「生産性ロードマップ戦略」—儲かる工場経営を目指して—第210話 経営判断に生かせる現場データを手にするには?
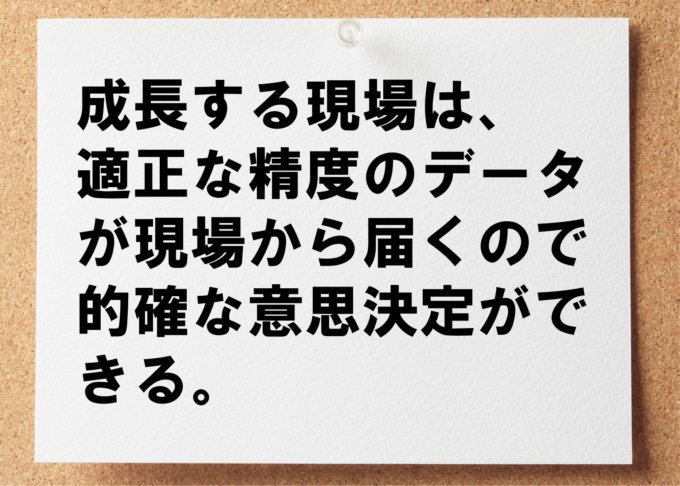
「時間の正確さを気にするようになってきました。」
機械加工企業、製造現場管理者の言葉です。
多くの現場では作業日報を活用しています。この企業の現場も同じです。直接作業と間接作業の所要時間を報告させています。
ただし問題がありました。長年、曖昧な定義でやっていたのです。数値の合計が8時間になっていなければならないのに、それ以下の日報が散見されます。
また、精度に個人差もあるのです。Aさんは0.1h単位であるのに対して、Bさんは0.5h単位になっています。こうした状況が放置されていました。
そこで、全員が同一基準で報告するやり方へ変えます。見積もりや人時生産性向上活動をフィードバックするためです。経営者は現場データをドシドシ使いたいと考えています。
ただ、全員が同一基準で報告するやり方へ変えることは簡単なことではありません。本気で取り組んだことのある経営者ならお分かりです。
データ品質を整えるのに時間がかかります。地道な取り組みが欠かせません。
経営者がやり方の変更を宣言する一方、その目的も現場へ伝えれば、一人ひとりの意識は高まります。自分たちのデータが工場経営の意思決定に貢献していることを知るからです。
現場は報告する数値の精度を気にし始めます。取り組み初めて数ヶ月後、データ精度が高まってきました。冒頭の言葉です。
経営者は多様化するお客様の要望を実現させたいと考えています。制約条件は製造手離れの善し悪しです。突発特急案件に対する柔軟性、業界トップ級のリードタイムを実現する機動性。したがって、新規顧客を開拓するのに製造現場も役割を果たしていることに気付きます。
また、新規顧客を開拓するキモは儲かる価格を設定してお客様と交渉することです。コスト把握抜きで儲かる価格を設定できません。ここでも製造現場が重要な役割を果たします。
経営者には現場の状況を知らせてくれるデータが必要なのです。
経営者は、作業日報をはじめとして、現場へいろいろな報告をさせます。時間、数量、水準に関する定量情報です。現場のデータを工場経営に生かします。
何のために日報をつけさせているのか?
日報で得られた情報を何に生かすのか?
ここが明らかですか?
