「生産性ロードマップ戦略」—儲かる工場経営を目指して—第271話 分業と集約、分散と集中の判断軸があるか?
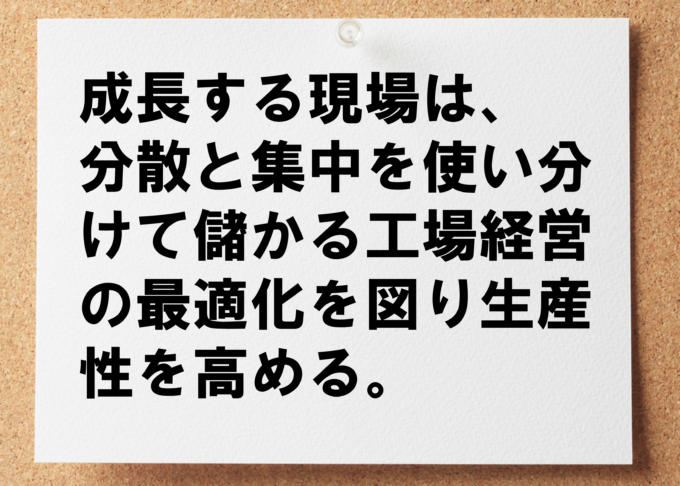
「先生、前工程と連携して現場で検査をすることをはじめました。」
100人規模機械加工メーカー製造部門長の言葉です。
リードタイム短縮には前提条件があります。生産の流れを乱す要因が少ない現場であることです。
生産の流れを乱す要因を放置したまま、人時生産性を高めようとしても混乱を助長します。「流れを乱す」、「流れを滞らせる」、「流れを遮る」要因は解消しなければなりません。
経営者の方々の頭には各種ボトルネックが浮かぶのではないでしょうか?この現場では品質が問題となっています。品質改善から着手をしました。
品質管理には2つの着眼点があります。そのひとつが「不具合品をそもそも作らない」です。検査部門と前工程が連携して自主検査をやってみることにしました。意欲的な現場はなんでも早いです。早速、トライアル結果の報告が届きました。冒頭の言葉です。
これはリードタイム短縮の伏線にもなります。品質問題対策でありながら、同時にリードタイム短縮の具体項目にもなるのです。
品質作り込み体制の具体項目に自主検査があります。加工しているその場でどんどん検査をやってしまうやり方です。外観を重視される部材の検査で特に威力を発揮します。
「不具合品をそもそもつくらない」ために品質をその場でフィードバックします・・・とは言え、中小現場の作業者の多くはオペレーションで手がいっぱいです。
そこで、検査部門と連携して自主検査体制を構築しました。ただし検査部門にも従来の業務があるわけで、簡単に体制が構築できるものではありません。
プロジェクトの目的を理解した従業員の思考回路が変わり、相互補完をする姿勢が生まれたおかげです。応受援性の高さは現場力を表しています。
品質フィードバックが早ければ、早いほど不具合品の”大量生産”を防げます。自主検査体制は品質改善につながるのです。
また、従来、加工後、通い箱に中間製品を入れて検査室へ運び外観を観ていました。自主検査をやれば、「通い箱に中間製品を入れて検査室へ運ぶ」手間がなくなります。
自主検査と出荷検査を連動させれば、検査の作業時間総和を短くできるのです。品質問題対策と同時にリードタイム短縮になると目論んでいる根拠がここにあります。
前工程と検査を一緒にしてしまうのは工程設計手法のひとつです。プラントレイアウトでは重要な論点となります。
・分割と統合
工程を分割すると、価値を生み出さない「停滞」と「運搬」が生まれます。工程設計では、そうした観点で「統合」するか?「分割」するか?を考えます。
分割と統合、分業と集約、分散と集中。これは工場経営上の論点です。最適化はどちらで実現できるか・・・・。この2択は戦略的意思決定です。
2020年に発生した新型コロナウイルスは、サプライチェーンのありかたについて課題を投げかけてきました。分業と集約、どちらが最適なのか?
