「生産性ロードマップ戦略」—儲かる工場経営を目指して—第21話 儲かる工場経営での指差呼称を実践する
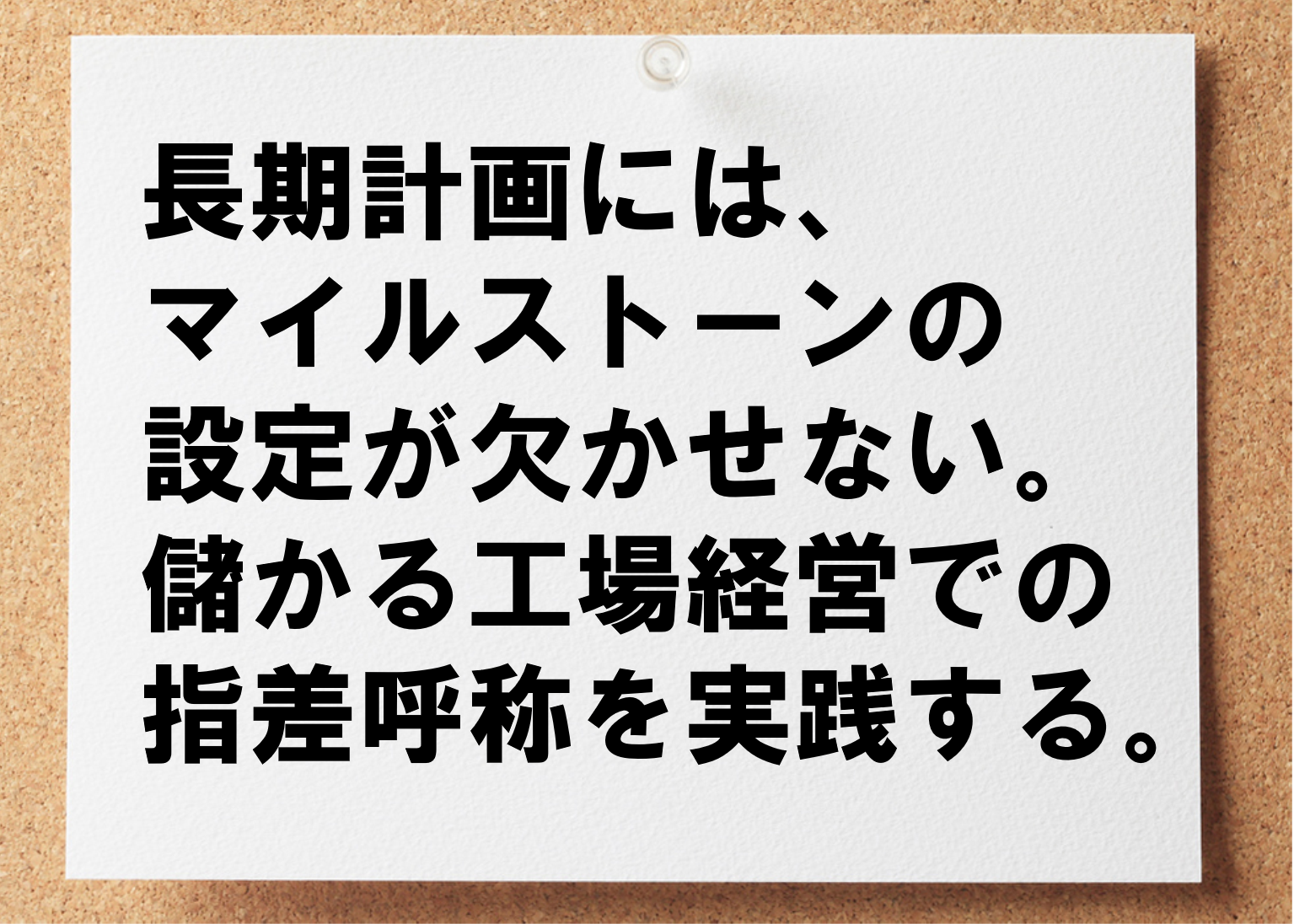
一旦立ち止まって進捗中のプロジェクトの現時点を見回して、当初計画と比較する、そして、先の見通しを立てる。長期計画にはマイルストーンの設定が欠かせない、という話です。
先日、知人を自家用車の助手席に乗せて、運転をしていた時のことです。車が信号の無い交差点に入り、こちら側の車線が一旦停止となっていました。当然に車を停止させ、その後、車が来ていないこと、安全を確認したのちに、車を前に進めました。
その際に、私がとった動作を見て、知人が一言。「おっ、癖になっていますね。」
その知人が指摘した動作とは・・・・・・・・・・。
多くの工場で実践されている指差呼称です。
動作を開始する時に、見間違いや操作ミスを防ぐのに効果があります。また、自らの安全が確保されているかの確認もできます。
現場で新人を受け入れる際に実施される”安全教育”に必ず入っているメニューのひとつです。
多くの工場では、現場の通路、あるいは作業エリアの床に描かれた足形を目にします。指差呼称を促すマークです。歩行中に、これから踏み出す先の安全が確保されているかを動作と声で確認します。
私も新入社員で配属となった現場の受け入れ先でしっかりと、この安全教育を受けました。安全担当の指導員が自ら手本を示しながら新卒の新入社員へ教えてくれました。
「通路を横断する時には、渡る前に、一旦停止して、右ヨシ!、左ヨシ!、前ヨシ!と声をかけること。そして、声といっしょに指差しの動作をすること。」
さらに、現場で実習を行った時、現場の責任者(当時は組長と呼んでいました。)からも事前の安全教育を受けます。その組長からも同様に指差呼称の指導がありました。
「設備を動かす前には、起動ボタンに向けて指差呼称を・・・・」
工場の現場において、指差呼称は安全確保の基本中の基本です。指差呼称を行った場合、なにもしない場合と比較してエラーの発生率が約5分の1に低下するとの調査結果も出ています。科学的にもその効果が証明されている指差呼称を、現場に定着させたいです。
安全への意識を持つ人ならば、こうした動作を工場内では習慣的に行います。私の場合、この動作が今でも、特に車を運転している時に習慣的に出てしまうわけです。
その時同乗していた知人も技術者出身で工場勤務の経験があったので、私の動作の背景を知っていました。イイ習慣は日常生活でも大いに活用できます。
当社のコンサルティングでは5年先、10年先の「見通し」を立てた工場経営をご指導しております。付加価値10年ロードマップ戦略。儲かる工場経営では、”今”もさることながら、”先”を知る努力が欠かせません。
多くの経営者は、”今”の問題や課題への対応に手いっぱいです。その結果、経営者が投じるエネルギーの8割、9割は”今”への対応であるように感じています。それでは、長期的な視野で安定して儲かる、儲かり続ける工場経営を実践することは難しいです。
なぜなら、市場も技術動向も、常に変化しているからです。
さらに、その変化のフレもハヤサも大きくなっています。
ですから、これからは従来にはない規模の変化(フレ×ハヤサ)に対応しなければなりません。この変化に適切に対応できなければ生き残れません。
そのためのロードマップです。そして、このロードマップを機能させるために極めて重要な役割を果たしているのがマイルストーン。つまりチェックポイントです。
計画は計画通りに進まないからこそ計画であり、事業計画は使い倒すものであると以前、申し上げました。(事業計画は使って、使って、使い倒すモノである)
