「生産性ロードマップ戦略」—儲かる工場経営を目指して—第282話 リアルタイムの現場見える化になっているか?
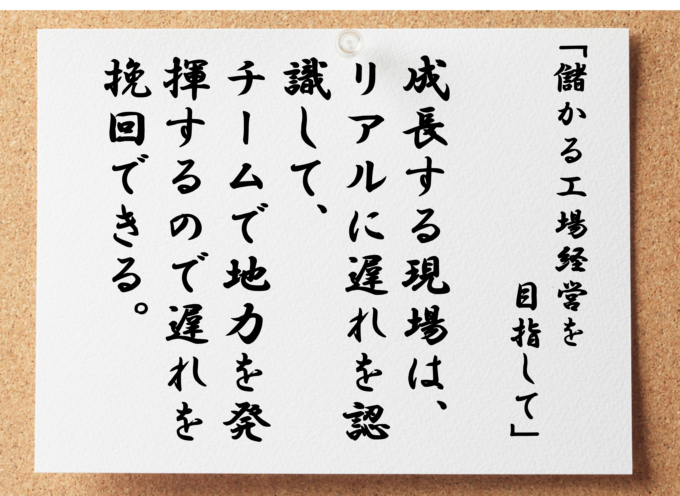
「リアルでなければだめですね。」
今月からプロジェクトをスタートさせた自動車部品メーカー経営者の言葉です。
数年前から収益がかんばしくありません。コロナ禍の影響は少ないものの、儲からない収益構造になってしまったようです。
魅力的な商品、製品を扱っています。経営陣、幹部が覚悟を決めて本気を出せば上手くいきますよ!!と激励しながらプロジェクトを開始しました。
人時生産性向上プロジェクトはいきなり始めません。急いてはことを仕損じます。環境整備からです。いくつかある環境整備のひとつに「現場見える化」があります。
生産の状況を数値でとらえるのです。具体的なやり方を確認しているとき、経営者が語ったのが冒頭の言葉です。
貴社の工程管理は機能していますか?
・生産計画
・生産統制
これら2つが工程管理の体系です。体系ですから抜けがあると機能しません。体系とはそう言うものです。
日々の生産活動でストレスを感じませんか?活動が体系になっていないからです。抜けがあると担当者は力ずくでやります。担当者は辛いです。
「管理」はそれ自体で存在し得ません。比べるものがあって初めて機能します。生産計画と生産統制は一対です。
当コラムでしばしばお伝えしている「カイゼン」の著者今井正明氏の次の言葉があります。
「標準のないところにカイゼンはない。いかなるカイゼンにおいても、その出発点は、現在の立脚点である。あらゆる作業者、あらゆる機械、あらゆる工程に適用される正確な測定基準が必要である。」
「基準」がなければ改善をやってもしょうがないということです。
比べるものがなければフォローも評価もできません。経営者は仕事にならないのです。現場は自分で決めた勝手な基準で仕事をやり始めます。
・生産計画で基準を設定する。
・生産統制で実績と基準を比べる。
これで生産活動のPDCAを回します。やりっぱなしではダメです。CとAが抜けると仕事の精度や水準が高まりません。フィードバックがないとスキルアップは無理です。
生産統制が大事です。
CとAが抜けたままでも納期は守れます。これが「力ずく」です。火事場の馬鹿力はたまに発揮するものであって、毎日が火事場の・・・では担当者が疲弊します。
貴社の工程管理体系を見直さなければなりません。
生産統制で必要なのが「現場見える化」です。生産状況を数値化します。数値化すれば実績を比べられます。基準vs実績、計画vs実績。これが管理です。
そして、ここで確認しなければならないことがあります。時間軸です。貴社では計画vs実績をどのような時間軸でやっていますか?
