「生産性ロードマップ戦略」—儲かる工場経営を目指して—第278話 日程計画を現場に決めさせていないか?
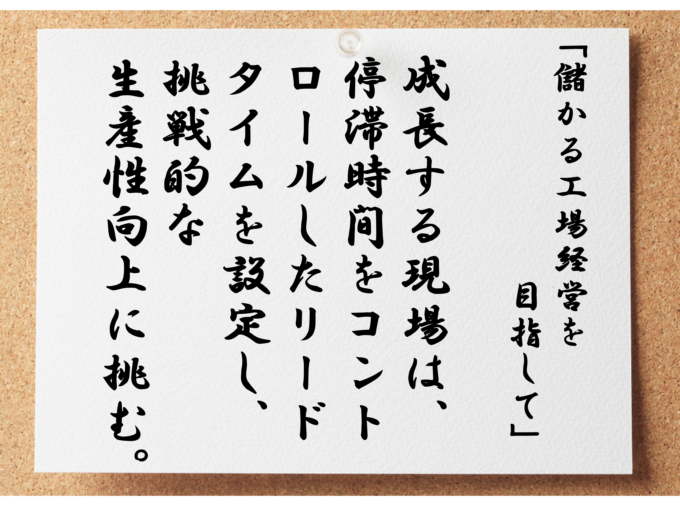
「日程計画を現場に決めさせたらダメですね。」
個別相談でご相談いただいた中規模メーカー経営者の言葉です。
売上高至上主義から人時生産性向上へ舵を切ろうと決断しました。従来の売上高に焦点を当てたやり方を続けても、発展性がないと感じています。
現在、一般的な生産性や良品率を指標としていますが、収益とのつながりがイマイチです。今、売上高がコロナ禍以前の水準まで戻らない状況に直面しています。
この経営者の優れているところは、ご自身の体系を持っていることです。ただし、売上高に焦点を当てていたやり方が時代にそぐわなくなりました。
それなら、それを変えればいいだけです。
やることは「体系」のVersion Upです。
まずは、今までのやり方を確認します。工程管理の2本柱です。日程計画について、冒頭の言葉が返ってきました。
経営者は大日程計画で年間付加価値額を明らかにします。そこから導き出されるのが月別必達受注量です。
そして、3カ月程度先の受注量見通しを中日程計画で確認します。もし、必達受注量に未達の月があれば、埋まるまで頑張らなければなりません。
中小製造現場の管理者時代、未達の月を埋めるために、現場の若手とお客様のところへ足を運んでなんとかしようとしていました。
リーマンショック後の時期です。黙っていては受注が減る一方でした。必達受注量という具体目標があれば頑張れます。その背景に付加価値額があればなおさらです。
「給料アップを実現したかったら、付加価値額を積み上げないとダメだよね。」その若手もこの理屈を理解するようになりました。腹落ちした仕事なら踏ん張れます。
中日程計画の判断基準は「現場に予定を入れられるか、入れられないか」ではなく、「必達受注量に達しているのか、達していないのか」です。
全ては利益アップ、給料アップを目指した人時生産性向上のためです。先の経営者もそのことに気付きました。
お客様からの問い合わせ案件の受注可否を現場の判断基準でやっていると、結局はハッピーになれないということです。経営者はそのことを現場へ教えなければなりません。
日程計画を使いこなすためには、リードタイムを設計し、それをコントロールする必要があります。貴社の現場では「正しいリードタイム」を設計できていますか?
リードタイムは単純に実績から設定できればいいというものではないのです。正しいリードタイムでなければなりません。正しくないリードタイムだったら正す必要があります。
弊社の人時生産性向上の実務ではリードタイムを重視します。
削減の時代から積み上げの時代に変わった昨今、詰めて、空けて、取り込むことが中小現場の命脈を保つのに必要であると考えるからです。
儲かる工場経営の体系の根幹をなすのがリードタイムです。
実務ではリードタイムを決定する2つの設計を進めることになりますが、前提として、設定するリードタイムが「正しい構造」でなければなりません。現場は構造を理解していますか?
リードタイム(基準日程)=加工時間+検査時間+運搬時間+停滞時間
リードタイムは原則、工程記号を構成する4つの要素工程の作業時間計で評価できます。最後の要素工程に注目して下さい。「停滞」です。
現場が停滞時間をコントロールしているなら、正しいリードタイムが出てきます。
しかし、現場が主体的に停滞時間をコントロールすることはできないものです。イイとか悪いとかではなく、そういうものです。
現場は日々、納期に追われています。納期遵守を絶対と考えている現場が、ムリと思われる納期を避けるのは当然です。
現場は、自分が提言した納期を守れなかったら責めを負わされると考えています。だから、経験と勘に照らし合わせて、”無難な“計画を立てるのです。
責められてまで、挑戦しようと考える人はいません。リードタイムの判断を現場に委ねると最後の項目を多分に含んだものになります。その方が現場は安心です。結局、現場の我流では経営者の願望を実現できません。
詰めて、空けて、取り込むことに挑戦するなら、リードタイムは、経営者の指示にしたがってストレッチな目標として設定される必要があります。
挑戦には経営者の後押しが必要です。
・正しいリードタイムは「停滞時間」がコントロールされているので挑戦的である。
・正しくないリードタイムは「停滞時間」が放置されたままなので保守的である。
経営者は自分の決意を現場へ伝え、奮起を促します。
「無理なことは分かっているが、生き残るには、これを実現させなければならないのだ。」
日程計画を現場に決めさせたらダメな所以はここにあります。
リードタイムを使いこなせるようになると、現場はあることに気付きます。
・リードタイム ≒ 仕掛品量。
手離れがイイものづくりは仕掛品を減らすのです。管理の手間が減り、新たなスペースが現場に生み出されます。
儲かる工場経営の観点では下記です。
個別のリードタイム→工場全体のリードタイム→仕掛品の増減→キャッシュ増減
正しいリードタイムが設定できれば正しい日程計画が出来上がり、経営者が目論む付加価値額が積み上がります。リードタイムの考え方を現場へ教えなければなりません。
・ミクロのリードタイム(商品別、製品別)
・マクロのリードタイム(工場全体)
人時生産性向上プロジェクトで取り組みを進めますが、闇雲に正しいリードタイムをやろうとしても失敗します。注意が必要です。
「停滞時間」の存在を明らかにするところから始めます。さらに、認識された「停滞時間」を除去する背景を現場に腹落ちさせなければなりません。
「納期を守っているのだから問題はない」と考えている現場に新たなことを知らせる必要があるのです。
腹落ちしない仕事をいくらやっても当事者意識は生まれません。問題が起きても放置されるだけです。そのうちうやむやになって取り組みが雲散霧消になります。
手順を踏まなければならないのです。ロードマップはそのひとつです。
次は貴社が挑戦する番です!!
成長する現場は、停滞時間をコントロールしたリードタイムで挑戦的な生産性向上に挑む。
停滞する現場は、停滞時間が放置されたリードタイムで保守的に変わらないまま仕事する。