「生産性ロードマップ戦略」—儲かる工場経営を目指して—第240話 現場は果たすべき役割を理解しているか?
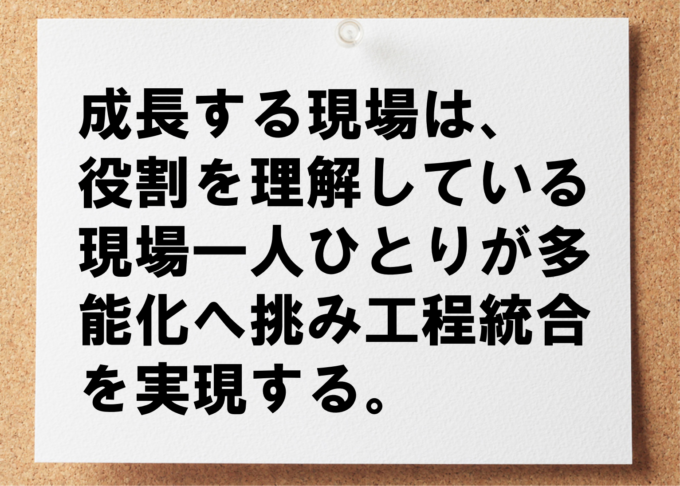
「このフライス盤と向かい合わせになるようNC旋盤を移動させました。」
今年からプロジェクトを始めた機械加工企業、経営者の言葉です。
人時生産性が2,000円台後半で低迷しています。既存製品だけでは埒があきません。新規顧客開拓で黒字化をめざしているところです。
少しずつですが、経営者による「外」の活動が実を結んできました。新たな受注が決まりつつあります。既存製品とはプロセスが異なる製品です。
新規製品への対応力を高めなければなりません。「生産の流れ」をつくる方針を現場で議論していたとき、これまでどんなことをやったのか尋ねました。
冒頭の言葉です。
工程設計のいわゆる工程統合です。
人時生産性向上の論点に「詰めて、空けて、取り込む」があります。製販一体戦略です。手離れのイイ生産が求められます。納期遵守ができているから問題はないと考える現場にはできないことです。判断基準が異なります。
当然のことですが、納期遵守は大切です。これ抜きの事業はありません。ただ、今や納期遵守は当然のことです。競合も納期は守っています。競合と同じ事をやっていても儲からない時代になりました。
そもそも、競合と同じ事をやっていては、行き着くところは決まっています。喜ぶのは発注先の企業だけ。貴社は苦しいままです。体力勝負は中小製造企業の戦略ではありません。
他社を凌駕する事業で躍進したいと考えるなら、現場にも人時生産性向上の論点を教える必要があります。現場は「外」を知らないからです。納期遵守以外の論点を知らない現場は悪くはありません。教えてもらわない限り、理解のしようがないのです。
手離れの良い生産でリードタイムを短くしていきます。その観点を与えてくれるのが工程設計です。具体的には工程分割と工程統合の2つです。
ヘンリー・フォードは流れ作業による大量生産を実践しました。工程分割はその論理的根拠です。困難を分割して効率を高めます。作業者は単能工です。少品種多量生産です。熟練を必要としません。
ただ、このまま多品種化に対応しようとするとロスが生じます。工程分割されたラインの限界です。2つに起因します。
①流れの複雑化
②工程間の停滞
これらは、工程統合で解決できます。
例えば標準工程A→B→C→Dを「A+B+C+D」に統合するのです。全ての対応が工程内となります。工程間が存在しないので停滞が減り、生産の流れができるのです。
例えば、セル生産方式です。作業者は細分化された作業を順番にこなします。究極は一人屋台方式です。
工程統合の具体項目は2つです。
・工程間の物理的な距離を縮める。
・工程間の管理的な距離を縮める。
セル生産方式の他の代表事例として、機能別レイアウトを製品別レイアウトにすることがあげられます。製品毎のラインです。
先の企業でやったのは、(小規模ですが)これです。従来レイアウトでは離れていた旋盤とフライスを隣接させることで、加工待ち時間がなくなりました。
向かい合わせに配置しているので、作業者は前を向き、後ろを向き、仕事をこなすのです。タクトを合わせると、リズムができます。
また、いくつかの工程をローダーやロボットで連結させて、1つの工程のようにすることもしばしばやられる方法です。トランスファーマシンがそれに相当します。
ただし、物理的な距離を縮める移動ができない場合もあります。費用上、レイアウト上の制約です。この場合は、既存レイアウト上で「生産の流れ」を設計します。
流れる量が多い製品群で分類して、流し方を固定し、ルールを決めます。管理の手間を省くのです。ポイントは同期化です。工程間の停滞を排除します。
工程統合、工程集約は製造業のトレンドです。機械加工業界における、NC旋盤とマシニングセンタの機能を合わせ持った複合加工機の活用は具体事例です。
加工途中のロードアンロードが不要なので加工精度が高まり、省スペースにも寄与し、人時生産性も高まります。
外注で製造した鋳造品を機械加工する現場は多いです。生産量が多ければ効率は高まります。ただし、多品種で少量だったどうでしょう。
鋳造品を運搬する手間や欠陥や変形など鋳造品質に起因するトラブルを考えると、いっそうのことバルク材から削り出した方がいいかもしれません。複合加工機なら一気にできます。
昨今は切削加工とAMの組み合わせも出てきました。技術の進化は多様な工程の統合を可能とします。工程統合は人時生産性向上の具体策です。
ただし、闇雲に工程統合をやろうとしても失敗します。工程統合の前提条件を忘れてはなりません。多能工化です。工程統合=多能工化。
作業者に求められる役割が変わってきました。単能工から多能工化へ。「言われた仕事だけやればいいのだ」から「この製品をまるごとつくるのだ」という思考回路に変える必要があるのです。チーム力が問われます。
先の現場には、周りと連携して仕事をする雰囲気がありました。組立て系の製品を扱ってきたからです。連携しないと仕事ができない業態でした。
多能工化が図りやすい雰囲気があり、プロジェクトがドンドン進みます。
これからは作業者の役割も変わります。多能工化できない現場は複雑化、高度化する技術を操れません。競合に負けます。多能工化は生き残り条件のひとつです。
次は貴社の番です!
成長する現場は、役割を理解している現場一人ひとりが多能化へ挑み工程統合を実現する。
停滞する現場は、相変わらず自分の分担にしか興味を示さないので生産の流れができない。