あるご支援先でのことです。幹部に現場の計画と実績をどのように管理しているのか尋ねたところ一枚の表を見せてくれました。
月毎の売上高、生産数量、営業利益、経常利益。
損益計算書の数値に生産数量を加えて「整理」した表です。1か月遅れの1か月間単位で管理していることになります。自社で経理部門を持っている経営者ならもう少し、早く損益計算書を手にできるかもしれません。
が、外部の税理士や会計事務所にお願いしている経営者なら1か月ほど経過しないと手にできないこともあるようです。その企業の生産統制は、1か月遅れの1か月間単位管理となっていました。
スループット分析もしていましたが、如何せん損益計算書ベースです。現場の生産活動の実績とずれる結果が出ることもしばしば。スループットがマイナス表示になることもあります。
損益計算書の費用はいわゆる発生主義です。したがって製造現場の製造活動とはズレます。「分析をするのですが、よくわからないのですよね。」とは幹部の言葉です。
残念ながら生産統制ができていません。そのご支援先では「現場見える化」の環境整備が課題となりました。
生産統制の目的はただ一つです。
・遅れを認識して、挽回する。
「遅れ」と「挽回」です。
これだけです。
したがって、「現場見える化」はリアルタイムにやりたいのです。遅れの認識と挽回を適切にやるためには、少なくとも1か月遅れの1か月間単位とはなりません。
いわゆる死亡診断書を手にしても死んだ人は生き返らないのです。遅れを挽回するにはリアルタイムでやりたくなります。
大日程計画で必達仕事量が明らかになります。したがって、日々、必達仕事量VS実績仕事量の管理です。
計画VS実績。
日々是決算。
遅れたら、即、挽回。
1か月間の稼働時間は限られています。私たちは、限られた工数のなかで必達仕事量を達成し、それを超えなければならないのです。
必達仕事量VS実績仕事量をリアルタイムに把握したいのです。必達仕事量の表現方法は2通りあります。
・生産数量
・付加価値額
必達仕事量とは儲かるための仕事量に他なりません。収益上のトントンを生産数量で表現できれば儲かる基準を生産数量で設定できます。現場には響きやすいです。
ただし、多品種少量生産の特注現場では儲かる基準を生産数量で設定することはできません。その場合、儲かる基準は固定費となります。
したがって、生産統制のやり方は下記です。生産計画と比べます。
・計画生産数量VS実績生産数量
・固定費VS付加価値額
流動数曲線や貴社独自のやり方で日々是決算の結果を表記すれば、リアルに遅れを認識できます。(ご支援先の現場ではこのあたりいろいろと工夫されています。)
遅れを認識したら、チームで挽回です。計画通りなら何もしません。
日々是決算の「基準」を現場へ提示しておけば、経営者は現場に仕事を任せられます。その分、経営者は楽になるのです。貴社ならではの「基準」をつくって下さい。
儲かる基準を生産数量で設定するか?
固定費で設定するか?
こうした「現場見える化」ができれば人時生産性向上プログラムは加速します。リアルであればリアルであるほどそうです。
1か月後よりも1週間後、1週間後よりも1日後、よりリアルに実績を見せられた方が現場は動きます。人は数値で示されると、黙っていられません。客観的だからです。
ただし、闇雲にこれをやってもダメな場合があります。リアルタイムで追いかける先にある「共通の目標」がなければ、現場は踏ん張れないからです。
リアルタイムに遅れを認識できても、その後の挽回ができません。共通の目標があるから頑張れるのです。
遅れ発生は非常時と言えます。挽回する場合、力ずくでもかまわないのです。緊急事態なので、理屈抜きで挽回しなければなりません。
そうした地力はチームが機能していてこそ発揮されるものです。ワンチームという表現もありました。組織活性化が前提にあります。
「現場見える化」があっても、挽回する気力のない現場にとって、その仕組みは宝の持ち腐れです。
先の企業では3ケ月目標、6カ月目標、1年目標、5年目標、10年目標を掲げました。丁寧な目標設定は現場に一体感をもたらします。
次は貴社が挑戦する番です!
成長する現場は、リアルに遅れを認識してチームで地力を発揮するので遅れを挽回できる。
停滞する現場は、1か月遅れの1か月間単位で管理しているので遅れ自体を認識できない。