こうした事業計画は、そもそも立案時点で考えていたストーリー通りに計画は進まないから事前に準備する道具です。最初から経営者の計画通りに確実に事が進み成果物を獲得できるとわかっているならば計画表は必要ありません。
経営者の頭の中にさえ、計画が入っていればイイです。ですが、現実は甘くない。計画をやりきるには、前述通り、変化に対応しなければなりません。
ですから、計画を完遂させるには、時間軸を意識したチェックポイントは絶対に必要です。これがなければダメです。
出来上がった後、そのまま経営者の机の引き出しにしまいこまれる事業計画が、成功したためしがないことを思い起こせば気付かれるはずです。
かって管理者を担っていた10人程度職場で、設備を新たに導入して生産性を向上させるプロジェクトを進めたことがあります。
”小さなプロジェクト”でしたが、しっかりと計画表を作成し、現場リーダーと共に進捗を定期的にチェックしました。
定期的なチェックポイントを設けた理由は、計画立案時点で、最終仕様を決定するための要因が確定していなかった、つまり変化の要因があったからです。
このケースで設定した定期的なチェックポイントは、情報共有のために有効であったとともに、変化に対応するためにも欠かせませんでした。
プロジェクトの対象が「変化」するものであるならば、常に計画と比較する必要があります。チェックポイントは定期的な確認作業のきっかけを提供します。
つまり長期計画を機能させるための仕組みのひとつです。
こうした道具を現場の若手人財といっしょになって活用し、成果を実感できる機会をつくると、道具が定着していきます。
一旦立ち止まって、進捗中のプロジェクトを見回し、当初計画と比較する、そして、先の見通しを立てる。この行為こそがポイントです。
長期計画の狙いは、経営者の想いを実現させることにあり、そのためにイノベーションへつながるコア技術の深耕や強化をします。
変化へ柔軟に対応した取り組みが必要です。技術開発や商品開発は、変化そのものを対象にしたプロジェクトのようなものです。
研究開発は極めて不確実性の高いものを対象にしなければなりません。費用対効果から判断すると、経営者としては避けたい仕事かもしれません。
しかしながらモノづくりを主業とする企業が新たな付加価値を創出するための研究開発をやらず、現状維持を継続していたらどうなるか・・・・。
こうしたことも多くの経営者はご存知です。
そうなると、やるべきこととは、リスクを避けることではなく、リスクに適切に対応し、研究開発の有効性を向上させ、成功の確度を高めることです。
そのためのマイルストーンであり、チェックポイントです。
計画対比で現状の立ち位置を確認しながら、先の流れを見通すことが、モノづくり現場で長期計画をやりきる要諦です。儲かる工場経営で必要な経営者としてのスタンスです。
工場内で通路を横断するとき、一旦立ち止まり、足元や周囲を見回し、その後、先を見て、危険物がないかを確認します。
設備を稼働させるとき、一呼吸おいて、起動スイッチや設備全体を見回し、その後、異常がないことを確認します。
長期計画のマイルストーン、チェックポイントは特別なことではありません。現場では、災害や手順ミスを防ぐために普通に、指差呼称がやられています。マイルストーンも指差呼称も意図的に行っているうちに、習慣化するものです。当初は意思を持って行うことです。
儲かる工場経営でも経営者による指差呼称が大切です。
事業計画や年間計画を立てた後、定期的なチェックポイントを設けていますか?
経営者ご自身による工場経営での指差呼称を実践していますか?
まとめ:一旦立ち止まって進捗中のプロジェクトの現時点を見回して、当初計画と比較する、そして、先の見通しを立てる。長期計画にはマイルストーンの設定が欠かせない。