「生産性ロードマップ戦略」—儲かる工場経営を目指して—第283話 見えないことを見えるようにしているか?
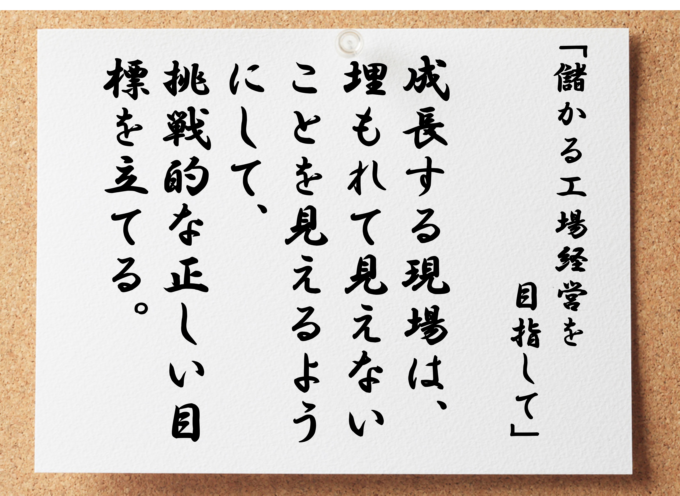
「停滞時間とはそういう意味なのですね。」
数カ月前にプロジェクトを開始した現場管理者の言葉です。
その企業の経営者は管理者育成に悩んでいました。人材育成なので人事関係の専門家に力を借りて・・・とも考えたようですが、しっくりこなかったようです。
弊社の考え方に納得いただきプロジェクトをスタートさせました。弊社が考える人材育成は製造現場ならではの再生産式です。
大手と中小の現場では仕事のやり方が違います。そもそも大手と中小のビジネスモデルは異なるので当然です。人材育成は特にそうかもしれません。
管理者の人材育成にはいくつかの要点があります。
スキルよりも大切なことがあるのです。工程管理を習得してもらい実践するときにも欠かせません。リードタイム分析で実務を進めているときに管理者が語ったのが冒頭の言葉です。要点を押さえてくれました。
人時生産性向上活動では「詰めて、空けて、取り込むモデル」の定着を目指します。豊かな成長発展を実現させる具体手段が人時生産性向上活動です。
弊社ではプロジェクトで実践します。利益アップ、給料アップの実務です。プロジェクトを通じて人材も育てられます。伊藤自身も各種プロジェクトの実践で鍛えられました。
さて貴社でも各種プロジェクトを展開していると思います。プロジェクトの目的はやり切って、成果を出すことです。経営者はプロジェクト自体が目的化しないように気を配らなければなりません。
プロジェクトで成果を出す貴社独自のキモは何ですか?
弊社でもご支援先に応じてお伝えしています。ご支援先の業種業態は多様です。したがって、基本的にはケースバイケースですが、共通の要点もあります。
プロジェクトは現状の立ち位置分析からやります。ベンチマーキングです。現場を見える化し、数値化してビフォー・アフターを比べられるようにします。
分析する=比較する
ここで絶対にやらなければならないことがあるのです。定義の設定です。「定義の設定」は優先度の高い要点です。
数値化する際のルールが統一されていないと議論がかみ合いません。ルールが同じなので「比較」が成立します。
例えば、標準時間は正味時間と余裕時間で構成されます。ただ、実務上、余裕時間ではなく余裕率で設定するのが普通です。そして、この余裕率には2通りの定義があります。
余裕率(A)=余裕時間÷正味時間
余裕率(B)=余裕時間÷(正味時間+余裕時間)
実務上の標準時間は正味時間と余裕率で決定されます。その結果、標準時間の定義も2種類になるのです。
余裕率(A)による標準時間と余裕率(B)による標準時間。
余裕率の定義をあいまいにしたまま、余裕率を(A)とした人と(B)とした人が議論してもすれ違います。(ちなみに伊藤はAが多かったです。)
経営者は「定義」を曖昧にしたまま、現場に数値化を求めてはダメです。定義も一緒に伝えます。そうしないと議論の場でムダが発生するのです。
あるご支援先で現場キーパーソンの打ち合わせに出席したときのことです。4人の現場キーパーソンが各自、活動進捗を説明し始めました。活動が数値化されています。
数値化していることは評価したいのですが・・・・・、残念ながら議論が進みません。
なぜか?
