「生産性ロードマップ戦略」—儲かる工場経営を目指して—第254話 分業化の目的を理解していないとどうなるか?
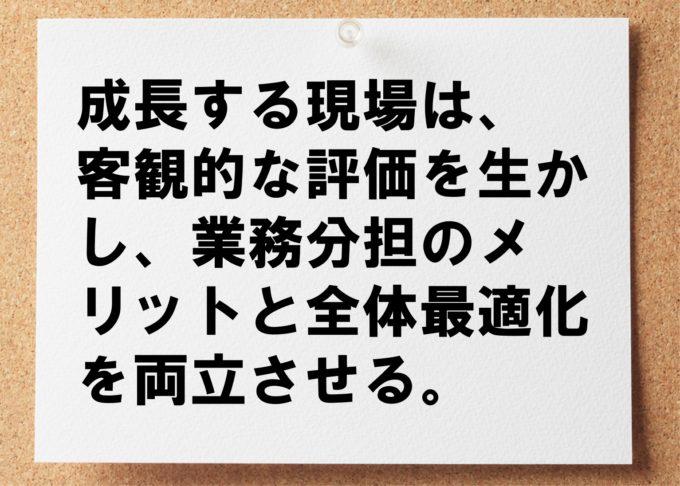
「無理なことを要求されて困ることが増えています。」
中堅製造企業、幹部の言葉です。
生産用設備を設計・製造している企業です。ニッチな分野の業界で存在感を示しています。ただし、ご多分に漏れず安価な海外品が攻勢をかけてきました。
このままではダメだと考えた幹部は製販一体体制の強化が必要だと考えています。顧客に選ばれるためです。プロジェクトが進行中です。
生産用設備という商品の性質上、販売して終わりではなく、顧客の現場へ搬入・据え付けまでやります。設備を立ち上げた時点で検収です。
その後は継続的なメンテナンスサービスを顧客へ提供しています。コロナ禍にあっても堅調な収益を確保できているのはこのメンテナンスサービスのお陰です。
メンテナンスサービスでは客先の現場で担当エンジニアとやり取りをします。故障の原因究明などです。
故障の原因が設備の使い方に起因していることがしばしばあります。過負荷のためにシャフトが曲がったとか、モーターが焼けたとか。
事前説明をして、マニュアルを届けているのに・・・。そうした場合でも「設備を入れたそちらに落ち度がある」と言われることがあるようです。
ある客先での話を伺いました。冒頭の言葉です。
設備を入れた客先で、なぜそのようなことが起きるのか?幹部が説明してくれました。
「担当者が多すぎるのです。」
設備制御担当者、機械構造担当者、電気配線担当者、稼働担当者などなど。その設備を稼働させるのに必要な分野が専門化され、それぞれに人を当てています。
結局、稼働させている設備のことを「ほんとうに理解している人」がいないのです。担当分野のことは知っていても、設備全体を把握している人がいません。
分業化の弊害ですとはその幹部の言葉。その企業は一部上場でその名を聞けば誰でも知っている大手メーカーです。
規模が大きくなれば、効率を高めるために仕事を分業化します。それ自体、間違いではありません。しかし、設備を総合的に評価できなければ、なんのための分業なのか?
