「生産性ロードマップ戦略」—儲かる工場経営を目指して—第264話 自分さえよければの考え方が助長することは?
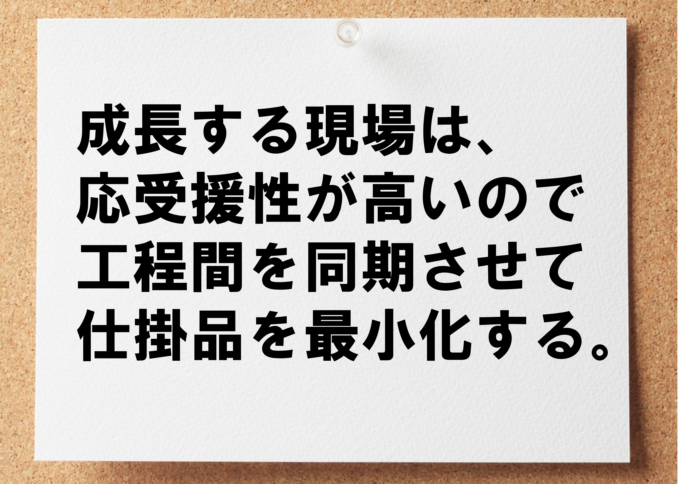
「先生、完成品でも同じですね?」
先週、個別相談をいただいた中堅設備メーカー経営者の言葉です。
多品種のため製品在庫が増えつつあります。増やそうとしなくても増えるのです。管理できない在庫が増えています。
「多品種」は止められない時代の流れなのでやり方を変えなければ在庫は増える一方です。経営者はそこに危機感を抱いています。
極めて健全な危機感ですねと伊藤はモニター越し(オンラインなので)にお伝えしました。
手元のキャッシュが気になります。低金利時代ですが、私達中小企業はその規模感を前提とするなら身軽であるべきです。不確実性が高い昨今だからです。
ここ一番の一撃必殺で勝負をかけるまではそうします。このメリハリ、バランスが肝要です。ここ一番のために手元のキャッシュを確保したいのです。
無管理の仕掛品を増やすと、リスクが増えます。その理屈を説明したときに経営者が口にしたのが冒頭の言葉です。
勘定あって銭足らず。工場経営に限らず、会社経営で留意しなければならないことです。だから手元のお金を管理します。
製造業の収益構造は固定費vs付加価値額。
固定費は経営者が意思決定します。私達はそれを費用と表現していますが、本質は投資です。5年後、10年後のための将来投資と言えます。
固定費の半分以上は人件費で占められている事実を知れば明らかです。昇給分も含めた人件費は将来の活躍に期待をかけた先行投資に他なりません。設備投資もしかり。
製造業は固定費を投資して、付加価値額を稼ぐ構造になっているのです。
まずは、現場へ投入したお金を回収しなければなりません。これには変動費も含まれます。出ていく勢いと回収する勢いを管理します。勘定あって銭足らずを回避するためです。
回収する勢いを削ぐ要因は除去しなければなりません。そのひとつを現場で目にできます。工程と工程の間を見てください。仕掛品が目に入ってきます。
仕掛品を減らせ!は儲かる工場経営の至言です。
仕掛品が回収の勢いを削いでいます。
その要因は「停滞」です。
仕掛品にはすでにお金がかかっています。直接的には変動費分、間接的にも将来投資分が費やされているのです。
しばしば言われますが、仕掛品=お金です。お金が眠っていると表現されます。お金が現場のあちらこちらで寝ている状況です。
例えば、生産規模が拡大し、仕掛品が徐々に多くなると、「停滞」するお金も徐々に増えます。これでは回収する勢いが落ちる一方です。
経営者が「仕掛品を減らせ!」と言いたくなる所以がここにあります。仕掛品は「停滞」を生み出します。そして停滞時間は仕掛品の数量から計算できるのです。
ここで、プレス工程と曲げ工程の工程間を考えます。プレス加工後、中間製品を曲げ工程へ運搬します。プレス工程と曲げ工程が同期していれば仕掛品はゼロです。
しかし、機能別レイアウトでジョブショップ型の流れを基本とする中小製造現場で工程間の同期は簡単にできません。
・プレス工程のサイクルタイムの方が短い。
・曲げ工程でトラブルが頻発する。
こんなことは普通に起きます。この結果、発生するのが工程間仕掛です。その後、停滞した仕掛品は曲げ工程の状況に応じて運搬されます。
中間製品の時間経過は下記です。
「プレス加工での作業時間」+「停滞時間」+「曲げ工程での作業時間」
プレス加工が終わっても、直ぐに曲げ加工されません。曲げ加工は一定の停滞時間の後です。停滞時間を計算できないと正しいリードタイムを評価できないことに気付きます。
停滞時間を計算するやり方も知らなければなりません。
