「生産性ロードマップ戦略」—儲かる工場経営を目指して—第204話 工程間の問題を解決するやり方は?
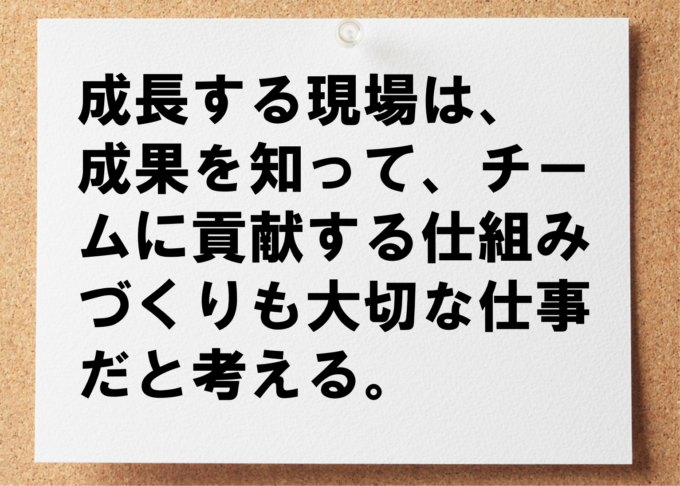
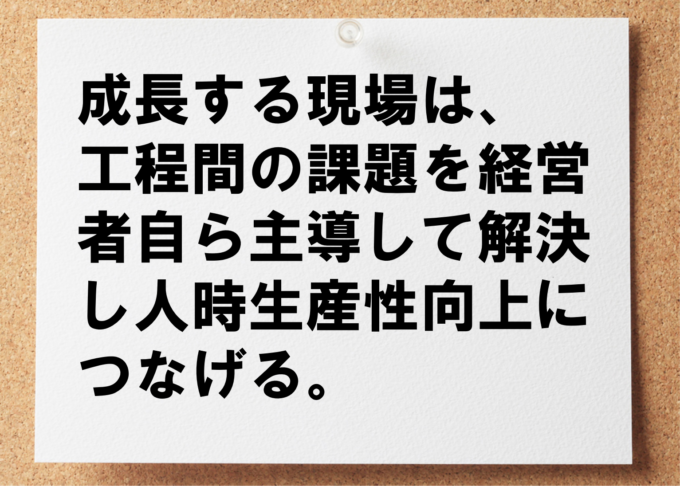
「先生、そのやり方に変わったらリーダーが楽になります。」
金属製品メーカー製造管理者の言葉です。
2つの工程で構成されている工場です。後工程で生産改革に挑戦中です。従来はロット単位で製造していました。そのやり方を変えます。
小ロットに対応する新たなやり方です。これを実現できると作業スペースが従来対比で3分の1に減らせます。トライアルでやったところ、なかなかイイ感じです。
この取り組みの前に、リードタイム短縮を目的とした工数削減も実現しています。現場活動の水準が高い現場です。
ここまでは、後工程だけの取り組みで成果が得られます。ただ、ここから先、前工程との連携が必要です。
前工程は部品を製造しています。そして、今、ここに問題があります。
前工程の原材料として調達する部材の納期をコントロールできていないのです。そのため、前工程で製造する部品の納期をなかなか確定できません。このしわ寄せは後工程に来ます。
前工程では、入手できた部材から手をつけ、出来上がったら後工程へ届ける・・・「成り行き生産」になっています。その結果、後工程も届いた部品から組立てることになるのです。
ですから、後工程では、納期を考慮して、“あえて”中間製品を作っておくことになります。その結果、作業台の上に仕掛品が多くなるのが”普通“となってしまうのです。
この問題は以前から認識されていました。これでは、後工程内で実現させたリードタイム短縮の成果を全社へ波及させられません。モッタイナイことです。
ではどうするのか?