規模が大きく、名の通った企業の現場だからと言って、適切な対応をしてくれるわけではありません。力関係にモノを言わせ、理屈に合わないことを求める担当者もいたりします。全ては、客先担当者の”品格”次第なのかもしれませんが・・・。
逆に100人程度の中小現場で優れた対応をしてくれる人に出会うとのこと。少数精鋭の中小現場です。分業とはいきません。専門分野だけを・・・とは言えないのです。
担当者は総合的に判断します。(せざるを得ません。)結果として、的確なやりとりができるようです。
分業の意味を理解できていないと先の大手現場のような事態が起きます。
プラントレイアウトの具体項目のひとつに工程設計があります。「統合と分割」は工程設計の初手です。
ここで製品Aを仮定します。主要工程は下記です。
1.材料選定
2.材料検査
3.切断
4.プレス
5.寸法検査
まずは、これら5工程を現場へ配置します。これらの仕事を割り振る考え方が「統合と分割」です。3種類の配置案を次に示します。
案1
1.材料選定
2.材料検査
3.切断
4.プレス
5.寸法検査
案2
1.材料選定と材料検査
2.切断
3.プレスと寸法検査
案3
1.材料選定と材料検査と切断とプレスと寸法検査
案1は主要工程毎に仕事を割り振る
案2は主要工程の一部を統合する
案3は主要工程の全てを統合する
案1では仕事を単純化しています。5つの工程それぞれに仕事を特化させた割り振りです。仕事の設備化がしやすく、作業も単純化しやすく、工程内での効率を高めやすいです。属人的になりにくい現場です。
案2では一部を統合しています。5工程が3工程に減っています。その結果、「工程間」が2つ減り、仕掛を減らしやすいです。一方で作業者はスキルを求められます。選定と検査、プレスと検査のように案1より複数業務をこなさなければなりません。多能工化です。
案2を突き詰めると案3となります。一人屋台方式、セル生産方式と言われる形態です。工程間の運搬と停滞を原則ゼロにします。究極の多能工化が必要です。リードタイム短縮の切り札です。一人屋台方式では工程内の効率化=全体の効率化です。
案3が究極の工程設計と言えます。が、難易度が高く簡単にできないのも案3です。組立系の製造現場でしばしば取り入れられる形態ですが、汎用性は高くありません。技術的な課題に直面します。
したがって、プラントレイアウトでは案3→案2→案1のように、どこまで分割するかを考えます。複雑なプロセスを単純化することに焦点を当てるのです。そうして工程内の効率を向上させます。作業者も仕事を覚えやすいです。
ただ、工程分割で欠かせない論点があります。全体最適化です。分割すれば工程内の効率は高まりますが、工程間に運搬と停滞が発生します。
これはムダ要因です。リードタイムに悪影響を及ぼします。
工程分割では、工程内だけでなく、工場全体の流れの最適化も同時に考えなければならないのです。
経営者は現場の2重構造を忘れてはなりません。現場はどうして部分最適化に偏ります。自分の仕事を優先に考えるのは自然なことです。
ここに全体最適化の視点を持たせるのは経営者の仕事になります。全体責任を持つのは経営者だからです。ここを現場丸投げで成果だけを期待しているようではダメです。
工程統合
メリット:「工程間」が消えるので、運搬・停滞が減り、仕掛を減らせる。リードタイムを短くできる。
デメリット:設備が複雑化する。現場では多能工化が求められる。
工程分割
メリット:設備が単純化できる。作業を単純化できる。工程内の効率を高められる。
デメリット:「工程間」が生まれるので、運搬・停滞が増え、無管理では仕掛が増加する。リードタイムが長くなる。したがって、全体最適化の視点が欠かせない。
工程統合と工程分割は生産の流れをつくるうえでトレードオフの関係です。どちらがイイとか悪いとかという話ではありません。
それぞれのメリットを最大化する落としどころを見つけことが論点なのです。プラントレイアウトのキモと言えます。
業務分担も同様です。統合と分割の考え方が当てはまります。先の幹部が語っていた大手現場では工程分割のデメリットが理解されていなかったようです。
業務分担上の「運搬と停滞」、そして「仕掛」とはなんでしょうか?思い当たることはありませんか?必要なのは全体最適化の観点です。
だからと言って、やみくもに全体最適化の視点を取り入れようとしても上手くいきません。まずは、自分たちの現状を客観的に知る必要があるからです。
自分の状況や姿を「自分」で評価することは意外とできません。先の大手の現場がそうです。一部上場の知名度がある大手です。現場担当者には優秀な学卒が多いことでしょう。それでもこうした状況になるのです。客観的な評価は自分では難しいのです。
ご支援先の経営者が知りたいのは、大手の事例も踏まえ、他社とくらべた客観的な状況です。弊社はそうした情報をお伝えしながらご支援を進めています。大手と中小を実地で経験し、中小の現場でできることとできないことを知っている弊社ならではのプログラムです。
先の大手のようになってはもったいないのです。貴社はいかがですか?貴社の現場は外部と比べるとどうでしょうか?
先の幹部が主導するプロジェクトでは独自の製販一体体制を目指します。
次は貴社の番です!
成長する現場は、客観的な評価を生かし、業務分担のメリットと全体最適化を両立させる。
停滞する現場は、部分最適化で自工程しか考えないので、業務分担の弊害に悩まされる。