「生産性ロードマップ戦略」—儲かる工場経営を目指して—第246話 意識改革の研修が上手くいかない理由とは?
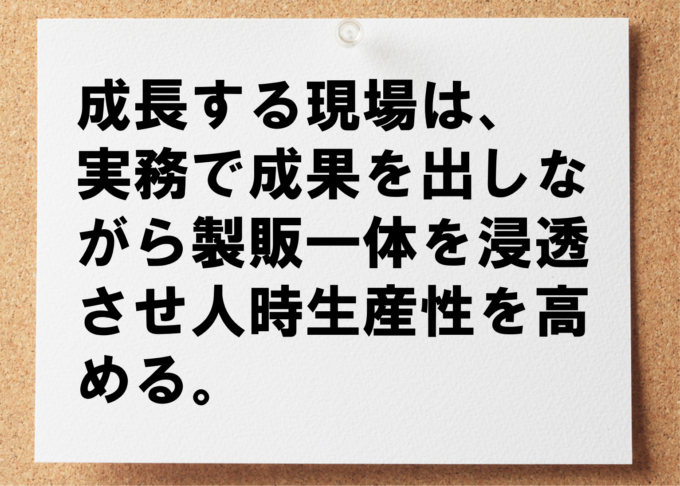
「経営方針を現場へ浸透させる研修をやりましたがダメでした。」
今月から人時生産性向上プロジェクトをスタートさせた経営者の言葉です。
現場には職人タイプのベテランが多く、チームの応受援性が高くないと感じています。一体感を高めれば現場活動が活性化して生産性を向上させられると考えました。
この時期にあっても幸いに受注は旺盛です。全ての案件をさばきたいと考えています。そこで、現場活性化を目的に、経営方針を浸透させるコンサルタントに依頼をしました。
その結果が冒頭の言葉です。
儲かる工場経営の体系は「内」と「外」、「製販一体」です。ベン図で表現できます。スタートは「外」です。事業の目的は顧客創出にあります。ドラッガーが指摘するところです。
お客様に選ばれる商品、製品、サービスを効率良く造って、はじめて儲かります。効率良く造る前に、まずはお客様に選ばれなければなりません。ドラッガーの言葉が腹落ちします。
スタートは「外」なのです。お客様であり市場です。「外」の変化に合わせて「内」を変えるのが正しい姿勢です。
構造改革
意識改革
現場改革
これらは経営者が「やらなければならない」と常に考えている改革です。「外」の激変ぶりを肌で感じる経営者なら、現状維持は相対的な後退、衰退であることを知っています。
継続的改革
継続的改善
これらに実施は、技術進化と競合に追われる製造業の宿命です。したがって経営者は現場を変え、意識を変え、構造を変えるプロジェクトの必要性を感じるのです。
しかし、留意点があります。「内」を変えるために「内」を変える活動は上手くいかないということです。
少数精鋭の現場は生産活動で手が一杯です。中小製造現場ならなおさらです。突発、特急対応も含め、毎日、納期遵守にエネルギーが費やされています。
重要度と緊急度が高い仕事に日々晒されているのです。重要度は高いけれども緊急度が低い仕事は後回しになります。改革業務は後回しにされやすいのです。
ただし、これは現場が持つ意識の問題ではありません。環境整備の問題です。「内」を変えるために「内」を変えるのではなく、「外」のために「内」を変える環境を整備します。
仕組みづくりをするための仕組みづくりではなく、「外」のための仕組みづくりです。
少数精鋭の中小現場を変える方法は実務を通じてしかありません。実務を通じて「外」の成果を出すことです。そうして現場を変えます。そうすれば結果として意識が変わるのです。
少数精鋭の中小現場は日々、生産活動で手一杯だという前提を忘れてはなりません。人的余力がある大手と同じ仕事のやり方をしても成果は出ないのです。
少数精鋭の中小製造現場ならではのやり方をしなければ上手くいきません。
「外」を対象にした目的のために「内」のやり方を変え、仕組みを造り、実務で成果を出して意識を変えるのです。目的設定が大事です。
・この商品の地元シェアを50%以上へ高めることに挑戦する。
・主要なお客様5社から獲得する付加価値額を20%増やすことに挑戦する。
・新規のお客様を2社開拓して、付加価値額5百万円/月積み上げることに挑戦する。
・従来、毎月2~3件断っていたお客様からの案件を全て受けることに挑戦する。
目的の対象が全て「外」です。これらを実現するために「内」をどう変えればいいのかを一人ひとりへ問うのです。「数値」に経営者の想いを語らせます。
・「外」を対象にした目的を「数値」に語らせる。
・「数値」を達成するために、やり方をどのように「変える」のかを問う。
・「変える」ための「仕組み」を造る。
・「仕組み」を機能させて、「実務」で成果を上げる。
・「実務」の仕事ぶりをフォローし評価する。
・「評価」されれば意識は変わる。
「ウチの社長はこうした仕事ぶりを評価してくれるのだ。」との新たな判断基準が共有されます。意識改革はこうして進むのです。変えろと言われても変わらないのが意識です。
さらに、一旦変わればそれが「普通」になるのも意識です。つまり意識は環境整備次第とも言えます。大手と中小の現場差異を感じて知った事実です。
現場改革→意識改革→構造改革
この順番です。意識改革→現場改革ではありません。これをやると「生き様」が改革の対象になってしまいます。
私たちの本業は事業を成長発展させて利益を積み上げることです。人の性格を変える手助けをする場所ではありません。中小製造現場には、そんな時間も暇もないのです。
製造現場は、「理屈」の前に「成果」です。
製造現場は、「抽象」の前に「具体」です。
製造現場は、「理性」の前に「感情」です。
3現主義とは言い尽くされた言葉です。大手や中小の現場を肌感覚で理解できていないと製造現場は指導できません。製造現場は極めてリアルな世界だからです。
リアルの中にバーチャルを組み込むのが手順です。実務というリアルで成果を出しながら、製販一体と言うバーチャルな空間を浸透させます。
いきなり製販一体を説いても、現場はピンときません。だから、まずは小さくてもいいので人時生産性向上の5大作戦なのです。
先の企業で実施した「経営方針を現場へ浸透させる研修」自体が悪かったわけでありません。その前にやる事があったということです。
理屈の前に成果でした。経営改革の仕切り直しをすることにしました。新たに今月からスタートです。実務を通じた成果(小さくてもいいのです)で現場を変えます。
ただし、闇雲に現場活動を始めてもダメです。
数値化構造が設計されていなければなりません。例えば、富士山の頂上を目指したいとき、「目指すは富士山の頂上、標高3,776m」という数値目標だけでは辛いということです。
プロセスも明らかにしなければ現場は踏ん張れません。到達標高、頂上までの残り登山距離、気温や気圧、体調の見える化など各種情報(数値)も手にできれば気持ちが変わります。
製造現場ならではの数値化構造です。人時生産性を軸に据えます。大手がその規模にもかかわらずベクトルが揃っているのは数値化構造のおかげです。
次は貴社が成功する番です!
成長する現場は、実務で成果を出しながら製販一体を浸透させ人時生産性を高める。
停滞する現場は、研修を繰り返すだけで大切なことを浸透できず人時生産性が伸びない。