戦略的仕掛品です。
これまで、後工程は、前工程から部品が届いたら組み立てるというやり方でした。組み立てるトリガーが前工程にあります。
それを、後工程が組み立てたいと考えたら、組み立てられるようにします。組み立てるトリガーを後工程が持つようにするのです。
生産の流れで大切なのは工程と工程とのつながりです。工程間連携。
その前に工程内がきちんとしていないとなりませんが、工程内のことですから、やろうという意思さえあれば、ここまでは一気に進みます、
しかし、工程間のつながりとなると少々やっかいです。部分最適の考えに固執していると対応できません。自工程のやり方を優先させたくなります。
ここでは、一気通貫、全体最適の考え方が欠かせません。そうしない限り工程と工程のつながりはよくならないのです。
従来から、前工程は自工程の都合によって部品をつくり、それを後工程へ届けていました。いわゆる「前工程押し出し方式」です。
後工程は、前工程の都合に合わせて組み立てることになります。したがって、前工程が部材入手日程をコントロールできないとなると、後工程は、その影響をもろに受けるのです。
仕掛り増へつながります。納期を考慮するために、どうしても作り置きしたくなるからです。現在、管理者の頭にある納期の時間軸は「週」です。週単位で生産計画を考えています。
前工程から届く部品の納期が分らない以上、とてもじゃないけど、日単位で生産計画を立てることはできません。納期遅れが怖いです。
そこで、後工程が「組み立てたい」と考えたら、組み立てられるようにします。だから「戦略的仕掛品」です。
これなら、日単位の生産計画ができます。なぜなら、後工程が「組立みてたい」と考えたとき、部品は必ずあるからです。日単位のリードタイムに基づいた生産計画ができます。
毎月、安定した一定量の受注がある。製品仕様も一定の範囲内にある。こうした前提が必要ですが。「戦略的仕掛品」で前工程も後工程も仕事をスマートにできるのです。
例えば、前工程は、7月の受注に対応する部品を6月30日までに製造し、戦略的仕掛品として準備します。
7月に入ったら、後工程は、受注が届くのに合わせて、リードタイムを考慮して、組み立てればいいのです。
必要な部品は準備済なので、日単位の生産計画ができます。加えて、生産改革で小ロット対応ができる新たなやり方になっているので、後工程での仕掛りはゼロです。
これが「後工程引き取り方式」です。
前工程と後工程との間に戦略的仕掛品が置かれるから在庫増となりキャッシュが・・・・という向きがあるかもしれません。そこで考えたいのは、後工程の仕掛品(中間製品)です。
先の企業の現場(後工程)へ足を運んだとき、作業場のテーブルの上にズラーっと仕掛品(中間製品)が並んでいるのを目にしました。そして、それが1週間、長いときは2週間近く放置されていたのです。
その背景は先に述べたとおり。
在庫を戦略的に活用したかったら「なるべく上流工程で」とは儲かる工場経営の定石です。後工程の仕掛品には作業者が投入した工数が既にのっかっています。
ですから、戦略的仕掛品は理にかなっているのです。小ロット対応ができる新たなやり方で成果を刈り取るためでもあります。
さらに、前工程押し出し方式では、前後工程の日程調整という、目に見えないコストが発生します。
前工程から届く日程が曖昧である以上、後工程の担当者は前工程と密な情報交換をして、日程の摺り合わせをしなければなりません。
後工程の担当者だけでなく、前工程の担当者もかなり疲れます。
その点、後工程引き取り方式では、戦略的仕掛品の管理だけで済みます。前工程は毎月最終日までに、決められた戦略的仕掛品(部品)を造っておけばいいだけです。後工程が使った分だけ埋めておきます。
後工程で何を使うかは事前に分るわけですから、月末納期の部品製造は自工程の都合で進められるのです。前工程押し出し方式では欠かせなかった“日程摺り合わせ”、この業務がなくなります。
管理者によると、後工程のリーダーはかなりの手間暇を掛けて、この業務をこなしているようです。この方式を採用する最大の効果は、リーダーの業務が楽になることかもしれないとは管理者の言葉です。見えないコストの削減。
冒頭の言葉です。
工程内の取り組みは現場に任せてもイイですが、工程と工程をつなぐ取り組みを現場に任せてはダメです。経営判断が必要となることに留意します。
先の事例では、戦略的仕掛品の是非を判断しなければなりません。これは経営者や幹部が経営課題として判断する事項です。
工程間をつなぐ課題を現場へ丸投げしてはいけません。経営者や幹部が主導します。それだけに工程と工程の間をつなぐ課題の成果は大きいのです。工程内の取り組みとは違うところです。先の管理者の言葉ではないですが、見えていなかったコストも削減できます。
さらには工程内の部分最適だけでなく、工程間も考慮した全体最適の考え方を現場へ浸透させる機会にもなるのです。
弊社では、このような儲かる現場活動の具体的なやり方をご支援しています。現場活動で新たな顧客を創出して下さい。
次は貴社の番です!
成長する現場は、工程間の課題を経営者自ら主導して解決し人時生産性向上につなげる。
停滞する現場は、工程間の課題が現場へ丸投げされて解決できず問題が放置される。