「生産性ロードマップ戦略」—儲かる工場経営を目指して—第252話 継続的改善を実現する環境整備とは?
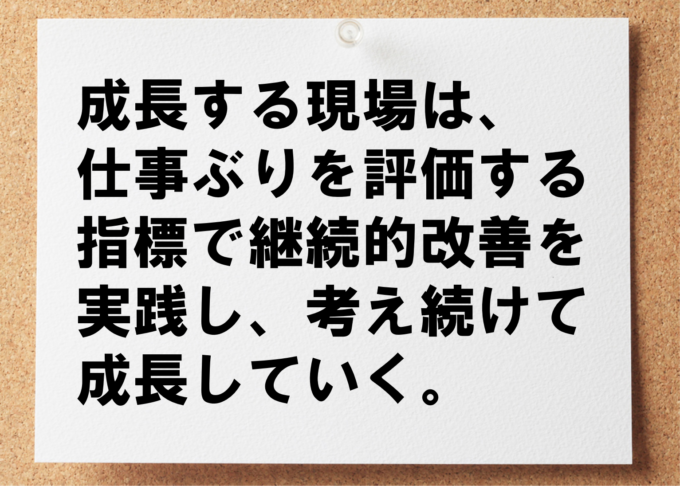
「継続的な取り組みができないのです。」
先週の個別相談で中堅製造企業、経営者が語った言葉です。
人時生産性が業界平均値より低いことがわかりました。このままではダメです。そこで属人的なやり方と決別し、積極的に付加価値額を積み上げる戦略へ転換することを決断しました。
数値で状況を見せられると黙っていられないのが経営者です。
あらゆる判断基準を「外」に変えます。
新たな挑戦をやり切るのに大切な観点があります。いままでの失敗を踏まえることです。同じやり方をしたくありません。同じやり方をすれば、同じ結果になります。
過去の失敗を振り返ったときに、経営者から出てきたのが冒頭の言葉です。
ISO9001では「継続的改善」が規定されています。ISO9001それ自体の有効性については議論のあることころですが、QMSで求める「継続的改善」は取り入れたい概念です。
改善活動を継続的にやります。「考え続ける現場」を育成するためです。
経営者の仕事は「工場の外」にありますが、「工場の内」にも気を配らなくてはいけません。時代の流れと共に「工場の外」は勝手に変わりますが、「工場の内」は変えようとしない限り変わらないからです。
多くの経営者はこのギャップにイライラを感じます。
市場やお客様は時代の流れと共に変わります。技術の世界で戦うのが製造業です。技術革新の影響を受け、既存市場が雲散霧消することもあります。
写真フィルム、カセット式ビデオ、ガラ携などなど、枚挙に暇がありません。
イノベーションが製造業成長発展の原動力ですから特別なことではありません。技術革新に応じて新たな市場が生まれ、お客様の要望も変わります。
需要と供給のバランスを決める「神の見えざる手」よろしく、「工場の外」では「(技術革新に刺激を受けた)神の見えざる手」がはたらくのです。
その結果「工場の外」はわが社の事情に関係なく勝手に変わっていきます。
生き残るためには「外」の変化に合わせて「内」を変えなければなりません。しかし、残念ながら、「内」には「神の見えざる手」に相当するものがないのです。
何もしなければ、変わりません。いつまでたってもそのままです。具体的な活動で現場を刺激する必要があります。その具体手法が継続的改善です。
貴社の現場には貴社の現場独自の仕事のやり方があります。これまでは、そのやり方でもよかったです。
しかし、今後も、そのやり方が通用するかどうかはわかりません。「外」は変わり続けます。それに合わせ、新たな判断基準を決め、やり方を変えなければならないのは明らかです。
仕組みづくりでは、成果もさることながら、そのプロセスも重要です。試行錯誤が貴重な学びの場になります。
答えのない問題に取り組むわけです。現場独自に考えるしかありません。「考え続ける」姿勢がなければできないことです。ワイガヤでメンバーの知識と経験値が高まります。
新たな判断基準を現場に導入したら、現場は混乱するでしょう。これまでとは違うやり方をするわけですから当然です。現場からの反発もあるかもしれません。
が、徐々に慣れ、いつの間にかそれが普通になります。考えなくてもできるようになります。これがゴールです。定着した状況です。考え続ける現場を育成しなければなりません。
経営者が社長業に専念するためです。
「内」は「外」と異なります。「内」には「神の見えざる手」がありません。したがって継続的改善が必要なのです。継続的改善で現場を刺激し、現場を変えます。
ご相談をいただいた先の経営者の現場では、この継続的改善がありません。改善活動もやっていませんでした。断続的に社長指示で改善をやらせたことはあります。しかし、全て曖昧なうちに終わりました。続かないのです。
そして、続かないのには理由があります。数値目標がありません。これはそうした現場に共通の問題です。
・継続的改善では具体的な数値目標が必要です。
・人時生産性で全てを語れます。
そこで、先の現場では、人時生産性を3,000円前半の水準へ高めることを第一段階の目標に設定しました。具体的な数値目標ができれば、継続的な改善活動がやりやすくなります。