例えば8月1日~8月10日、プレス工程と曲げ工程における工程間の10日間平均停滞時間は次のように計算できます。
平均停滞時間=10日間の仕掛品数累計÷10日間の1日あたり曲げ工程への運搬数累計(※)
流動数曲線の考え方を使っています。中小現場の管理者時代、このやり方で職場毎の停滞時間を計算していました。
精度を求めるとキリがありません。
精度はそこそこでいいのです。
計算値の時系列変化を知る方がずっと大事です。なにせお金が眠っている時間です。お金の長時間睡眠は工場の健康に良くありません。
停滞時間≒仕掛品数
これはリードタイムを計算するときに欠かせない公式です。
リードタイムは目で見える作業の作業時間だけで構成されているわけではありません。停滞時間も含めます。目では見えない時間を目で見える仕掛品数で評価するのです。
停滞時間≒仕掛品数なので、工場全体、生産ライン全体のリードタイムは仕掛品数に影響を受けます。至言の本質はここです。
仕掛品が増える→停滞時間が増える→リードタイムが長くなる→売上が立つまで時間がかかる→お金で回収できるタイミングが遅くなる。
仕掛品が増えるとお金を回収できるタイミングが遅くなるのです。勘定あって銭足らずの要因がここにあります。
先の公式(※)はプレス工程と曲げ工程での工程間を対象にした停滞時間です。これを工場全体、生産ライン全体で考えたらどうなるでしょう?
先の「プレス工程」と「曲げ工程」に相当するのは「受注」と「出荷」です。
「受注」と「出荷」を対象にした停滞時間を考えます。
・プレスが終わってから曲げ工程へ運搬するまでの停滞時間
・受注が決まってから出荷するまでの停滞時間
後者は納入リードタイムに他なりません。お客様にとって最も気になる数値です。先の公式から次が導けます。
平均リードタイム=仕掛品数累計÷1日当たり出荷数累計
工場全体、生産ライン全体の重要指標です。数値の変化を追い続ければマクロ的なモノづくり力が見えてきます。
勤務していた自動車部品工場ではこの数値を押さえていました。1ヶ月に十数万個の製品を生産します。気を緩めると滞留が起きてリードタイムが長くなり回収期間が長くなるのです。
応受援性の高い現場とそうでない現場の差はここに現れます。
工程間で同期するように設計されている生産ラインであるなら、生産の流れができやすく、仕掛品が発生するリスクは低いです。
しかし、多くの中小現場では同期していません。多品種少量の特注品生産ですから同期しているほうがまれです。
そうなると、自分の工程の都合だけを考え、「自分さえよければ」と言う思考回路しか持てない現場では仕掛品が積み上がりやすくなります。
次の工程の状況に合わせて、生産の流れをつくろうという意識、全体最適化視点がなければ工程間で助け合う雰囲気は生まれません。
「自分さえよければ」の考え方が仕掛品増加を助長するのです。
貴社現場の応受援性はどうですか?
仕掛品増の一因になっていませんか?
先の経営者が語ったように、完成品でも考え方は同じです。完成しても売上が立たない限り、仕掛品も完成品も「停滞」していることに変わりはありません。お金が眠った状態です。
完成品の管理をし易くする日程計画立案の手順が課題となります。
経営者はリードタイム短縮の観点から完成品在庫を削減しようと考え始めました。
現場の応受援性は高いとのこと。早速、モデルをつくって製販一体で大手の仕事振りを真似ます。夏休み明けから新たなプロジェクトスタートです。
次は貴社がスタートする番です!
成長する現場は、応受援性が高いので工程間を同期させて仕掛品を最小化する。
停滞する現場は、「自分さえよければ」なので同期化がなく仕掛品は増える一方である。