数値化の定義が各自、バラバラだったからです。稼働率ひとつとっても、分母に計画停止を含むのか、含まないのか、皆まちまちです。統一しないと数値比較ができません。
こうした「定義」で手を抜くと後々大変です。先の打ち合わせでは時間の半分以上を「定義」の確認、説明に費やしていました。
問題の本質に肉迫する前に、打ち合わせが時間切れになってします。
また、「見えないことを見えるようにする」も管理者に押さえて欲しい要点です。現場に埋もれていることを明らかにしないままプロジェクトを進めても成功しません。
例えば、工数分析は現場のあらゆる作業を明らかにして進めるものです。埋もれた作業があると正しい分析ができません。
ある塑性加工現場で工程分析をしたときのことです。分析結果が実態と合いません。調査したら「埋もれている作業」がいくつか見つかりました。
なぜ、埋もれた作業が出てきたのか?
多品種小ロット生産化が進む中、バリ取り、仕上げ、手直し等、それまで現場に丸投げしていた業務の負荷が無視できなくなったからです。現場が悪いのではありません。埋もれた仕事を業務として設定しなかった経営者にミスがあったのです。
経営者は埋もれた作業を放置してはいけません。
・現状を正しく把握できない。
・品質不正等、正しくない行動を生む温床になる。
埋もれて見えてない仕事を見えるようにしなければ、経営者は上記の困りごとに直面するリスクを抱えます。
リードタイム分析はリードタイムの構成を明らかにすることからやります。構成がいろいろあるからです。例えばリードタイムの構成を次のように説明できます。
工程内+工程間
リードタイム分析のうち、下記の時間測定はしっかりやられていることが多いです。
・工作機械の段取り作業時間
・溶接作業時間
・プレス設備の稼働時間
・組立作業時間
等々。
いわゆる工程内のリードタイムです。各工程にはキーパーソンがいて、自職場をがっちり守ってくれています。工程内での作業時間は明らかにされやすいのです。
一方、工程間はある意味で微妙です。工程間の経過時間を気にしている人がいるか?いないか?工程間のリードタイムは明るみに出にくいものです。埋もれたリードタイムになります。
無視できる水準なら問題ありません。しかし、そうでなければ、埋もれたままにしておけないのです。
・生産リードタイムの設定を誤る。
・工程間管理の希薄さが起因となるトラブルが発生する。
見えてない時間を見えるようにしなければ、経営者は上記の困りごとに直面するリスクを抱えます。先の管理者は埋もれたリードタイムを見つけました。
部門長や工場長等、管理者の仕事は、経営者の方を向きながら、現場へ経営者の目論見を伝えることです。経営者の意図を翻訳して現場へ伝えます。したがって、経営者の意図を現場が受け入れられるかどうかの判断を事前にできなければなりません。
経営者の意図は簡単に実現できないことが多いものです。
私たちは技術の世界で戦っています。日々、ブレークスルーに挑戦しているのです。経営者は無理と分かっていても豊かな成長発展のためにそうした課題を掲げます。したがって管理者は少々無理でも頑張ってやってみようと現場へはたらきかけるのです。
ただし、こうした管理者による現場への激励や働きかけには前提があります。管理者が現場のことをがっちり把握していることです。
もし、管理者に見えていない作業や見えていない時間があったら、物理的にできないことを無理強いする恐れがあります。管理者の要点のひとつとして、「見えないことを見えるようにする」を挙げている所以です。
管理者の人材育成にはいくつかの要点があります。
・定義の設定
・見えないことを見えるようにすること。
例えば上記です。管理者には現場を導くためにこうした要点を習得してもらいます。スキルとともにこうした見方を習得してもらうのです。
ただし、人材育成は闇雲にやらないことです。手順とやり方があります。特に管理者の人材育成はそうです。要点を押さえなければなりません。
先の現場管理者も見えない時間を見えるようにした結果、リードタイムの構成を実感したようです。正しい検討は正しい目標設定につながります。
経営者の願望成就に1歩近づきました。千里の道も一歩からです。
今度は貴社が挑戦する番です!
成長する現場は、埋もれて見えないことを見えるようにして挑戦的な正しい目標を立てる。
停滞する現場は、見えていることしか見ないのでもれが生じて正しくない目標を立てる。