継続的改善の環境整備の一つ目は数値目標の設定、具体的には人時生産性の目標設定です。分母と分子に分解すれば改善テーマを設定できます。
そして、もう一つの環境整備も忘れてはなりません。各工程の仕事ぶりを評価する指標設定です。原単位や品質、効率で現場の状況を見える化します。定義を明らかにして、指標の考え方を共有することが肝要です。経営者はこれでQCDを把握します。
数値を現状把握のために使います。センサーを現場の隅々に設置する感覚です。これを見れば現場の体調が分かります。現場の体温、血圧、血糖値、心拍数・・・。
日常的にこうした数値を把握するメリットは何でしょうか?変化に気づきやすいということです。数値は点で捉えてはいけません。変化で捉えます。先手を打つためです。
一方で、各工程の仕事ぶりを評価する指標設定ができていない現場では何が起きるでしょうか?こうした現場では、事が起きてから動き始めます。
そうなったら、経営陣から状況を報告するよう指示が飛んでくるのです。現場は落ち込みます。状況を数値化して報告したら「どうしてこうなったのだ」と責められるのが目に見えているからです。
こうした現場では「数値報告=叱られること」という図式ができています。現場も人の子です。できることなら責められたくありません。ごまかせるならごまかしたくなります。
現場が悪いとは一概に言えません。数値報告=叱られるという思考回路を埋め込んだ経営者にも非があります。この点はしっかり確認して下さい。なぜなら、こうした思考回路が蔓延している現場は、品質不正の温床になる懸念があるからです。
昨今、大手製造企業の品質不正が目につきます。2017年が特にそうでした。数値の改ざんや粉飾の真因は経営者や管理者側の姿勢にあったことが多くの報告書で明らかになっています。そもそも、ことが起きてから動くこと自体、なっていないと認識しなければなりません。
我々は変化を捉えて先手を打たなければならないのです。これが少数精鋭、中小現場の正しい姿勢です。数値はそのための道具です。現場の頑張りを評価するためでもあります。
各工程の仕事ぶりを評価する指標設定がない現場では、頑張りを評価しようにもできないのです。日常的に数値化されていないとそうなります。
各工程の仕事ぶりを評価する指標設定をしていますか?
原単位や品質、効率で現場の状況を見える化して、日常的に現場の体調を把握する環境整備で数値化報告=叱られることという思考回路を払拭します。
・人時生産性による、継続的改善の数値目標の設定
・各工程の仕事ぶりを評価する指標の設定
こうした環境整備をすれば、継続的改善がやりやすくなります。数値を現場の体調管理の道具とするのです。
平時、体調良好、体調不良での体温の判断基準を設定します。変化を捉えて現場に対応策を促すのです。
新たな判断基準が現場に定着すると、考えなくてもそうすることができるようになります。ただ、気をつけたいのは、「考えなくても」できるということです。
これは生産現場で効率を高める要点ですが、ここで進歩を止めると、便利さのお陰で考えない状況が続きます。したがって、「新たな判断基準が出来上がったその瞬間、その判断基準は新鮮さを失い劣化する」と考えることも大事です。
それがさらなる高みを目指した判断基準を考える動機づけとなります。こうして継続的改善が“普通”になるのです。経営者が社長業に専念できる環境が整っていきます。
ただ闇雲に継続的改善をできるようになろうとして、思い付きの取り組みを進めようとしても頓挫します。現場は「変わる」ことに慣れていないからです。
したがってプロジェクト形式でやります。時間を買う経営者はここの取り組みで外部の力を上手に使っているのです。
一人で悩みながら現場を導くのと、外部の力の後押しを受けながら現場を導くのとでは同じ試行錯誤でも状況が全く違います。
目隠しながら走るマラソンと伴走車がついて激励されながら走るマラソンくらいの差があるのです。時間を買うとはそういうことです。
「このような方針書があれば継続的な現場活動ができそうです。具体的な数値目標がなければ続かないですね。」とはロードマップの事例を目にしながら語った先の経営者の言葉です。来月からスタートします。
次は貴社が成功する番です!
成長する現場は、仕事ぶりを評価する指標で継続的改善を実践し考え続けて成長していく。
停滞する現場は、数値化報告=叱られるという思考回路で考えることをやめ成長を止める。