世界規模の非常事態に直面し、日本を含め、各国は感染拡大防止のため人や物の移動を制限しました。その結果、サプライチェーンが機能しなくなったのはご存じのとおりです。
分散している工程間のつながりが寸断され、営業・受注だけでなく、調達や生産にも支障をきたす企業が続出しました。
2021年版ものづくり白書によると、サプライチェーンへの影響で生産へダメージを受けた企業は約80%にのぼっています。生産ラインや工場が停止した企業もありました。
分散化の狙いは分業化による最適化です。しかし、こうした世界規模の非常事態では、分散されたサプライチェーンが安定生産のあだとなりました。
私達はサプライチェーンの分業と集約を見直す必要に迫られています。
グローバルに分散させた工程を国内に集約させることも考えなければなりません。一方で日本電産の永守会長は拠点をグローバルに分散させる方向性は変えない考えを明らかにしています。分散と集中は経営判断です。
これは国内サプライチェーンでも同様です。外注先の非常時対応次第では、リスク回避のため、内製化も視野に入れなければなりません。貴社のサプライチェーンは非常時にも機能しますか?分業と集約の見直しが必要です。
自動車業界は今、100年に1度と言われる変革期です。自動車の動力がどうなるか?答えのない問題に自動車メーカーは直面しています。
トヨタ自動車はガソリンエンジンに加えて、電動車ではハイブリッド車(HV)や電気自動車(EV)、燃料電池車(FCV)までを幅広くそろえる「全方位戦略」です。分散です。毎年、純利益2兆円を稼ぐ足腰が強い企業基盤がなせる戦略かもしれません。
日産自動車はEVと独自HV(e-power)2本柱に絞る方針です。またホンダは2040年までにグローバルでEV、FCVの2つ集約し、その販売比率を100%にするとの方針を明らかにしました。ガソリンエンジン車はゼロということです。
企業の命運をかけた分散と集中の戦略と言えます。協力会社は戦々恐々です。自動車業界では協力会社も含め、生き残りをかけた戦いが始まっています。
儲かる工場経営の要諦はお客様に選ばれる商品を効率よくつくることです。まずは、お客様に選ばれないと、どうしようもありません。
したがって、経営者は、「内」を現場に任せ、「外」と「製販一体」の仕組みづくりに専念したいのです。分業と集約、分散と集中は事業モデルづくりの判断軸にもなります。
事業を成長させる場合、コア技術は集中させて、お客様の業界を分散させるというのはそのひとつです。
業界で存在感がある企業なら、特定の業界で生き残れる可能性は高いですが、平均あたりでウロウロしている程度の存在だったらどうでしょう。それにもかかわらず、その業界にしかお客様がいなかったらどうなるか?
自動車業界一辺倒の中小製造企業がコロナ禍で苦境に陥ったと報道されていました。分業と集約、分散と集中は儲かる工場経営の判断軸です。
分業と集約、分散と集中は経営者の思考回路に組み込みたい判断軸です。これは現場活動にも通じます。現場にも持ってもらいたい思考回路です。
新たな工場や生産ラインを構築するときに、大切な観点を与えてくれます。先の現場の事例のように日頃の現場活動でも生かせるのです。
そして、新たな思考回路を現場に組み込むためにプロジェクトをやります。手順があるからです。手当たり次第、闇雲にやっても長続きしません。
プロジェクトを成功させる3種の神器等の環境整備も欠かせません。人の言動は環境に左右されます。見通しを示すロードマップも重要な役割を担っています。
先の現場は、そうしたプロセスを経て、自主的な実践モードに変わりました。分業と集約を使い分けています。貴社では取り組みが進んでいますか?
次は貴社が挑戦する番です!
成長する現場は、分散と集中を使い分けて儲かる工場経営の最適化を図り生産性を高める。
停滞する現場は、分散と集中の選択を誤って、我流で突き進み、業界で取り残される。