「生産性ロードマップ戦略」—儲かる工場経営を目指して—第193話 工程と工程間に潜んでいる無駄を見つける
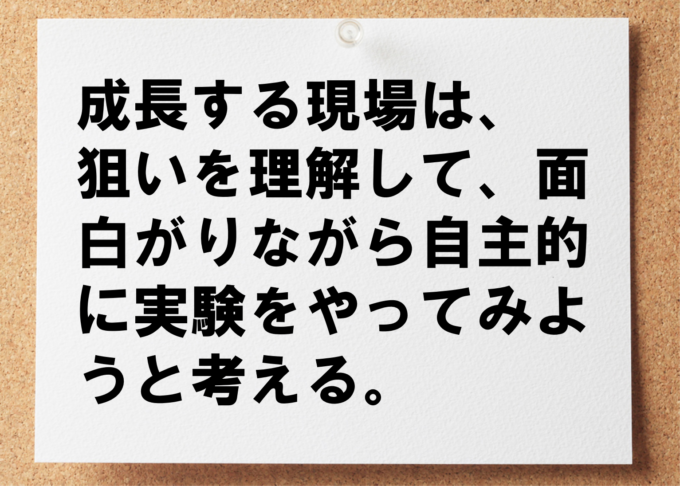
「先生、工程と工程の間に無駄な動作が潜んでいたんですね。」
先日、工程統合の実験をやってみた中小加工メーカー幹部が語った言葉です。
付加価値額生産性を向上させるポイントは手離れが良いモノづくりを実現させることにあります。既存顧客と既存製品だけに依存していてはジリ貧です。詰めて、空けて、取り込む、製販一体で付加価値額を積み上げる仕組みづくりが生き残りのカギです。
今やっている仕事のやり方を変えなければいけません。
先の企業では、現状を把握した後、早速、新たな仕事のやり方に挑戦することにしました。現場のビフォーアフターを図解して、何をどう良くしたいのかを解説したこともあってか、現場のノリも悪くありません。こうした挑戦に面白がっている風でもあります。
手離れが良いモノづくりの目的と手順を理解した現場では、リーダーを中心に、まずはやってみようとなったのです。
柔軟性のある現場は、考えるよりも行動を優先します。そうしたノリの良さを感じる、やる前から、何か期待感を感じさせてくれる現場です。
こうした実験を前にして、「やる時間がない」「やっても意味がない」と四の五の言う現場からは決して生まれることがないワクワク感を感じます。
いくつかのチェックを経て、まずは工程統合の実験からやってみようとなりました。
そして、実験の実施です。
実験後、幹部が実験に挑戦した作業者へ「どうだった?」と質問を投げかけました。
「はじめてやってみたので戸惑いましたが、慣れてくると意外と手際よくできるものですね。いままで気が付かなかったです。」
作業者の答えを耳にした幹部が、工程統合の実験結果で腹落ちしたことがあります。
やってみないとわからないものだ・・・・。
冒頭の言葉がそれです。
リードタイムを決める2つの設計のうち、現場レイアウトに影響するのは工程設計です。現場レイアウトの基本的な分類は生産管理の教科書に解説されています。
・固定式レイアウト
・機能別レイアウト(ジョブショップ型)
・製品別レイアウト(フローショップ型)
固定式は大型製品向け、機能別は多品種少量製品向け、製品別は少量多品種製品向けと説明されています。
ただ、昨今、中小製造現場でもマスカスタマイゼーションやマスラピッドが生き残りの手段となっており、手離れの良いモノづくりを実現させるレイアウトはそう単純ではありません。
現場独自の事情も踏まえ、ある意味、上記3分類レイアウトのいいとこ取りです。少数精鋭の中小製造現場ですから、柔軟性高くいろいろな実験をして、独自のプロセスを考えます。
手離れの良いつくり方を実現させ、付加価値額人時生産性を4,000円、5,000円とどんどん高めたいのです。
手離れの良い工程設計のキーワードは工程統合です。弊社では、中小現場での実現性を踏まえて、この工程統合を広くとらえています。
1)物理的、空間的に一緒にすること。
2)滞りのない生産の流れをつくること。
いずれのやり方にしても、狙いは、工程を分割したときに生じる「運搬」と「停滞」の排除です。先の現場で挑戦するのは1)になります。
現場診断や現場ヒアリングを通じて最適なやり方の仮説を立て、具体策を決めました。そして、検証です。
検証実験の結果、目論見通り、「運搬」と「停滞」が排除されたようです。予想外の時間短縮に現場の仲間からも「おおっ~」と声が上がりました。
生産性向上活動とは新たな仕事のやり方に挑戦することの繰り返しです。やってみないとわからないことばかり。ですから実験(仮説と検証)が必要なのです。
先の現場でもそうでした。実験によって工程間の無駄をあぶりだせました。
指示待ちで、試行錯誤を煩わしいと考える現場にはできません。独自の手離れの良い作り方を現場に定着させたかったら現場での実験が欠かせないのです。
それができない現場であるなら、試行錯誤をする挑戦心を引き出すところからです。
貴社ではノリ良く、工程間の無駄を排除する実験ができますか?そして、貴社での手離れの良いつくり方とはどんなでしょうか?
