名です。
また、2)製品やサービス → 顧客の利便性(付加価値)向上の変換でも売れるもの作るトヨタ独自の開発体制があるようです。
今後は、これら2つの変換にIOTが加わります。
2つの変換を効率よく行い、付加価値を拡大させます。
IOTが、現場の5年先、10年先を大きく変えます。
IOTを活用できた現場とできていない現場で大きな違いが出てくると感じています。
付加価値の拡大に直結することだからです。
自社工場に照らし合わせ、IOTを導入する時の考え方を整理しておきたいです。
IOTを導入する際、どちらの変換へ適用するかを、まず決めます。1)の変換なのか2)の変換なのか。
IOTを導入するための視点は、2つの変換と同じく2つです。
1)生産のコストに焦点を当てて自社工場内へ導入するケース。
2)客先での「コト」「価値」の機能の維持に焦点を当てて客先へ導入するケース。
どちらで付加価値を拡大するか、ここで決めます。
次は、採取するデータの選択です。ここでは、狙った現象や機能と因果関係のある工学的データを選択することがカギとなります。
先にも述べたように、設計品質が新たな付加価値を創出しています。
したがって、2)に焦点を当てたIOT導入が理想です。
お客様と一体になった取り組みになるので、関係性が強化され安定した事業展開が期待できるからです。
米ジェネラル・エレクトリック(GE)社は、航空機のジェットエンジンやガスタービンを対象に、温度や振動、圧力などをセンサーでリアルタイムで計測し、部品の経年劣化を判断するサービスを展開済です。2)のケースの実例です。
「なるほど、測定してみないとわからないですね。」
工場で技術開発業務に携わっていた時のことです。
製造プロセス開発の途中で、ある空間をArガス置換する技術が検討テーマとなりました。
ある空間へArガスを上部から充填します。
空間の底面からArガスを置換して、空間内の空気を底面から徐々に上部へ排出することを想定していました。
所定のArガスを充填したにもかかわらず、どうも空間内での置換率が上昇していないような状況に直面しました。
そこで、空間内の置換率をリアルタイムで計測することに知恵を絞りました。
関係者で計測できるシステムを組み、空間内の置換率をリアルタイムで計測してみると・・・・・。
予想とは全く異なる結果が得られました。
当初、空間の「底面」からArガスで置換されるとしていました。
しかし、現実には、「上面」から置換されていた。
比重よりも空間の上下温度差に起因した対流による要因のほうが強かったわけです。
分析結果を見て、全員で納得しました。
現象をリアルタイムに計測することで、見えてくることがあります。
ただし、そのためには、計測するノウハウ、採取されたデータの処理手段、等々新たな経験を積む必要があります。
自社製品が産業財で対企業の製品であるならば、GEのような2)を想定したIOT戦略が考えられます。付加価値拡大を加速したいなら最終的に狙いたい分野です。
客先での対応であり、事業として軌道に乗せるには事前の準備、訓練も必要。
したがって、2)の取り組みには計測ノウハウ、データを取り扱うノウハウ等、新たな経験を積み上げ、独自のやり方を構築する必要があります。”客先”でリアルタイムにデータを採取し、処理をして、知見を出す、という新たな経験です。
そこでまず1)で実績を積む。
1)でのIOT活用を考えます。
中小製造業では、まず、1)でIOTを生かすのはいかがでしょうか?
変動費削減、生産性向上を目的に、自社工場内でIOTデータが採取できないかを具体的に考えます。
狙った現象と具体的に採取できるデータを紐づけることができなければなりませんが、自社工場ならば試行錯誤も自由です。
工場内を舞台に、変動費削減、生産性向上を狙って、工学的な因果関係から特定の計測値を設定します。
リアルタイムで計測できるよう工夫をして、データを継続して見続け、変化をとらえる。分析結果を生かし、現場でも付加価値の高い業務ができます。
データを生かすことが今後、現場でも求められます。
現場でIOTを生かしませんか?
まとめ:IOTを導入するとき、1)生産のコストに焦点を当てて自社工場内へ導入するケース。2)客先での「コト」「価値」の機能の維持に焦点を当てて客先へ導入するケース。2つがある。試行錯誤がしやすい1)からやってみる。