ICTの進化で手軽にデータの自動収集ができるようになりました。今、大手で積極的に進められているIOTは20~30人規模の現場でも普通にやれます。
ただし、中小製造現場では、その前にやることがあります。手を汚して、データを集める貴社独自のやり方を確立することです。
そもそも、作業者の手によるデータ一元管理の仕組みがなければデジタル化もIOTもありません。大手でデジタル化がドンドン進むのは、作業者の手によるデータ一元管理の仕組みがあるからです。
ある部品製造現場での話です。作業日報には報告欄が10個以上あり、作業者は、長年、そこへ記入をしていました。このデータを何に使っていますか?と訪ねたのですが、知っている人はいません。
経営者にしても、従来からこの様式で記入させており、それ以外のことは特別に疑問を持たず、習慣的にやらせていたのです。書かせること自体が目的化していました。
データの目的を明らかにすれば、目的達成に必要なデータの様式や精度も明らかになります。製品別の人時生産性や儲かる価格を検討する時、1h単位はラフすぎます。
と言って0.1h=6分単位の精度では細かすぎです。15分単位くらいが妥当だろうとなります。目的を明らかにすれば現場もそれに合わせた精度で報告しようとするのです。
先の現場でも、次のようには説明してくれた作業者がいました。
「それまで、なんとなく、1時間、30分単位で時間を捕らえていましたが、工数削減や見積もりフィードバックに生かすと知って、時間をもう少し細かく捕らえるようになりました。」
数値は経営判断の手助けをしてくれます。現場からのデータ報告が欠かせません。中小製造現場の管理者時代、ここで苦労しました。
大手にあって中小の現場にはなかったことのひとつとして、作業者の手によるデータ一元管理の仕組みがあげられます。そのやり方を探るために試行錯誤しました。
考えてみれば、大手で勤務していた時代、データは現場から適切に報告されるという前提で仕事をしていたわけです。中小現場ではその仕組みをつくるところからでした。
作業日報に限らず各種データを現場から報告させようと考えるなら、次の5段階です。
1.知りたいことの全体像を教えてくれる情報を特定する。
2.その情報を評価する最小限のデータを特定する。
3.データの定義を設定する。
4.そのデータを報告してもらう目的を明らかにする。
5.定義が定着するまで繰り返し、繰り返し、しつこく現場をフォローする。
中小現場の管理者時代、担当職場の中に10数人の機械加工職場がありました。事業モデルはいわゆる「人工生産」です。QCDの決定権は全てお客様が握っています。
そうした現場でしたが、あえて付加価値額人時生産性向上に取り組みました。作業者の給料アップにつなげたい事情があったからです。
まずは、取り組みの全体像を教えてくれる情報は何か?と考えました。人時生産性が現場の儲ける力の全体像を教えてくれます。
したがって、個人別の人時生産性を把握するところからです。では投入工数を把握するにはどうするか?
当時、その現場でも作業票がありました。しかし、ご多分に漏れず、フィードバックに生かされていません。数値の精度も疑わしいものでした。
そこで、最小限のデータに絞ったのです。実績出来高だけを報告させることに変えました。それと同時に、標準出来高を設定し、実績が未達のときは未達理由を記入します。
「13時半から15時まで設備が故障で停止したので20個分の未達であった。」となります。時刻の最小単位は10分と定義しました。
人時生産性向上のために、標準出来高対比で未達時に焦点を当てたのです。未達原因となった事象の時間を正確に把握するよう現場へ指示したわけです。
目的は個別の人時生産性を高めて、お客様へレートアップ交渉をすることと説明しました。
なにせ「人工生産」事業モデルの現場です。作業者の給料アップにつなげたかったらそれしかありません。
そもそも、そうした儲からない事業モデルであること自体が問題でしたが・・・・。
そして、レートアップ交渉の意味を理解できた現場は新たな取り組みに一生懸命、取り組んでくれたことを憶えています。
製造業は工学です。数値評価が多くなります。これが小売りや他のサービス業と異なるところです。したがって、数値、データの扱いが大切になります。
日々納期に追われ生産活動に忙しい現場からどれだけ実のあるデータを集められるか?現場活動を成功へ導くカギです。最小限のデータに絞り、定義を明らかにし、目的を説明すれば現場も考えます。
管理ばかり強化しても儲けにはつながりません。必要なこと以外はさせないことです。
定着するまで、経営者が繰り返し、しつこく言い続けることも肝要です。しつこさは本気度を伝えます。そうすることで、適正な精度のデータが確実に経営者へ届くのです。
儲けの源泉は「外」にある以上、経営者の仕事の舞台は「外」になります。経営者は「内」を現場に任せないと社長業に専念できません。
経営者が不在であって適正な精度のデータが確実に届く仕組みをつくれば、意思決定ができます。現場データが貴社の命脈を保つのです。
先の現場では見積もりのフィードバックを始めました。儲かる価格を全社で共有します。
次は貴社の番です!
成長する現場は、適正な精度のデータが現場から届くので的確な意思決定ができる。
停滞する現場は、現場が忙しいことを理由にデータ定義の見直しすらしない。