製造業では、多くの業界で「運搬」と「停滞」をなくして生産性を高めています。
昨今、薬品業界で、上記2)の手法を技術的に実現させたようです。
薬を製造するには、有効成分をつくるために、原材料の化学反応を何度も繰り返す必要があります。工程別に4~5個の大きな容器を設置し、その中で原材料をかき混ぜたり、熱を加えたりしていました。
「撹拌工程」→「加熱工程」→「撹拌工程」→・・・というように1つの工程を終える度に、中の半製品を次の工程の容器へ移し替えます。
つまり、容器サイズが生産単位となるロット生産です。
このロット生産方式では、生産量を増やしたかったら、ロット単位の設備投資が必要となってきます。また小刻みな生産調整も容易ではありません。ロット単位だからです。
稼働率を高めようにも限界があり、容器から容器へ中間製品を移すときにミスする懸念もあります。
製薬業界では開発競争が激しさを増しており、製薬各社は小回り性や柔軟性の高い生産方式を求めていました。
しかし、医薬品は複雑な化学反応をいくつも経なければならず、従来、品質を安定させる技術や設備の課題を解決できませんした。
そうした中、2014年ごろから世界の製薬業界で注目しはじめた手法が出てきました。パイプを通じて複数の小型設備を巡る連続生産の手法です。石油化学製品の小型プラントがイメージできます。
化学反応の研究が進み生産設備も進歩を遂げ、イノベーション、生産改革が起きたのです。
その手法を活用し、武田薬品工業など製薬各社は、薬の製造にかかる期間を大幅に短縮しようとしています。
この手法では、生産性向上に加えて、設備が小型化し、従来設備対比で設備投資を抑制できると期待されています。
(出典:日本経済新聞2019年11月5日)
手離れの良い生産現場は作業スペースの効率化につながりますが、製薬業界も同じことを狙っているようです。製薬業界は、1個流し生産のような多品種小ロット生産に対応したやり方を実現させたと言えるのではないでしょうか?
工程と工程の間の無駄を排除する生産改革は特別なことではありません。鉄鋼業界では1970年代に銑鋼一貫製鉄所を実現させています。
製鉄所での製鋼技術は、大きく3つのプロセスです。
・銑鉄をつくる。
・銑鉄を溶かして、転炉あるいは電炉で鋼をつくる。
・鋼塊を圧延、鍛造して製品をつくる。
その昔、この3つのプロセスが別々に行われていました。そこで、高炉→転炉をつなげ、さらには鋼塊を作って圧延・鍛造する作業で鋼塊自体をやめてしまうアイデアが出てきました。
転炉の中の溶鋼を鋼塊用の鋳型ではなく、断面が長方形の底がない鋳型に注ぎ、鋳型から出たところを水で冷やせば帯状の鋼が連続で出来上がります。
それを圧延すれば板材に、また鋳型の断面が丸ければ棒材ができるというわけです。連続鋳造、略して連鋳(C.C.)と呼ばれています。
銑鋼一貫では、工程間でインゴットが発生しません。「停滞」がなくなり、インゴットを保管する場所も不要となりました。工程と工程の間の無駄を排除する生産改革です。また、余熱も活用できるので経済的効果はさらに大きくなります。
製薬業界の新手法にしても、銑鋼一貫にしても、工程と工程を物理的、空間的に接続するだけでなく、プロセス開発という技術課題をクリアしてこそ実現できました。
伊藤も学生時代、1980年代後半の頃ですが、いくつかの製鉄所を見学したことがあります。当時すでに銑鋼一貫となっており、溶けた鋼がドンドン製品の変わる様を目にして技術の凄さを体感しました。
工程と工程の間にある無駄を除去するには技術の進化が必要な場合もありますが、手離れの良いつくり方という考え方では中小製造現場と同じであるとも言えます。
「運搬」や「停滞」をなくすることが製造現場の使命です。
大手の素材や化学系メーカーではプロセス開発が必要な事例も多いです。技術開発という試行錯誤が大部分を占めるが、考え方は中小製造現場と同じであることに気付きます。
会社の規模に関係なく、手離れの良いモノづくりが儲かる工場経営の要諦だということです。そのためには実験も欠かせません。モノ作りは技術ですから試行錯誤は当然です。
先の現場では幹部と管理者が主導して取り組みを進めています、経営者も現場のレイアウトを大きく変える水準の挑戦を望んでいます。あとはやるだけです。
次は貴社の番です!
・成長する現場は、狙いを理解して面白がりながら自主的に実験をやってみようと考える。
・停滞する現場は、四の五の理屈を言って、しかたがないからやろうと考える。